Introduction: Laser Cut Colorado Heart Pendant
Sooo, I work at an Industrial Design Firm that specializes in Wood Stickers. They are pretty rad. I am the CLO (chief lazor operator) and I zap other things too. We zapped cheese the other day and zapped a pumpkin pie last Thanksgiving. When we were just a start-up we created jewelry and pendants, then the Wood Stickers took off. I still get a little time to create personal projects though.
The video really shows it all.
Let's get started.
Items Used:
- Cherry wood backer
- Wood veneers
- Rockler medium wood glue
- Jumprings
- Ball chain
Tools Used:
- Epilog Helix Laser
- Adobe Illustrator
- Sandpaper 320 & 400 grit
- Clamp
- Wood planks 2X2"
- Silicone sheet
- Masking paper
- Hydrophobic clear coat
- Jewelry pliers
Time Needed:
- 2 hours
Skill Level:
- High - laser and Illustrator knowledge needed.
Step 1: Crerating Your Design in Adobe Illustrator
I use Illustrator based on its ease of use and my familiarity with the program.
- I start with a heart shape, copy and paste a duplicate heart and expand one to fit over the other. Near the small heart inside of the large one and make sure they are centered perfectly. Select the outside heart shape and set your line width to .001, this tells the Helix that this is a cut line.
- Using the eliptical tool, create your holes for the jumprings. Set the line size to .001 copy (control C) and place it where you want the hole for your first jumpring. Now paste your other hole and place it for your second hole.
- Select the second heart and fill it with black, this is your raster area which will hold the veneers. Place your cherry wood plank on the laser and start your print dialog for your raster etch.
- Or just download the .AI or SVG files I included on this step.
Step 2: Creating the Cherry Wood Backer
I started with a milled sheet of sustainable cherry wood approximately 16" X 3" X 1/8".
I sanded it well, starting with a 220 grit paper and the 400 grit, for a really smooth surface.
- Place your wood on the laser and set up for the heart shaped etch. All lasers vary so you will want to do a test etch to be sure your veneer will fit flush once your etch is complete. Once you have found your desired depth, raster your heart design.
- Now, mask your plank with masking paper and cut (vector) your heart pieces out. The masking paper helps to reduce any burn marks the laser makes during the vector Cut.
- Place the plank on the bed exactly where you put it for the raster process. Enter the dialog for printing your vector files, send to the laser and cut out your shape.
- Next, we will need to sand the board to remove the sap and smoke trails.I use a 220 grit for this part.
- Blow all the wood dust off of your plank and apply your masking paper. Cut the paper so that it does not touch the ruler edges inside of the laser bed.
- Place the plank on the bed exactly where you put it for the raster process. Enter the dialog for printing your vector files, send to the laser and cut out your shape.
- Turn on your laser and air compressor.
- Press start on the Helix and watch the magic.
Step 3: Cutting the Wood Veneer
I used exotic wood veneers to mimic the colors of Colorado's flag the best I could.
Wood used:
- Ebony = Blue
- Spelted Maple = White
- Cherry = Red
- Maple = Yellow
Your laser should have a cheat sheet for your cuts, if not, a little experimenting is in order.
- Cover the front side of your veneer to keep the smoke from damaging it.
- Optional - Tape your veneer to a board to keep from losing your tiny pieces in the vector grid.
- Vector cut as many as you need and repeat this process for each color of veneer.
- Pull from the laser and remove the masking paper.
Step 4: Bonding Your Pendant Pieces
After cutting all of your pieces, it's time to finish your pendant.
I used Rockler medium wood bond for this process.
- Start with the top piece and spread the wood bond on the heart just under where this first piece goes.
- Repeat this process for each piece until you reach the bottom.
- I then take two silicon pieces and and sandwich the pendant between them.
- Now sandwich that part between the two wood planks.
- Clamp them together for ten minutes or so to assure a great bond.
- Now sand your pendant with a 400 grit sandpaper so that it is smooth to the touch.
- Once you are happy with the sanding, blow it off with compressed air and spray with a semi-gloss hydrophobic spray. I suggest three coats allowing dry time of ten minutes between each spray.
After your pendant fully dries, add your jumprings and chain - strut in style.
Stay tuned for more laser fun.
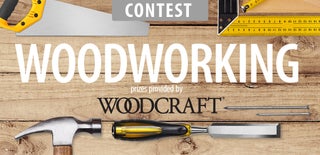
Participated in the
Woodworking Contest 2017
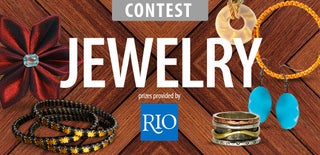
Participated in the
Jewelry Contest 2017