Introduction: Making a Graver and Template Set for Engraving
so in this instructable, I am going to show you how to make a set of gravers with the template. From past 3-4 weeks, I am researching on engraving and I found myself so much attraction towards this work that I decided to step into this new kind of work. I saw many companies selling the set of gravers but overall in the end if you are going to use them then you definitely need to sharpen them again because their sharpness not going to last long because if you are a beginner then I think you are definitely going to break a lot of tip during your work and for that you need to sharpen that graver and there is no doubt that you are not getting the exact angle you need to grave the metal surface. so by considering this thing in my mind I decided to make a set of gravers completely out of scratch and decided to share my experience to other so that anyone who is fascinating about doing this new work can easily able to master this technique. This doesn't seem hard to make the graver shape but if you don't have power honing wheel then this will take a lot of elbow grease to make the set. I am also in one of them who don't have power honing wheel. Some of the things are easier for you to understand in the video part so I definitely recommend you to watch that as well and if you himself a master engraver saying this video on this instructable and found anything wrong then let me know in the comment section so that I am able to update that and everybody knows about that mistake. Other than that if you like this instructable then make sure to leave your valuable feedback in a comment section. I'm extremely happy to read your feedback.
These pictures are taken from my one plus mobile. From my past, I am using my mobile to record the video and to click pictures. I think I tried my best if you find any flaw then let me know I tried to perfect in my upcoming project.
Step 1: Material and Tool Used
So before jumping to the building sections, I would like to tell you about the material generally used to make the gravers. If you want to make a set of graver then you definitely not going to use the normal carbon Steel. You need a material which is going to hold it edge for a long time. If you compare normal carbon steel to the high-speed Steel and pay some attention to the composition then you find that high-speed Steel has some different composition. It contains a different kind of element like chromium vanadium molybdenum tungsten so these kinds of material provide much resistance towards aberration so that the reasons why high-speed steel is preferred to make the gravers. Other than that you can use tungsten carbide blanks for making a set of the graver. The only downfall of carbide is that it is very brittle than high-speed Steel but on the other side it going to hold the edge for a longer time. Many master engravers told that if you are beginners in engraving then it's better to use high-speed Steel as a graver as compared to carbide because carbide is less forgiving. So father material you have only two options either to go with high speed steel or you can go with carbide.in my case I go with both of the material to take a look that what amount of difference is in both the material and even if you were beginner in the engraving you will notice the difference between both the materials. And I found that difference during my first attempt at engraving. For the engraving surface I am using mild steel and the stool I am using is made up of carbide 90 degrees graver and during my first three-four lines I break the carbide graver 7 times and then I switch the graver to onglette graver which is made up of high-speed steel and also more forgiving towards the smaller corners. few hours I practice with the outlet graver to make myself comfortable with this new kind of work and once again some confidence I switch the graver bit to the carbide and succeeded as some extent even though I am still breaking the tip of the gravers but the number 7 which was in the first attempt decreases to 1 and I think with the passage of sometimes this number decreases and came down to 0.
Material used:-
1. Carbide blanks high-speed blanks
3. Ceramic stone or Ruby stone for honing the graver.
4. 5 mm thick acrylic
6. ¾” diameter mild steel rod
7. M4 Allen bolt to hold the graver
8. M3 grub screw for alignment of the template
Tools Used:-
4. M2.5, M3, M8, M10 drill bit
Step 2: Parameters Used in Graver Making
Face angles play an important role in cut down the material surface. This thing varies from material type. Usually angles from 30°- 60° used in engraving. If you use them on the wrong material the result is in the broken tip. Here are some parameters you can follow:-
1. For softer material angles from 30°- 40° works
2. For mostly used material angle from 40°- 50° works
3. For material like stainless steel angle from 50°- 60° works great.
The same thing has been important for heel as well. Generally angle from 15°- 20° works for a heel of the graver. The importance of heel is to prevent the graver dive deep into the material surface
Step 3: Commonly Used Gravers
Before making the graver trample our need to know about different kinds of size, shapes of gravers. In my research, I found that many Japanese master engravers made a bunch of their own set of gravers which doesn't even exist in the books. From that research I learned that it's completely depends upon you that how you can solve your problem. This thing completely depends upon your problem solving techniques. If you saw a person named Ford Half Japanese metalwork you may learn how many different kinds of gravers need to make to solve the problem if normal graver didn't work at that stage. So before jumping to the designing section, I would like to tell you about different kinds of commonly used gravers which I am going to made in this Instructables and their uses.
V-Point Gravers have a diamond-shaped face but with a sharper cutting angle. They're used for removing background material, shading, cutting borders and star shapes, and for raising beads for stone setting. So all the gravers whose angles vary from 70, 90, 96, 105, 110, 120 & 130 degrees come in v point gravers. Each person prefers different gravers, but what I experienced in my first attempt is that gravers having angles less than 90 degrees are more likely to break or chip. You have to be a little careful about these gravers.
Flat Gravers have a flat cutting edge with either parallel or slightly tapered sides. They're useful for removing or texturing backgrounds, bright-cutting, block lettering, and cutting consistent width lines for borders. The flat gravers with the slightly tapered sides also are used for inlay work.
Round Gravers have a round cutting edge with either parallel or slightly tapered sides. They're used primarily for raising and rolling beads for stone setting or cutting smooth curves when engraving or chasing.
Onglette Gravers have a cutting edge that comes to a fine point and curved sides. They're used for stone setting, line engraving, lettering, and inlay work. Perfect for cutting smooth curves and fine lines.
Oval Gravers have an oval-shaped face with a curved cutting edge. They're useful for shading curved surfaces, deep cutting, and for some styles of block lettering. They're also used for raising and rolling beads for stone setting.
Knife Gravers have straight sides that taper to a very sharp point. They produce deep, narrow cuts making them great for fine-line engraving and for removing excess metal from around stone settings.
Step 4: Designing the Templates
So the crucial step in making a set of graver is how you can make your templates. Because these are the only thing with which you are able to follow the profile and transfer it on to the graver. The process of making the template is very easy and to illustrate you I am going to upload a set of pictures describing how you can make doors template. So there are few things which going to play an important role in increasing or decreasing the size of the template. Because largest the size of the template, more will be easy to follow that profile precisely, and smaller the template difficult to do your job. as far as gravers are concerned there are two different kinds of graver one are those in which you are using a hand-held hammer to cut down the material surface and second are those in which you use some kind of power tool to remove the material. In my case, I am using foredom to do the job and for the tool attachment, I'm using number 15 hammer handpiece. The link for all of those are in the tools section. So there are few things you need to be considered while designing a graver template as follow:-
1. Length of the graver:-
Graver plays an important role in designing the template because if you are using hammer and chisel engraving technique then you can kept your graver length quite long as compared to the pneumatic or handheld have a piece which are work with some Power tools because the graver which you are using along with some Power tools need small graver blank for the cutting action because the tool holder itself has some length and if you are keeping your gravers too long then it would be very difficult for you to do your job. On the other hand, if you are using hammer and chisel technique in which you need to strike the hammer on to the graver back, in that case, you can get the graver length long enough because you have to hold that in your hand and strike with the hammer. You cannot use smaller graver with hammer and chisel technique because it is very difficult to hold that graver and follow the path to cut down the material so that's why I am saying that length of the graver place the important role in designing the template. Longer the length of the graver more will be the area you have to hold the graver to its place during the sharpening process in the templates.
2. Thickness of the sending block:-
The thickness of sending block also plays an important role while designing the template because more will be the thickness of your sending plate the more will be the height needed to keep that phase angle and as a result, a larger template is going to be constructed. So it is difficult for me to illustrate you with just simple writing about the template making process so that's why I am going to upload a set of pictures which will clarify you how you can make the graver template and what are the factors you needed to know while designing your templates. If you did not understand in this phase then I would recommend you to watch the video I think that will clarify your doubt on this part of the project.
3. Face angle of the graver:-
Face angle of the graver is another important part of designing the graver template. The face angle varies from 30-60 degree. The bigger the angle is the more will be the height of the template and vice versa.
To make the template first draw a box equal to the length and thickness of your grinding stone or plate. Then you have to draw a line whose length is equal to G mm (see Image 2) at an angle which lies between 30-60 degree. This usually depends upon the type of material onto which you have to engrave. For most of the material 45-degree angle works. Then draw a perpendicular at the end of the G towards the table surface and measure that distance which is X mm (see Image 2). Repeat the step for heel as well by taking the angle from 15-20 degree with the same length G mm which we used earlier we got length Y mm. Now we have two lengths having distance known for both sides. Now draw a horizontal line on a paper and draw perpendicular onto it. At X mm distance draw a circle where you need to drill the hole for the graver holder. After that extend that line to Ymm more. That is going to make the heel. The tip of the Y mm is the Point where the graver tip is going to be reached. Then make the required shape and angle by considering that point as the extreme end and everything you have to draw needs to remain below that point. This is how your face and heel can be formed. The same process has to be repeated with the clearance template the angle varies from 5-8 degree. If it seems too step then lower the angle. If you don't want to use this template then try to use thinner material like near about 2 mm. That case, you don't need a smaller template.
Attachments
Step 5: Making the Alignment Hole in the Template
The alignment hole is also one of the necessary parts in designing the template because this is the only thing which helps you to align the graver and lockdown to its place at exact position in each attempt in different graver templates. So the location of the hole can be made anywhere on the template you want but the main point to be noted that the hole was not too far from the graver holder reach. If you Mark the hole location too far then the graver holders will not be going to lock down and you are ended up with the nasty result. Other things also taking care of while marking the alignment hole is that the location needed to be the same position in all of the templates because the dimension and the graver holder is same for all of the templates and if you make this alignment hole wrongly then you are ended up with inconsistent grind and that is not good for engraving. It is always good to design the whole location according to the smallest template because if you design it according to the longer template and made it to for then there might be a chance that the hole appears out of the smaller templates. So these are the few things you need to know about this alignment hole.
Step 6: Making the Template's
Once the design phase of the template has been finished the only thing left is to make them for use. For that, I glue the templates onto a piece of acrylic. For the acrylic, I am using cast acrylic because it works well on to the scroll saw because it did not melt during the cutting process. so I would definitely recommend preferring cast acrylic over the extruded acrylic because cast gives you a better result. So once the templates have been glued onto the acrylic I mark the hole location with a spring loaded center punch and I am very careful during this process because the tiny amount of misalignment can affect my graver final outcome. Then I cut all of the templates onto my scroll saw. Here I tried my best to get as close as possible as I can because this is also the first time I am using this scroll saw and the quality of cut completely blew my mind. I highly recommend this kind of power tool in the workshop. Since it's my first project with the scroll saw the cuts are slightly wiggly because of the lack of experience and to remove that wiggle I use a set of needle files to do that work. I hold them into my vice and then carefully reached to the final lines what I needed. This is definitely not the accurate method but if you pay some attention to this then you will achieve closest to that accuracy. You can use CNC or laser cutter for this project. The 3d printer also is a good option for making these templates. So go whatever you find easy. So once the templates are completely finalize the only thing left is to drill the holes. So as I described earlier there are going to be two holes one for the graver holder and second for the holder alignment. For the holder, I am going to drill 10 mm hole because I am using 10 mm bolt for the holder lock down onto the template and for the alignment hole I go with 3mm hole because I am using 3mm grub screws. So at this stage, the templates are ready to use.
Step 7: Making the Graver Holder
So this one is also the most time-consuming process in this build and the main reason for this is that I made 6 unsuccessful tries and then able to make this final version. But even then if I compared this with the finishing I am definitely not happy that much but I think if you have a lack of tools then you have to compromise at some place. So come onto the building section of this holder I cut down ¾” piece of round stock and I roughly cut down it to around 1” in length. Then with the help of center finding jig, I marked the center onto this stock and repeat the same procedure onto the back side also. Then I first use 3mm drill to make the pilot hole and I approach the same thing from both sides drill the hole from the back side since the dimensions of the graver blank is 4mmX4mm and therefore I drill a 4mm hole. Once the 4mm hole has been drilled throughout at one of its ends I drilled 8mm hole and that is used to make the tap for m10 bolt which I am going to fit inside this holder blank. Once the tap has been made inside that hole I made a test piece and insert it into the jig. And everything seems to be work fine. Then I hold that holder into the vice and drill through the hole into that so that graver blank can be put inside that hole. Onto the threaded portion, I drilled a slightly larger hole so that no additional work needs to be done on that side. Since I drill a 4mm hole and the 4mm square graver blank not going to fit inside that hole so I hold that holder into the vice and start filling down the hole to a square section until the graver blank fits inside that hole. Once this thing is achieved I made a mark perpendicular to one of the square faces and the main reason to do this is to make a locking mechanism for the holder to lock down the graver to its place during the grinding process of the graver blank. Once the mark is done I center punch and drill the hole and then make the thread with the m4 tap. Now comes the tricky part that's why I said that it's good to use lathe machine for this process. So to remove the bulkiness of the holder I hold it inside the drill and then grind the taper but making sure not to remove too much of the material because out of 19 mm 10 mm is used by that bolt and in the remaining material we need to provide some space and drill hole for the 3 mm grub screw and that thing also need some space. So this kind of things you need to take care of while grinding the taper. Another thing you need to remember that the portion where you make a tap for 4mm hold down, don't grind that area too much otherwise the number of thread decreases and you are not able to hold your graver in the holder. One thing also to suggest you that if the holder seems bigger for some of the templates then change the angle in the design and remake the template, you can also change the hole position of the holder slightly down where your grinding is not disturbed by that holder. So you can say this is a little bit of try and error. In my case, I grind that holder into a triangular shape so that it will not come in the way of grinding plate. I also remove the bulkiness of the nut as well I hold it into the drill and then grind the surface to make it round in shape.
Step 8: Making the Hole Locator
this is the easiest part of this build and what you need to do is hold the graver holder into the jig and insert the graver blank inside the holder and lock down the graver to its place inside that holder. Once it's placed then I make one side of the graver completely touches the grinding plate. Then recheck that position. Once it confirmed with the help of mechanical pencil I made a mark and then carefully drill that hole by making sure that it will not displace from its place. Then I tap that hole with M3 thread so that the grub screws can be fitted inside. If you are going precisely then you will definitely get the exact result. The same thing occurs in my case and everything fits perfectly.
Step 9: Graver Length Setup
Once the holder is made to keep the graver length to a fixed portion I need to make a fixed length tube with which I can measure the graver length and lock down it to 50 mm. For that, I hold the holder into the template and then setup the graver inside the holder and kept the length from surface of the template to the tip of the graver around 50mm and then I measure the distance from top of the tip to the top of the holder which is around 27 mm required. Then I cut down a piece of copper tube to the required length and that length is used to hold the grave to fixed length.
Step 10: Cleanup of Blanks.
This might not happen with you but the carbide blanks I purchased have some sort of coating over them. I don't know much about that layer may be they are some sort of oxidation. I noticed that the surface is also not flushed like the hss blanks so I start grinding them onto my diamond plate until the shiny surface appears along the full length. That doesn't seem to be necessary but it definitely makes the blanks dead straight like the needs to be and then I proceed to the next phase.
Step 11: Cutting Process of Carbide Blanks
cutting process of carbide blank is very different than the normal material because of hardness. The blanks I am using are 6 inches in length. Which is too long to use as a graver so I cut them to 3” long portion so that it would be easy to use them. For cutting, I use two different methods. In first I use foredom and a diamond wheel to cut down the graver blank but the one wheel completely wear off to cut down one blank. So I approached a different technique. I grind the line around the perimeter or the graver with the help of diamond file and then hold it as closer to that line in the vice. Then apply a little amount of force to break it in half. It is very easy to snap this in half but to get a good cut you need to scour the line around all four sides. Otherwise, the cut didn't come good and you need to do extra work to clean them.
Step 12: Clean Up the Ends.
Then the work left is to clean up both sides and make them square and even because in the grinding process if the edge is clean then you are going to get a better result as compared to jagged edges. I use a diamond wheel in my foredom to do that work. One thing I want to suggest that don't apply too much pressure onto the wheel and always kept water to cool down the material and your grinding disk. The diamond plates are very thin and the diamond particles are glued onto it. If you apply too much pressure onto the wheel the particles start removing from the disk and your disk is no longer usable. If you overheat then it will cause the same result. So be gentle while using diamond wheels because they are not super strong like the diamond.
Step 13: Grinding the Initial Bevel
Once everything has been set up the only thing left is to grid the initial levels. This is the most time-consuming process of this build. I highly recommend going with a 150 grit diamond plate that will remove the material a lot faster than the 400 grit. For one graver I took 2-3 hours for the initial bevel. This is not a difficult task the only thing you need is to take the reference of the sides of the shorter template and grinding the blanks. Make sure to constantly check the shape of the graver to keep the precise shape. You can use optivisor for this work that would give you a better understanding of the graver dimensions. The template you are using the same kind of profile being formed onto the graver. The only difference is that the size reduces. Grind the blanks until you get the desired result. You can decrease the size as you needed because smaller the size of the tip better it works onto sharp corners. Also, it takes less time to grind the tip of the graver and polishing process.
Step 14: Making the Face and Heel
Once the initial bevel is done as I told you it doesn't take a long time to form the face. Because of the smaller size. For the tip, I use 1000 grit size and then home the tip up to 3000 grit. You can go up to 10000, I don't have 10000 grit but I definitely wanted to reach at that finished state because shiny the surface of the graver better will be the finish of the graver. The same thing needs to be repeated for the heel as well but doesn't make too much long heel because of longer heel more likely to break and chip the cutting surface. So don't make a bigger heel. The main advantage of the heel is it prevents the graver to dig right into the material surface onto which you are going to engrave. It is more likely to provide a parallel surface to the graver so that once it bites the metal that heel helps the graver to glide. To fit these graver in the hammer handpiece I slightly round off the edges of my gravers because its dimensions are little too big for the handpiece. To grind them I use the diamond wheel in the foredom rotary handpiece to finish the job.
Step 15: Conclusion
So that's all the process to build the graver and by this process, you can make any kind any shape any angle of gravers. To keep all the gravers together I have a scrap piece of resin in which I drilled a couple of holes and that pieces I am using for the organization of these gravers. Nothing too complicated just drill right size of holes and you are ready for the work. If you afford power honing wheel then go with that because it did the job done at a faster rate if you can't afford like me its good to have 80 grit or 150 grit diamond plate.
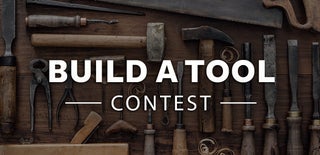
Participated in the
Build a Tool Contest