Introduction: Iris-Port for Safe Working Closeby (Covid-19 Corona)
During Covid-19 Corona the best way of preventing spread of the virus is social distancing. But often this is not simple. Specially if you are in a business where it's needed to come close to your customers. The use of plexiglas or glass walls can create a separation between you and your client, but it wont work if you have to use your hands to operate equipment or tools or simply need to touch the client.
This solution is inspired by medical Iris ports used in medical labs.
I work in an optician store in the Netherlands with optometrist, contact-lens specialists and opticians who have to work close to customers. I wanted to create an solution that works and is easy to make.
It is probably the simplest design i ever made but highly functional. It is designed with Fusion360 (files included in remix step)
Supplies
3D printer
Colorfab Ngen filament
Silicone plate 3mm thick 60 shore
Step 1: Printing the Rings
I used a Ultimaker 2+ and Colorfab Ngen material. The designs is maximized for printing on a Ultimaker 2. It exactly fits the platform. To be able to use the maximum dimensions i did not use any build plate adhesion settings, only glue! This works well with Colorfab Ngen with a nozzle of 0,4mm. Temperature settings Nozzle at 250 degrees and a build-platform at 90 degrees celsius.
I used a wall thickness 3mm filling 50% to make the whole construction rigid. This is important because of the silicone rings of the next step. The silicone rings need to be clamped very tightly between the printed parts otherwise they will get lose after some use.
Ring 4 is meant to be on the outside (customer side) The ring falls exactly in the opening in the plexiglass. I used 8mm thick plexiglass. If you use plexiglass of another thickness you need to increase or decrease the height of the inner ring. (files are included in remix step)
Step 2: Making the Silicone Disks
For this i used a silicone plate of 3mm thick shore 60. I used food grade silicone which is availible at local silicone sellers. I payed €80 for one square meter. I was able to make 7 complete ports from this.
The thickness and shore hardness is needed to prevent the flaps simply bending down. At 3mm and shore 60 the flaps keep standing up. These values are not extremely tight. Something between 2,5 and 3,5mm thick will work. Also the shore hardness between 50 and 70 will work. But a thicker plate and higher shore hardness will result in lesser flexibility.
We tried it manually (see picture). Simply use the included drawing to draw the dimensions on the silicone and cut it out with a sharp knife.
Step 3: Assembly
The opening in the plexiglas window is 104mm diameter. I made an wooden mold for an handmill and cutted out the opening. Please beware that the mill can cut a smaller circle then the mold. In this case you need to make the mold bigger to eventually end up with an opening of 104mm.
Assemble ring 1,2 and 3 together with the 2 silicone discs. Use 8 M3x30mm bolds and nuts (See exploded view and pdf drawing). 4 holes are still open at 90 degrees from each other.
The silicone disks need to be assembled 60 degrees rotated of each other (see picture)
Ring 4 is meant to be on the outside (customer side of the plexiglas). Ring 4 falls exactly in the opening in the plexiglass. Use 4 M3x40mm bolds and nuts to mount Ring 4 to the Assembly of ring 1-3
Step 4: Adjust/Remix
I Included .step and fusion360 .f3d files to use for adjusting.
Feel free to adapt to your needs. Plexiglas thickness can be adjusted in Ring 4.
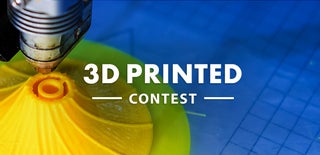
Participated in the
3D Printed Contest