Introduction: DIY Sheila Maid Clothes Drying Rack
If you'd ever been to my house you would have noticed that almost every door does double duty as an air dryer for clothing, towels, you name it. Air drying saves you money and is better for the environment but it doesn't look tidy. Over the summer I was visiting a friend and they had this awesome clothing air dryer that lowered down from the ceiling. Which totally makes sense because the air is warmer up near your ceiling so things will dry faster. I came home from that trip and hopped on google to find one of my own. After searching for a while I discovered the thing I was looking for was called a Sheila Maid. I also discovered that they were too expensive for my liking. I had some misc parts leftover from other projects and a 3D printer so I figured I could make one of my own. If you want to know how to make your own sheila maid come along with me and I'll show you how I did it.
Step 1: Tools, Software, Parts
Tools
- 3D Printer
- Laser Cutter(you'd be fine with a jigsaw and an 8mm drill bit )
- Hand Saw
- Chip Brush
- Clamps
- Impact Driver
- Optional 3D Printed Dowel cutting jig(see attached STL)
Software
- Fusion 360
- Inkscape
- Slicer of your choosing (3D Printing)
- K40 Whisper (Laser cutter software)
Parts
- 3 - 608zz Berrings
- 3- 26mm long 8mm diameter dowels
- 3- 60mm long 8mm diameter dowels
- Nylon Mason Line
- 3mm Birch Plywood (I used 2 30cm by 30cm pieces due to the cutting area of my laser.)
- Wood Glue
- Wood Stain
- Polyurethane
- Screws
Attachments
Step 2: Dreaming and Designing
I've included all of my final stl and svg files so if you want to skip right to the making you can download them and move on to the next step. If you'd like to know more about the thought process that led to these files read on.
To start out I looked at a lot of Sheila Maids online. In looking at them I started a breakdown of what made a maid... The four main parts were bars of some sort, pulleys, some structure to hold the bars in place, and a place to anchor the lines on your wall. With these main components in mind I got to designing the pulleys.
Pulleys are made up of a fixed support, a wheel, and a pin to connect it all together. I started my design with the wheel. I knew I would be running two pieces of Mason line in each most of the pulleys so I opted to design a plastic sleeve with two channels to keep the lines from becoming tangled. The fist thing I needed to do was get the 608zz bearing into Fusion 360. I turned to Instructables user Rpalak's Fidget Spinner Instructable for guidance on how to pull this off. After all what is a fidget spinner if not a fancy wheel around a pin you hold. With my bearing imported it was time to make my wheel sleeve to do that I made a sketch of the profile and revolved it around a center axis line. With that the wheel part of my pulley now designed in fusion it was time to work on the fixed support.
Looking online many of the Sheila Maids used pulleys with really beefy lag bolts to stay in place. Given the flex of my dowels and the fact that I wasn't planning on making the structure for my Sheila maid out of cast iron that seemed like overkill to me. I decided I could support my Sheila Maid with four screws per pulley (I ended up only using two per pulley in the end) Knowing I wanted four screw holes, the size of the pulley wheel, and that I was going to use a section of 8mm dowel for a pin I had enough info to inform my design choices. I fiddled around until I had a fixed support I thought looked neat and would do the job. From here I decided to work on the wall anchor and line stops.
The concept for the line stops came from the plastic bits on the end of window blind lines. They are little cones with a hole in the top and a piece of plastic the lines tie around to prevent them from fitting through the hole. These were easy to design. For the cone I used the revolve function again and for the plastic bead I just made a sketch of two circles and extruded the outer ring. I could have done this with a revolve as well but it was simple enough to do it with an extrude. With the easier part of the job out of the way I started in on the wall anchor. I wanted a few things from my wall anchor that it would have a lip to keep my cats from accidentally dropping my airing clothing, a satisfying secure feel when the stop cones were in place, and lastly to be easy to operate. To achieve the first goal I added a filleted lip so even if the stop cone was pulled from its spot they wouldn't just slide free. For the satisfying secure feel I used a chamfer around the hole for the stop cones to rest in. That way the stop cones kind of snap into place. Once I was happy with the wall anchor I turned my mind to the structure of the Sheila Maid.
I quickly sketched something up in Fusion. Knowing the kerf on the laser would be small I just went with holes the same diameter as my dowels. Then knowing I wanted to hang it I made a whole in the top center I could use to tie the mason line around. Finally since I was going to be laser cutting not 3D printing the structure instead of extruding the sketch I exported it as a DXF. I imported the dxf file into Inkscape and set the line colors to prep it for laser cutting. With the lines colors set it was time to cut, print, and tweak the designs.
Step 3: Cut and Tweak the Design
I only had so many pieces of 3mm birch plywood so instead of just running headlong into making I decided to iterate and refine my designs. To do this I turned to my trusty and always plentiful friend, Cardboard rescued from cardboard shipping boxes. This way I could figure out how many layers of birch ply would be needed to make my support structures. Using my laser I cut the design out of cardboard and then mocked up the Sheila Maid. I learned two important things when mocking it up. One was at their full length the 8mm dowels I was using had too much flex just two lines. This informed the final length of the Sheila Maid. The other was that I would need three layers of birch ply for the support structures. Once I was happy with the mock up I moved on to the real thing.
I cut the layers I needed for the structure out of 3mm birch plywood. once I had six wooden layers cut I used wood glue to secure them together. To make sure everything stayed aligned while the glue was drying I used small pieces of the dowel and clamps.
Step 4: Printing, Pounding, Pulley
While the glue was drying I started the 3D printer printing. I used supports when printing because I wanted the holes to be as close as possible to their drawn dimensions. While the pulley parts printed (say that three times fast) I used a 3D printed dowel cutting jig and my hand saw to make 3 26mm long pins for my pulleys. Once the pulley parts had printed I used a block of hard wood to persuade the bearing into the printed bearing sleeve. With the impact persuasion completed I mounted the wheel in the pulley with the wooden pin and just like that I had a pulley. I made sure it spun freely patted my self on the back, made two more, and went to bed.
Step 5: Assembly, Staining, Waterproofing
With the glue dry on the structural pieces of the Sheila Maid it was time to put it all together. I put a little wood glue on the ends of the dowels and inserted them into the structure pieces. They fit like a glove which gave me a sense of satisfaction. While I waited for the glue to dry I prepped my other desk to be a safe place to stain my maid. Once the glue on the dowels was dry I applied stain to the Sheila Maid following the directions on the can. I left the stain to dry and impatiently waited to apply the clear polyurethane coat to the Sheila Maid. This coating serves two purposes one to protect me for any wood stain bleeding onto my clothing and two protect the wood from the damp clothing I plan on draping over it. With the polyurethane coating applied and dried it was time to hang up my new Sheila Maid.
Step 6: Hanging the Sheila Maid
I located the spot on my ceiling that could support my new Sheila Maid and mounted the pulleys using my impact driver and screws. Luckily for me my ceiling is ships lap so I had strait lines to follow all the way to the wall. The three pulleys mount one over each end of the Sheila Maid and one near the wall to change the direction of the mason line from horizontal to vertical. With the pulleys in place I ran the Mason line through them and tied off to the Sheila Maid using a bowline knot.(If you don't know how to tie a bowline that is okay because there's an instructable for that.) Now it was time to raise it up and set the down and the up positions with the stopper cones. To set the up position I raised up a pair of my PJ's to a height I was happy with and slid the smaller stopper cone over both lines. Then I fed on the stopper bead and tied it off so the stopper cone would be the right height to hold my Sheila Maid where I wanted it. Then I flew in my PJ's and stopped just before my first stopper cone hit the pulley. I secured the bigger bottom cone at this height using the same technique. Now all that was left for me to do was a load of laundry so I could put my new DIY Sheila Maid clothing rack to use. If you want to see it going up and down you can see it in action and my poor spelling on Gfycat.
Thank you for taking the time to read this Instructable. I hope you had as much fun reading it as I did making it.
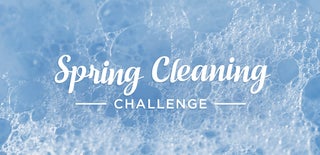
Participated in the
Spring Cleaning Challenge