Introduction: DIY 3D Printed Solder Fume Extractor and Filter
Soldering is an essential part of constructing electronics projects, but the fumes can be annoying, and are a potential health hazard.
This article presents a design for a soldering fume extractor using an active carbon filter to direct fumes away from your immediate work area, and hopefully make them less problematic.
The design is inspired by the devices described in these Instructables, but this is a completely new drawing with some significant changes:
- https://www.instructables.com/Build-Your-Own-DIY-3D-Printed-Soldering-Fume-Extra/
- https://www.instructables.com/Minimalist-3D-Printed-Fume-Extractor/
The main change is to eliminate the holder for the filter media. In this design, the media is installed directly into the unit and the top is sealed using a screw down lid. This is intended to reduce the likelihood that air bypasses the filter media while also simplifying the design.
Additionally, all the screw points use heatset threaded inserts.
Errata
Please note I modified the drawings after I produced the unit in the photos to correct some problems. I made the following changes:
- Incorporate a 0.5mm tolerance on the lid
- Use heatset inserts for the front panel
- Provide a 0.2mm tolerance for the case fit guides
- Move the Potentiometer mounting approx. 10mm towards the centre of the front panel to provide better internal clearance
I did not reprint after making these changes, but I don't anticipate there would be any major problems.
Supplies
Tools:
Outside the need for a 3D printer, there are no specialised tools required that the average electronics hobbyist won't have on hand.
Materials:
- 3D Printed case - get the files from https://www.printables.com/model/876955-yet-another-solder-fume-extractor
- 120mm fan grill such as https://www.printables.com/model/876725-120mm-honeycomb-pattern-fan-grill
- 5mm LED Holder (standard fit) https://www.printables.com/model/625992-5mm-led-holder
- A knob to suit your potentiometer: https://www.printables.com/model/100359-potentiometer-knobs
- Active carbon filter media, 10mm thick, e.g. https://www.altronics.com.au/p/t1292-micron-filter-set-to-suit-t1290-97/
- 2 x M3x8mm cup head screws for front panel mounting
- 2 x M3x12mm cup head screws for lid mounting
- 4 x M4x35mm cup head screws for fan mounting
- Heatset threaded inserts for all above screws (4 x M3x4mmx5mm and 4 x M4x5mmx6mm (https://www.amazon.com.au/dp/B0CBGXMCL8?psc=1&ref=ppx_yo2ov_dt_b_product_details)
- 1 x 120mm x 25mm thick computer fan
- 1 x fan speed controller electronics suitable for your fan (3 and 4 wire fans need different electronics) e.g. https://www.instructables.com/4-Wire-Fan-PWM-Speed-Controller-Using-555-Timer-IC/ or use an Arduino/purchase a ready made controller
- DC barrel jack which will fit an 11mm mounting hole
- Toggle Switch
- 5mm LED (and a current limiting resistor if not built into your speed controller)
- Hot melt glue (or double sided mounting tape)
- Heatshrink tube or electrical tape
- Possibly sandpaper and/or needle files
- 1 x 12v power supply
Step 1: Print Parts and Gather Other Supplies
3D print all the required parts. I printed multiple parts together in the following groups:
- Front Panel and Lid (2h)
- Body Left and Body Right (12h30m)
- Fan Grill (1h40m)
- LED Holder (10 minutes)
- Potentiometer Knob (15 minutes)
The fan grill could probably be printed at the same time as the front panel and lid.
Gather all your other supplies. It's essential that your fan be a 120mm unit which is 25mm thick. A thicker fan could work, but will protrude from the back of the finished unit (you could consider a thinner grill) and you'd need to use different length mounting screws.
It is also important to make sure your fan control electronics are suitable for the fan you have. Four wire fans are controlled differently to two or three wire fans.
Step 2: Install Heatset Inserts
Install heatset inserts as follows:
- Lid closure 2 x M3
- Fan mounting 4 x M4 (two in each half of the enclosure)
- Front Panel mounting (not pictured) 2 x M3
I have had success installing the inserts by holding the insert with thin, pointed tweezers then applying heat with the side of my soldering iron tip.
I set the iron temperature to the maximum working temperature of the filament, in this case I used 220 Deg C and then just let the insert work it's way into the plastic as it heats up.
You need to take care to go slowly or you risk plastic pushing up into the insert. If this does happen, use your tweezers or a similar pointy implement to push the errant plastic back down. This must be done while the insert is still hot (i.e. immediately after removing the soldering iron.
Do not proceed to put any fasteners into the inserts, or otherwise apply pressure to them until they have completely cooled and the plastic has hardened around them.
Step 3: Assemble the Case and Install the Fan
Follow these steps to assemble the main part of the case and install the fan:
- Assemble the case by pushing the two sides together. If you find it won't fit, identify any areas where the extrusions might be interfering and reduce them using a file/sandpaper.
- Test fit the front panel and filter lid, correcting any problems using suitable abrasives.
- Feed the fan wiring through the hole into the bottom part of the case, then install the fan and the grill using the 4 M4x35mm screws.
- Before fully tightening the fan screws, ensure the two halves of the case are brought tightly together. In this design, the fan provides most of the structure holding the assembly together.
When using heatset inserts, you need to be careful not to over tighten any screws so that you don't break the insert free from the plastic.
Step 4: Install the Electronics and Front Panel Hardware
These steps will need to be varied depending on your fan speed controller electronics.
The electronics are secured inside the case using either hot glue or double sided mounting tape. I used hot glue.
Make any electrical connections to the circuit board before you glue it in.
The circuit needs be installed fairly centrally inside the lower part of the enclosure, being careful to install it in such a way that it won't interfere with the front panel hardware.
I recommend you bench test before you glue the board in. Connect it to the power supply and make sure the fan functions as intended. One you're satisfied everything is working as it should, go ahead and secure the circuit into the case using either the double sided tape or hot glue.
The power inlet DC barrel jack is installed in the back of the case
The requirements to install the front panel hardware will depend on the control circuit you have. When connecting it all up, try to maintain the wiring in a neat fashion, and use heatshrink or electrical tape to cover any exposed connections.
Keep in mind that some components install from the outside in - DC barrel jacks are a prime example. For these, you must pass the wiring through the appropriate hole in the case, then solder to the component. Don't forget the put any nuts etc over the wires inside the case if that's needed.
Once you're done connecting everything up, give it another test. If it is all working, then screw the front panel in place using 2 x M3x8mm screws
Step 5: Install Filter Media
The filter media needs to be 120mm x 120mm. The media I purchased is 130mm x 130mm, so I cut it down using scissors.
Install the correctly sized filter media into the device through the slot in the top of the enclosure, making sure that it doesn't have any bends which could hit the fan.
Secure the lid to the top of the enclosure using the 2 x M3x12mm screws
Step 6: Completion & Enhancements
Your fume extractor is now assembled and ready for use - make sure to change the filter media on a regular basis.
One possible enhancement to the design would be to power it using a 5 volt USB charger. The fan could be powered via a boost converter, with the 5v supplying the controller.
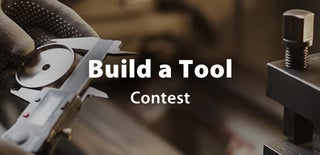
This is an entry in the
Build-A-Tool Contest