Introduction: Finishing Walnut Box With Integral Hinge
I have had an unfinished wooden box hanging around my workshop for years, I moved house three years ago and it's been in both houses, so I guess I started it a year or two before that.....so it was definitely time to finish it.
I abandoned it as there were various mistakes all over the box and I wasn't quite sure how to fix them all and didn't have enough motivation to finish. I had tried to fix part of it before (around four years ago) but that didn't go well so left it alone again.
Now I have more years woodworking experience I have a better understanding of how to fix problems/cover up problems/make design features out of problems, so I was determined to finish it this time.
It is/will be a walnut box with large box joints, a drawer at the bottom and integral flush wooden hinges. Part of my downfall before were the hinges, there is very little information about these hinges and I don't recall seeing ones with flush hinges either.
**Having looked back through my Instructables I found a photo of it part finished in my 'Building a yew coffee table' which I published in January 2014.....so more than six years ago. I would have only been woodworking a year back then.
Step 1: Things to Fix
The things I needed to fix
- Hinge recesses - these were not uniform and poorly done
- Gap filling - there were gaps in the main box joints all over
- Wood covering - the wood behind the drawer was not finished well
I also needed to make some new hinges as the recess would be a different size
Step 2: Enlarging the Hinge Recesses
As the box had already been assembled enlarging the recesses wasn't as easy as it would be on a flat bit of wood. Normally I would use a router table so the widths and distance from the edges would be the same top and bottom.
I started by clamping the main box to by workbench and added a straight bit of wood to the rear to act act as a stop. I then used another bit of wood to act as a fence so I could route a line, then move the fence along bit by bit until I had made the recess the right width. I then did the same to the other side so they were both equal.
I then went on to the lid which was a little harder as the recesses needed to match up exactly with the main box, once I cut these I had to go back to both the main box and lid to make tiny adjustments to both until they were as similar as I could make them.
Step 3: Making Wooden Hinge
I used some Ash I had to make the hinge so started off planning/thicknessing the wood to the correct thickness followed by rip cutting them to the correct width.
I then used a pillar drill to make a hole for the steel rod I was going to use in the hinge. It took multiple times to set this up, but drilling before making the wood in to a hinge saves the hassle of ruining a hinge if it all goes wrong later on.
I the used my crosscut sledge to make the finger joints on the two parts of the hinge making sure the cut depth was the same as the thickness of the hinge. I then used a belt sander to round over the edges and curve the outer corners.
Step 4: Tidy Up Lid and Glue Hinges
Having been on the floor for four/five years there were a few large dings to the top of the lid I needed to sort out. I got the iron out and got some wet kitchen roll, place the wet roll over the dent and heated it up with the iron. I did this a couple of times and this seemed to bring the dent back to the surface. I have used the technique before and it always surprises me how well it works (it's great for wooden kitchen worktops)
I then cut the shape on the lid and added a fillet to the front and sides of the top face followed by some sanding to the inside face of the lid and the top of the box as these wouldn't be easily sanded once the lid was in place.
I followed this by gluing and clamping the hinges in to place.
Step 5: Disguise Poor Joints/workmanship!
Next I tidied up some of the other parts of the box. There was a bottom to the box which slotted in to place but wasn't really held with anything, as the faces of the wood were a bit poor too I thought I'd stick some bits of wood over the ends and the base to cover up the rubbish faces and to hold the base in place.
I filled some of the larger gaps with the pointy end of some wedges and made a paste of sawdust and glue to fill the smaller gaps.
Step 6: Finishing
Once all the gaps were filled and the hinges dry I sanded the whole box to 240 grit using a random orbital sander.
I then applied a coat of hardwax oil to all the surfaces.
Step 7: Finished
All in all I am quite pleased with the final result as I wasn't sure how well it would end up. The filled gaps don't look too bad and I like the hinge a lot, it looks pretty cool being flush with the lid and back.
Let me know what you think.
Thanks for reading!
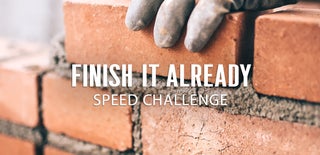
Second Prize in the
Finish It Already Speed Challenge