Introduction: Link's Master Sword From the Legend of Zelda: Hyrule Warriors
After hunting for good Master Sword replica tutorials, I found that most were done in wood (requiring expensive power tools and know-how) or were cheaply made from paper and tape. With conventions increasing their security restrictions, many replicas and fake weapons aren't allowed inside. Therefore, I created a sword that is cheap, durable, and couldn't hurt a fly. If you are making this for children, they can easily whop each other with it without causing any harm. The materials are easy to get, and many crafters will already have these items in their inventory.
The sword pictured here is my first attempt ever at carving foam. If you follow the instructions, you can find out how you can make yours look even better than mine as I will point out where I went wrong/what I learned while making it. The one pictured above also doesn't yet have its clear coat on, so it doesn't yet have the metallic sheen of metal. I live in a very cold city in the winter and it has been too cold to do any spraying outside recently.
*If this tutorial was useful to you, please vote for it! I always take the time to answer questions, so feel free to ask away!
Attachments
Step 1: Materials Required
- EVA foam floor mats - available for about $12 at Walmart for a set of 4
- Roll of thin foam - available at Michael's for about $10 (use their 40% off coupons)
- 3/8 in x 36 in (0.95 cm x 91.4 cm) dowel (available at Michael's for less than $1)
- Dremel - you will need coarse and fine sanding bits, and possibly a fine ball engraving tool
- Wood burner - with a wide flat attachment and a very fine point (optional)
- Heat gun - cannot be substituted with a hair dryer (highly recommended, but optional)
- Contact cement - I use LePage brand, but Barge is also a well-known brand (available at Home Depot)
- Goop glue or another suitable glue for foam - available at Walmart, Michael's, and Home Depot
- Exacto knife and extra blades
- Knife sharpener (highly recommended) - available at Walmart for $20, but will save you money!!
- Large cutting mat (I only had a small one which was really tough to cut on)
- Flexi Dip/Plasti Dip - black or grey is recommended (about $15)
- Acrylic/spray paints and a variety of small art brushes
- High gloss protective spray - Krylon Crystal Clear spray works well (available at Michael's)
- Masking tape
- Dust/respiration mask and goggles
- Scissors
- Pen/fine marker
- Newspaper
- A copy of the pattern (download the pdf file attached above)
Step 2: Blade
- Print the pattern.
- Tape the blade pieces together (you will need to cut the end off of one of the papers to tape it to the other).
- You need to cut 2 of these. 2 pieces will fit on one foam sheet. Pin your pattern to THE WRONG SIDE of your foam. Pictured above is the pattern on the RIGHT side of the foam.The reason for tracing the pattern on the wrong edge is because it is very easy to not cut a perfect 90 degree angle. The edges of the sword glued should be cut perfectly, while the right side will be shaved down to make the sharp edge. I made this mistake and realized after that my edges weren't perfect and would therefore make an uneven blade edge.
- With a very sharp blade, cut out the blades. If your blade doesn't cut like butter, it is too dull. The edges of your foam should cut smoothly and shouldn't rip at the foam.
- Trace the middle line on to the wrong side of your foam on both pieces starting at least 2 inches from the tip all the way to the bottom. Use a dremel to carve out the space you will need for your dowel, making sure not to go all the way through your foam. You will notice my lines aren't so straight. To make your line precise, hold your foam and dremel firmly - otherwise it will stray slightly. Test the fit of your dowel before gluing.
- Put contact cement onto the wrong sides of your foam (including the space you carved out) and your dowel. Once the glue is dry, press your dowel down on one of the pieces and sandwich the other foam piece down on it. Press them together well (I sometimes stand on my pieces to squish it together well).
- Trace the inside line of the blade onto the sides of the sword. Use a dremel or sandpaper glued to a paint stick to create the angled edges. The tip of the sword should have edges that slant and meet at the tip – and then the outside edge can be carved to make the edge that does from the center of the middle to the tip of the blade. Use reference photos for assistance. The middle line around the tip on the pattern isn’t perfect, so round it out by hand. The squared sections at the base of the blade should be tapered, but not formed into a point. Leave about 2-3mm of an edge on them.
- Trace the emblem onto the blade (you can cut it out in parts to trace it). Using a very fine dremel point or a very fine wood burner point, carve the emblem into the sheath. This is where I made another error. I was thinking that the Flexi Dip would fill the groove I made if I went too small with the wood-burning tip. However, Flexi Dip dries super thin and doesn't seem to fill in any details at all. Therefore, you can use a finer tip and get much better results. I used a soldering bit to carve the detail, but that was much too large and made a bumpy appearance.
- Leave the bottom of the blade untouched so you can fit it to the cross guard perfectly.
Step 3: Cross Guard
This was the most difficult part for me to engineer. At first I tried to carve the whole thing out of one piece, but that was impossible and didn't give great results. By creating it in pieces, you get much sharper edges. You can also see in my image that it looks a bit rough. This is because I didn't use a fine grit sanding bit with my dremel. You can have MUCH nicer results with sharper edges with a smooth dremel bit. I am currently working on Link's shield, and the fine bit makes ALL the difference!!!
- Trace all of the lines of the crescent piece 2 times onto foam. Cut them out, making sure your blade is very sharp in order to get the most accurate lines. The tight curve on the square part of the cross guard is difficult to cut, so you can cut straight across and carve it out with your dremel easily.
- First we want to taper the edges of the crescent to form them into points. The ends are points and the middle is thickest. Hold the pieces sideways. Hold a pair of scissors at an angle and make a 2cm cut from the bottom corner of the crescent towards the center of the crescent, ending your cut at the top.
- For the carving, you can either choose to use a coarse sanding bit on your dremel first and then clean your edges with a fine bit, or work it completely with a find sanding bit. Use a fairly low speed for shaving.
- Hold your dremel at a 45 degree angle. Starting with the inner edge, shave the 45 degree angle needed until you read the drawn line. Next, hold your dremel at a 45 degree angle pointed down. Line up the edge of your dremel bit with the next line and shave the next edge, meeting with the one you just made. Work on the next edges in the same fashion. If your dremel is flicking the tip of the crescent, hold the piece against your finger tightly for support. Make sure you don’t drill all the way through your foam.
- For the piece that attaches to the blade, you will need to cut a piece out of the back so it can fit over the blade. Trace the gap from the pattern for the middle piece and either shave it out with your dremel or cut it out with a knife. Only cut out half of the width of the foam. Next, you will need to round the edge from the crescent shape. You will also need about a 45 degree angle cut on the edge. For the middle of the squared part, you will need to make it curved. Hold your dremel in the middle of the piece facing the outer edge of the crescent and shave downward, and then shave up to meet the edge, making a curve rather than a flat edge. If you haven’t already cut the curve, draw on the line and use your dremel to carve it out.
- Lastly, trace the gem shape on your foam where it should be placed. Carve this area so that the gem can sit flat when it is glued on. You might have to use alternative dremel bits to carve this out. Make sure all your edges are very sharp – using a fine dremel bit is the best for this. Otherwise, you can use a wood-burning tool with a bit with a large flat surface to glide over the foam, making sure not to burn it. Note that using a lot of heat on this piece can shrink your foam slightly. After you are finished carving these pieces, put them aside.
- For the next part of the hilt, you will want to cut out the 2 gem shapes with a very sharp knife. If you are a pro at cutting really deep angles with a ruler and knife, you can try cutting the gem shape straight out of the foam without needing to carve it. To do this, you would need to trace the shape on the back of your foam. Using a ruler on the inside edge of your line, hold your knife at an angle that will end at the middle of the gem and make your cuts. Otherwise, cut out the shapes normally and use a dremel to carve out the shapes using a fine sanding bit. Carving the shapes is really simple – just make sure to hold onto your pieces really well as the dremel tends to make them fly out of your hand. You will carve an angle on each flat edge until you meet the center. Working on two opposite edges and then the next opposite edges seems to be the easiest way to do this.
- The next step is the winged bits. Creating these is really simple. With a very sharp knife and a metal ruler, hold your knife at a 45 degree angle against the ruler and cut a long line down your foam. Flip your foam around and cut the same angle in order to get long pointed strips of foam. You will need these strips in different widths. You can use the pattern pieces to draw points for how wide each piece should be. Note that they are slightly wider at the top than at the base and that the outermost piece is the widest and the innermost is the smallest. You will need 12 pieces total, but it is a good idea to cut a few extra in case the ones you cut are too large or small when combined. Cut each piece longer than it needs to be and taper the edges so that they will sit flush on the ridges you carved on the crescent piece. You can do this easily with a pair of scissors starting on the sharp edge.
- The last piece to cut out is the center piece, which you only need one of. If you have bumpy edges at the back of your foam, you might want to sand them down so they are flat and glue down smoothly. There are two ways in which you can do the center piece. You can either glue everything together and drill the hold where the dowel will go, or more simply you can trace your dowel onto the center of the middle piece and cut it out (giving you two pieces). You will also need to trim the corners of the crescent to make tapered edges, but this time you will have to trim from the center of the edge as this is the center piece. You can smooth the edge with your dremel.
- Next, there are some small cuts to be made to help the strips from the winged pieces fit into place. Cut out the winged pieces from the final product image below. Trace the lines from the gaps made into your crescent pieces. Next, make the gap narrower by drawing lines about 3mm closer to the center. Using a 45 degree angle on the edge, use your knife to cut all the way down into the foam. Follow the curve of the crescent with your knife to cut out the pieces.
- Finally, it is time to glue all of the pieces together. Using contact cement, cover the backs of the crescent pieces and both sides of the middle pieces. Also cover the backs of the gems and the strips for the winged pieces. You will also need glue on a few small areas, such as the 45 degree angles cut into the crescent pieces, the tapered edges of the thin strips for the wings, the area on the crescent pieces where the tapered edges of the strips will meet the crescent, and the spot where the gem will go. When the contact cement is dry, attach the center piece to the crescent pieces and secure well. Next, attach the strips for the winged edges, curving them along the edge, ensuring a close fit. When one side of strips is done, cut the excess off so the edge is flat. You can use a pair of scissors for this, but make sure your scissors are flat along the top and not angled in any direction. Lastly, glue on the gems. If you didn’t cut a space for your dowel, you will drill a hole in the center of the piece at this point.
- Check your piece to make sure everything is perfect and do extra 'demeling' where it might need to be done. You will need to check the fit of the cross guard over the blade on your dowel. You might need to shave more on the inside of your cross guard to make it fit. Once your fit is good, cover the bottom of the blade and the inside of the cross guard with contact cement. Once it is dry, slide your cross guard on and press your glued areas on well. You might want to use your dremel at this point to do some fine tuning on the fit of the cross guard. Your edges should be completely straight, and if the blade makes the piece bump out at an angle, shave it down.
Step 4: Hilt: Bump Between the Guard and the Grip
- The patterns here are the side and top views of this piece. Cut out about 4 pieces of foam using the largest circle pattern on the right. Glue them together using rubber cement. Using your dremel, smooth the edges of your foam so you have a nice cylinder to work with. Next, shape the top piece of the first layer of foam to look like the image below. Leave the second piece flat. Next, carve the last curve to match the image below. You will need to hold onto your piece tightly while using your dremel so it doesn’t fly away on you. Make sure to use a fine dremel bit to make your piece smooth.
- Lastly, you will need to drill a hole through the center of this piece to fit it over the dowel.
- Attach the bump to your dowel using Goop glue or another suitable glue. Push it up your dowel so it is snug.
Step 5: Grip
- To create the base for the grip, you will want to wrap a long strip of thin foam around the dowel. Using the pattern below, use the measurements of the width of the blue lines to create a long strip of thin foam. Put contact cement on both sides of the foam and your dowel from the bump to the length of the grip. Wrap the foam tightly around the dowel until you reach a thickness just a bit smaller than the middle circle in the pommel pattern.
- Becausethe edge of your foam will stick out, use your dowel to smooth out the edge to match the rest of the grip.
- Next you will need to cut 4 long strips of thin foam in the width shown below (in green). You will also need to cut two more of these strips to fit around the edges of the grip (shown with the red line). Cut out the pattern below and cut off the edge with the red line. Check to see if it fits around your grip perfectly. If it doesn’t, resize the pattern and print it again. Cut all of the spaces between the green lines using either a blade or a pair of scissors (you can fold the piece to make cutting easier). Line up the piece on your foam and use pins to hold it on. You want the edge with 4 gaps to line up with your gem on your cross guard. Using a pen or fine marker, draw the lines on the grip. Cut the strips of the foam at the bottom at the proper angle (see the red line). Next, put contact cement on your strips and glue them down. You will need to cross over the strips in a certain way. Two opposite sides will be left under right, and the others will be right under left. See the images of the one I made to view how this was done. You can either place the strips of foam at the edges of the grip first or last. I recommend cutting your strips to size first and then adding contact cement to the edges of the foam as well as the back as mine separated a little when I sprayed it with Flexi Dip.
One very important thing to keep track of is that your placement of these strips is perfect. Somehow mine became slightly off center. You can draw a line down the center of your grip following the middle of your gem if it helps. If you don't want to cross over the foam pieces and you want it to sit flush, simply print and fit the pattern to your grip perfectly and then cut it out of foam and glue it on to your grip as one piece. If you do this, you'll want to make sure to glue the small edges of the foam that will connect so that they don't separate when using the heat gun or Flexi-Dip.
Step 6: Pommel
This piece is made of about 5 layers of foam. One of the pattern pieces is the side view, and the other is the bottom view. First, trace the middle circle on your foam 3 times and cut them out. Glue them together using contact cement and smooth the edges using a dremel. Draw the small circle in the middle of one end. Next, cut out two of the largest circles and glue them together. Use your dremel to smooth out the edges and then glue them to your smaller piece using contact cement. Use a dremel to shape the angle on the pieces. Use a dremel to carve a hole big enough for your dowel, making sure not to drill all the way through as this is meant to cap off your sword. You want the bottom of the dowel to reach the bottom of your pommel. At this point you might have to cut down your dowel to size using a small hand saw or power tools. Use Goop glue or another suitable glue to glue the pommel to the dowel.
Step 7: Finishing, Coating, Painting, and Protecting
*Reference photos are included in the pdf.
In order to seal the foam, you will want to use a heat gun on it. Set your gun to about 975-1100 degrees Fahrenheit and run it over your piece until you get a somewhat sparkly appearance on your foam. It generally doesn’t take more than a second to see this as you run your gun over it. This helps make the pores of the foam small so it doesn’t suck up all your product for the next step.
Before painting, you will want to prep your surface to make the paint adhere to the foam. The best way to do this is by spraying Flexi Dip or Plasti Dip onto your piece (I added about 3 layers). You can also do this by adding several layers of wood glue to the surface.
Using the reference photos, paint your sword. You can use acrylic or spray paints. Link’s sword isn’t crazy silver and has an aged look, so you can use sponges to lightly apply a variety of greys and browns to the surface. You can also use white to add highlights and darker colours to add shadows to make the sword pop. If you make mistakes, you can easily repaint the surface.
Lastly, use a clear coat to your finished piece. This will protect the paint from chipping. I recommend using a spray with a very shiny sheen to give your finished piece a metallic look.
Step 8: Notes
Tips
Use an Exacto knife with good quality blades. I tried using one from the dollar store and it didn’t work at all with the foam. I recommend purchasing a knife sharpener like the one pictured below. If you sharpen your blade after a few small cuts or one long cut, you will cut through your foam like butter. The softness of the foam dulls blades incredibly fast. If you don’t sharpen your blades, you will have to change your blades constantly. This sharpener is a good investment for foam work.
For great tutorials on how to work with foam, I recommend viewing Evil Ted Smith’s videos on YouTube. He demonstrates how to sharpen blades, create patterns, work at an angle, and how to use contact cement.
Be sure not to hold your heat gun too long on your final product as the heat can release the glue. This happened to me a little bit on the edge of the sword blade. If this happens, run some contact cement in the crevice and squeeze it together again after it dries.
Supplies
I am using Eva foam floor mats that are 7/16” (11mm) thick – just under half an inch. This means the blade is 7/8” thick and the hilt at its widest point is 1 5/8” thick.
SafetyMake sure you wear a proper dust mask/respirator and goggles while drilling at the foam. Protect your work area with newspaper. This also makes cleanup much easier. The very fine dust from sanding gets everywhere and spreads far. You can protect your clothing by wearing an apron (or better yet, wear old clothes).
Contact cement, Goop glue, spray-paint, and Flexi Dip/Plasti Dip have a strong smell and should be used in a well-ventilated area. The Flexi Dip spray is especially strong (I’m not sure about Plasti Dip, but I assume it’s similar).
Be careful when using the heat gun and wood burner as they reach really high heats and can burn your skin on contact. A hair dryer will not work as a substitute for a heat gun.
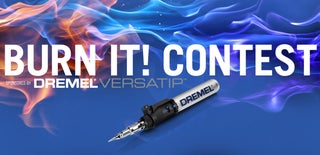
Participated in the
Burn It! Contest