Introduction: Extend Suction Cups Application With Custom Brackets. I Made Them at TechShop.
Background:
Suction cups are used in many applications. To extend its application, we need to design a bracket that could hold the suction cup and then interface the bracket with another connector or surface. Suction cups are cheap but not all places sell them. At Family Dollar Store near my location, they cost 3 pcs for a couple of dollars. A more reliable source is the Florida ebay seller 1megadeal. He sold them 24 pcs for $7 with shipping included.
To illustrate how to make a suction cup bracket, I searched for a very common real-world problem and solve it.
Problem:
When cars get old, window glass system could start to fail and normally we could assume that vehicle warranty for that is way passed. Either new car or old car, the repair of Window glass INOP or Fall Off are equally expensive. The dealer could charge over $300 per window. Normally, if the window is not on the Driver Side Front Door, vehicle owners would be very hesitant to pay for the high cost of repair. Taking out of door trim require knowledge of the door trim fastening system and proper removal tools. The door clips might require replacement as well or they could break during the removal and reinsertion. In some old vehicles, the Side Air Bag could be on the front doors. Professional non-dealer mechanics would be very hesitant to attempt it. For same reason, non-expert should never tamper with them to avoid accidental deployment, injury or wrong deployment during an actual side crash. Live could be at stake if warning are not followed.
A cheap alternative is to seal the window glass so it won't fall off. Most people uses duck tape or packaging tape to hold up the glass. These create very unpleasant look and tapes leave marks and glue residues that are very hard to remove. Overtime, they sagged and caused high and untolerable wind noise.
Solution:
A better way to hold up the window glass is to use suction cups. A suction bracket need to be designed.
Remove the suction cup metal wire. Create the bracket design in Autodesk Inventor. With some measurement and a few trial and error, it could be accomplish fairly easily. The prototype and final parts could be printed on MakerBot 3D Printer.
Normally, it would take about 4 to 6 suction cups to hold the window glass for a couple of months. When it starts to slip, just pull out the suction cups, pull the window glass up and reseal it. The reason you need a bracket is because the rubber weather gap is wide enough for the suction cup to get 'swallowed' below the rubber seal and potential create more trouble.
I made the width of each bracket about 1.5 inches wide so to distribute the load along the window sill. Another approach would be to make them about 8 inches wide that could use 3 suction cups to even out the load on the plastic door trim at the door sill. I think either way would work. I have chosen to print 6 pcs of the 1.5" wide brackets.
I round the edges with 1mm radius everywhere. This would avoid any sharp corners for human safety, marks on the door trim, sharp contact with the glass, keep dirt from entering the gap and sharp contact with the suction cup neck.
If you have friend that need them, this would be priceless gift. Please comment and place as your favorite if you find the window bracket useful idea. I am entering this intructables and hoping to catch more attention. Please help tweet so we could get out the idea to people in need.
Lesson Learned:
I just got the suction cups from the FL seller. The shape of the back end is different from that sold at Family Dollar Store.
So before making any 3D printing, obtain your suction cup from the FL seller. They are less clear but the suction cup is softer and the suction force is stronger.
Due to the heat from vehicle parked under the sun and combined with compressive load, the prototype warped out of shape. Picture will be added later.
Additional Note:
Always use 100% fill for final parts whenever material strength is required.
Suction cups are used in many applications. To extend its application, we need to design a bracket that could hold the suction cup and then interface the bracket with another connector or surface. Suction cups are cheap but not all places sell them. At Family Dollar Store near my location, they cost 3 pcs for a couple of dollars. A more reliable source is the Florida ebay seller 1megadeal. He sold them 24 pcs for $7 with shipping included.
To illustrate how to make a suction cup bracket, I searched for a very common real-world problem and solve it.
Problem:
When cars get old, window glass system could start to fail and normally we could assume that vehicle warranty for that is way passed. Either new car or old car, the repair of Window glass INOP or Fall Off are equally expensive. The dealer could charge over $300 per window. Normally, if the window is not on the Driver Side Front Door, vehicle owners would be very hesitant to pay for the high cost of repair. Taking out of door trim require knowledge of the door trim fastening system and proper removal tools. The door clips might require replacement as well or they could break during the removal and reinsertion. In some old vehicles, the Side Air Bag could be on the front doors. Professional non-dealer mechanics would be very hesitant to attempt it. For same reason, non-expert should never tamper with them to avoid accidental deployment, injury or wrong deployment during an actual side crash. Live could be at stake if warning are not followed.
A cheap alternative is to seal the window glass so it won't fall off. Most people uses duck tape or packaging tape to hold up the glass. These create very unpleasant look and tapes leave marks and glue residues that are very hard to remove. Overtime, they sagged and caused high and untolerable wind noise.
Solution:
A better way to hold up the window glass is to use suction cups. A suction bracket need to be designed.
Remove the suction cup metal wire. Create the bracket design in Autodesk Inventor. With some measurement and a few trial and error, it could be accomplish fairly easily. The prototype and final parts could be printed on MakerBot 3D Printer.
Normally, it would take about 4 to 6 suction cups to hold the window glass for a couple of months. When it starts to slip, just pull out the suction cups, pull the window glass up and reseal it. The reason you need a bracket is because the rubber weather gap is wide enough for the suction cup to get 'swallowed' below the rubber seal and potential create more trouble.
I made the width of each bracket about 1.5 inches wide so to distribute the load along the window sill. Another approach would be to make them about 8 inches wide that could use 3 suction cups to even out the load on the plastic door trim at the door sill. I think either way would work. I have chosen to print 6 pcs of the 1.5" wide brackets.
I round the edges with 1mm radius everywhere. This would avoid any sharp corners for human safety, marks on the door trim, sharp contact with the glass, keep dirt from entering the gap and sharp contact with the suction cup neck.
If you have friend that need them, this would be priceless gift. Please comment and place as your favorite if you find the window bracket useful idea. I am entering this intructables and hoping to catch more attention. Please help tweet so we could get out the idea to people in need.
Lesson Learned:
I just got the suction cups from the FL seller. The shape of the back end is different from that sold at Family Dollar Store.
So before making any 3D printing, obtain your suction cup from the FL seller. They are less clear but the suction cup is softer and the suction force is stronger.
Due to the heat from vehicle parked under the sun and combined with compressive load, the prototype warped out of shape. Picture will be added later.
Additional Note:
Always use 100% fill for final parts whenever material strength is required.
Attachments
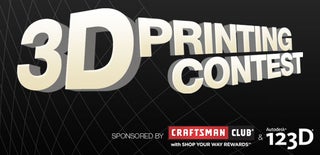
Participated in the
3D Printing Contest
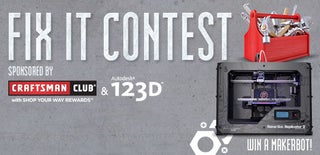
Participated in the
Fix It Contest