Introduction: Inlaid Multi-stone Cuff Bracelet
Inlaid stone is not as difficult as it looks. Flat pieces are much easier than the curved ones, so I hope to add an instructable on that type in the future, but in the mean time, try the bracelet. Silver is very forgiving and mistakes can be corrected fairly easily. A big part of getting started in lapidary work is the equipment. If you have it or have access to equipment, then the sky is the limit on what you can do.
Step 1: Basic Bracelet Form and Materials
I purchase most of my materials at Rio Grande https://www.riogrande.com/ They have the best prices and ship quickly.
Supplies: sterling silver 2"x6" sheet, 18 gauge, dead soft
1x3mm rectangle wire, dead soft
sterling silver half round wire #2 gauge
hard solder, easy solder, and flux
rubber cement, paper, spray sealer (even clear fingernail polish works)
assorted colorful stone slabs
lab grown ruby .5"x.5"x.4", dop stick and dop or super glue
pins with head bent over to hold framework
firebrick to pin frame on for soldering
330 epoxy
2 patterns of your design
You will need a trim saw, torch, and grinder such as a Genie or Pixie. If you don't have them, often a local club or college will have a shop. You will also need a pickle solution.
Step 2: Creating Chanels for the Stone
Although this looks complicated, it is not. It just requires a LOT of patience. My inspiration for the bracelet came from a necklace I had made. The necklace was flat and much easier to do because the curvature of the bracelet required adjusting some of the channels and stones. You can see that I made the bracelet stones more in line with the curve. I made my bracelet 2"x6" but you can down scale if you want a smaller one.
1. Draw your design on paper and cut the rectangle wire to match the lines. Gently bend and shape to fit pattern. Bend the top of straight pins over with needle nose pliers to form a "U" shape. Place the pattern on your firebrick and position the rectangle wire upright on the pattern. Push the pins into the fire brick and the "U" on the pin will hold the rectangle wire in a upright position.
2. Measure the outside of the sheet silver (bracelet) and cut 4 pieces of half round wire to make a frame around the outside of the sheet silver.. Make sure the curved edge of the wire is on the outside and the flat part is snug against the sheet silver. Flux and solder the wire together and to the sheet with HARD solder. Quench in water and place in pickle solution.
3. Flux and solder the design framework together with HARD solder. The paper will burn away. Quench in water and place in pickle solution to clean the silver.
4. Rinse silver and fit framework inside the bracelet frame. Trim if necessary. It is important to keep the ends of the channel flush at a 90 degree angle so they fit snugly against each other. A file works well to even the cuts. If the metal doesn't touch, solder will not fill in the gaps, so be careful to make every bit of metal touch.
5. Flux and solder the design framework to the bracelet sheet and frame with EASY solder. Once all the metal is attached, quickly quench in water and place in pickle solution again.
6. Rinse bracelet and form around a bracelet mandrel. Use a wooden mallet and begin at the end of the bracelet to make your curve.
Step 3: Shaping Stones
You can buy stones in slab form or cut your own if you have a saw. Make sure they are a little taller than the frame and framework of your bracelet because you will eventually grind and polish them flat. Using a copy of your pattern, cut out the individual shapes and glue them on your slabs with rubber cement. Make sure to number the paper pieces and your bracelet slots, so it you don't shape the wrong stone. A felt tip marker works well. Seal the glued on paper pieces with clear spray paint or clear fingernail polish. This protects the paper when you are grinding and polishing on wet sanders.
Trim the pieces as closely as possible on a trim saw and then use a wet grinder or stained glass grinder to do the final fitting of stones to the framework slots.
Step 4: Fitting and Shaping
All the slabbed or flat stones can be glued in with 330 epoxy. You want them to stick up a bit as in the photos. The ruby was adhered to a dop stick so I could form a dome because I wanted the extra dimension. I shaped polished it starting with an 80 grit wet wheel and stepping through 100, 200, 600, 1200, 3,000, 10,000, 12,000, and 50,000 grit wheels to get the high polish.
Step 5: Final Polish
The flat stones also went through the steps of 80 to 50,000 grit to get a nice polish. As you can see, the grinding and polishing process wore down the stones until they were flush with the silver channel framework. I buffed the sterling silver with a silver polish and then set the ruby with 330 epoxy.
Tip: If the framework isn't vertical, you can straighten it with pliers. If a piece breaks or melts, you can remove that segment and cut another piece and solder it where the broken one was. No stress....it is all just a matter of patience. :)
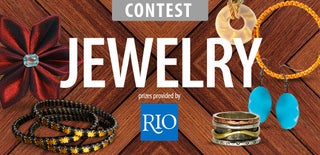
Participated in the
Jewelry Contest 2017