Introduction: De-Fleshing Tools
Disclaimer - This talks about something some people might find a little gross that's part of a leather-making process.
I recently learnt how to tan animal hides and as part of the preparation you need to make sure all the 'flesh' is scrapped off the hide. It's a little gross to be honest, and it was pretty hard work. So I made a couple of different de-fleshing tools to scrap the hides down.
Instead of making something from scratch, I designed these as blades for paint scrappers that people likely already have lying around.
Supplies
- Paint scrapers
- Saw Blade
- Drill
- Grinder
Step 1: Apply the Template
Print out the blade patterns and after cutting them out use a gluestick to fix them onto the saw blade.
There are three different designs:
- Comb blade for common scrapers
- Straight blade for common scrapers
- Combination blade for bolt-on scrapers
The rounded corners are to avoid hooking into the hide and tearing it.
Attachments
Step 2: Cut Out the Blades
Now use an angle grinder to cut out the blades, you can use a cut-off disc for cutting the combs into the blades. Now take these to the grinder and make sure the scrapping edge is even and then grind a bevel onto them. The bevel only needs to be on one side, much like a chisel, not both sides like a knife.
Now mark the holes with a centre punch and drill them to size. If the steel is too hard to drill you will have to anneal the metal first. This is done by heating the metal up red hot and allowing it to cool slowly.
Step 3: Heat Treat the Blades
I normally use a gas torch and some firebricks at this stage, but you can also use some charcoal and a hair dryer as a blower. You need to bring this up to about 724°C (1335°F), but the easiest way to tell is when it's glowing 'Cheery Red' or a magnet no longer sticks. When it's hot enough dip the cutting edge into some oil (I use cooking oil, but you could probably use old motor oil).
Once it's cooled down sand it to remove the burnt oil and then stick it into an oven for an hour at about 200°C, this will temper the blade so it doesn't chip
Step 4: Clean Up the Blades
There are a few ways to go about this depending on what look you want. I left some of mine raw with the blackened oil scale still on there, this will help protect against rust. The combination blade was sanded and polished before applying a coat of oil.
Step 5: Mount the Blades
Now swap out the original scrapper blades for the new defleshing blades. The combed blade is more aggressive and the straight blade is good for a final scrap down.
Once you are finished scraping the hide, clean and then oil the scraper to prevent rust.
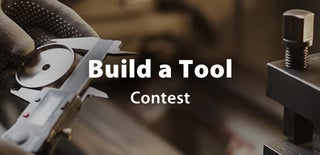
This is an entry in the
Build-A-Tool Contest