Introduction: Hammered Silver Agate Pendant
In this tutorial you will learn the process to make a hammered silver pendant with a bezel set stone. This project is great for beginners and will cover a lot of silversmithing skills such as: soldering; texturing sheet silver; stone setting and oxidising using liver of sulphur.
I love making pieces that are all rustic and hammered (I guess they are a bit like me in many respects haha). This is different from my usual clean style, but hammered jewellery can be very forgiving and fun to make.
Eye catching statement necklaces like this are sure to attract compliments to the wearer making them great products to sell or give as gifts.
I hope you learn a lot from this tutorial, if you like it and want to see more tutorials then you might like to subscribe to my Youtube Channel:
Supplies
Blue Lace Agate
The star of the show for this pendant was a stunning Blue Lace Agate cabachon. Not only was the stone gorgeous but it was also my favourite shape for a cabachon (almost tooth shaped!).
Silver Sheet
For the backing plate of the bezel setting I used a piece of 0.7mm sterling silver sheet but you can use thicker if preferred. I buy my sheet silver from Cookson Gold:
https://www.cooksongold.com/Sheet/-Alloy=Silver_Sheet/-Thickness=0/-Type=0/&prdsearch=y
Fine Silver Bezel Wire 5mm x 0.3mm
This Fine Silver Bezel Strip, also known as bezel wire, is traditionally used for making Rubover or or Cabochon settings. This fully annealed strip measures approximately 5mm wide x 0.3mm thick and can also be used to create flat rings and short cylinders without the need to pierce from larger sheet.
Step 1: Cutting the Bezel Wire
The first step was to determine how much bezel wire I needed to wrap around the stone. To do this I cut a strip of paper (around 5mm wide), wrapped it around the stone as tight as possible and then glued the overlap down with a glue stick (classic Prit Stick).
This left me with a paper hoop that when I snipped with the scissors was the perfect length of bezel wire for the stone.
I laid the strip of paper out onto the bezel wire and used a pencil to mark a line where the end of the strip was. Next I used a wire cutter to snip the piece of bezel wire off.
The wire was the perfect fit for the stone so the next job was to solder it.
Step 2: Soldering the Bezel Wire
You'll see from watching the video of the project that I was unsuccessful with my first soldering effort on this ring so I thought I'd skip right to the method that worked!
I mixed up some soldering flux with a borax cone and dish until it had a nice gooey consistency.
For this join I decided to use Hard silver solder as it has a higher melting temperature than Easy solder. This meant that when I soldered the bezel to the plate later on I could use the Easy solder and not melt the Hard solder on this join (I hope that makes sense).
I wrapped the bezel wire around the stone and made sure that both ends met perfectly to form a tight seam. Then I applied a small amount of flux to the seam.
I put a small piece of hard solder on to my soldering block and then placed the seam of the bezel wire to rest on top of it. As I heated the piece with a soldering torch the flux caramelised and created a capillary effect which pulled the solder into the seam.
Thank you to Andrew Berry from At The Bench for that technique!
Step 3: Cutting and Texturing the Back Plate
With the bezel soldered it was time to cut a backing plat for the pendant. To do this I pushed the stone into the wire so it would retain it's shaped and played around with laying it down onto the silver sheet.
When I had a rough idea of how it would sit I used a pencil to mark a line on the sheet and then cut the section off with my jewellers saw.
Next I placed the stone onto the newly cut sheet and traced it's outline with a pencil onto the sheet. This gave me an idea of where to texture the sheet with a ball pein hammer.
I hammered the sheet until I was happy with the texture, being careful not to hammer inside the line I'd marked (I did hit it a few times but no big deal).
Step 4: Soldering the Bezel to the Backing Plate
Time for the fun part: soldering the bezel to the backing plate!
To start this process I laid out a sheet of 240 grit emery paper on my bench and sanded one edge of the bezel completely flat so it would sit flush with the silver sheet and create a good solder join.
Then I curled up a piece of scrap bezel wire and rested the backing plate on top of it on the soldering block. The idea here was to create some clearance between the piece and the soldering block so I could get heat underneath it with my torch. Some elegant jewellers do this with a Bunsen burner tripod and wire mesh but I had to use what was at hand in my crude workshop.
I brushed on a small amount of flux, got the bezel wire into place and put pieces of Easy solder on what would be the inside wall of the bezel.
To heat the piece I began with a single hand held torch and focused most of my efforts underneath the piece until the flux had fluffed up and caramelised. Then I brought in a second torch to really bring enough heat to make the solder run.
After a satisfying quenching I bathed the piece in a "Pickling solution" which is a light acid. Jewellers "pickle" just helps to dissolve the flux residues and clean off oxidisation on the silver after soldering.
I mixed the pickle with manufacturers instructions and left the piece in until it was clean.
Step 5: Shaping the Pendant
It was time to make this piece look like a pendant! I used a pencil it mark an outline of the shape on the sheet and used my saw to cut away the bits I didn't need.
The resulting shape was a bit rough so I refined it with a no.2 and a no.4 file ... it was really starting to take shape!
I also used the no.4 file to clean up the solder join on the bezel at this stage.
Finally I used a small drill bit to make a hole at the top of the pendant for a jump ring.
Step 6: Getting the Bezel to the Right Height
At this stage the walls of the bezel setting were just a bit to high for the stone so I used files and emery paper to bring them down.
It's best not to have the walls too high or setting the stone will be a nightmare, where if they are too small then there won't be enough metal to bend over the stone. It's all about finding that Goldilocks zone!
When the walls of the bezel were right I used some 500 grit emery paper to sand over the edges and seams of the pendant and I worked the back with a wire brush (I wanted the back to have a kind of rough look).
Step 7: Making a Jump Ring
To help this pendant hang from a chain I made and attached a simple jump ring to it. I could've spent time making a fancy bail but I think the jump ring fit the rustic aesthetic of the piece.
I wrapped some 0.8mm silver wire around the handle of a file to form a tight coil. Then I cut a straight line down the coil to liberate a few tiny rings (sorry about the camera angle here ... it was pretty impossible to film such dainty work on my own!).
I threaded the jump ring through the hole on the pendant and used pliers to close it up so the ends met and formed a tight seam.
The seam on the jump ring was soldered with Easy solder and pickled.
Step 8: Turning the Pendant Black
I wanted to give the pendant a weathered look and to achieve this I darkened it with a Liver of Sulphur soloution.
This "Oxidising solution" is readily available from most jewellery suppliers and was very easy to use. I simply mixed up a small batch following the directions on the bottle, made sure the pendant was clean and then dunked it in the solution for a few minutes.
This process is pretty cool as you can see the silver changing colour before your eyes ... though the Sulphur does make your workshop smell like farts. Probably best to keep the place well ventilated if you use this stuff!
I removed the pendant from the Liver of sulphur solution and neutralised it in a mixture of baking soda/water. I was left with a rather cool looking black pendant!
Step 9: Setting the Stone
I pressed the Agate cabachon into the bezel setting and it was a great fit (so great I couldn't get it out actually).
It was time to secure the stone in place by pushing the edges of the bezel over it. To do this I used tool called a bezel rocker (great name for a band).
Starting at the corners I pushed the bezel over the stone to secure it in place (the video explains how to do this in better detail than I can articulate it here).
After pushing as much of the bezel over with the rocker as I could I used a burnishing to to smooth over the edges of the bezel. After this stage the stone was secured forever (hopefully).
The final touch was to sand over the piece with a few grits of emery paper (500, 1200, 2000) to reveal the low spots in the texture and any tooling marks/scratches that give the piece character.
Step 10: Take Snazzy Photos and Give It Away
I have to say I really enjoyed making this pendant and I've already spent £65 on cabachons for future creations! Making hammered pieces like this is very fun and forgiving ... if they don't turn out perfect that just adds character.
My girlfriend loved the pendant and was happy to finally get some use out of that gorgeous agate she'd had for years.
What did you think? Feel free to leave a comment with any questions and I will be happy to help!
I hope you learn a lot from this tutorial, if you like it and want to see more tutorials then you might like to subscribe to my Youtube Channel:
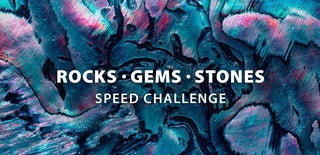
Grand Prize in the
Rocks, Gems, and Stones Speed Challenge