Introduction: Mackay Hammer.
Mackay Hammer. Soft Metal Non Sparking
A soft hammer non sparking for workshop. I find the hammers I have are not quite right for working brass and plastic bushes seals and other parts. The handle is not quite right and the head is usually too small. I made this one for tapping in various bushes and bearings or tapping a job in the lathe to get setup. I did not make it to be used as a sledge hammer, delicate work with finesse only.
I am impressed with the ability of Fusion 360 and the 3d printer. Creating the part you want as a pattern then casting in metal to get a finished part with minimal waste. Printing in a pattern with 2 half's, allows you to defy gravity a bit more when printing.
One of my older brothers has been a Fitter and Turner/ Machinist for 55yrs. When I showed him my hammer and the 3D printed pattern a couple of months ago he said if I make any more he would have one. I didn't document my first try so thought I would make a second one and try and fix the mistakes.
This same process can be used for multiple parts required for any job. Build plate size on the 3D printer is the main limits.
Supplies
The Hammer
3d printer and generic filament
Tennis racquet grip to cover handle.
Scrap aluminium 70% total weight. ( I used old roller blind blind tubes and other bits and pieces.)
Scrap copper 30% total weight. ( I found some copper pipe and asked a plumber for spare even electricians may have scrap.)
Tin 50g ( purchased from a supplier )
Varnish to suit 3d filament and metal. ( I used a 2 pack for plastic and spray can for metal ).
Mould Box if needed
1 length 90mm x 12mm pine wood pre painted
1 length 120mm x 12mm pine wood pre painted
Form ply 8mm for base approx 450mm x 250mm
16 x 40mm 8G chipboard screws.
10 x 12mm 8g chipboard screws.
3d printed box handles
Consumables
Moulding sand ( I used bricklayers sand and 1 bag of ball clay)
Furnace, crucible and safety equipment. ( safety is the most Important thing )
Step 1: Design the Hammer
I went through all the hammers I have and held each one testing for weight and balance and grip. I made notes of the ones I liked and why. I found most were too long in the handle and too small in the head. I decided on the attributes I wanted from the ones I liked, and took measurements. I also took a photo of the one that was the closest too what I wanted as an end result.
I used Fusion 360 to design the hammer pattern.
The printer I used had a maximum build plate size of 320mm x 320mm so I kept under 300 overall length.
I used the measurements I had recorded to make the handle the right width and shape and length.
The head was done the same however I decided on a hexagonal head that would come out of the mould box easier. I also included some hold down points so I could secure easily in the milling machine.
The big addon was the huge feeder I had to include so the metal had a way of feeding the head when it cooled.
I used 9mm dowel to align parts I glued into the top part and tapered the ends for easy alignment and separation.
I'm a beginner at metal casting and don't claim to be anything more. I expected to have mistakes in my design but I will also learn from those mistakes so should be all good.
Step 2: Making the Mould Box
I made a new box that would take the shape of the hammer better. I allowed 100mm extra length and width then the printed hammer mould.
I cut my length of wood in half then I cut 2 pieces at a time so that 2 pieces were identical.
I used chipboard screws 40mm to secure each board. I had a flat table setup square so each side was put together square and straight.
When the top and bottom where assembled, I put on the top box a few different ways until I got the 2 faces that aligned well then secured the box handles with 12mm 8g screws.
I used an electric cutter to cut some Criss cross grooves inside the box to help grab the sand when packed.
I screwed the base on with 2 screws (12mm 8g).
Step 3: Pack Sand Box
Due to imperfections with my printer I decided to coat the pattern surface with a think coat of 2 pack varnish.
The capillary action of the varnish helped to curve and smooth the surface around the wording and other edges. This made it better when packing the sand.
I started with the base and used talcum powder as a parting agent. Coating the surfaces then sieved sand over the part and packed in layers until I reached the top of the box section. I cut back and installed the base cover (ply wood).
I turned over and decided on where to position my Sprue, then i used some dowels as extra steam vents on top of each hold down point. The feeder, I oversized to 40mm to allow for heaps of extra metal to fill the hammers head when cooling.
I positioned the sprue in the middle of the handle. The reason I chose this point was to have Alu fill the base of the handle first then feed the head with the copper coming in last and condensing in the head at the end of the pour. The purpose of the copper is to add weight to the head nothing more. I will tilt the mould box approx. 5% when pouring to ensure metal runs to the bottom of the handle first.
I did use a 1mm brazing wire to poke some steam vents around the mould both top and bottom boxes. This did help.
Step 4: Pouring the Casting
On the first try I decided to heat the copper separate to the aluminium. I put a small amount of tin with it and with the aluminium. I brought the alu up to about 900 c and the copper to 1090 c.
I put the Alu crucible on a steel plate cleaned dross then poured in the copper. I stirred with a stainless rod to mix then poured the casting.
On the second remelt of failed ones I just broke up and remelted all in one crucible.
I set up my box with a slight angle approx. 5% downhill toward the handle.
The result wasn't too bad my sand was a bit moist and steam pressure pushed on the mould in a couple of places around the head. Given it's a hammer and I'm going to bash stuff with it I thought it was ok the wording was ok but the steam pushed on it and I lost the "C" in "MACKAY". The wording was ok not perfect but passable for me.
The un machined metal just looks a bit duller then Alu but the same and I can see crystalline surface on the tops that cooled to the atmosphere.
I probably should have tapped the box straight away to help settle out any air pockets.
Step 5: Machining
The final step was to machine.
Remember this is a soft metal hammer to bash things with. If you don't have access to a mill just make your best effort with a grinder and file and some sand paper, it should still be ok to bash stuff with.
I cut away the sprue and feeders with a cutting blade on a grinder. Being careful not to cut away anything I was going to use to hold down the part in the milling machine.
I gently filed the bottom of the head and handle support to tidy up any excess steam vents I made with wire. This gave me a uniform flat surface to sit on the bed of the milling table.
I first held down the handle and machined the head flat. Then I changed the hold down points to the head and handle height support and machined the handle top surface. I flipped over and repeated the same process. So that now I could position in the vice 90 degrees to the bed and hold by the handle.
I used the grinder cut off wheel to remove all excess metal.
I used a square to set the head perpendicular to the bed and machined the face of the hammer and top of the head. Changed the angle of the vice and machined the other 4 faces as best I could without getting too carried away.
I also drilled a 10mm hole through the handle support so I can hang on a nail on the wall.
I did find that the metal has become quite rigid almost brittle compared to 100 % Alu. It does machine ok and leaves a nice silver shiny surface.
Perhaps I used too much Tin.
Again it's about to be bashed around, it's a "Mackay Hammer".
Step 6: Finished
I cleaned with soapy water then wiped with thinners and towel dried. I sprayed with a can of clear lacquer that is good on both metal and plastic.
I wrapped the handle with a tennis grip I got from the local sports store. It feels nice in your hand firm and not too soft.
I also tried, with a hand engraver to fix the missing "c" but no good. I have got an engraving machine down the back I am still learning to use, so I might try to engrave my brothers name on the other side and send it too him for his birthday. Maybe a few patterns over the top of any casting mistakes.
It has turned out to be rigid and brittle in the handle. When I remelted another one, I used a small sledge hammer to break it across the weakest direction of the handle. It snapped instead of bending like I would have expected of Alu. Did take quite a strike though. I may have used to much tin in that one. However it was real easy to machine in the handle area. The head was more dense and seemed to be more copper even though the colour wasn't there. If it breaks I will remelt and add more copper and Alu no tin.
All in all it was fun to make I learnt a lot and will endeavour to perfect in the future.
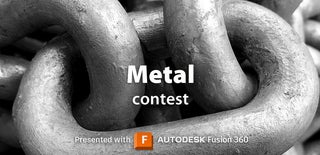
Runner Up in the
Metal Contest