Introduction: Electric Unicycle Upgrade
Electric unicycles have to be the most bizarre but interesting Personal Electric Vehicles (PEVs) around. The same technology that keeps Segways upright is used to allow people to zip along on a single wheel.
I was lucky enough to find a second-, or maybe even third-, hand electric unicycle nearby. After taking it apart I realised the plastics were not structural and so I could easily 3d print a new shell. Here I show you how I took a $500AUD product, added lights and an extendable handle, which allow me to use it safely at night and avoid having to carry it when not wheelying along.
Supplies
3D printer (CR-10 mini was used with a bed of 220x300x300mm)
2.5kg PETG filament
200g flexible (rubberised) PLA filament
Electric unicycle (Motorlife)
4 x 220mm M10 bolts with nuts
4 x 50mm M10 bolts and nuts
1 x extendable handle (Pack and Roll Trolley Cart from Office works)
2 x 24v headlights
2 x 12v sidelights
1 x on/off switch
1 x 5A fuse
1 x fuse case
12 x electrical connector blocks
Electrical connectors & wires
Soldering iron & soldering wire
Red nail polish
Step 1: Strip the Original Unicycle
Remove all parts from the Motorlife electric unicycle plastic shell (apart from the rubber leg pads) whilst also taking note of the orientation on the main circuit board.
Please note – even when the battery is disconnected many of the capacitors remain loaded and can rapidly dissipate their energy if a short between the terminals is created (as I found when a stray screw did just that resulting in a loud electrical crack and the gyro requiring to be reset).
Step 2: 3D Print the Parts
Below there is a list of the 3D printed parts and what they do:
1 x Top shell (main shell component holding most of the electrical parts)
1 x Electrical side shell (one half of the middle shell, which houses the main unicycle circuitry)
1 x Battery side shell (one half of the middle shell, which houses the battery)
2 x Bottom bracket shell (the shell components that are secured to the unicycle)
2 x Light spacer (8mm spacer that locks the LED spotlight into position)
2 x Nut lock (a plastic spacer that locates over a main nut and prevents it from unwinding)
2 x Rubber lock (a rubber cap that covers a main nut and prevents it from unwinding)
2 x Rubber stopper (a rubber cap that prevents the nut lock lifting)
4 x Nut landing (a replaceable landing shoulder for the main nuts)
1 x Bolting tool (a plastic socket used to tighten the main nuts in a confined space)
3D print all of the component parts. Please note that this could be a whole Instructables article on its own, the main 5 shell components took a combined 86 hours and 2.5kg of PETG plastic to print, not including all the failed prints of which there were many.
My main recommendations are:
I created this from PETG, however, Nylon would be my preferred material if I didn’t 3D print in such a humid climate.
Use a 0.6mm extruder or larger.
Print a 1.8mm minimum wall thickness.
Use 25% minimum infill.
All parts should be printed upside-down to minimise support material.
Print 2 x Rubber locks & 2 x Rubber stoppers in Flexible PLA plastic. These parts should be considered as disposable as it is likely they will get damaged on removal.
Attachments
Step 3: Create the Lighting Circuit
Please refer to the lighting diagram I have provided.
To prevent having to step down the voltage on the lighting circuit I linked 4 x 12-24V lights in series directly to the electric unicycle 65V battery. I added a 5A fuse for safety in case of a short circuit and an on/off switch so that the lights can be switched off when not required.
Please note- test the lighting circuit for an extended period (such as 1 hour) to ensure that no light overheats in such a way as to melt the PETG surroundings. I did this before disassembling the spotlights as their metal cover acts as a heat sink so that I could feel for the heat with my hand.
Once you are happy that the circuit is safe it is time to create a circuit to suit the shell. Disassemble the two LED spot lights and remove the LED circuit boards. To do this you have to cut the wires or remove the solder. Once the circuit is free, connect a red and black wire to the cut terminals.
To tap in to the electrical circuit, splice a line from both the positive and negative ends of the unicycle circuit nearest to the battery terminals. Add connectors to mate with the lighting circuit. Connecting in this way allows the lighting circuit to work in parallel with the motor circuit which provides a constant source of power for the lights without disturbing the motor electronics.
Step 4: Shorten the Extendable Handle
Remove the extendable handle from the Pack and Roll trolley.
To remove the handle, the pins holding the black plastic handle in place must be separated by forcing them apart. Once the top handle is off, the legs can be threaded out of the bottom of the box.
The extendable handle from the Pack and Go trolley can be installed without modification, however, it will stick out the top of the Unicycle by around 125mm. It is best to cut it to length so that the handle is supported/protected by the top shell when retracted. Disassemble the parts as much as possible without damage. Using a saw, cut a notch in the lower section of the leg to allow the removal of the plastic stopper. Cut the ends of the 2 upper, the 2 lower sections and the 2 inner button shafts by the required length to shorten the handle. Replace the plastic stopper parts, that you have removed, back into the bottom sections. Drill pin holes on the upper sections for securing the plastic handle. Assemble the handle and try it out, then test the handle on the printed shell. Please note – The legs must be threaded through the underside of the top shell and orientated correctly so that the pins match up with the corresponding location holes in the shell. Then the handle with button shaft should be installed from the top. If the parts are cut incorrectly, the pins on the leg stoppers may not locate in the corresponding holes. This will prevent them from being activated in the conventional manner. It is always advisable to test this prior to gluing the bottom stopper in place.
Once you are happy the handle mechanism works smoothly at each (top, mid and bottom) section, hot glue the bottom stoppers in the lower leg sections.
Step 5: Reinstalling the Bling
Install the chrome battery light indicator covers and then the battery light indicator circuit. Install the Unicycle on/off button and secure with its threaded washer. Hot glue the battery light indicator and the on/off button washer to prevent it backing off.
Step 6: Adding the Must Haves
Insert the lighting on/off switch under the handle, this should click into place. Install the charging port, also under the handle next to the on/off switch and secure with the threaded washer (take note which direction the notch is for ease of connecting to the charger). Hot glue the washer in place to prevent it backing off.
Step 7: Which Way Is Forward
Although this unicycle can be used in either direction, I always preferred to go in the direction that allowed the curved tyre inflation valve to pass any object reducing the risk of it jamming. On my unicycle, I have therefore placed the extendable handle on the left when the red light is at the rear.
One of the spot light lenses requires to be red to act as the rear light. Using red nail polish, paint the rear side of the lens including inside the cavity where the LED will reside.
Install the side lights to the top shell by inserting the wires through the hole and using the nuts and bolts provided with them. Insert the spot light lenses in to position. Now insert the LED circuit board with the LED inserted into the back of the lens and slide in the 3D printed light spacer. Apply hot glue to the spacer to hold it in position.
Solder/connect the components as per the lighting circuit diagram provided.
Please note - you do not have to have all the components arranged as per the diagram. However, if all components are arranged in series, it should not overload any one light or miss out any essential part of the circuit such as the on/off switch.
Step 8: Assemble the Sides
Install the two metal protective covers on the inside of the side shells using the original screws. Bend the metal if there are any restrictions or obstructions. Secure the side shell together using the 4 x M10 x 50mm nuts and lock bolts.
Step 9: Complete the Top Shell
Hot glue the unicycle circuit board in to the top shell so that it will slip into the electrical side shell on assembly. Make sure that it is in the same orientation as it was in the original shell, as this part holds the gyroscope which keeps the unicycle upright and working like a Segway. Install the extendable handle into the top shell and lock it in its mid-point position.
Step 10: Assemble the Bottom Brackets
Insert the M10 x 220mm bolts through the bottom bracket shells so that the head is flush with the bottom plate and then, using the original 12 x screws, secure the lower shell brackets to the unicycle frame.
Step 11: Build Up the Middle Section
Slide the side shells over the bolts making sure the bolts locate in the grooves. Install the battery in to the battery side shell.
Reconnect all the electrical components leaving the battery connectors last.
Slowly slide on the top shell making sure the bolts go into their respective holes and that no wiring gets pinched between the shell parts.
Step 12: Complete the Build
Drop a nut landing over each bolt (making sure it is located in the hole with the pyramids facing down), then install the nuts and tighten them using the bolting tool.
Drop the nut locks onto the nuts on the battery side of the unicycle making sure that the nuts are orientated to insert into the nut locks bottom cavity.
Install the rubber locks over the nuts under the extendable handle and the rubber stoppers over the nut locks.
Step 13: Say Hey!
Let me know what you think or get in touch if you are thinking about doing the same.
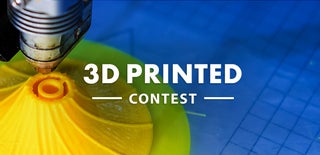
Participated in the
3D Printed Contest