Introduction: Make Hard Wood Floors From a Tree
This whole project started because of two wind storms that hit my mom's house. The first knocked down a bunch of trees which I cut into firewood about two weeks prior to the bigger storm which brought down my maple tree. I ended up with about three cords of wood which is about what I can burn in a couple of years. The second storm brought down even more wood and was going to cost $9,000+ to have professionals clean it up so I scoured the internet for ideas.
I decided that I would slab it out and sell it on ebay but nobody was buying anything other than Ash slabs (which I slabbed to sell). I found a buyer for finished cherry board which led me to acquire the Alaskan Sawmill. Then I looked into what to do with the maple and found that bowling alleys are made out of this exact tree, a Black Maple!
My wife loved the idea and we figured that we could get about 1500 sq. ft. out of the tree if we used some of the larger branches (something the internet tells me is a no-no). Realistically, we needed about 600 sq. ft. to do the areas of the home that I cared about and 900 sq. ft. to do the entire first floor of our house (which is what she cared about). Since Black Maple flooring is about $8/sq. ft. the potential savings for our flooring was huge!
If you combine the savings from the cost of cleanup and the cost of the flooring, that's nearly $15,000 (after tool acquisition and rentals)!
Warning: This is a time intensive project. It isn't a weekend long thing. Slabbing the boards takes time but you eventually get pretty quick. Then it becomes an issue of transporting slabs from point A to point B. Also, after completing this project, I can tell you that there is A LOT of waste unless you have experience in making lumber (then, it's just a lot of waste). I ended up getting about 400 sq. ft. out of this tree plus about a hundred peppermill blanks and enough wood to make tons of cutting boards.
Supplies
Tools:
- Chainsaw, at least 60cc with a 28" bar. Search Craigslist or inherit one like I did.
- Ripping Chain - they have a finer pitch for a better cut (make sure that it fits your bar and drive)
- Skip tooth and regular chain for cutting down the tree (skip tooth works best to help clear the saw dust from really big cuts like 24" long. Again, make sure that it fits your drive links and length)
- Alaskan Mill
- Bandsaw capable of resawing about 6". Mine is a little under powered at 1.125 hp.
- Resaw Blade for the bandsaw. I used about 10.
- Table saw
- Jointer, the longer the bed the better
- Planer, I used the older version of this at home to standardize my sizes then I used one where I work on my lunch hour.
- Big Planer - This is what I used on my lunch hour. It. Was. Awesome. (way more power than I needed, you could probably get away with something like this planer instead. if you buy that, then you won't need the smaller DeWalt)
- Router and table - This isn't the model that I used. I have an old Craftsman that I adapted to a birch box that sits in my table saw. It's not ideal as it's a plunge router instead of a fixed base.
- Tongue and Groove Bit - I could tongue about 450 sq. ft. per bit or roughly 1500 linear ft. I used two bits.
- Creeper - or something else to move logs around with.
- Feed Rollers - at least two.
- 2004 GMC Canyon, not the 4x4 version
- 1999 Toyota 4Runner SRS (optional for when your Canyon breaks in half midway through the project)
- floor nailer (go to a pawn shop or eBay and then resell it. Then it will only be $100)
- Stain - I used Minwax Red Oak (don't buy it on Amazon, it's stupidly expensive)
- Stain applicator
- Top coat - I used Bona HD satin. It's supposedly good enough for commercial applications which is nice. It's pricey but not much more than Varathane and it can be walked on in 8 hours. Furniture can be moved back in to the room in a day or three depending on its weight.
- floor sander
- belt sander
- palm sander
Materials
- Large tree, preferably a hardwood but that's up to you. Nature selected a Black Maple for me (and also an Ash, Cherry, Pear, Dogwood, and small chunk of Black Walnut)
- Latex Paint - get the mis-tints from Lowe's.
- paint brushes
- gas/oil and bar oil
- 2x12x12' or a sheet of plywood
- time...lots of time
- storage space, like triple what you think that you will need.
- plastic tarps
- chain/ratchet straps, wedges, rope, etc. for felling trees.
- Calories, unless you're looking to lose some weight (I lost 20lbs on the milling part of this alone and I still ate like a racoon throughout the process).
Step 1: Have a Wind Storm (or Two) and Clean It Up
This is actually the easiest part of this whole project. Just cut the little stuff off your trees. You can't use branches where the pith, the center of the growth rings, is off to the side. We turned all of the little stuff into mulch. It took about two days to clean up all the branches. Then, we hauled them to a friend's house to mulch his woods to try and keep some of the pricker bushes under control.
Once you're down to just the large (10"+ diameter) branches with the pith in the center, it's time to break out your Alaskan Mill!
At this point, you should be painting the ends of the logs so they don't check/crack. Paint them as soon as you cut them. Also, ONLY CUT DOWN WHAT YOU CAN MILL THAT DAY! If a tree lays in the dirt, it will absorb the mud and moisture and start to rot and discolor. If you have to cut it all down at once, put down some 1x2s for the logs to rest on so that they aren't directly on the ground.
Hone your charcuterie board skills while you're on breaks.
(we also found multiple instances where tree branches grew back into the tree which was weird but cool! see photo)
Step 2: It's Milling Time!
Have a plan before you start. I wanted 4" wide flooring that would be 3/4" thick. So, add half an inch to your desired dimension and get cutting. For me, that would mean that I should have been slabbing boards to at least 4.5" thick (5" would be best because sometimes the cut can be curved.
Use some 1x2s as levers to get the tree up onto a log so that you are cutting at a downward angle. Ten degrees of tilt helps tremendously.
I used a 2x12x12 as my initial guide. I've seen people use old aluminum ladders too. I liked that my 2x12 was much longer than the tree because it made starting the cut far easier. I used the board for every cut because of the start and ending bits of the milling process.
As you cut, use a few thick wedges or a handful of shims to prop the board up so that it doesn't pinch the bar as you cut.
Then, slab your tree into your desired thickness, 5" for me. Don't try to mill the tree into floor boards at this point. You will hate life. Transport the slabs to your workshop and paint any cracks or exposed endgrain. I used a creeper and old beer box to slide and position the logs in my garage before stacking them. Sticker the slabs with 1x1s and then use an old box fan to provide circulation. I also made a solution of bleach water (1:50-ish) and sprayed the slab faces to help inhibit any mold growth.
Step 3: Cut Boards
Go ahead and skip arm day at the gym!
Lift those slabs into place and start cutting them to your desired thickness. This is a long process but there isn't much more to it than that. I made my own fence as my saw didn't come with one and I liked that it was extra long and tall. That really helped get a good, straight cut. Make sure that your feed rollers are flush with your table and that they don't have anything sticking up that could catch on the slabs.
I painted my ends to help prevent the cracking and checking. That's optional I guess but I did notice that it saved a lot of board feet from becoming unusable. If you're going to be painting the ends, only cut what you are sure that you can get painted and stacked within the next 24 hours.
I'm just going to point out that my local wood/lumber store (like the fancy craft wood places which have mills) would have cut all of this wood for $500-$700. I spent $100 in blades, ~$150 on the band saw, $20 on belts and pins. So, for just a bit more, the mill could have done this job in a few days. That said, there would have been a ton more loss.
Step 4: Dry It.
For this, you'll need a box fan or two. This is the same process as what it was for the slabs. Make some 3/4" square by about 4' sticks to use as stickers. DO NOT USE OFF-CUTS FROM YOUR BAND SAW. Using green wood will cause sticker shadow, a dark stain in the wood under the sticker, which can go all the way through the board, rendering it useless. I stickered mine every 18-24" and I'm happy with the results. If I had to do it again, I would ratchet strap the boards flat (I saw it on the internet somewhere) since I was only adding a few layers of wood at a time. If you can get a ton of weight on a tall pile that was stacked quickly, you will probably have less cupping. As I stacked, I placed some Ash slabs on top of the piple to keep it as flat as possible.
Depending on your conditions, you may have usable wood in a month. I dried mine in my basement which was about 25-30% humidity and it was pretty good within a month or two. I left it go for a couple extra months just to be sure.
Step 5: Wait...but Be Productive
If you're feeling adventurous, dry some wood by the fireplace and make presents for people! If you try to dry a log, it will crack. To prevent this, put two coats of linseed oil on your piece to help even out the drying process. I had pretty good results after about a month of fires. Just rotate the piece(s) each night or occasionally throughout the night so that the entire piece gets heat.
I made some pens, peppermills, and a seam ripper for my mother.
This is also a great time to cut the chunks of leftovers into usable blanks so that they can start the drying process.
If your truck is now in two pieces, this is a great time to learn to weld! I used a little welder from Amazon that was $100 which I also used to fix my $50 craigslist jointer.
Step 6: Make Enemies in Your Immediate Surroundings (Plane Your Boards)
I'm not even joking about this. My neighbors came over to yell at me....twice, when I was using the Dewalt planer. I did everything that I could to try and minimize the noise but it's a seriously loud machine (and they are...ummmm....fancy people). Use a small planer to standardize your board width. That way, you can take it into school and use their planer which is massive!
I standardized my boards down to 1.25", 1.125", and 1" and marked them. The planer at school could take off 1/8" at a time instead of 1/32 or 1/16 if the blades were new. The planer at school wasn't great at moving up and down which is why I standardized my widths at home where I could do it quickly.
That said, I did learn that a local wood working shop offered planing services at some really reasonable rates. I think that it would have cost me $400 for what I had to plane. Considering that I spent $125 in blades and a ton of time, that $400 would have been well spent. Investigate what you have around you to save time and money.
Step 7: Joint!
There really isn't much to this which is why there aren't many photos. Get a jointer. The longer your bed, the more flat your joints will be. Mine was a 48" x6.25" jointer. I bought a jointer off craigslist that needed a new motor and a thing to attach the fence fabricated. It took about an hour to fix it up and about five hours to joint everything. I used the chips for mulch around the front of the house. My neighbors weren't thrilled about that either (evidently, you can't just put wood chips down and call it mulch but what is mulch if not just wood chips from a mill?).
Pay attention to any imperfections that you may have. With some attention to detail, you can save a lot of board feet from ending up as scrap. Edge imperfections can also be creatively routed so don't discard boards just because they are slightly dinged up.
You could pay a shop to do this step as well but it was oddly enough relatively costly. It's not really hard work so just do this yourself.
Step 8: Cut to Width
Somehow, I forgot to take photos of this step. Rip it to width on a table saw. Lock your fence in place with a pair of clamps and check your width often. Once you cut your first accurate piece, set it aside to use as a gauge. This step too a bit of time because I ran out of floor space in my garage so I was always having to take a long way around to stack or get wood. Plan ahead and you'll save time (wild idea, right?)
Step 9: Time to Get Groovy!
Again, this really isn't that difficult. I made a jig so that I could use a vacuum on my router. It was a loud process but only took a day to complete. I don't really have anything fun to say about this other than to watch your fingers. Feather boards and a real router table would have helped keep the boards more flat but I managed without much trouble.
This is where you can get rid of a lot of edge imperfections if you pay attention to your boards. Use the tongue side on parts with edge imperfections and the groove side on good sides. This is something that a shop wouldn't do so I'm glad that I did it on my own.
Paying a shop to cut tongue and grove was nuts. I guess I understand since I had something like 1500 linear feet of wood that would need to have four sides done but it really only took about a day. The math worked out to around $70/hr to have a mill do the same work. I'd just do it on your own.
(p.s. waive goodbye to your trusty truck of 12 years)
Step 10: Install, Finally....
If you've ever installed wood floors, you know that this part isn't that bad. In fact, it was probably the easiest. Make sure that your board widths are the same across each row. I used a small hand plane at times because I noticed some runout on a few boards. I will say that some of my joints are tighter than I would like and others are a bit gappy but overall, I'm really thrilled with this project. It would look phenomenal in an older craftsman type home (think pre-1920s) or a woods cabin. The slight imperfections don't fit my stick built 1980s house but I'm the only one who is going to be going around looking for imperfections.
Prepare to lose your voice because you'll be yelling at people for sliding chairs, walking in heels, and generally using the floors. After a year of preparation and work, you're going to be protective. (literally, I can hear my daughter tapping in socks right now and it makes my skin crawl)
Bonus shot: my 16-year-old lab refused to move during the initial renovation. We kept that chunk of carpet for him because he prefers it to the new bed we bought him.
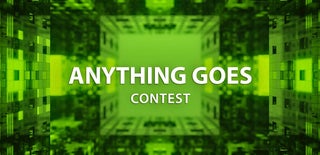
Participated in the
Anything Goes Contest