Introduction: Modular Concrete Pedestrian Commuter Bridge
Hi everyone, my name is Daniel and I'll be going into grade 12 in September. In this instructable, I'll be outlining my design process for creating a pedestrian bridge and surrounding environment in Fusion360. Here's an animation I made that shows the pedestrian bridge and some of the surroundings.
Supplies
- Fusion360
If you don't already have an free student account, go to the Autodesk website and click get started under Fusion360. It's a really powerful CAD tool that combines simulation, rendering, animation, and cloud storage into one app. You can also run it in your browser if your computer isn't very good. Many of Fusion360's basic features are intuitive to learn and there are many tutorials available online, so I'll be highlighting some of the features that are less known.
Step 1: Location
Photo Credit: Google Maps, Airbus, CNES / Airbus, First Base Solutions, Maxar Technologies
There is a vehicle bridge (circled in yellow) in my area that crosses a major highway. Many people commute to work every morning from the carpool parking lot and bus stop (circled in red) southwest of the bridge.
Unfortunately, there aren't pedestrian sidewalks that run along the full length of the highway crossing, as you can see in picture 2. The only safe ways to get to the carpool lot are driving or taking the bus, which doesn't run frequently.
I'll be designing a pedestrian bridge to go from the community on the east side to the carpool lot. The proposed path of the bridge I'll be designing is highlighted in blue in picture 3.
Step 2: Dimensions of the Surrounding Location
Photo Credit: Google Maps, Airbus, CNES / Airbus, First Base Solutions, Maxar Technologies
I wanted to have a rough model of the surrounding area to better understand how my bridge would fit in. Using the map tools in Google Maps, I was able to figure out the rough dimensions of the existing vehicle bridge and the highway that runs under it.
To access the measure tool:
- Hover your cursor over the Layers icon in the bottom left
- Click More from the menu that appears
- Scroll down and click the Measure tool
Using the measure tool, I determined that the existing vehicle bridge is 120m long, and 29.5m wide. It has 3 lanes in each direction. The highway underneath the bridge also has 3 lanes in each direction is approximately 61.5m wide.
Step 3: Creating a Model of the Existing Vehicle Bridge
Before we get started, I'd like to mention that you can access Fusion360's search bar by pressing "S". From here, you can type in the name of any command and quickly jump to it instead of trying to look through the toolbars. This saved me a lot of time during my design process.
The sketch on the YZ plane (picture 1) contains the geometry for the existing vehicle bridge. Knowing only that the width of the bridge is about 29.5m, I did my best to recreate its cross section. The purple arrow shows the rounded railing of the bridge. I also added a concrete divider between the two directions, shown by the red arrow. After finishing the sketch, I extruded the bridge to 120m long.
I then created another sketch on the surface on the bridge (picture 2) for the road markings. To accurately create all the road markings, I used the rectangular pattern tool. The road markings in my model are slightly exaggerated for greater visibility, measuring 0.625m wide. They divide each side of the bridge into three 4m wide lanes. The road markings are extruded 1mm upwards so they appear as distinct faces.
Finally, as you can see in picture 3, I applied a powder coat (white) appearance to the road markings and a concrete - tiles appearance to the rest of the bridge.
Step 4: Creating a Model of the Highway Under the Bridge
The sketch on the XY plane (picture 1) contains all the geometry to create the highway lanes. The road markings are the same as the ones on the vehicle bridge, except for one detail. The red arrows in the picture point towards rectangular profiles, which are the solid yellow border lines seen on the inside edge of the highway. On this sketch, there are also four circles which will be extruded to form the concrete support columns for the bridge (shown by the purple arrows).
When extruding the highway, I used the offset feature within the extrude tool. As you can see in picture 2, the extrusion starts from 10m below the vehicle bridge and goes up 4m, leaving 6m of clearance for semi-trailers and other large vehicles.
The second picture shows the finished vehicle bridge and highway. The appearance applied to the road markings is again powder coat (white) while the border lines are done in powder coat (yellow). I left the appearance of the highway as the default steel - satin, since it looks reasonably similar to asphalt.
Step 5: Creating the Curved Highway Ramps
This was perhaps the biggest challenge of the entire project. A curved ramp can't be created with a simple extrusion, so it requires a more creative approach involving the loft tool.
First, I created two sets of circles and lines on the XY plane (picture 1). The circles will serve as guide rails for the lofts later on. The line will be used to create a plane perpendicular to the circle.
Next, I sketched a rectangular profile (highlighted in red in picture 2) on the edge of the bridge. This will be where the ramp starts.
The final step before using the loft tool is to construct a plane at angle and sketch the profile where the ramp ends. In this case, it's a 4m by 4m square - since the highway is 4m thick and the lane is 4m wide. It's highlighted in blue in picture 3.
Finally, it's time to loft. See picture 4 if you'd like a visual, otherwise here are the steps:
- Select the rectangular profile from picture 2 as profile 1
- Select the square profile from picture 3 as profile 2
- Beside guide type, select centerline
- Select the circle from picture one as the centerline - it will guide the loft into a circular shape.
- Repeat this on the other side of the bridge
Step 6: Creating the Ramps for the Other Lanes
To create the ramps for the other lanes, I again used lofts. I first used the offset plane tool to create a plane away from the existing vehicle bridge. I then copy and pasted the original bridge geometry onto a sketch on the new plane. This will be where the existing vehicle bridge ends. Finally, it's a simple loft between the two profiles. Make sure to repeat this on the other side of the bridge.
Step 7: Creating the Carpool Lot and Bus Stop
The carpool lot was fairly simple to create, consisting of rectangular patterns and extrusions just like the road markings on the bridge. To model the bus stop, I first used the box tool to create the basic shape - it measures 18m long, 3m wide, and 5m tall. Then, I used the shell tool to hollow out the box and give it a wall thickness of 50mm. The appearance of the bus stop is glass - window.
Step 8: Design Objectives of My Bridge
The model of the surrounding area is done, and now it's time to design the pedestrian bridge to the carpool lot. The proposed path is shown again above.
Since the bridge will be built over a highway, and is also near a large neighbourhood, minimizing the construction time and noise is important. After researching some architecture, I was particularly inspired by brutalism and the idea of form follows function. I decided to base my design on modular concrete sections that can be built offsite and quickly assembled onsite. While not the most aesthetically pleasing solution, they reduce time, cost and noise, which are important in real life.
Step 9: Creating the Pedestrian Bridge
Since the pedestrian bridge runs over the highway, I decided to make it closed. The added winds and noise of an unenclosed bridge might cause nausea and discomfort to some people. I also decided to make the cross section circular to encourage laminar wind flow around the structure and reduce noise.
I sketched a profile of the bridge, making sure to include holes to place rebar (green arrows) to reinforce the concrete. The Make It Bridge contest page suggests considering the use of sensors, and that's what the hole shown by the red arrow in the center is for. A laser could be placed in the hole and beamed off a reflector at the other end to measure how straight the path is. It could help engineers determine whether or not the bridge is within its tolerances and if it's still safe.
To duplicate the 16m long modular sections, I used the move tool. Select the first modular section, click create copy (as shown in picture 2), and drag it out using the arrow icon. Fusion360 will help you by snapping it into place.
Step 10: Creating Elevators at Both Ends of the Bridge
I briefly explored trying to make accessibility ramps, but decided it wasn't feasible. Wheelchair ramps are limited to 5 degrees of incline for user safety and comfort, and the bridge is 10m above the ground. Switchbacks, or zigzagging ramps, are a possible solution, but they're only used for small elevation changes.
I designed elevators instead, using joints to demonstrate their functionality. I'm using a slider joint, because the elevator moves along one axis. There are two mistakes that you might make if this is your first time playing around with joints. First, make sure both parts involved in the joint are components. This will not work if they're only bodies. Second, select the component that will move relative to the other one first, and then select the other component. In this case, I selected the elevator first, and then the elevator shaft. To create an elevator at the other side of the bridge, I copy and pasted (ctrl C + ctrl V) the elevator shaft and the elevator and moved them into place.
Step 11: Adding Spaceships
I decided to put a spin on the scene and added some sci-fi inspired spaceships instead of cars and trucks. I've linked all the files below if you'd like to take a closer look at them.
When creating the ships, I added lots of curves and pointy edges. Fillets and the create form environment are both useful for creating rounded surfaces. The cone shaped engines were created by creating lofts between circular profiles and points. I also made use of shiny appearances for the bodies of the vehicles (like platinum - polished) while using other colours like red and black as accents.
I imported the ships to the bridge model, duplicating them and aligning them using the move tool. I positioned some ships as if they were about to change lanes, and tilted some ships to create the impression of a banked turn.
Coruscant Landspeeder
Coruscant Skyways Authority
Coruscant Tailfin Ship
Coruscant Wood Ship
Step 12: Done!
And that's it! I had a lot of fun working on this project and discovering some of the features of Fusion360. I hadn't really used the animation feature a lot so it was nice getting to use it. The rendering environment in Fusion360 didn't seem to work so well - maybe it's because the model size is too large. Thanks for taking the time to read this Instructable. I hope you've learned something from this Instructable, and feel free to leave any comments you have below.
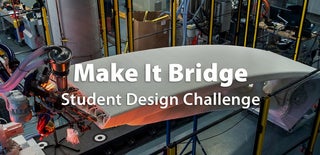
Runner Up in the
Make It Bridge