Introduction: Foam Prop M-358 Talon From Mass Effect
I recently did my first cosplay at New York Comic Con this year. I had several requests for a tutorial on how I did my foam prop that went with my costume.
After hearing about how they were being very strict with props this year, I decided I wasn't going to risk bringing my wood-built Talon. I also didn't want to just go with my armor, without a prop... the props really add that extra touch to a costume! To that end I decided to try throwing together a foam version that would pass prop-muster.
This was a last-minute decision. I first heard about the strict prop policy on Friday, and was going to the con on the Sunday. So I started this project at 10PM on Friday night, and finished about midnight on Saturday! With a few hours to eat and nap, it was about 20 hours end to end.
I've never done a tutorial before, but here goes! :)
P.S. Forgive the quality of the photos, they aren't always the best. Also, there are a few bits of which I have no photos, because I wasn't particularly thinking about doing a tutorial at the time - so didn't document as much as I maybe should have. ;)
Step 1: Materials
The materials list for this build is not too terribly long...
- 1 x Harbor Freight foam floor mat
- 2 x 9" x 12" x 6mm Craft Foam Sheets
- ~4" of Vinyl Bead Molding
- 3 1/2" of a 9/16" Wooden Dowel
2 1/2" of 3/4" outer-diameter cardboard tube
(inner diameter fits the wooden dowel)- DAP Weldwood Contact Cement
I also used a little Crazy Glue (cyanoacrylate) and hot glue in a few spots, though I could've used the contact cement.
- Performix brand Plasti-Dip spray-on rubber coating
- Rustoleum spray paint (colors as desired)
- Brown, black, orange, umber and a touch of red acrylic paint
- Scotch BLUE Painter's Masking Tape
- Rub'n Buff Wax Metallic Finish
Step 2: Tools
There weren't a whole lot of tools involved in this build.
- Heat gun
- Standard self-healing cutting mat
- Dremel rotary tool with the 1/2" sanding drum
- Snap-off knife
- Smith's Pocket Pal knife sharpener
- Scissors (for cutting out the patterns)
- Straight pins (for pinning the pattern onto the foam while tracing it)
If you've never built with foam before... well, the sharpener is a VERY important tool to add to your toolbox!
I don't know why, or how, but the foam will dull a steel blade in no time flat! You will want to sharpen your blade after every 4 or 5 linear feet of cutting. If you don't keep your blade sharp, it will start to catch on the foam and tear it instead of cutting it. This will leave you with messy edges that need to be cleaned up later.
Step 3: Initial Layout
This build was based off of plans done up by Sorenzo Props, and available in his Etsy store here. I did have to print them out at 120% scale though. From originally building the piece in wood, I had already played around and knew that as drawn, the gun would be way too small for my hands. Through trial and error of printing it out and putting my hand up to the print-outs, I knew 120% was the right scale.
First job was to cut out the pattern to trace on the foam. I cut out the very outer line of the pistol except for the chamber (inside the hollow area at the top).
The core of the build was two layers of the floor mat. I traced the shape on one piece, then cut it out, leaving about an inch margin around it. I then took that piece and glued it back to back to the mat again to make the double thickness. I glued the textured sides of the mat together, so that the outside would be flat and not need to be sanded off.
Then simply cut out along your tracing. Be careful to keep the knife perpendicular to your cutting surface, so that the edges of the piece are flat, not angled. ... unless of course the piece in question requires an angled face.
Step 4: Adding Cut-out Layers
The next step I did was to cut out the inset areas on the top handle piece, and on the sides of the back of the gun, above the grip.
For the pieces in the top handle, after tracing them out, I shallowly cut the outline with my knife, and then sliced it in laterally from the top of the gun, to make the inset. I rushed a bit, and didn't do a very good job of keeping the blade straight. It's hard to tell though once it's painted unless you look closely.
The long inset groove above the grip, after tracing out with my Sharpie, I used the sanding drum on the Dremel to run from end to end. I was able to use the radius of the sanding drum to measure and control the depth. Then I just had to clean up the corners with my knife.
The little inset right above the grip was done just with some brute hackery with the knife (after tracing it out).
Given that these bits required a lot of little cuts, it was especially important to keep the blade very sharp during this phase!
At this point I also did some beveling and rounding using the Dremel. You can see this in these photos... the back of the top handle bit has a simple bevel along it's edges, while the top of the gun above the grip is completely rounded over. Additionally I removed thickness from the trigger to make it thinner, like an actual trigger. These bits were all simply free-handed based on reference images.
Step 5: Adding Built-up Layers
The next step was to add the layers which are built up from the base layers. This was achieved by cutting down the pattern as in Punished Props' video linked at the end of this instructable. This step especially requires some intimate knowledge of the piece you are building, and is where your reference material will come in very handy!
The panel-line details were added using a handy technique (different from the one used when building with MDF shown in Bill's video). Trace the lines where you want to have those panel breaks. Once you know where they go, score them lightly with your craft knife... they don't need to be too deep. I scored mine to a depth of about 1/8". Once you have all your lines scored, go over them with your heat gun. I find it works best on the high setting. When you hit the seams with your heat gun, they will open up and make beautiful faux panel lines!
After gluing these layers on, I used the Dremel to bevel and round all the various edges as indicated on the reference drawings. In this case it includes all the bottom edges of the gun, as well as the back edge of the layer in white. You can see in the picture here also where I started shaping the grip.
Step 6: More Bits and Bobs...
The bead molding was cut out and glued in place below the rear end of the top handle bit.
Shaped the barrels. These didn't come out great, but the build was rather crunched for time, so I didn't worry about it too much. I rounded out the barrels by taking the Dremel with the sanding drum and running it around the outside of each barrel... essentially a sort of "inverse lathe" effect.
I haven't started adding actual lighting to my props yet, (wouldn't have had time even if I were), so I added the Mass Effect-standard lights on the side of the body using the same technique as the panel lines. The light itself eventually just got painted with a very bright red paint.
The last bit was the chamber. The cardboard tube was beveled on the ends and had a little piece cut out of it to approximate the reference material. After slipping the dowel into the tube, the bottom of them was sanded flat so they would sit snugly. The combined unit was glued in place in the top of the gun, behind the main barrel.
Step 7: Priming
Priming is definitely one of the easiest steps in the whole build.
The first thing you should do (which due to lack of sleep, I forgot on this build) is to heat-seal your piece. Basically, this just involves running the heat gun back and forth over all the foam. As you do so, you will notice the surface of the foam take on a different texture. Basically it is melting shut many of the small holes on the surface of the foam, making it less porous, allowing the PlastiDip to stick better.
Once you've got the whole thing heat-sealed (which doesn't take long), it's time to put it under PlastiDip! Basically PlastiDip is a spray on version of the rubber found on tools, like on the handles on a pair of pliers. Spray outdoors if possible, and away from the wind, or make sure to work in a well ventilated area. Read the labels. Give your piece several thin coats... that way you will avoid runs (something I'm still working on - lol). I find the hardest part here is usually making sure to get all the little nooks and crannies.
NOTE: Rustoleum makes a similar product, called FlexiDip. I tried it once, but found it to be very thin and it did not provide good coverage. It is entirely possible that I got a bad batch, but for the time being, I'm sticking with PlastiDip.
Once you've got a nice, dry coverage of PlastiDip, move on to.....
Step 8: Painting!
Once you prime your piece with the PlastiDip, it will take a sudden leap forward in terms of its quality. It goes from looking like what it is... a bunch of glued together foam to a single, unified piece.
However, once you start painting it is when it really starts to look like something cool!
Painting is pretty straight forward. The most important part here is to be meticulous with your masking tape. The better you do your masking, the cleaner your paint job will look. For pretty much all the colors of the object itself, I stick to the Rustoleum Painter's Touch series, unless I want metallic finishes. Though I still stick to Rustoleum sprays.
Using masking tape and masking paper, I first sprayed on the beige color. After letting that dry, I masked the black areas of the grip, the fore-grip and the black details around the barrel, chamber and on the sides. The area above the grip I did in a metallic gun-metal color.
While the Talon is usually painted in black and white, I opted to do this one in colors that matched the Blood Dragon armor I was carrying it with.
Once all the basic colors are blocked out, you can then go in and do the details. The stripes on the top handle and finger guard are in a red instead of the yellow, again to go with my armor. To do the stripes, I masked the edges and simply brushed on some Testor's model paint.
For the "T-7" label on the side, I cut a stencil out of masking tape. Once applied in place, these also were just hand-brushed on with Testor's model paint.
You can also see in the second picture here the painted-on light on the side, in front of the T-7 stencil.
Step 9: Weathering
This step still scares me a bit when I get to it... before I start. It always, however, winds up adding a lot to the piece! You've now got your finished and freshly painted piece in hand. Paint is all clean and pristine, ... looking like it just rolled off the manufacturing line. This is all fine and well, but usually you want your piece to look like it's seen some action, ... lived a little life!
There are two basic steps to this effect... one is dirt and grime, the other is wear.
To do the dirt and grime I use the acrylic wash process. In a medium sized, flat plastic cover or tray, I squeeze in some globs of black, brown, maybe some oranges, and a even a little red for this piece. What additional colors you use is up to you, and can give effects of the piece having lived through different environments. Reds and oranges for a planet like Mars, maybe greens and purples for some sort of marsh environment like Dagobah. Who knows - the sky's the limit!
I then take a medium-bristled brush - neither too hard nor too soft, dip it into some water, dab it into the colors, and then wash this over the piece. You want to try to get the darkest bits into all the corners, cracks and crevices. This will simulate accumulated dirt in places that are hard to clean. Do not try to make the color uniform. Have blotches that are more black, other spots that are more brown, others of other colors.
Once you've washed over the surface and into all the cracks, take a paper towel and wipe most of it off all the surfaces. You should now have a nice accumulation of crud. It didn't wipe off this piece too well, I think because the spray paint hadn't had time to fully dry and was still slightly tacky.
I like to leave a few spots where I don't wipe it fully off the surfaces... especially with a little color. This will simulate a grease or oil that stained the surface and does not easily clean off.
Step 10: Weathering Part Two... Wear
This is one of my favorite parts of the finishing steps! Break out your Rub'n Buff (RnB) metallic wax finish. There are techniques to do this also with silver paint pens instead.
Before you get started with this, be warned and be careful! Use only a TINY, tiny bit of RnB at a time! A little bit of this goes a long way! You can get a good effect applying it with either your finger, ... or I've also recently started using some sort of little make-up brush (I THINK they are eye-shadow brushes, little foam tips about the size of a cotton swab). I don't like cotton swabs though, because I find they tend to pull apart. How you apply it though really is personal preference and what works for you. If you've never used Rub'n Buff before, definitelyexperiment on some scraps before applying it to your piece to get the hang of it.
Look over your piece, and try to imagine its day-to-day life. Imagine as it gets rolled over on a battlefield, or jostled in a crowd, thrown in a packing crate, or tossed on a work bench, imagine where it would rub against things and where paint would rub off. Usually these will be edges and high spots. Experiment with application. Corners would get extra worn. Experiment!
One of my best applications of RnB was on a casting by Quantum Entanglement Props which I painted up (the red and black pistol above). I had put my sprays on a bit heavy and wound up with a run. I sanded the run off, but then instead of repainting it, I simply applied RnB over the scuffs from the sanding. The result was a very natural looking scuffed corner!
Just like with the acrylic wash, don't make it uniform. Make some lightly worn edges, make one or two really heavily worn spots. That will give it a more natural feel.
Step 11: Finish... and ENJOY!
Now that you've got everything painted, weathered and worn... you've got one final step!
Make sure to give your piece several coats of a clear coat finish. This will lock in all your painting efforts and keep them from wearing off too quickly.
If you're going to a con, you may want (or need) to throw an orange tip on the barrel. I used two pieces of orange electrical tape to do mine. I put one piece on, sticky side out. I made it tight enough so it wouldn't fall off... and by putting the sticky side out, it will be able to be cut off later without damaging the paint. Then, just to keep it from collecting dirt, I put another piece on over that one, sticky side in.
Now that you're all safety-set, you're ready to throw on your armor, and head out to take on the Reapers!
ENJOY!!! :)
Step 12: Additional Resources
This build would've been a lot more difficult without the help of some additional resources.
My whole prop-making hobby got kicked off by watching this video by the amazing Bill Doran, of Punished Props! He provides some very valuable techniques, while also showing how easy it can actually be to get started with this craft!
For splendid reference images of almost every weapon and character in the Mass Effect series, you can't beat deviantART user Troodon80! The one for the M-358 is available here.
You can follow my builds and work on my Facebook page, Dark Channel Props.
Thanks for reading! :)
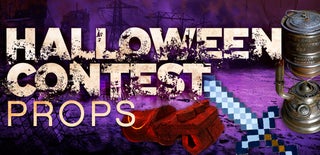
Participated in the
Halloween Props Contest