Introduction: Duct Tape Mannequin
In this tutorial I will be showing you a simple, step by step guide on how you can create your own life-size mannequin.
If you have ever made a costume or a cosplay for yourself or somebody else you've have probably thought that a mannequin would come in useful, to position items, to figure out scales and sizes, to draw patterns on, or simply to display a costume that has been finished.
You can often find cheap display mannequins for sale, but they are generally in weird poses and there is no guarantee that they will be the same size as you or the person the costume is for.
With this method you will be able to make a cheap, light weight and accurate mannequin in less than a day, and all you need is some Duct Tape (and a couple of other things, but Duct Tape is important)
Step 1: You Will Need . . . .
This is what I used to create my mannequin, I am 190lb and 6' 5" tall, so you will have to guestimate what you will need from that. I always recommend to have too much material rather than too little, saves you a 2nd trip to the store.
*** There are alternative materials and methods that can be used, to save time and money. I will note these in Italics like so **
Duct Tape - 100 - 150 Metres
I recommend getting a good brand of tape, sure you can get cheap stuff, but it generally is difficult to work with. Spending a littel extra could save you a whole heap of time.
Plastic Plumbing Pipe - 6-8 Metres
You may not need this much, depending on the complexity of your frame, but this is approximately how much we used.
Plastic Plumbing Pipe Connectors - Right angles, T-Joints, and Straight Connectors
These will help you to join the pipe together to make a sturdy, light weight frame. Make sure you draw a plan of what you'll need before you go to the store, we had to make 2 trips as we were 2x T-Joint short :(
*** You don't have to put a frame into the mannequin, but if you want it to stay upright it is recommended. YOu could use timber, or dowels, or anything that will support some weight. You could always use Duct Tape to join everything together instead of the connectors ***
Painting Overalls - (Gloves and Overshoes are optional)
Basically you need something to protect your skin from the duct tape that can be cut away. We used a cheap painters overall as it is light weight and easy to cut. Overshoes and gloves can also be used if you wish to have hands and feet on your mannequin.
*** To save money you could use an old long sleeve t-shirt, sweatpants and socks ***
Expanding Foam
You will need to do some research here as not all expanding foam is the same. We used a product that was sourced form a fibre glass supplier. It is a chemical reaction, so it does air dry unlike some building foams you get in a can.
Our foam expanded at a rate of 1kg = 30cm Cubed, so we bought 5kg to be sure.
Make sure to get expert advice, always read the directions and use appropriate safety equipment. Always test any new products before use.
*** Don't want to get messy with expanding foam? Or could use old clothes, packing peanuts, newspaper to stuff you mannequin ***
Ancillaries
We stocked up on disposable gloves, mixing cups, mixing sticks, scissors and tools before we started. Make sure to plan out you stages and be prepared.
Step 2: Frame Design
Next up you'll need to design and plan you frame. If you are making a mannequin for yourself you will need someone to take measurements for you. If you are making it of someone else, you will need them present so you can measure them.
Process:
- Sketch Frame
- Measure
- Foot to Foot
- Foot to Waist
- Waist to Shoulder
- Shoulder to Wrist
- Connector Insert Distance
Note Component Lengths
Start by planning you frame with a rough sketch. We went with a square base, 2x uprights for the legs, a cross section at the hips (we had thought about making the mannequin in 2 parts, but decided against it due to time constraints) and used some angled connectors to create the bends are the shoulders.
To get accurate measurements we held the components in the position we desired them and measured accordingly. The first measurement we took was the distance between the feet in a natural standing pose. Taking notes of each measurement is a good idea at this stage, we made a separate sketch for each new measurement taken.
It is very important to consider the length of pipe needed for the insert of the connectors as if you don't consider this your measurements will be WAY off :/
Step 3: Build Your Frame
Now it's on to the fun parts, Construction :)
Process:
- Measure
- Cut
- Clean edges
- Layout Components
- Press Fit
- Check Measurements
If you have made detailed notes on all the lengths you need you can get to cutting.
Remember, measure twice, cut once
I used a Mitre Box and Tenon Saw, but you can use whatever you have, the cuts do not need to be perfectly square, but it does help.
I used a sharp blade to tidy up the outer edges of each cut, this helped with insertion into the connectors. You could use some sandpaper.
Before assembly I laid all the parts out to make sure I had everything in the right order, the fittings do come apart but we tried to avoid have this as it is a bit of struggle.
Once we got to the midway point it was time to check our measurements. Holding sections up against the body revealed we were slightly too long with some of our lengths, so we needed to cut some new ones to get it to the desired height.
Step 4: Wrap in Duct Tape
Process:
- Change into sacrificial clothing
- Assume correct position
- Remove slack form fabric
- Wrap
Get you v̶i̶c̶t̶i̶m̶, eh, I mean subject dressed in whatever you have chosen, either the paper overalls or some alternate clothing that covers the desired areas.
Make sure that the feet and arms are in the correct position before applying the tape, you can use the frame to test.
Use small pieces of tape to hide/remove any loose areas of fabric. We wanted a very accurate copy of my body, so the tape was applied quite tight to capture the detail. Flattening the excess material prior to wrapping helped us do this.
Depending on how well you know the subject you might want to get them to apply the tape themselves to the private areas.
Once all the slack material has been removed it's time to start wrapping. We found it was better to break off length of tape and apply them individually rather than just running the tape around a limb in one go.
We were very liberal with out application of tape, making sure to add vertical lengths to act as reinforcements to the horizontal strips. If you choose to follow this tutorial and use expanding foam, taking you time at this stage and ensuring all parts are covered with at least 2x layers of tape will help reduce any leakage once you start adding the foam.
Once you've got everything covered you can spend as much times as you like making fun/embarrassing/tickling your immobile subject :)
Step 5: Remove Duct Tape
Process:
- Release Arms by cutting along the inside/back
- Cut from back of the neck to the small off the back
- Cut inside of legs from ankle to above the knee.
Make sure that you have medical scissors that you can use to carefully cut the duct tape/fabric. Our scissors proved to be too big and were not suitable. Do some testing before you commit to the full body.
Cutting from the wrists to the armpits on both arms and at the back, from the next to the small of the back will allow the subject to remove the upper half of the mannequin. Take extreme care when cutting, use fingers to pull the duct tape away from the skin before snipping with the scissors.
Once the upper half has been cut away and removed we found that the subject is able to cut from the ankle to above the know themselves quickly and easily with no risk of getting cut.
Step 6: Mount and Seal
Process:
- Disassemble Frame
- Insert
- Seal split line
- Seal to frame
- Manipulate duct tape to correct form
Once the subject is freed from the duct tape skin it's time to put the whole lot together.
We split our frame and the hips and inserted the top section into the body and arm cavities then lower the skin down over the leg section and connected the frame.
Once we were happy with the position we used Duct Tape to seal up the split lines, but only the splits on the arms and lets, we left the back slit to aid getting the foam in later. Again, we used a combination of vertical and horizontal strips to ensure a solid binding.
As our frame penetrates the mannequin at the feet with paid special attention to making sure the this area was fully sealed.
Once everything was seal we manipulated the shell into the correct form. This does not need to be perfect, as the pressure from the foam expanding will do a job job of filling out the Duct Tape skin.
Step 7: Fill With Expanding Foam.
Process:
- Gather utensils, materials and protective equipment.
- Mix Foam
- Pour into form
- Watch for leakage, patch if required
- Seal openings
- Work in sections until complete.
As we mentioned earlier, the foam we sourced will be different from the foam you source, so there is no point going into technicalities. Our Foam worked on a 1:1 mix ratio and the reaction time was less than 60 seconds, so we needed to act quick, working in small sections so that we could control the build up inside the form.
Always have measuring cups that you use to pour into a mixing cup, this helps avoid cross contamination which could potential spoil your entire batch. Clearly mark the product, the lids and the cups you use to measure.
Pour both portions at the same time, mix well and pour. We were working in 100 ml - 200 ml pours building up each leg in turn until we got to the hips.
You will see the foam force the Duct Tape into the correct form, it is important to keep an eye open for any leakage at this point.
Once we reached the hips we sealed off the arm openings and filled the arms before sealing the split at the back and filling the main body.
For the final pour, we sealed up the neck opening so that there was just enough room to pour foam through. We mixed up 2x big batches, poured them in and quickly sealed the hole. As we but in too much foam and the pressure was too great there was some ;leakage through the hole and the sealed up split at the back.
Step 8: Duct Tape Mannequin
And there you have it, one Duct Tape Mannequin made in under and day and for less than $100 (way less in fact, I think we only spent $50!)
There were some areas where the foam didn't quite take the spape of the form, but this can be padded out with newspaper or foam and then covered with Duct Tape. I will probably wrap this again from head to toe, giving it an nice even skin.
The beauty of this method is that it can be used on ANYTHING, body parts, people or even objects.
I hope you enjoyed this tutorial. Sorry for the horrible spelling/punctuation, I'm better at making stuff than I am at writing about it :)
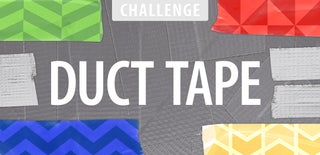
Runner Up in the
Duct Tape Challenge 2017