Introduction: Mig Welder Upgrade Diode Replacement in Bridge Rectifier
Inferior diodes often found in cheaper range of mig welders are prone to failure. Once one blows the rest will follow rapidly. Why? Because the type of diodes fitted in the bridge rectifier are linked together so that the sum of all of the diodes covers the amps and voltage generated by welding with the machine. These press fit diodes are the same as used in vehicle alternators.
Obviously installing these enables the welders to be sold at the lower end of the market and for a while they hold out but inevitably fail.
The diodes are installed in a heat sink made from aluminium. In this video, I show how we can remove these inferior diodes from the bridge rectifier and install new Standard Recovery Vishay 70 amp 1600 volt diodes that collectively exceed the workload of these welders and provide a more robust machine with the ability to work at the lower end of the welding scale as well as the higher end with ease.
So instead of having 12 press fit diodes we will install 4 bolt on diodes into the existing bridge rectifier, making the install as easy as possible.
Step 1: The First Image Shows the Original Diodes Removed From the Rectifier and the New Diodes to Replace Them.
Step 2: Full Instruction Video Showing How to Repair and Upgrade a Blown Rectifier in a Mig Welder.
Mig Welder Repair.
Walk through video Upgrading from inferior cheap diodes on a Sealey 180 Mig Welder and many other similar priced welders, which are fitted with press fit diodes that are prone to overload failure.
I used Vishay 70 Amp 1600 volt in parallel pairs, which is two sets of matched pairs, one reverse polarity and one standard polarity. The diodes are clearly marked with arrows showing the current direction.
This modification involves some soldering so you will need a soldering iron capable of heavy duty work. For this I used an old copper iron heated on a gas ring which worked very well.
The repair cost:
2pc Standard Recovery Diode 70HFR160 70A 1600V VISHAY £8.47 plus £3.90 postage
2pc Standard Recovery Diode 70HF160 70A 1600V VISHAY £8.47 plus £3.90 postage
I would not have been able to upgrade this welder had it not been for the people in welding forums who provided photographs and suggestions and reasoning as to why I should not simply replace with another inferior bridge rectifier containing what appear to be vehicle alternator diodes which are not up to the job. So a big thank you to you guys for sharing your knowledge. Category
How-to & Style
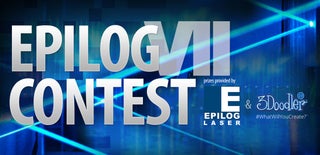
Participated in the
Epilog Contest VII