Introduction: Death Eater Cosplay With 3D Printed Details
There are many fun elements to this costume and to portraying such a diabolical character. As with any build there were lots of frustrations but some delightful surprises along the way as well.
I'll sort these steps into logical order and instructions to follow, but really, most of these various parts were overlapping and happening at the same time, with very little order and quite a lot of it I was making up along the way, just trying things out till something worked. (Or didn't... )
Let's start with the mask. I think the key to a scary Death Eater is the beautiful mask. I love that the movie designs portray an emotionless face, a sort of impassive death skull. It's a terrifying design and therefore extremely fun to create!
Step 1: 3D Printed Files
If useful I could upload the .stl files to Pinshape and Thingiverse, but here they are as well.
For the mask use the face, head and teeth files.
Step 2: 3D Printed Death Eater Mask
Creating the model for this mask started out as a Saturday morning experiment, using some tools and methods I wasn't sure would work. I was working in SketchUp using a few plugins, SubD, Vertex Tools and Quad face tools which allow for more organic models than is typically seen from SketchUp. After some initial success with the model I got excited and spent the rest of the morning fine-tuning and completing the mesh and that really was the motivation to do the entire costume.
If you are familiar with SketchUp, another organic modeling plugin is Artisan, either would work, though both are a different paradigm to modeling than is the typical SketchUp work flow. I found a model on the 3D Warehouse of a human head and modeled the mask to fit it, not worring about the scale until the model was finished, it's easy in SketchUp to re-scale an object using the scale tool or tape measure tool. When completed I took measurements of my own head and tried to scale the mask to fit. I had to split the model to fit inside the printer, and after trying a few options found a good angled split above the eyebrows worked well.
Despite my measurements I did have trouble with dialing the scale in correctly, so it took a bit of trial and error to get it fitting well.
I used basic cyanoacrylate (crazy) glue, with quick set spray. I glued and sprayed the middle portion first, then worked around to the edges to align the two halves as accurately as possible. A 2nd pair of hands is very helpful with this.
To finish the mask surface I sanded the surface with 120 grit paper then used wood putty over areas that needed it. I found having a small cup of water nearby allowed for dipping my finger and smoothing out the putty really well. After the putty was dry a quick sanding of 120 grit and final sanding of 240 left a nice surface ready for painting.
I did 2 coats of filler primer, then used a silver paint with hammered texture for the base. Then drew a number of thin curly designs on the computer, mirrored them for each side of the mask and cut them out with a vinyl cutter. I didn't have a plan for how to apply these, just tried to make sure they were mirrored as well as possible on the mask and evenly spread around. I use the vinyl transfer paper as this formed and adhered well to the surface, but was also easy to peel off after spraying the mask with a dark metallic color.
The final touch was using some silver acrylic and rubbing it evenly all over the mask. This brought out the texture, provided a final color I really liked and tied the mask together overall.
In the model I had created small loops to attach a band to for wearing, but these weren't designed well and broke off pretty easily. I simply glued a black stretch band to the inside sized to fit my head.
Step 3: A Wand Worthy of the Dark Lord
In imaging my Death Eater, one aspect I liked the idea of was creating a bit of backstory, something personal about this Death Eater, and for me that was the wand. I think most of us assume that Slytherin house is the origin for most if not all followers of Voldemort, but in my mind surely there are members from the other houses as well.
I wanted my wand to reflect a corrupted character from Ravenclaw house, so his wand has the skull of a Raven.
After creating the mask model, I was overly confident in my organic modeling skills. This model provided it's own challenges but after plenty of mistakes and false-starts, I had the handle created for my wand. My idea was this wand would be a fusion of silver and wood, the raven's skull handle would blend into a wooden handle that I would turn on a lathe.
I included a recess in the base of the raven neck to join with the wooden handle, printed, sanded and primed it.
On the lathe this was a good opportunity to try muti-axis turning, something I've been wanting to do. My first attempt in walnut shattered when I cut too aggressively on it, so I tried with hickory and more care. Multi-axis turning involves moving the stock off the original axis. You don't have to move far at all, I was moving only 2-3 mm to each side of the center to create a unique pattern along the length of the wand. A few other details were added and it was sanded, stained and waxed.
After gluing it to the printed raven skull, I used more cyanoacrylate glue and quick set spray to add texture and mass to the glue joint and eventually all over the skull as I liked the appearance.
I painted it silver at first, then after the success with the mask, painted it dark and wiped on silver acrylic to bring back the sheen and weathered texture.
For more details, I put together a video of the process here:
Step 4: Long Robes and Tunic
Starting with an existing robe pattern would be a wise choice. I am not wise. I decided to create my own pattern.
I wanted a robe that wasn't too full or long. For testing patterns I like to find bed sheets at a thrift store. Grab some that are on sale and you have lots of fabric for just a few dollars. Of course, you can find some useable fabric as well and the tunic materials and inside lining of the robe were thrift store finds.
In creating patterns, (which I'm a total noob at), I started by taking some general measurements of my torso, and drawing out some basic shapes that were similar to other examples I could find online. I used builders paper to draw patterns on as it's cheap, comes in large roles and I had some on hand. After transferring the test pattern I added some seam allowance as needed and created a basic robe. As expected it needed some adjustments, then for the final robe I also broke down the larger pattern into thinner segments as I liked the look of the extra seams.
The outer black fabric was sewn back together into the major segments, then traced onto a dark blue sheer fabric for the inner lining. A lining at all is optional, but I did like this combination.
The outer robe was sewn together as was the lining. Before combining them though, I used a decorative stitch on my machine and ran the front of the robe from one side to the other twice to create a contrasting decoration, then the lining could be inserted, sewn inside-out, turned back and sewn on the edge again if desired, and the bottom was finished with a serger edge just to simplify and speed the process.
The tunic was also created from a made-up pattern, with paper templates and a test version created first. To create the texture for the shirt, lines were drawn at equal intervals on the outer fabric, which wasn't easy as this fabric was stretchy, then it was sewn to another identical piece of fabric along those marks. Toward the top you can see that the fabric started to bunch up a bit, which still looked ok, but this was a lesson learned too late to vary which row is stitched to equalize the fabric overall. The arms were also stitched in a crossing pattern toward the shoulders before attaching the arms to the main body of the shirt. I did not create this pattern on the back as it wouldn't be seen and this process took an unfortunately long time.
You could save yourself a lot of trouble by finding a really interesting fabric that has unique texture or even embossing in it. It will cost more than a simpler fabric, but you will save a lot of time as well.
One part that I don't have pictures for is the balaclava. This is cheap and easy to buy or quick to sew a simple version, just something to cover your neck and head. I also just used some existing dark pants.
Step 5: Creating the Wand Belt
I think part of the fun in doing a costume like a Death Eater is that you can completely personalize it. There were many different death eater characters with variations in their outfits which just opens up the possibilities. This belt was designed to be similar to a version worn by some of the movie characters, but it's not a direct copy. I modeled the clasps with some simple swirly details to mimic the mask details, with a loop to attach to the center circle and with an empty chamber to insert the belt and attach with glue.
All the 3D printed parts were sprayed with filler primer and then with the same hammered silver paint for some texture. They were then weathered with acrylic paints using a mix of dark colors that were painted on and mostly wiped off.
The belt was the same faux leather I've been using in other parts of this costume, folded over and stitched on a machine to make it just a bit thicker. It was inserted into the clasps with cyanoacrylate glue and that held it very well. I sewed two belt widths, one for the main belt that was about 1-1/4" wide and a 2nd one for the wand holster that was about 3/4" wide and printed a clasp that was slightly smaller for the smaller belt.
I cut up a wire hanger and bent and beat it into loops to attach the clasps to the center circle, and then gauged by eye about where the wand holster should be and sewed it into place. (In truth I didn't like my first placement, so you can see in the final photos the smaller belt was cut and re-attached. It worked fine, just owning my mistakes.)
One final note, working with this faux leather was ok when sewing on just one or two layers, but when trying to attach the holster to the belt and having 4-6 layers of this material, it really gave my machine fits, so some of the stitching was done on machine and some by hand and all of it was frustrating, but possible.
Final weathering and texture for the belt was done by rubbing a bit of brown but mostly silver acrylic into it to match the bracers.
Step 6: Arm Bracers With the Dark Mark
The arm bracers were the last part of the costume completed and are of course optional, but I really liked the way the printed stamp worked with the faux leather to create the dark mark.
I think these would look better with some metal grommets and leather cord lacing them up, but I was out of time and had to improvise with what I had, which was velcro. I used some spare fabric and cut it down to a shape that overlapped my forearm, cut out mirrored copies of the bracers in the faux leather, heated and weathered the material similar to the boots, with lots of scratches and texture. When ready, I heated the surface well and then quickly moved it from the ironing board to my table (for a hard and stable surface) and pressed the 3D printed stamp into place. A few seconds with as much pressure as I could place on it and then peeled it back away for a wonderfully indented and well detailed mark.
On it's own the mark doesn't stand out as well as I'd like, but I took some silver acrylic and rubbed it around the entire bracer which brings out the texture and gives it a great weathered sheen but also carefully rubbing the paint around the indented mark will color just the raised surface leaving a much more defined mark. Very cool.
An alternative method for coloring the mark can be found in the notes of picture #4.
I glued some stiffer material to the back of my bracers and attached some velcro and ready to go.
One final note, in the last picture you can see that a tattoo can also be created with the printed stamp, using a marker that doesn't dry too quickly. It may also help to color the stamp with a marker then breath on it for a few seconds to add a bit of moisture before pressing it to your arm. Not all markers work though, so you may need to experiment a bit before committing your services to the Dark Lord Voldemort.
Step 7: Making the Boots
Before making your own boots, have a look around at what you could find at thrift stores or online that might work. While possible to make boots, the method I'm using ran afoul of several problems and in buying different glues and pure frustration, pretty sure I didn't save any money trying to make these myself.
I started by finding some shoes at a thrift store, that were the basic shape I needed. I definitely looked for boots but these shoes were the best option I could find. That said, I later learned the leather was treated and many different adhesives did NOT work on the shoe leatherThe, but more on that later.
I started by testing a few patterns on my leg until I had a shape that seemed to work well. I used the same faux leather as with other parts of this costume, but to give it some rigidity I spray-glued it to some really stiff material as backing, then sewed the inside together and turned it back out into the leg-tube. The plan was to glue this directly to the shoes, I tried fabric glue and contact cement, neither held well. I tried scratching up the shoes with sandpaper and rubbing them with acetone to try and remove the leather treatment, but it still didn't work. Ultimately I loaded a very aggressive sanding mop into my drill press and sanding the shoes down to the raw leather. I also switched and used 3M Super 77 as the adhesive, which worked pretty well.
With the spray glue, getting the leg 'tubes' aligned correctly on the shoes was very difficult as it sticks instantly and strongly, so it took a lot of prying around and didn't result in as nice a transition as I would have liked, but most of the problem areas were covered by more strips of faux leather.
Cutting strips of faux leather, the rest was pretty simple, spraying the leather and wrapping it across parts of the shoe. I decided to cut the leather at the sole of the shoe and when wearing these some of the leather did start to peel away at that area after walking around a while, so you may want to try some extra reinforcement or a different approach.
Again, I was ultimately happy with the results, but not convinced this is the best method.
Step 8: Final Thoughts and Some Fun Photos
This is the first time I've done an outfit with a full mask which hides all expressions, and also muffles your ability to talk. It's interesting moving around a Con floor and trying to talk or relate to people but tons of fun to walk around with an imposing stride looking like death itself. Obviously it's also hot, but wasn't unbearable.
I hope this will be helpful if you try to do something similar and I hope you'll share any results, would love to see some other versions!
Cheers!
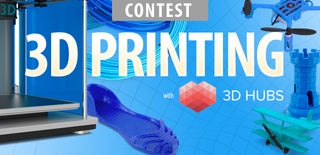
First Prize in the
3D Printing Contest 2016