Introduction: LOTR - Forge Your Own Elvish Ring
Hello fellow makers,
One day whilst browsing on Pinterest I came across an article on the makers of The One Ring as featured in The Lord of the Rings and The Hobbit movies.
In the article was a link to the site of the creators and best of all they have an English to Elvish translator!
I knew I simply had to make my own Elvish ring.
In this Instructable I will be making a hand forged silver bronze ring with a name and surname engraved in Elvish and topped off with a quartz crystal.
Although the project might look intimidating at first glance, everything was done using the most basic tools and if you don't have access to a CNC (inexpensive desktop CNC's will also work) I will also show you an alternative method to engrave on the ring.
Let's get started...
Supplies
To make this Instructable you will need the following:
- 3-4mm Bronze rod (I reused some from an old/failed project as you only need a tiny <10cm piece)
This can be found at your local hardware store in the welding/brazing section. I recommend using bronze when learning and then moving on to precious metals later.
- Quartz crystal
- Access to a CNC machine
- Silver solder
I recommend buying a kit like the one I linked as you will need the different melting temperatures for different parts of the ring, otherwise you can also use tin solder for the low temperature areas.
- a Butane/propane blow torch
- a Hammer
- an Anvil** (at $15 I highly recommend getting something like this)
Any piece of heavy metal with a smooth surface can be used, before I made myself this small jewellers anvil I used an old hammer head mounted in a vice and it worked great.
- Sanding paper (waterproof) around 60 to 400 grit and I would highly recommend a sanding sponge/block
- Metal polishing compound blocks
- Leather safety gloves
- Pliers
- Cutters
Optional:
- A Dremel
- Felt polishing pads
*As an Amazon Associate I receive a small percentage from sales made through provided links at no cost to you, this helps fund future projects.
Step 1: Translation:
First step is to generate our Elvish text to engrave.
I use the English to Elvish translator provided on the original LOTR ring creators website.
In order to engrave the text we are going to need a vector. To do this I took a screenshot of the generated text and cropped around it.
Next we need to convert the image to a vector, we can do this for free using Autotracer.
Step 2: Start Forging:
Safety first!
Always wear leather gloves and face protection when forging metals, the pieces can cause serious burns even after standing for a while. Always handle your metal as if it is hot.
Now we will need to start shaping our bronze rod.
For this ring you need a length of rod that is the circumference of your ring finger plus about 3cm more for the crystal clasp.
In the end I will forge around 10cm of rod to flat bar but I suggest you forge this length first before cutting off the excess as it will make handling it easier.
You can measure your ring size using a piece of string. Take the string and wrap it around the base of your finger, marking where the string first overlaps with a pen. Then, line that up with a ruler and take down its length
Now we need to anneal the bronze rod, with the butane/propane torch you need to heat up your bronze rod until it gets to a cherry red color and then quench it in a bucket of water (or if you are comfortable working with hot metal you can hot forge it without quenching first)
Tip: Pick a hammer that has a defect free head as all the scratches and dents from the head will be transferred to your piece.
When the rod has reached temperature you can place the rod on the anvil and start hammering it down on one side, try to keep your hammer head as flat as possible whilst moving across the rod.
While hammering you will feel the bronze getting harder, once you feel this happening you will need to reheat the rod as above.
Flipping the rod over from time to time will help keep it straight.
Keep repeating the above until you've reduced the thickness of the rod from 4mm to around 0.8mm.
Now you can reheat the rod and then place it on its side and gently hammer down the side to end up with a uniform bar that's approximately 5-6mm wide and 0.8mm thick.
Step 3: Cut It Down to Size:
When you're done forging you can cut off the length of bar needed for the ring and a piece for the clasp.
I used a diamond cutoff disk in my Dremel for this, try and keep your cuts as square as possible as it will make the soldering easier and your joints less visible.
Step 4: Prepping for Engraving:
In order to engrave the face of the ring we will need a flat surface.
I start with a coarse wet stone used for knife sharpening (these are the cheap $2 ones you don't want to use your expensive knife sharpening kit) but you can also use a piece of 180 grit sandpaper wetted with some soapy water and placed on a plane of glass.
Sand down the face that will be engraved until it is flat.
I follow up with some 400 grit just to get rid of most of the scratches.
Step 5: No CNC?..No Problem
If you don't have a CNC available to do the engraving you can follow one of my previous Instructables where I etched a ring using photoresist film.
Step 6: Engraving Setup:
Now we have our brass bar ready to be engraved and the vector so we can get to the fun part.
First you'll need to upload your vector file to your favourite CAM software to generate the engraving toolpath. I use a 15 degree 0.1mm engraving bit.
To test the gcode I used some leftover aluminium stock and ran the engraving process.
Now we can move the toolpath gcode to the CNC software and get to cutting.
Step 7: Engraving the Bar:
With everything on the software side ready to go we can fire up the CNC.
For small pieces like this I place some painters tape on the machines table as well as the back of the piece that will be engraved, then stick the piece onto the tape on the machines bed using some 2 part CA glue (superglue).
This gives us a solid vibration free mounting and is easy to remove.
I setup the piece so that it starts engraving from the centre, this just makes it easier to space the design out.
Zero your machine, add a drop of oil for a cleaner cut and let it go.
Step 8: Soldering the Ring:
Time to solder the joint.
First we need to bend the bar into a flat oval so that the two ends are together as flush as possible, now place on a suitable surface to solder on (I did my brazing on some ceramic furnace tiles)
Add silver solder flux and a small piece of silver solder (medium/hard) in the joint and start heating the joint with your butane torch.
When the piece reaches the melting point of the solder it will flow into joint.
Wait for the piece to cool completely.
You can now use a small hammer to start gently hammering it back into a circle, I like to use a smooth metal rod that I place inside of the ring and then hammer around it but you can also use the horn on your mini jewellers anvil.
Step 9: Refining:
Before adding the crystal clasp I decided to refine the ring by smoothing the sharp corners using a fine jewelers file and sanded away most of the imperfections using 400 grit sandpaper.
Step 10: The Crystal Clasp:
To mount the clasp for the crystal I started by filing the area where the solder joint is slightly so that we have a flat surface for the clasp.
Next I propped the ring up using a metal rod between two pieces of ceramic furnace tiles to make soldering easier.
Place the piece of brass bar onto the ring base, add flux and a piece of silver solder on each side of the joint and start heating until the solder flows into the joint.
If you use different temperature silver solders you will use the "hard" for the first joint and the "soft" for this joint as to not melt the initial weld.
Leave the piece to cool completely.
After cool I used a grinding stone in my Dremel to remove any excess solder and to refine the shape a bit.
Step 11: First Polish:
For the first polish we want to focus on the crystal clasp as we will not be able to polish it again after setting the crystal in place.
I started by cutting a slit on either side of the clasp using the diamond cutoff disk in order to have four thinner pieces that will wrap around the crystal.
Next I switched over to a rubber compounding bit to polish away any imperfections and burrs.
Then using a course compounding block and felt polishing bit I shined up the clasp area.
Step 12: Oops!
Whilst deciding on how to bend the clasp fingers to go around the crystal I bent the one a little too much and it broke off.
Luckily I could just grind away the leftover piece and make it three claws...
Moral of the story, plan your design beforehand and try to only bend once!
Step 13: Setting the Crystal:
With the fingers of the clasp bent upright I placed the quartz crystal piece into the clasp.
Then using a small hammer gently tap the fingers around the crystal being careful not to hit the crystal itself.
Continue taping each finger until there is no wiggle left from the crystal.
If you are worried about the crystal coming loose you can also add a drop of adhesive to the bottom of the clasp before inserting the crystal.
Step 14: Final Polish:
With the crystal in place it's time for the finishing polish.
I started with the coarse compounding block and a felt polishing bit and then moved down to medium and fine until all the scratches are removed.
As seen on the pictures I didn't want to sand and polish the edges of the ring too much as I wanted to keep the forged look.
You can finish off the ring with some liquid polish and a soft cloth to bring out that mirror finish.
Tip: If your engraving isn't very visible you can cover it with a black permanent marker, let it dry and buff off the excess using a soft damp cloth.
Step 15: Enjoy!
And that's it, now you can slip on your beautiful new creation!
I hope you guys find this Instructable useful and if you have any questions please feel free to leave me a message or comment bellow.
Please share your own creations with us by clicking the "I Made It" button below.
Happy making!
-
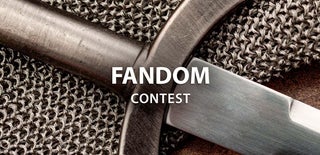
First Prize in the
Fandom Contest