Introduction: How to Make an Among Us Costume
The video game Among Us has become incredibly popular lately, and I wonder if it is partly because of the super cute little armless astronauts who spend most of their time doing random jobs around their spaceship. Of course, you can't let their cuteness fool you, there is always an imposter in their midst!
My goal with this pattern was to try and capture some of the sweet quirkiness of the characters in an easy to build project, using really basic supplies such as interlocking foam mats and a hot glue gun.
Here are the tools and materials I used:
- Pattern : I used the one that I created. You can find it on my website. It includes 5 sizes to fit most people.
- 10 mm thick x 60 cm (24”) square interlocking EVA foam floor mats:
- Size M and L: 4 for the helmet and 2 more for the backpack
- Size S: 3 for the helmet and 1 more for the backpack.
- Size XS: 2 for the helmet and 1 more for the backpack.
- Hot Glue Gun (paid link): I highly suggest a glue gun that has adjustable temperature. If you use a temperature just a little bit higher than the melting point of the glue, you will have fewer burnt fingers, and not have to hold pieces together as long as they cool.
- Very Sharp Knife (paid link): If it is not really sharp you will have a terrible time when you are cutting the foam. I use a surgical scalpel or utility knife.
- Gluing Surface: A surface that you don’t mind getting glue on.
- Heat Gun or Blowdryer: Used for heating and forming the foam.
- Light Coloured Gel Pen: Used for any markings on the foam. If you use a ballpoint pen and then try to paint over it with a light colour, the pen ink will migrate through the paint and you will never be able to cover the lines.
- Paint: Artists acrylics are good paints to use, but I have also used ordinary house paint as well. If you want a really durable, long-lasting finish, I would suggest using a flexible paint, such as Plaid FX (paid link) paints.
- 2.5 cm (1”) webbing: Used to attach the backpack to the helmet.
- 2-2.5 cm (3/4"-1”) velcro: Used to attach the backpack to the helmet.
- Ruler
- Scissors
Please note, some of the above links are affiliate links, and I do get a small commission if you buy through these links. It doesn't cost you any more and it helps me out!
Step 1: Safety First!!
- Wearing the helmet severely limits your vision. This increases the chances of falling injuries or not seeing an approaching obstacle or vehicle. Be very aware of the activities you are taking part in so that you do not get into a dangerous situation. This helmet is not recommended to be worn by children unless under adult supervision.
- Some EVA foam contains a chemical called formamide. There are some people that say there isn't enough formamide in EVA mats to be harmful, and others that say there is. Do your research and come to your own conclusions. At the least, I would say it is a good idea to open your foam mat up and let it sit in the sun for a day or two, as most of the chemical will off-gas from the foam. Or buy foam that is labelled formamide free.
- Do not wear your helmet until all fumes from glue, foam, and paint are gone. The helmet is a fairly enclosed environment and you only have one set of lungs.
- Do not block off the face hole with glass or plastic. It is open to allow proper airflow for breathing. Closing it could cause suffocation.
- Sharp knives and hot glue can cause injury. Be sure to use in accordance with the manufacturer's instructions.
Step 2: Measure Your Body
Using a flexible measuring tape, measure around your body at shoulder level (including your shoulders). Be sure to include any clothing you’ll be wearing with the costume. This measurement will give you an idea which pattern size to print. There are 5 different sizes to fit most people!
Step 3: Printing and Taping
Print the appropriate pattern pages of the PDF for the size you are making. Make sure the scale is set to actual size or 100%. Most of the pattern pieces are larger than one sheet of paper. For these, line up the “+” marks and tape the sheets together. I find it is easier to line up the marks if I hold the papers up against a window so that the light coming through the window allows me to see through to the lower registration marks.
**Make sure the scale is set to actual size in the settings when you print.**
After printing, measure the print guides with a ruler to verify that they are the correct size.
Step 4: Trace the First Two Pieces
Use scissors to cut out the paper pattern for the helmet, just barely leaving the black line visible. Don’t cut on the curved dotted line for the face opening yet. There are also dotted lines at the bottom of the helmet pattern. These are reference marks if you would like to make your helmet a different length. Sizes XS-M all fit entirely on a standard floor mat with the longest length option, but size L and XL require cutting at one of the shorter lines if you are making it from interlocking floor tiles. I recommend making the helmet the longest length you can, and then shortening it later if preferred.
Place the paper helmet pattern piece on the foam mat and carefully trace it using your gel pen.
Wherever there are alignment marks or centre lines in the pattern, transfer them onto the foam, and once you lift your paper off the foam, extend that line inward and mark the letter so that it will be included once you have cut out the foam piece.
Trace the helmet piece a second time, flipping it over to create a mirror image of the first piece.
** Quick tip** If you trace right on top of the alignment marks while there is a sheet of foam under the pattern, it leaves an indentation in the paper. This is handy when you flip the paper, because then you know where your alignment points should go. You could also just hold the paper up to a window so you can see through it, and then transfer the marks to the back side.
Step 5: Trace the Last Two Pieces
You now need to cut out the face opening along the dotted lines of the paper pattern. Trace the helmet piece with the face opening once right side up, and once flipped over.
You will now have 4 helmet pieces traced on the foam, two with face openings and two without. Make sure the two sets are mirror images before you cut them out!
Step 6: Start Cutting!
Using your sharp knife, cut directly on the lines. If the cuts look rough, that means your knife is too dull. Either get a new blade or sharpen your knife. It’ll make a ton of difference. Also, you will get a better quality cut by cutting along the same line a few times with moderate pressure rather than trying to cut all the way through in one pass.
Cut out all four helmet pieces.
Remember to watch where your fingers are at all times and make sure you don’t cut them off!
Step 7: Heat and Form
EVA foam gets a little bit flexible when it is heated up, which is great because we are trying to create a rounded shape from a flat material.
Turn a blowdryer to it's highest heat setting, or a heat gun to one of its lower settings.
Heat one of the foam helmet pieces on both sides. Only heat in the central areas of the foam. You don’t want to deform the edges, so try to keep the heat away from them. This step requires patience as it takes a while for the heat to penetrate into the thick foam material.
Once the foam is heated up, use your hands to stretch the foam over your knee or another rounded object. The goal is to stretch the centre area, creating a convex surface in the foam.
Repeat this for the other three pieces.
Step 8: Get Out Your Glue Gun
I use hot glue for my projects now, as I am a bit leery of breathing the fumes that go along with contact cement. It takes a little more practice, but you can still get really good results. I like to glue a section about 5 cm long and hold it together until the glue cools. This time can vary depending on how hot your glue gun is, but for me, it is about 10 seconds. I really recommend using a hot glue gun with adjustable temperature, you can turn it quite low which saves your fingers from burning and also means you have to spend less time holding the parts together while the glue cools. If there is a long piece to glue, it is best to glue both ends so they line up properly first, then glue the rest of the seam in the centre. This reduces any errors due to the stretchable nature of the foam.
** If you do use hot glue to make your mask, be careful not to leave it in a hot car because the glue will melt, leaving you with a hot mess! **
Glue the V cutout on one of the back helmet pieces together. Glue a small section at the outside edge of the V cutout, making sure to keep the two sides lined up. Hold it until you are sure it has cooled. If you let go too early, the foam will spring apart and you will have to re-glue it. Once the outside section is glued, apply glue to the rest of the seam and then press down on both sides of the V cutout, squeezing the two sides of the foam together and creating a nice clean seam. Repeat for the second back piece.
After a bit of practice, you will get a feeling for how much glue to apply between the sides so that just a little squeezes out when the parts are pushed together. Once the glue has cooled, the squeezed out bit can be peeled or rubbed off of the seam.
Step 9: Glue the Back Pieces Together
Line up the two back pieces with the now glued V cutouts facing each other.
- Tack the points at the top of the back pieces together.
- Tack a small section of the bottom edge of the back pieces together.
- Tack a small section where the V cutouts line up on the back pieces.
Now that the two halves are held together in proper alignment, work along the seams, gluing about 5 cm at a time and holding the edges in place until they cool.
Step 10: Glue the Front Pieces Together
Now that the two halves are held together in proper alignment, work along the seams, gluing about 5 cm at a time and holding the edges in place until they cool.
Repeat almost the same process for the front half of the helmet:
- Tack the points together.
- Tack the top of the face cutout together.
- Tack the bottom of the face cut out together.
- Tack the bottom together.
Once it is all tacked together, finish gluing all the seams.
Step 11: Glue the Front to the Back
Now, stand the two halves up and line up all the top points. Tack the two halves together at the top. Tack the two sides together at the bottom on both sides.
Glue the rest of both side seams.
Step 12: Reinforce If Necessary
I am quite happy with the strength of my hot glue seams, but if you want to make absolutely sure they won’t pop apart at an inopportune time, you can reinforce them with some fabric.
Lightly sand the foam horizontally on the inside of the helmet along the bottom of one of the seams. Cut a strip of fabric about 2 cm wide and 7 cm long. (1”x3”)
Apply glue to the inside helmet where the strip is going to go and then lay the strip on top of the glue. Because I keep my hot glue gun set very cool, I can press the strip down into the glue using my fingers without burning them. If you don’t have an adjustable temp glue gun, you should use some scrap foam or something to press the fabric down onto the glue. To keep the edges of the fabric from fraying, apply a thin layer of glue all around the edges of the fabric strip. Repeat for any other seams you want to reinforce.
Step 13: A Ring for Your Head
Try the helmet on and see how it feels. You may be fine with how it works, or you may want it to be a bit more stable on your head. If that is the case, you can add a ring that goes inside the helmet and rests on top of your head.
Measure around your head and look on the pattern for the corresponding measurement. For example, if your head measures 57 cm you would want to cut on the two lines that have the 57 label on them. The solid line is the inside of the ring and the dotted line is the outside.
Trace and cut the ring from foam.
Glue it into the helmet at the top. I found it took a little trial and error to get the ring in a spot that felt right for me, so I would suggest to just tack the ring in place with a tiny bit of hot glue to make it easy to remove and adjust for the optimum placement.
The head rings can also be used to keep the helmet at the right height for your face. If the helmet is too low, just stack up more rings until it is sitting in the right place.
Step 14: Face-Hole Rim
Trace and cut the faceplate rim, being sure to mark the centre line.
Align the centre of the rim with the centre seams of the face opening and glue the rim in place, starting at the centre and working your way to the outside. You may have to stretch the foam just a tiny bit to get it to line up perfectly with the edge of the face opening.
Alright, that’s the helmet made! If you want to make the backpack, keep reading.....
Step 15: Start Making a Little Backpack / Oxygen Tank
I currently have two sizes of backpack to go with the helmets. One goes with the size XS and S and one goes with size M, L, and XL.
Print and cut out the two rectangular backpack pattern pieces that go with your helmet size.
I tried to save a bit of paper so you will find that the Backpack Main Piece is actually just half of the pattern piece. To get the full-size piece, trace it on the foam and then flip it over along the dotted line and trace it again to make a larger rectangle. That is the piece that gets cut out.
Once the Backpack Main Piece is cut from the foam, cut out the Bottom and Top piece from the pattern.
Trace and cut two Bottom and Top pieces from the foam.
Cut the Back Center Support from the pattern and cut one from foam.
Cut one Backpack Panel from foam. This will not be seen so it can be made with foam that doesn’t look so great. In a pinch, you could even glue a few scraps together to make a larger piece and use that.
Step 16: Glue the Ends on the Backpack
To make your life a little easier, it can be helpful to heat up and curve the two sides of the Backpack Main Piece before gluing.
Glue one of the pointy ends of the top piece to the side of the Backpack Main Piece.
Wrap the Backpack Main Piece all the way around the outside of the top piece until it gets to the other point.
Glue the other point.
Glue the centre of the top piece to the edge of the Backpack Main Piece, and then finish gluing that whole seam.
Repeat for the bottom piece.
Step 17: Add Support in the Centre
The backpack will still have a tendency to balloon out on the sides, so glue in the Back Center Support piece in the centre of the backpack. This piece will be glued with its edge 10 mm (the width of the foam) below the edge of the side. Tack each side and then glue the rest of the centre support piece.
The Backpack Panel piece is also going to help hold the sides together. Test that it fits inside the edges of the back of the backpack. If the thickness of foam you used was not 10 mm you may have to trim a bit off the top and bottom to get the right fit.
Glue the Backpack Panel piece into place, starting by gluing it to the Back Center Support.
Step 18: Add the Back Panel
The Backpack Panel piece is also going to help hold the sides together. Test that it fits inside the edges of the back of the backpack. If the thickness of foam you used was not 10 mm you may have to trim a bit off the top and bottom to get the right fit.
Glue the Backpack Panel piece into place, starting by gluing it to the Back Center Support.
Glue the top and bottom flush with the edges of the Bottom and Top pieces.
Glue the Backpack Panel to the sides of the backpack. Due to the inner curve of the backpack, these will not glue flush with the edge, so just make sure the glue gets into where the two pieces contact. Hold the edge of the backpack down on a table while waiting for the glue to cool. That helps give the backpack straight sides.
Step 19: Strap It Up
Cut two pieces of 2.5 cm (1”) webbing 20 cm (8”) long.
Heat the cut with a lighter to melt the end and keep it from fraying.
Make a mark 9 cm (3.5”) up the two webbing straps
Make a mark on the Backpack Panel 8 cm (3”) down from the top edge of the backpack. This will be the top edge of where the straps get glued on.
Make marks for the placement of the straps. On the larger size backpack, I spaced the straps 8.5 cm (3.25”) apart, and on the smaller one I spaced them 7.5 cm (3”) apart.
Sand the foam of the backpack below the 8 cm mark where you will be gluing the strap.
Line up the 9 cm mark of the webbing straps with the 8 cm line you made on the backpack and then glue the straps to the backpack. It is important to note that the 9 cm is the part that you glue, not the part that extends past the top of the backpack.
For extra strength, you can add extra glue around and on top of the straps as well.
Cut two 8 cm (3”) long strips of hook and loop fastener (the hook part) and glue or sew them to the section of the strap that is free. I find that some hook and loop adheres well with hot glue and some do not. It can be worth giving the back of the hook and loop a quick sanding before gluing, as well as gluing over the edges.
Step 20: Attach the Pack to the Helmet
Hold the pack against the helmet and determine where you want it to sit.
Make a mark at the top of the backpack on the helmet.
Measure down 8 cm (3”) from that mark, and that is where you will want the slots for the backpack.
Cut slots in the helmet the same distance apart as you spaced the backpack straps, and the same width as your straps.
On the inside of the helmet, sand the foam just above the slots and glue two strips of hook and loop fastener (the fuzzy side) extending vertically from the slots.
Work the backpack straps through the slots and secure them with the velcro to attach the backpack to the helmet.
Step 21: Painting Party!
Time to paint your creation! You can use whatever type of water-based paint you have handy, though you will get different durability depending on what you use. Paints such as house paints work, and I have used them more than once, but they are quite prone to cracking when the foam flexes. Next best are artists' acrylic paints; they cover well and are more flexible when dry than house paint. If you want your masterpiece to last a long time and be really durable, there are specifically made flexible paints out there. I have tried Plaid FX paints and have been quite happy with them. It seems to depend a lot on the colour you use, but across the board, they will be more flexible than standard artists' acrylics.
Step 22: Done.
You did it!! Now you can enjoy an awesome costume you made yourself:)
Thanks for hanging out with me!
If you'd like to see more of my projects you can find me here:
Subscribe to my YouTube Channel
Follow me on Instagram
Check out my Pattern Shop
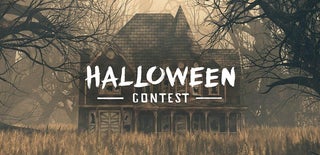
Runner Up in the
Halloween Contest