Introduction: MAKE YOUR OWN WOODEN MALLET WITH a CNC MACHINE
A simple Mallet made from a 6" x 18" x 1" Oak Board. I had a leftover Oak board from another project so decided to turn it into a mallet which would be useful for assembling tight fitting wood inlays and joints or pegs. the goal was to make it sturdy and heavy with a large flat striking surface allowing it to transform force into pressure over large square surface.
Supplies
The supplies I used are as follows:
Carbide Create (for drawing the profile for the CNC)
Carbide Motion (for running the CNC)
Wood Glue (I used Titebond Original)
1" x 2" x 1/2" Brass Billet (Inserted into the center of the head for added weight)
Shapeoko 4 XXL CNC
1/4" Down spiral Cutting Bit
Hand router with a 1/4" round over bit.
Orbital sander and sandpaper 100 - 400 grit
Clamps / Vice
Small hand saw
6" x 18" x 1" Oak
Step 1: Draw the Profile
Set up the Job in Carbide Create. (See the image above for my settings.)
The Oak board is 1" thick so in the end you will have three parts glued together making the head just under 3 inches.
Draw the head. this is a simple square with a 1/2" round on the corners
Draw the handle below the head and shape it as you wish. I would make it about 1" wide so the handle fits well in your hand.
The handle will be 1" think as this is the thickness of the board. I angled it a bit so that it is not perpendicular to the head. The purpose of this is to make it so the head hits flat when you swing it while your wrist is still at a slight angle.
I think it makes it feel a little bit more ergonomic.
Now make a square in the middle of the head
Duplicate the head and rotate it 90 degrees and make one more copy of that and place it just over 1/2 inch from the first copy.
The reason we do this is grain direction. An oak board will have the grain running from top to bottom lengthwise.
This is how the wood is strongest. So the handle and center of the head will have grain running from top to bottom.
The sides of the head will have grain running from left to right. once this is assembled it will make the head even stronger.
Step 2: Program the Cuts
1) Create a 1/4" pocket around the center of the two sides of the head.
2) Create a contour around the outside of the two heads this needs to be a 1" deep cut
3) Create a contour around the outside of the handle this needs to be a 1" deep cut
4) Create a contour on the inside edge of the hole in the head that is attached to the handle. also a 1" cut.
5) Add Tabs around each of the components so the piece does not break off while cutting.
6) Save the file and Generate your G-Code
Step 3: CNC Time
You need to fix the work piece on the CNC. I used the clamps that came with the machine however you can put masking tape on the bed and then tape the board and glue the two pieces together with superglue. if you do it this way you don't need the tabs from the earlier step.
Personally It's faster for me to fix it in place with clamps.
Install a 1/4" down spiral bit in the router/spindle
Turn on the CNC and home the machine.
Set the Zero (I normally use the left bottom corner of the work piece as Zero)
Load the G-Code and run the program.
When the cutting is completed use a small saw to remove the tabs and liberate the parts from the rest of the board
Step 4: Assemble and Finish
Glue one side of the mallet head to the handle. Use as much glue as is needed to fully cover the surfaces being joined.
Flip it over and insert the brass bar for added weight
Put in more glue on the other side and insert the other half of the head.
Put it in claps or a vise and squeeze it tight.
Wait until the glue is fully dry
Using a router you can put a 1/4" round over on the head and most of the handle
Sand everything with 100 grit sandpaper on an orbital sander this will allow you to make sure all seams are perfectly smooth and any corners the router couldn't reach can be smoothed out here.
Now sand it all again with 150 grit and then 240
Apply butcher block oil with a rag and let it dry
You can now sand it again with 320 grit and re apply the oil and let it dry
Now sand it one more time with 400 and re-apply the oil.
Once dry the mallet is complete.
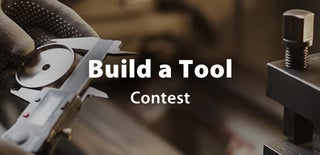
This is an entry in the
Build-A-Tool Contest