Introduction: Making the Rat King From Destiny 2
Hello, and welcome to this Instructable.
Before we begin, this is a Non Functioning Prop Replica
My name is Thom I run Sorenzo Studios where we make things. My favourite things to make are replica props weapons, but I don't often get to make things for myself.
Every now and again something appears in a movie or video game that is so beautiful that I have no choice but to drop everything and make it.
When I first say images of the Rat King Exotic Side Arm from (the then un-released) Destiny 2 video game I knew I was going to have to make it. As soon my studio entered in the traditional winter lull I set about making the this beautiful piece.
Due to the complexity of the design (and my desire to do the design justice) I decided to use this project as an excuse to fully embrace current technology, and opted for using more advanced digital design and fabrication techniques. I wanted to see could we achieve something like this in record breaking time. The whole process was carried over a 6 week period. Technology has helped us to speed up everything that we do, and it is for that very reason I have entered this Instructable in to the Epilog IX Challenge in hope of acquiring a new laser cutter for our studio which we are long over due.
I will make some apologies in advance:
Firstly, I'm terrible at spelling and grammar, so I will be editing this over time, if you're the first to read, I do hope it makes some sense!
Secondly, I am fully aware that not everybody is going to have the skills, the time or the technology to recreate this, but since it is one of the finest pieces my studio has produced to date, I simply had to share our experiences.
This is just ONE way that this piece could be made. Like with making anything, there are no wrong ways, but some methods work better than others. Many of the processes/products/techniques we utilised could be substituted by others, and if you do think you could achieve similar result by doing something differently, by all means please do, and don't be afraid to let me know how you got on.
Due to the complexity of this build, it was written with the assumption that the reader would have a basic knowledge of making a prop similar to this. It is not a Step by Step guide, I could have gone into much more detail with some elements, but most of these areas could easily be stand alone Instructables.
If you would like me to elaborate on any of the step, please let me know in the comments and I will do my best to answer you promptly.
Regardless, I hope it all makes sense and I hope you enjoy it <3
Step 1: Gather References
The accuracy of your finished piece is going to depend on 2 things:
- Your skills in being able to recreate a design
- The amount of reference material you can acquire
You need to know what the piece you are trying to create looks like inside and out! You need to see it from all angles, you need to know what size it is, you need to know what colour it is and you need to know what it is (supposed to be) made of.
With the Rat King, there wasn't a lot of reference available at the time, but Bungie, the company that made the game, had commissioned a Prop Replica to be created which used the in game designs, so this was a great point of reference for the design.
Other than that we use in game stills to start with, Google Image Search is extremely useful here, as was the Destiny Reddit community. Once we got into the sculpting stage, we looked a anatomical references for the Rats and the Rat Skull.
There is no such thing as too much reference material!
Step 2: Sculpting
No matter what way you create a piece like this, you are going to be sculpting. Whether that be the traditional way, using clay, or more like model making, building up shapes and forms from sheet materials or a combination of both.
This was my first instinct, crack out the clay and sit down for a week and sculpt the intricate barrel before moving onto the handle and magazine. After analysing the Reference Material it became clear that sculpting this piece would be a challenge, with the amount of the detail require, the symmetry on both sides and my self imposed time limited. I quickly released that this was not the route to go.
I called upon my good friend Glen Johnston to see if he could help. Glen has worked with me on a couple of projects in the past and is an Incredible CG Artist and is also a HUGE geek, just like me. Glen has a background in animation and works with Blender software which describes itself as:
' the free and open source 3D creation suite. It supports the entirety of the 3D pipeline—modelling, rigging, animation, simulation, rendering, compositing and motion tracking, even video editing and game creation.'
Once I had briefed Glen about the project he didn't even wait for me to give him the go ahead to begin, he started then and there.
The first task was to tackle the barrel, or more precisely, the rats. This is where his animation skills came in. Instead of creating 6 rats, or even 3 rats then mirroring them, he started with just One Rat and added a posable armature to the form so that he could control it, moving it's limbs and positioning it into any pose. Using the reference images, he was able to manipulate the body and limbs of the rat into position and could then just copy and paste the rat to create the next one.
-- Images 1-3 --
Once all 3 rats were positioned correctly he simply copied and mirrored them. At this point he had added a basic mock up of the handle to assess the scale and size of the overall piece. He also added in the rat skull which was sculpted separately based of reference pictures of actual rat skulls. The rats are embedded into the body of barrel, the texture of this was created manually, pushing/pulling and flattening the surface. Like with traditional sculpting CG is also a process of refinements. The last task of the barrel section was to go in and enhance all the fine details, like the feet and toes, the facial features of the rats and the fur.
-- Images 4-6 --
According to Glen, that handle was created using some of the more basic CG modelling techniques and came together pretty quickly. The only real issues were the textured areas on the lower section and magazine and the Tsukamaki wrapping on the handle.
After some discussion we decided that the magazine should be left exposed from the base of the handle (as it was in the Bungie Commissioned Replica which was exhibited at E3 and other gaming conventions) instead of completly inserted into the handle as is seen in game.
-- Images 7-10 --
Step 3: Prototyping and Testing
Working in a programme like Blender is fantastic, but it can't always solve real world problems, so we went through an extensive period of testing and prototyping.
My biggest concerns were size/scale and how the components connected.
Traditionally, to figure out the size/scale of a prop piece you would simply scale an image or a blueprint to what you thought was correct, print it out, cut out the outline and measure it up against your hand. This could be repeated until you had the correct scale and you would start you build. Generally you need to hold onto a prop gun before you can determine if it is too big or too small.
With digital design, you could in theory do the same, but instead I utilised the power of Rapid Prototyping by way of my Ultimaker FDM printers. Now I could go into explaining 3D printing in depth, but Instructables is already crammed full of amazing 3D printing information, so if you want to learn more be sure and check out their extensive list of 3D Printing Classes and Projects already available.
Glen had already scaled the model within Blender to what he thought would be adequate for an average human hand, so I split the model and printed just the handle section to give it a real world test fit. We did end up scaling up about 20% as it was a little on the small side. The process was repeated and once I was happy with the overall size I printed all the components.
-- Images 1-2 --
For molding and casting I knew I wanted to keep the elements separate as they would be molded in different materials, cast in different resins and painted using different paints, so it made sense to create them all seperately.
To aid with the molding process and bonding the 2 parts together, a simple channel and groove elements were added on the top of the handle and bottom of the barrel so that they could register together when it came to bonding them.
-- Images 2-4 --
It was at this stage that I noticed that the bottom on the magazine did not line up with the bottom of the handle when fully inserted. Now you probably recall I decided that we wanted to have the magazine exposed in the finished piece? Well after some thought I deduced that it might be a good idea to have 2 different sized magazines, one that extends out of the handle and one that fully inserts. This misalignment might not have been spotted if I hadn't completed this testing phase.
-- Images 5-6 --
Step 4: Stereolithography Printing
From the conception of this project I knew it was going to be a challenge, and was not going to be anything like what we had done in the past.
With such a detailed piece I set out to AVOID sanding as much as possible. If I were to be required to sand build lines from a traditional FDM 3D print, it would take a lifetime and would most likely dampen/loose some of the details.
For this reason I chose to have the part professionally 3D printed using state of the art Stereolithography technology. Stereolithography works similarly to FDM printing, but instead of laying down layers of melted plastic, a laser is used to cure liquid resin in layers. The laser is fired at the surface, curing the resin and the cured piece is either submerged into the resin bath, or lift out from it incrementally. It is a very cool process! It is able to print at a much higher resolution and is the perfect choice for such a complex and detailed piece.
The parts were printed by Materialise here in the UK on their Big Frame High Definition Stereolithography machines using the Somos Xtreme material.
The resolution was incredible, the barrel was flawless, so we went straight to molding with ZERO preparation required! The only sign of obvious build lines was on the flat parts of the handle, which was a pleasant surprise. Some minor wet sanding took care of these.
Step 5: Bonus - the Wonders of Technology
While I was waiting for the 3D prints to be delivered Glen surprised me with some fully rendered images of his model. For a FREE program, it is truly amazing what can be done in Blender.
Now, I fully expect to get some negative feedback about this Instructables (not just for my terrible spelling and grammar) due to the use of advanced and somewhat out of reach technologies.
When I started, I did everything by hand, the long hard way, LOTS of sanding! Over the years I learned that new technologies are to be embraced, they are tools that we can use to improve what we do and how we make.
Having the most elaborate, expensive and sought after equipment does not make you a better maker, just like not having these pieces does not mean that you cannot make something beautiful. You can always make it, it might not be perfect, it might take longer than you would like, but with enough effort you will get there.
This project was to see what could be done when you combine a multitude of skills, abilities, technologies, techniques and materials.
In the spirit of Instructables I have included the digital files for the Rat King, so that anybody with access to a 3D printer can print their own. I would just ask that you do not sell or distribute these, they can our little secret.
Step 6: Molding the Barrel
The intention was to keep all of the mold as simple as possible, both for molding and for casting.
The barrel section was molded with a standard 'dump' pour mold. A mold box was built around the piece, this is held in place with hot glue and the master is taped down with double sided tape. HERE is a video which demonstrate how a mold like this might be done.
*3D printed parts are generally hollow, which mean they have air inside them, which means they float. If your part is not firmly attached it may float to the top which will ruin your mold.
I used Mold Max 30 from Smooth On. This is a tin based silicone with shore hardness of 30, a pot life of 60 mins and a cure time of 24 hours, which is perfect to allow the air trapped in the silicone plenty of time to escape from around these fine details. Mold Max does need to be vacuum degassed, so a degassing chamber is required. (Mold Max NV does not require degassing, so this could be an option if you do not have a degassing chamber)
After 24 hours, the part is carefully released from the mold. There was an issue of locking bars that formed in the silicone through the eye sockets of the skull. To release the master, the silicone was cut in a zigzag pattern so as to slice the bars, in turn freeing the part. The zigzag cut allowed the silicone to register back into itself for future castings.
The magazine was molded in a similar fashion.
Step 7: Molding the Handle
Molding the handle was a little more complex, but I had a plan and I stuck with it.
Traditionally, molds for something of this shape would be made in 2 Parts, so that the silicone mold could be opened and the part released. This generally means that there would be a seam line that would run around the outline of the part where the the pieces of the mold meet. I did not want this as I did not want a seam line on the body of the cast parts that would require sanding.
The initial idea was to make it in 2 parts, one section would be formed along the top face of the master with a core that would run down the cavity for the magazine. The second part would be one solid piece which would cover the ENTIRE handle section. I knew this was ambitions and that freeing the master and subsequent castings would be difficult, but figured at worst I could slice the mold open to assist releasing the part.
I created a simple MDF box and used more MDF to create a space saver that would reduce the total amount of silicone required. I wrapped the master in tape and used non sulphur clay from Newplast to get it lined up evenly in the box.
*Silicone will react to sulphur so you should always make sure to use non sulphur clay!
-- Images 1-4 --
I clayed right up to the top surface, making sure to make contact with the master. Registration keys were added to the clay and some pour spots made of clay were extended up from the surface (this would be the orientation for casting also) The final step was to position a aluminium rod down the centre of the magazine cavity, I figured this would help keep the core in place, but would also allow me to ensure the core had registered correctly to the main mold.
-- Images 5-6 --
The top was poured with Mold Max 40 from Smooth On, this has been my go-to silicone for the vast majority of my work. The 24 hour cure time means I rarely run into problems with bubbles of trapped air and I've learned to schedule when I pour my molds til last thing before I leave for the night so it's ready for de-molding the next day. Once the first pour was cured I opened up the mold box and started to clear away the clay.
Once it was all cleaned It was re-inserted into the mold box and closed up ready for the second pour. You can see from image 11 the reg keys in the core section, this along with the aluminium rod should ensure the piece line up.
-- Images 7-11 --
I figured that this method wouldn't be the easiest to free a casting from, but I was pretty confident that it would come free, with a bit of a struggle once the resin has been fully cured. The biggest concern was the silicone getting locked in the trigger cavity, but I came up with a solution for that. The shape created by the hollow of the trigger is conveniently a perfect circle. I simple cut a disc of 0.5mm styrene and attached it to the body. This will prevent the silicone from bonding to itself and locking the piece in place, but also gives me a nice clean casting with minimal clean up.
-- Image 12 --
The second part of the mold is poured from the open underside of the box, with the master. There were some bleed holes drilled into the MDF space saver to allow air to escape.
Silicone ONLY bonds to silicone so it is important that if you are pouring silicone on top of silicone and you DO NOT want the parts to bond you need to apply a release agent. I use Ease Release 200 for coating the master s prior to pouring and also to prevent silicone bonding to itself. I deliberately did not add mold release to the MDF space saver section so that the silicone would grab onto the fluffy surface, giving the mold some support and also saving a bit of time with the opening/closing of the mold box during the casting process.
-- Image 13 --
The mold came out perfect. Releasing the master was a struggle due to the overhung section at the bottom of the handle. I pulled about 4 or 5 resin castings before I started to notice some damage to this section which prompted me to re-think the design and create Ver 2.0 of the mold which I'll cover later.
Step 8: Casting in Resin
I almost exclusively use Smooth On products when it comes to molding and casting. They are simple to use and there is a wide variety available to suit almost any purpose.
I experimented with a number of resins for each of the parts, but settled on the following:
The barrel section was cast in Task 4 polyurethane.
This is specially formulated for thin sections with high levels of detail. It does have quite a long cure time, which is it's on inconvenience, but produced beautiful castings every time.
The magazine and handles were cast using Smooth Cast 305. This is more of a standard fast cast resin. It is widely available, easy to use and works incredibly well.
Both of these product promise bubble free castings, but I now will always pressure cast my resins. The mold and liquid (uncured) resin are placed into a pressure pot which is then pressurised. The pressure causes any air trapped within the resin to shrink drastically. As the resin cures, the air become trapped forever inside the solid resin, and you are left with a perfect casting.
Without the use of a pressure chamber I feel there would have been quite a few imperfections in the castings, which would need to be filled and sanded before painting.
Step 9: Revising the Handle Mold
Molding is an art form, and you never start learning, so re-making or re-working a mold is something you should not be ashamed of.
The first version worked, had I only wanted 1 or 2 copies, it would have worked perfectly, but I intended to make more copies, so I wanted a mold that was easier to release, and less likely to deteriorate.
First task was to slice off a wedge well below the overhang at the bottom of the handle that was causing the resistance during de-molding. I then reinserted the master and clayed up to bottom edge of the over hang, replace the mold box and poured more silicone.(I missed a picture or 2 here, but hopefully you can follow what I did?)
-- Image 1-2 --
I then set about removing the main body of the mold, piece by piece, cutting it away carefully with a scalpel. I made sure to keep the freshly pour silicone wedge in place as I did this. Once the silicone was striped away, so to was the clay. I made sure to re-insert the disc to the trigger so as not to lock the mold in place.
-- Image 3-6 --
I sealed the whole thing up again and then poured in some Mold Max 30 this time, to give me a bit more flexibility when de-molding. With Smooth On Silicone, the number generally refers to the Shore Hardness, the higher the number, the more rigid the silicone.
-- Image 7 --
You can see it came out perfect, leaving me with a 3 piece mold where the seam line are formed along hard, right angle edges, minimising the need for sanding. To de-mold I'd start with the top lid, breaking way the excess at the pour spouts, then I'd remove the bottom cap, break the vacuum around the handle by pulling the silicone away and then the casting would slide right out.
-- Image 8-9 --
Step 10: Painting the Barrel
Thanks to the wonders of modern 3d Printing Technology and supplier molding and casting product there was NO SANDING required on any of the resin cast parts!
All of the components were mounted on small plinth using a section of thread bar, this is so they could be picked up and placed down with ease. I paint 3 guns at once, 9 pieces in total.
To begin, everything was coated with Mipa 2K 4+1 Acyrfill Primer which is a High Solid 2 Pack Primer which needs a catalyst to cure. It is generally used in the automotive industry and needs to be spray through a HVLP Air Gun. Again, this is a system I have been using for a number of years now as it yield far superior control and durability of finish. A standard rattle can primer would suffice and could possible do just as good a job.
I did a lot of testing of paints and colour before I decided on how to paint the barrel section. I ultimately decided that I decided that I wanted the barrel of this to be chrome, but I was not going through the misery and turmoil of vacuum metalising, so I started looking for paint options.
Simon Murray has thought me almost everything I know about airbrushing, so he was my first ports of call.
After much testing I decide to go with Quicksilver Chrome from Createx Colors.
THIS STUFF IS INCREDIBLE!
- Water Based
- Straight from the bottle
- 3-4 light coats with an airbrush and it's done!
The first task was to give the part a few coats of 2K High Gloss, also from Mipa. This was tricky as I didn't want to over spray as the thickness of the paint could easily have hidden all those lovely details.
Blown away by how good this paint is!
The final task was to carefully paint the inside of the barrel with a little black, before dusting the muzzle with blue to give the appearance of muzzle burn.
Step 11: Painting the Magazine
The barrel and the handle was going to require a lot of masking, so I made sure to stock up on Tamiya Masking Tape, in my opinion t is the best on the market.
The parts were coated with Createx AutoBorne Black as a sealer before I hit it with my colours. I masked off the textured area so I could give it a coat of chrome. I wasn't concerned about the gloss chrome effect for this section as it will be heavily weathered. ( a couple of pictures are missing here, but I'm sure you get the idea)
I then used the Winsor and Newton Art Masking Fluid to mask off the textured area so I could coat the rest of the mag in Wicked Black in one easy pass. The liquid mask peels off in one go, it was a total game changer for this project.
Once everything was black and chrome it was on to weathering. I used multiple light washes of black, dabbing it away with a wet towel until I was happy with the result. Obviously this was done at the same time as the main body of the gun, so to achieve a similar weathering style.
Rare Earth Magnets were attached to the top of the magazine then embedded with resin. The counterparts to these magnets were glued to a small insert piece which was then glued to the inside of the handle.
Step 12: Painting the Handle
As before, everything was sealed with Airborne then coated with Wicked Black. Both these paints can be mixed with the High Performance Reducer to assist with a smooth even coat through an airbrush. Multiple light coats were applied with a Iwata Eclipse HP-CS which is what i currently use. Paint is dry to the touch in around 10-15 minute.
The first area masked was the trigger, so it could be coated with Quicksilver Chrome. Before I continued with the rest of the paint job, I designed a vinyl mask to stick on top of the trigger after it was painted, to protect it during the rest of the process. This was much easier than applying tape to what would be a rather difficult area.
--Images 1-3 --
The next challenge was the effect that appeared on the shroud at the top and bottom of the handle. Reference pictures and in game footage didn't really give a clear indication of how best to paint this section, so I did a bit of experimenting. My first thoughts was that it kind of looked like a grey.black camouflage, I used the Fluid Mask to blank off areas then sprayed them with a grey coat. This process was repeated multiple times, each time applying the mask in different areas and increasing the darkness of the grey paint.
When the mask was peeled away it looked HORRIBLE, but a light dusting of black paint, softened the effect and made it much more appealing.
-- Image 4-7 --
Further efforts saw me used different texture sponges to create a similar effect (which I ultimately preferred) I'll have some photos of this later on.
The liquid mask proved it's value when it came to painting the handle.
The grip imitates a Tsukamak wrap, it makes no sense, disappearing into the body and would be impossible to recreate in the real world. I used the liquid mask to cover the gaps between the ribbon, mask the body with tape and sprayed on a nice oxide red.
-- Image 8-10 --
The last on the painting was the weathering and the fine details. A few sections on the body require some masking. Tape was used to add the white accents to the side and front and chrome was added to the Crown detail by first spraying it with chrome, then filling it with fluid mask thru a syringe, the spraying it again with black before removing the mask.
-- Image 11-13 --
I mentioned previously that I wasn't entirely happy with the camouflage effect that I painted, so for my second attempt I used a texture sponge to apply different shades of grey and then dusted the effect with black from the airbrush. I much preferred this look!
-- Images 14-15 --
Once all the masking was removed it was just a case of weathering the handle and the textured section. This was done in the same manner as the magazine, in fact ti was done at the same time as the magazine to keep a consistent look throughout.
Step 13: Sealing an Bonding
As you probably gathered, I painted several guns at the same time, which was equally frustrating and enjoyable. It was great being able to try out different techniques, the worry that if I messed something up I'd need to starts ll over again was removed but it was extremely exhausting to repeat the masking 3 times over. In all, It took 3 whole days to paint all 3 pieces.
The last task was to clear coat everything before gluing them together.
The Barrel was sealed with a High Gloss 2K Lacquer from Mipa which really made the chrome paint pop! Naturally I had done some experimentation before hand. Chrome paint is very tricky, often a clear coat on top of chrome paint will dull the effect to a grey tone. With the Mipa lacquer, the chrome was only enhanced.
The handle and magazine were coated in a Matte 2k Laquer. I really wanted a harsh contrast between the barrel and the handle, so the matte finished helped achieve this perfectly.
The pieces were where bonded together using a 30 min Epoxy. Pads were placed in the clamp to ensure they left no mark on the surface. One of the biggest advantages of a 2K paint system is it's hardness and durability.
Step 14: Thank You
And that's all folks.
I really hope you enjoyed. If you have any question, please don't hesitate to comment or message me directly.
Thanks for you time.
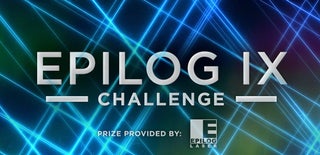
Participated in the
Epilog Challenge 9