Introduction: How to Design a 3D Scale Model in Adobe Illustrator
This instructable has special tips for how to design a 3D scale model in 2D drawing software. I use Adobe Illustrator, but the same basic techniques can be used in Corel Draw, Inkscape or other vector drawing software. I use my Illustrator drawings to drive a laser cutter, which cuts the pieces that can then be assembled into a 3D scale model.
Step 1: Tools
1. Access to vector drawing software. I use Adobe Illustrator, but you could also use Corel Draw or Inkscape.
2. (Optional) Access to image editing software, like Photoshop, to prepare reference photos.
Step 2: Setup Your Document
The first thing you will need to do is create your drawing and organize your workspace.
Since I am designing a model that I will be executing using inches for my physical dimensions, I use inches for my drawing scale. I make the drawing 24" by 18" because that is the size of my laser cutter bed. You can also make this size match the materials you will be using, for example 12" x 12" plywood sheets.
I set the color model to RGB, because that is what my laser cutter recognizes (as opposed to CMYK, which is used for printing).
I turn on the grid and set the grid subdivisions to 8 because much of my work is done in 1/8" increments. For example, the plywood I typically use for models is 1/8" thick, so most of the slots I create are 1/8" thick. I make sure the colors of the grid lines are easily visible.
I set 'snap to grid' on, but I will be toggling this setting on and off frequently, so I know the keyboard shortcut for doing that (shift ctrl ").
I've created my own workspace that has the windows I most frequently use:
- Navigator
- Info (for reading the measuring tool)
- Align (for arranging shapes)
- Pathfinder (for creating custom shapes)
- Transform (for changing the dimensions of shapes)
And of course, the Layers window is essential.
Three colors will be used in my drawing: RGB red is a cut line on my laser, RGB Blue is a vector engraving line and RGB green is a line that I can use in my drawings but will not effect the laser. I use green for important references, for laying things out, and for 'virtual testing' which I will talk about later.
Step 3: Understand Your Scale
I am creating buildings for war gaming terrain. The miniature models I use for war gaming come in different sizes, but they average around a 1:50 scale. I like to translate that into some rough dimensions that guide my work. For example, and 8" long and 6" wide building is the equivalent of a 33' by 25' building - a good sized house! Each floor will be about 3" tall, the equivalent of 12' ceilings.
Understanding your scale will drive the selection of your materials, the tools required for cutting your materials, and the logical size of your drawing space and the models you design within it.
Step 4: Create Design Elements
The really fun part of designing a scale model is creating some of the design elements that will drive the overall look and feel of the model. For this example, I have decided to use an art deco flavor for the building. I look through online images of real buildings and also free clip art libraries to find motifs I like.
If I find a good black and white clip art image, I can use the image trace function to turn it into a vector drawing.
If I find a color photo of something I like, like this ornate door, I draw over it using the pen tool. I click around the image, making a very boxy version, and then I use the direct selection tool to select individual anchor points and smooth them into curves. I can fine tune the curves by moving the handles attached to each anchor point.
If I need a shape to be perfectly symmetrical, I draw one side of the shape, copy, paste and flip the copy, maneuver it into place so they touch, select both halves and use pathfinder to unite them into a single shape.
Once my elements are vector drawings, I can size them effortlessly to fit the buildings I create.
Step 5: Creating Basic Components
I usually start with my walls.
I prefer to create shapes like rectangles by clicking on the art board and entering the dimensions in the popup window. This way I know they are right. Then I move the shapes to lineup where I want them on the grid.
I like to use top and bottom tabs and grooves or slots where possible; I just think it is a cleaner look than the saw tooth corners many people use when creating laser cut models. Wood glue is what really holds a model together, it is stronger than the wood itself! The tabs are there mostly for alignment and registration while the glue is drying, and a few well-placed tabs and slots are all that's required. I try to hide them whenever possible.
Always measure the thickness of your construction material with calipers; don't trust that the nominal thickness is accurate. The 1/8" baltic birch plywood I use is remarkably accurate and consistent in its thickness, so .125", or one grid block in my drawing, gives me a very good fit.
To add bottom tabs to my wall, I create a rectangle that is 3/4" wide and 1/8" high. I make a second copy and place them where I want them. Then I select the wall and the tabs and use the pathfinder to unite them. This turns them into one solid shape. This is important, because the red line is a cut line on my laser, and if I don't remove the red line that separates the three pieces, I will get three pieces instead of one.
A 1/8" long tab will fit nicely into a 1/8" thick floor, but for the second story walls I want longer tabs that will project down through the floor into the first story walls below. The easiest way to lengthen a tab is to use the direct selection tool to select the two corner anchor points and then use the down arrow key to move them down. If snap to grid is on, they will both move down exactly 1/8" at a time. This technique is a great way to make adjustments: to lengthen or shorten walls, lengthen or shorten tabs. Snap to grid is very helpful, but if you need a measurement that does not fit the grid, toggle it off long enough to make the change, then turn it back on.
The slots on the top of the first floor walls are made in a similar fashion as the bottom tabs, except instead of 'pathfinder>unite' you use 'pathfinder>minus front' to cut the space out of the wall shape. For this to work, however, the slots must be 'above' the wall in the drawing. Expand the layers in the layer panel to see where the slots are and either move them above the wall in the layer panel or select them in the drawing, right click and pick 'arrange>bring to front'. In my experience, working in the layer panel is the easiest and most reliable way to arrange your drawing components.
Step 6: Do Virtual Layout and Testing
This is the most important tip I can give you about creating any complex design in vector drawing software: use your prior work as a reference for creating the next step of the design, and test the fit in your drawing before you create anything in real life.
The heart of this approach is to make alternate views - top views, bottom and side views - of parts you've already designed. I often make these views in green because they are references for me and not necessarily a part I want to cut or engrave. Then I pull these alternate views into other parts of the drawing to help me draw the next piece of the design, or I assemble them into larger parts to make sure things fit the way I expect. Doing this has basically eliminated my need for prototyping, as my designs almost always work the first time.
In this example, I make a bottom view of my tabbed wall. I always make the alternate views right next to the main view, so I can drag and stretch rectangles visually, with snap to grid on, without calculating or measuring dimensions or placement. (Basically, I trust my eyes more than I trust my calculations.) I make the view of the wall green, but I make the bottom view of the tabs red because I'm actually going to use them to cut the slots in the floor in another part of the drawing. I group the three elements of the bottom view and then copy and paste the group into a new layer where I will draw the floor.
I make four copies of the wall, rotate two of them 90 degrees, and then arrange them into a square with butt joints. Then I drag out a rectangle around the walls, leaving a 1/4" border on all sides. I make this rectangle red and my floor is finished, complete with eight red cut slots that are perfectly positioned for the tabs on the walls.
Even though I used four identical walls, the floor is not square - the butt joints make one dimension 1/4" longer than the other - but I didn't have to calculate to account for this; it happens automatically in the drawing because of this method. The placement of the slots is also affected by the butt joints, and overlooking this is the kind of mistake that is easily made. Using my virtual layout method is not only faster and easier, it is far more accurate.
Step 7: Making More Complex Shapes
While basic rectangles are the easiest to draw, they don't always make for an interesting design! You can modify your shapes using a variety of tools.
In my example building, the second floor has balconies. I created these by selecting the rectangle and using the reshape tool to bow out the side. Then I created a couple of rounded corner rectangles for the balconies and put them in place. After selecting all three shapes - the floor and the two balconies - I once again used pathfinder>unite to create a new, compound shape. Between the pathfinder tool, the shape tools, the pen tool and the direct selection tool you can create almost any shape you can imagine. As with most things, practice and experimentation are essential to learning what is possible and the easiest way to do your most frequent modifications.
One way to draw a more complex shape is to use the pen tool and draw over a reference photo, as I did for this church front, or as I did for the art deco door. This can be tricky if your reference photo is at an angle instead of straight on. In this example, I used Photoshop's transform functions to make the photo as square as possible. Even a badly distorted or incomplete image can be enough to inspire your design. The goal is to be inspired, not to necessarily duplicate the reference.
Step 8: Optimize Your Drawing
Sometimes, just getting a drawing to look right isn't enough. If you, like me, plan on using the drawing to drive a CNC machine like a laser cutter, you also need to care about efficiency. The parts of my house design that take the longest on the laser cutter are the engravings, not the cutting.
Each of the walls is covered with a brick design. The easiest way to draw the brick is to create a bunch of little rectangles, arrange them in a staggered brick pattern, and copy and paste them. This approach, however, is inefficient from an engraving point of view, because every line will be traced over at least twice. This will double the engraving time! So I drew the brick with single lines, not rectangles, grouped the lines and copied and pasted the groups. This is what I mean by optimizing.
It applies as well to the art deco floral design. It is very easy to get duplicate lines when using the image trace function - it creates outlines around the white spaces and the black spaces. After an image trace you need to un-group the drawing, select the white spaces and delete them. There is also a setting that tells image trace to ignore the white, and this has the same effect.
Every detailed drawing should be inspected for duplication and inefficiency, or you may be shocked when you take it to your laser cutter and learn how long it is going to take for your job to execute!
Step 9: An Example of Virtual Testing
In my Stained Glass Chapel, I had narrow facade pieces on the sides and a steeply angled roof. The size of my roof panels came from laying out side views in a drawing of the front, incorporating the butt joint at the top. One side of the roof is slightly longer than the other - this was derived through the virtual layout method. (I don't even know the math that would allow me to calculate this, because it is affected by the angle of the roof.)
I knew I had to create notches for the narrow facade panels to project up through, and I created 1/8" notches to accommodate them. But when I pulled those side views back in and arranged them, I saw that the pitch of the roof required deeper notches for clearance! So I used my direct selection tool to grab the notch and extend it to where the conflict no longer existed, and then I pulled the extended notch back into the roof drawing. I put it next to the existing notch and used it as a reference as I made each of the notches deeper. Finding this issue at this stage of the design saved me from needing to return to my makerspace and re-cutting the roof.
Step 10: Learn More From This Video
If you would like to see some of these Illustrator methods being applied, you can watch this video and pick up some more tips!
Designing scale models is a lot of fun, and it's even more fun when everything works right the first time! Try some of these methods, and let me know any improvements you come up with - I always love to learn better ways to do things!
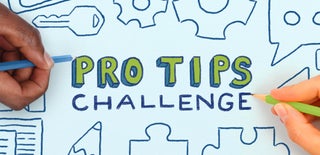
Participated in the
Pro Tips Challenge
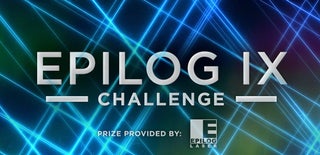
Participated in the
Epilog Challenge 9