Introduction: Make a Bangle Out of Fabric Scraps and Resin
Please consider subscribing to my YouTube channel for more projects
Hello fellow makers,
If you have been following my previous instructables you might have gathered that I like making composites with resin.
This time around I wanted to make a deeper casting and came up with this bangle.
The bangle consists of a few layers of fabric that is then casted in a 10mmX20mm deep resin layer.
Let's get started on making your own!..
Step 1: What You Will Need:
To replicate this Instructable you will need the following:
- Pieces of old fabric
For this bangle I used a piece of old jeans and some beautiful left over shwe-shwe.
- Access to a 3D printer
- 2 Part clear casting epoxy
Amazon - 2 part Clear casting epoxy
- Laminating brush
- Release agent
I use red PVA release agent as it works with a wide variety of resins, it's super cheap and a bottle lasts forever.
- Sanding paper around 60 to 400 grit
- Clear coat
- A hobby knife
*As an Amazon Associate I receive a small percentage from sales made through provided links at no cost to you, this helps fund future projects.
Step 2: Making the Mold:
We will start by designing a mol for our resin to be cast into.
You will need to adjust the model according to your bangle size, I made this one a medium.
Usually with these types of projects are refined using a lathe but as most makers out there I lack access to one so I designed the mold that the inner takes a 5mm bolt that can then be fitted to a drill for a makeshift lathe.
This is a low filament use project that has no supports and can be printed with any filament.
Step 3: Cut the Fabric to Size:
Next we need to prep our fabric.
Using a new sharp hobby knife (you can also use scissors but I find the hobby knife to be much more precise) I laid the fabric out onto a glass pane and measured out 20mm strips.
To add some bling I wanted to add a copper accent to the bangle, my first thought was to use a copper wire but I was worried that it might trap air bubbles. Then I saw the self adhering copper tape used for repairing PCBs on my shelf... PERFECT!
It's flat, easy to apply and very shiny.
Step 4: Prep the Mold:
This is a very important step!
We need to make sure that the resin casting releases from our 3D printed mold.
To ensure this I applied a minimum of 3 coats of PVA release agent on the inside of the mold. Make sure you leave the coats to dry thoroughly in-between.
Step 5: The First Resin Layer:
With the release agent applied and dry we can start our first layer of resin.
Lay down a few layers of old paper or plastic so that the resin doesn't spill onto your workspace.
Next lay down your strips of fabric on the table and mix up about 20 grams of resin according to the manufacturers instructions.
I use a fast curing epoxy resin for this first layer to save some time but you can the slow curing casting resin.
Step 6: Layering:
With the fabric strips soaked in resin we can start wrapping them around the centre mold.
I started with the two pieces of denim, wrapping them tightly. Cut off any excess with a sharp hobby knife so that the seam is not visible.
To hide the seams better I placed them on opposite sides.
Next I took the strip of copper tape, removed the adhesive cover and placed it around one side of the bangle so that I sliver of it would be visible under the final strip of fabric.
Now finally place the last piece, for me this was the beautiful pink shwe-shwe and smooth it with a laminating brush.
Place the centre mold onto the outer mold and leave it to gel (you want the resin to set up but still be tacky, test this with the resin leftover in the mixing cup)
Step 7: The Second Deep Cast:
With the fabric layer gelled we can now do the final pour.
Start by mixing around 40 to 50 grams of epoxy resin according to the manufacturers instructions, the exact amount will depend on the size of your bangle.
I then placed the resin into a vacuum chamber for about 3 minutes to get rid of any air bubbles, if you don't have access to a vacuum chamber you can place the container with resin in a bowl with warm water and let it sit for awhile until all the bubbles have floated out.
Slowly pour the resin into the mold until it's completely full.
Leave to cure at least 24 hours.
Step 8: Demolding:
Now for the moment of truth....did you use enough release agent....
Luckily in my case giving the mold a slight bend broke the resin piece loose from the mold and I was able to pop it out of the mold.
Remember to not remove the centre mold!
Next you can thread through the M5 bolt and secure it with a nut (I used a 45mm long bolt).
Step 9: Shaping the Bangle:
We can now attach the bangle to a drill and start shaping it.
I used a little DIY cutting tool that is just a normal snap off blade clamped between two wooden blocks so that just about 1mm of the cutting edge is visible to roughly get the bangle to shape.
I then switch to 60 grit sandpaper to refine the shape and then 220 grit wetted with some soapy water to get rid of the scratches left by the previous grit.
When you are happy with the shape of your bangle we can finish it with wetted 400 grit sandpaper to get an even mat finish without any deep scratches.
Step 10: Prepping for the Clear Coat:
With the shaping done we can remove the inner mold.
I used a twist and pull motion to remove the centre mold and then washed away the leftover release agent with some warm water.
You will feel that the bangle has quite a sharp edge on the inside that can be removed by simply folding your 400 grit sandpaper and sanding down the edges until smooth.
Wash the bangle thoroughly with warm soapy water when you're done sanding, rinse well and let it dry completely.
Step 11: The Finishing Touch:
The last step is to add a layer of clear coat to protect the bangle from scratches and yellowing caused by UV.
To make handling the bangle easier while painting I glued a mixing stick on the inside of the bangle with some 2 part CA glue (superglue) that we can snap off when finished.
To cut down on cost I invested in a small airbrush to do all of my spray painting but you can get the same results using a can of clear coat by following the manufacturers instructions. I mixed my clear coat quite thin so that it flows well and gives a brilliant glossy finish.
Once finished I left the bangle to dry for 24 hours then you are ready to slip on your new creation!
Step 12: Enjoy!
I hope you guys find this Instructable useful and if you have any questions please feel free to leave me a message or comment bellow.
Please share your own creations with us by clicking the "I Made It" button below.
Happy making!
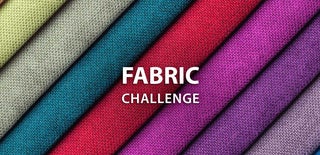
Participated in the
Fabric Challenge