Introduction: Easy Wood and Bone Jewelry
Are you in posession of one or more dogs that like to splinter large bones? Or maybe you have some leftover bones from a successful hunt? Many years ago I was scooping poop in a dog yard, and I was looking at all these small, interestingly shaped bone splinters the dogs had created, and decided to see if I could make some interesting jewelry. The process is easy and fairly straight-forward, and will yield an interesting and unique design for every piece.
In this instructable I will be making a pair of earrings, but for a first-time project I would recommend something larger, like a necklace.
Step 1: Tools and Materials
Tools
This is a quick list of only the necessary tools, feel free to complement with any power tools or similar
- a small saw
- a rough wood file
- sandpaper ( I use from 40 grit and all the way up to 1200 grit)
- pencil
- wood oil (Danish oil works perfectly)
- glue (You'll want a strong type, I've found epoxy, like Araldite, works great
- A hammer, axe, or a dog with strong jaws to break the bones
- (optional) Wood stain
- (optional) Wood wax
Materials
- Legbone from a big mammal
- Wood pieces
- Copper/brass/gold wire, or jewelry hooks from a local hobby store
- (Optional) Leather for necklace-straps
Step 2: Making the Pieces, and Glueing Them Together
The main feature of these necklaces and earrings is the natural and irregular shapes, and the best pieces for this come from the legbones, the strong, hollow ones. If you have a large dog who's used to eating bones, their chewing will often produce nice pieces (given that they don't eat the pieces, of course). If not, then an axe or big hammer will do the same trick. The pieces should ideally be less than 1 cm thick, if not they can end up being very "chunky" when you add the wood.
The wood can be from anything. If you're making this for someone special, maybe a slice from a tree from a place that means a lot to them, or just scrap pieces from other project. In this tutorial I will be using scrap pieces from a birch burl I picked up once that has these wonderful dark points running through it. These pieces should as well be no more than 1 cm thick. I usually sand them down to about 5 mm.
At this stage you'll want to sand the contact side of the wood and bone so that they are completely flat. With the bone I always use the inside, and on this occasion I cheated a bit and used a Dremel to wear it down first, and then flat against a piece of wood to make it completely flat, as pictured. I use 40 grit sandpaper, as it's rough enough, and also leaves small grooves in the material that gives the glue something to stick to.
PRO TIP: To check that the contact sides are completely flat, put them together and hold them sideways up to a window or a lamp. If they are not completely flat, you'll see the light coming through.
Once you are satisfied with the fit, glue the pieces together, let them dry and let's move on to the shaping!
Step 3: The Shaping
This is where most of the magic happens. Start by removing most of the excess wood. A small drag-saw, like the one pictured in the "Tools"-section, works perfectly, or a rough file. If there is any excess glue around the edges, remove this with a sharp knife. It makes it easier to see how much material to remove afterwards.
Next, notice the different angles on the bone pieces. You want to transfer these angles to the wood, creating the look of a single piece. It doesn't matter what kind of tool you use for the grinding, personally I use either a Dremel or a small coarse needle-file. Start with the biggest sides, and then move around the piece until all the sides have been covered. Along the way you'll want to keep an eye out for any gaps between the wood and bone, and keep removing material until the gaps disappear. In this step I also adjust the thickness of the wood, depending on how the piece feels and looks.
So far so good! Coming up, we have what most people refer to as "The boring part". PRO TIP: Find a good movie, and the time will fly!
Step 4: Sanding, Staining and Oiling
The sanding is, in my eyes, the most important step in this instructable. It can be done very quickly, but if you take the time to do it properly, the wood will really shine. The grits I use are 40, 60, 80, 100, 120, 180, 240, 360, 420, 600, 800, 1000 and 1200. (Most of the photos in this step have had the brightness and contrast slightly adjusted, to show off the drawings in the wood better)
Pro Tip: When sanding, switch directions between grits, i.e. start sanding left-right, then next paper sand up-down, then left-right again. This makes it easier to see where you have sanded, and also where you need to sand more.
When I'm sanding I like to take time and make sure I erase all marks made by the previous paper. For these earrings I won't bother sanding the bone (I like the natural look), but sometimes it looks good to smooth it out and sand it as well. When you get halfway through the sanding (240 grit in this case), I recommend to either oil the wood or, as I did, stain it. Doing this at this stage will make sure that you leave a bit of color or oil deeper in the wood, bringing out the depth in it better.
After the stain or oil has dried, continue sanding until you reach a smoothness you are happy with (If you stain it, be careful with the first paper so you don't sand everything away). I realized after I while that I was out of 1000 and 1200 grit papers, so I had to stop at 800. Make sure the wood is dry and dust-free before you give it a good helping of oil. Leave it to dry overnight, and lets move on to the next step!
Step 5: Finishing Touches
Once the oil has dried, and you're satisfied with the result, it's time to make these earrings hang. There are many ways of doing this, and I've chosen to do this as simple as possible, mostly because I haven't got the proper tools for soldering, nor the skills. The thing to consider though, is how the piece is going to hang. You'll want to consider both which end is the heaviest, and also how the piece looks. It will hang and move better if the heavy part is the lowest, but for the earring on the left, I chose to have the biggest part at the top because it would look better when paired with the other one.
At this point I would also add the wax, if you're using it. If not, grab another movie and rub the piece you're working on with the palm of your hand. This is not necessary, but it will give the piece a nice shine.
And that's all there is to it! Thank you for reading, and good luck crafting!
Step 6: (Optional) Making a Leather String for Necklaces
This step is completely optional, but I figured I'd show it, because I think leather goes really well with the natural look of the wood and bone. In the pictures I will only show the the technique itself, and not the completed string with a necklace.
To start, you'll need some leather, the thinner and more flexible it is, the better. Choosing leather that has little flexibility or making the strip too wide will make it harder to twirl, so keep this in mind when choosing.Start by cutting a strip no more than 5mm wide, and ideally longer than you need. Then split the strip down the middle, but leave a small bit uncut to keep the piece connected. Then, grab a safety needle, your favourite TV show, and plop down in a couch.
What you're doing here is essentially twirling and crossing, twirling and crossing, until you get to the end. Grab a piece of string in between your thumbs and index fingers, and start twirling the strings anti-clockwise. Once you're gotten them twirled together, put the string in your left hand over the string in your right. Twirl the strings again, then put the left string over the right string again. Keep doing this until you get to the end, then tie a knot.
Voila! Here's a quick and simple string who's uses are only limited by imagination.
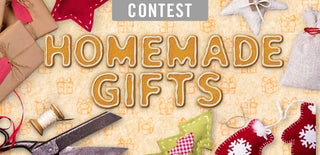
Participated in the
Homemade Gifts Contest 2015
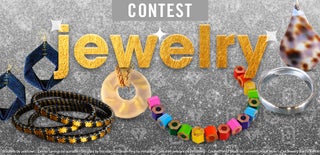
Participated in the
Jewelry Contest