Introduction: How to Make a 3D Printed Drill Jig for Dowel Joints
Dowel joints are a great alternative to biscuits or dominos for creating strong joints in woodworking. They also help keep larger glue-ups aligned and surfaces flush. While there are many drill jigs available to buy, I designed and 3D printed a simple jig with interchangeable inserts to drill perfectly centered holes. Read on, and I'll show you how.
You can watch the video to see how I designed the parts, or read on. All the parts were designed in Fusion360 and printed on the Monoprice Select Mini 3D printer in PLA.
STL Files are Posted here
Step 1: Begin With a Sketch
The first step in Fusion360 is to create a single sketch for the entire profile of the jig. I like using one sketch because it helps me to visualize the overall form of the object.
Start with the hexagon, using the polygon tool and set the distance between flats at 0.77". This is slightly oversized, and if the jig works well, I'll come back and make some aluminum inserts using 3/4" hex stock. I added a center hole 0.645" oversized to accept a 5/8" shank on the inserts.
The cylinders on either end are 0.40" in diameter and spaced 1.25" from the center. These dimensions are setup for the jig to accommodate stock up to 2 inches thick.
Once you're happy with the overall shape, exit the sketch and move on to creating the solid body.
Step 2: Create the Solid Body
To create the solid body, we'll extrude the sketch in three steps. Once you extrude the first profile, the sketch flips to invisible. To turn it back on, expand out the tree on the left side of Fusion360 and click the lightbulb to make the sketch visible again.
The steps I used are:
- Start by exturing the outer pins to 0.80" tall.
- Extrude the diamond shape at 0.40"
- Extrude the hexagon insert at 0.19" leaving a pocket that is 0.21" deep.
Step 3 will give a small clearance for the hexagon shaped inserts, which are 0.20" tall. Make sure you don't pull the circular hole along, too - we'll need a hole all the way through the jig to accept the inserts.
Step 3: Remove Excess Material
For the main part of the jig, we need the thickness to provide an adequate guide for the drill bit, but it uses a lot of material. The benefit of 3D printing, is it's really easy to cut out material we don't need for a functional part.
Create another sketch on the top surface of the jig, between the pins. Use the offset tool to bring the outside profile inside by 0.1". Repeat the same process to offset the hexagon outwards by 0.1". Finally, I added a rib across the center, partially because it looks good and mainly to keep enough surface area to provide a stable base when drilling.
Extrude all the pockets by 0.2", or halfway, through the solid to reduce the amount of filament needed.
Step 4: Finish the Edges
With the final shape created I like to come back around and dress up all the corners with fillets and chamfers. First I add fillets around any corners that are perpendicular to the build surface. These are the corners that the extruder will trace during the print. Then I add chamfers on all the corners that are parallel to the build surface. I find I get better looking results with chamfers than with fillets, but that's just an opinion.
Step 5: Add a Hole for a Set Screw
The final feature to add to the jig is a hole for a set screw. This is 0.11" in diameter and centered in on of the hex faces. After printing, I'll tap the hole to accept a #6-32 machine screw. This step is completely optional, but adds stability to the jig, and keeps the insert from falling out.
Step 6: Create the Inserts
Repeat the same process to create the inserts. I made 5 separate inserts for 1/8", 3/16", 1/4", 5/16" and 3/8" drill bits. The center holes are oversized by 0.02" to make for a smooth guide for the drill bit.
Critical dimensions for the inserts are:
- Hexagon Distance Across Flats: 0.75"
- Hexagon Extrusion Height: 0.20"
- Cylinder Diameter: 0.625"
- Cylinder Extrusion Height: 0.40"
- Center Holes: 0.145", 0.2075", 0.27", 0.3325", 0.395"
Step 7: Print It!
- Layer Height: 0.21875mm
- Shell Thickness: 2mm
- Top and Bottom Thickness: 2mm
- Infill: 50%
Step 8: Cut the Threads
With the print finished, use a standard metal tap to cut the threads for the set screw. I used a 6-32 socket head to secure the inserts in the jig. This is entirely optional. The inserts snap in to the pocket in the jig.
Step 9: Drill the Holes
To use the jig, set the hexagon side of the jig onto the surface you want to join. Twist the jig so that the pins make contact on both sides of the board, this is how the self-centering feature works. The hole in the insert will be perfectly centered as long as both pins stay in contact.
Put the drill bit into the insert before starting the drill, this will reduce the amount of wear on the plastic inserts. Use the jig to guide the bit. Repeat on both boards and you'll have perfectly centered holes to accept dowels. For me, I find the 1/4" insert gets the most use.
Step 10: The Finished Product
This was a fun project, and being able to create the tools I need has been really rewarding. I'm definitely keeping this one handy, and it's so easy to modify for whatever your specific needs are.
Thanks for reading!
-------------------------------------
You can also find me at:
YouTube (all my DIY videos)
Instagram (What I'm working on @greatlakesmakes)
My Website (Geek out on some engineering know-how)
Facebook (be my friend?)
-------------------------------------
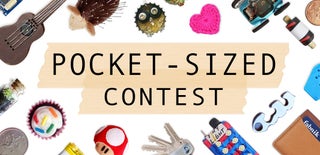
Participated in the
Pocket-Sized Contest