Introduction: Automated Motorized Turning Neck for 12' Giant Home Depot Skeleton and 12' Inferno Skeleton
Would you love to make your awesome 12' Home Depot Skeleton or Inferno Skeleton even more awesome?
This Instructable will teach you how to make an animatronic rotating neck for your 12’ Home Depot Skeleton or 12’ Inferno Skeleton. This will allow your skelly to look around randomly anytime it is on. The motorized animatronic neck looks lifelike and will bring another level of wow-factor to your display! I designed this in Tinkercad to use as many off-the-shelf parts as possible. Enjoy!
Supplies
Price: Materials List:
$ 1.38 (8) body screws #6 x 1/2” screws https://www.homedepot.com/p/Everbilt-6-x-1-2-in-Phillips-Oval-Head-Zinc-Plated-Wood-Screw-12-Pack-808081/204587432
$ 1.38 (2) Servo housing screws #8 x 1-1/2" https://www.homedepot.com/p/Everbilt-8-x-1-1-2-in-Phillips-Flat-Head-Stainless-Steel-Sheet-Metal-Screw-2-Pack-801361/204275464
$ 20.00 (1) Servo –Feetech FT5330M available on Amazon here: https://www.amazon.com/FEETECH-Voltage-Waterproof-Digital-Aluminium/dp/B097DWW6PY/ref=sr_1_1?crid=1QWGKWFN0MHHR&keywords=feetech+ft5330m&qid=1663206104&sprefix=ft5330%2Caps%2C200&sr=8-1
or on ebay for usually $10 cheaper (just search it).
$27.50 (1) Motion circuit board – https://www.thercgeek.com/category/Random-Servo-Motion-Generator-p397002944
$2.55 (1) Set of male/female DC cable 2.1mmx5.5m 12v 5A 18AWG – https://www.ebay.com/itm/201031851120?hash=item2ece6e9c70:g:wjwAAOxyVLNS8Sc&amdata=enc%3AAQAHAAAAsCIENSrNZdcDOX2SvQMfI%2Btzicn08uEUZdW0R968WQRbjSZ9p%2BjKAF1nKXZm%2BmMIAuKZBNeMG8N6jqfLpNkD50uu40N9F7wSCHyejxZO1R9tDdaDGj6KRAu7VKJpVNUM7jJrGN7iSTwBHnwUa0NHXyULBqeynwo%2FJN7ywkkYTStCxcAfNsbz%2B1mxw1mv6KcEXpfoO0kK9yzeV39SHapfYPxBCNDtQgTg4vNUWZznfauR%7Ctkp%3ABk9SR7LNnZbaYA
$9.86 (1) Main body tube – 2”x 2’ pvc pipe https://www.homedepot.com/p/Charlotte-Pipe-2-in-x-2-ft-PVC-DWV-Schedule-40-Pipe-PVC072000200HA/100585960
$2.35 (1) Inner core tube – 1” x 10” Schedule 80 pvc pipe https://www.lowes.com/pd/LASCO-1-in-x-1-in-x-1-in-dia-x-10-in-L-Schedule-80-Nipples-PVC-Fitting/3381532
$.91 (1) PVC retaining ring cut from coupler - https://www.homedepot.com/p/Charlotte-Pipe-1-in-PVC-Schedule-40-S-x-S-Coupling-PVC021001000HD/203811385#overlay
$ (1) Set of 3d printed items (link below in steps). My parts were printed free by my public library. You can also send files to online print services for a fee or print them at on your own.
$ 2 (1) 10-24 setscrew 3/4" long for regular skelly, 1/2" long for inferno
$ Various: Solder, flux, foam tape, pvc or other plastic glue
This project assumes you have some experience with basic shop tools and soldering. Please don't hurt yourself.
Tools Needed:
3d printer (or use on-line print service)
Chop saw
Dremel tool
Countersink drill bit
Drill or drill press
10-24 tap (or use bolt to thread hole)
Sandpaper, file
Soldering Iron
Glue gun
Phillips Screwdriver
Flat/Phillips jewelers screwdrivers
Scissors
Wire cutter/stripper
Step 1: Prepare Main Body Tube
Cut a piece of 2" schedule 40 pvc pipe that is 4.75" long making sure the ends are straight. Measure and draw a rectangle on one end that is .825" wide and 1.65" deep. I used a mill, but a Dremel works fine. The servo will slide down into this. Measure and drill 3 holes all the way through the pipe as shown in pic. This is best done on a drill press, but a Dremel or drill can be used in a pinch. Use the counter sink bit to allow all screws to be flush with tube.
Step 2: Prepare Inner Rotating Tube
Cut a piece of 1" schedule 80 pvc pipe that is 5.725" long from the 10" pipe nipple. Cut a ring from the pvc coupler that is 3/4" wide (I used a lathe, but a Dremel works - keep the ends as straight as possible). Sand the inside of the ring until it can slide all the way onto the grey tube. Glue it onto the tube 1/8" from one end (use pvc glue or plastic glue). Use a file or dremel to create a groove that is 1/8" deep and .5" wide.
Step 3: Output and Prepare 3D Printed Parts
I designed the 3D printed parts in Tinkercad www.tinkercad.com which is a good development platform for beginners. Download and 3D print the parts from the links below.
*Note – Different 3d printers hold different tolerance. I output parts on several machines and they all fit slightly different. You may have to sand the outside of the servo housing to get it to slide into the tube. A small lathe is also useful for this.
I output my parts in white filament, but you might also decide to use green or a darker color for the inferno version. Nylon works best.
Prepare the lower servo housing half by countersinking the two holes. Attach it to the servo housing top with the two long screws (The two screws MUST sit flush). Test fit this into the white tube. If it doesn't fit, you may have to sand it.
Next, take the flange bushing and make sure it is able to slide onto the grey tube easily. This needs to be fit inside the white tube as square as possible and the grey tube needs to be able to rotate freely inside of it. Sanding (or lathe is handy) work may be required. Take your time as this piece needs to operate smoothly with no binding! It needs to be able to plug flush into the bottom of the white tube and the grey tube needs to be able to rotate in it smoothly. You don’t want it tight at all, but you don’t want it so loose that it wobbles.
**Note - I combined a couple parts from earlier drawings and made the updated bushing and flange collar into one piece. Easier to assemble.
Next, select which model you are choosing. There are two different torso collars - They are labeled in the pic above.
Take the lower flange and the torso collar and fine sand their mating surfaces. You want them to rotate/slide easily with no resistance.
Make sure the grey tube can fit into the collar. Sand or lathe as needed. This fit can be tightish as we will attach it to the tube.
Upgrade Option - Use a lathe to make the Flange Bushing out of HDPE, Nylon, or Delrin plastic to be much more smooth and slippery. This allows easier motion and exact fit.
Servo Housing Top
Servo Housing Bottom
Bushing Flange
Skelly Torso Ring
Inferno Torso Ring
Step 4: Prepare Servo for Mounting
I selected this servo for several reasons. It is water resistant and it has metal gears and a reasonable amount of torque. Take the servo and cut off the mounting tab on the side AWAY from the wire. I used a mill but a Dremel works fine. Install two rubber grommets in the other tab’s holes and install the little brass inserts. Cut a couple little squares of double-sided foam tape and stick it to the top of the servo on the end with the tab removed. This will allow the servo to sit level when screwed down.
Once you have confirmed the servo housing fits in the white tube, unscrew the halves. Install the servo with two provided tiny screws. Select the large servo arm and cut the ends off so its length is the diameter of the grey tube's ring.
Use two long screws to attach the two halves together. Use a zip tie to keep the servo wire out of the way for now.
Step 5: Prepare Your Bushing Flange to Match Your Skelly or Inferno Head
Unscrew the round plate from the bottom of your 12’ skelly or inferno's head and save the screws. You can get fancy and match drill the holes in the large disk like I did, or you can just drill 4-6 small holes around the perimeter.
I made a photo copy of the screw patterns and and transferred it onto the flanges and drilled them. *Note – when installed, the side with the little hole will face forwards in the skelly.
Step 6: Prepare Your Torso
Remove the round plate that is is screwed onto the neck of the torso. Prepare the power wire by removing it from the grommet with a plyers and feeding it up through the neck hole. Get a piece of grip tap (or get some medium sandpaper and cut a 1/2" wide strip a couple inches long). Attach this vertically on the steel neck bar with superglue. This will help prevent the grey tube from spinning on it once tightened down.
Step 7: Assemble the Body and Rings
Slide the grey tube into the flange bushing and slide into the white tube and attach with two small screws. (when predrilling these holes, try to not go all the way through the bushing. You don't want to create any bumps or anything that will restrict the shaft from rotating.) Predrill and attach the bottom flange. Make SURE the little hole is facing forward (the power wire feeds through this).
I used some lithium lubricant on all the rotating pieces. You want it to operate smoothly without any rough spots.
Slide the torso ring onto the bottom of the grey tube. NOTE - There are two versions, use the correct one for your application!
Step 8: Prepare the Circuit Board
While researching construction on this project, I spent a TON of time on the web looking for an easy circuit that would randomly move the servo without having to do any programming. This one works great and can actually control up to two servos to operate randomly. Perfect for my build!
There are three adjustments on the circuit board. Make adjustments with a tiny flat screwdriver per picture. It is recommended to set them for slow and sporadic movement to not put stress on the servo or the skelly parts. Setting for fast jerky movements also causes power spikes and may shutdown the power supply.
Cut three of the pins off as we will only be using one channel and need the space for routing wires. Use some insulating tape between the servo's metal body and the back of the circuit board. On the right side of the board, we will only be using the positive and negative pins. You can cut the third one off. Bend one pin slightly forward and one slightly backward. Hot melt glue the board to the servo. Plug in the servo to the left side of the board with the brown servo wire to negative. Carefully bundle up the wire and hot melt glue it in place. This all needs to be able to fit into the white tube, so take your time.
Time for the power wires! *** NOTE!!!! - For some reason, they swapped the plug polarity on the skelly and the inferno models, so make SURE you use the right one or this won't plug in correctly when you are done!!!. Run the plug through the top servo housing hole. Run the other plug up through the torso ring and bushing flange. (NOTE - Make sure you select right version either skelly or inferno). continue threading plug wire up through the flange and through the bushing flange hole.
Cut two little pieces of heat shrink tubing and slide onto wire and solder red to red and black to black. Slide heatshrink over joints and shrink it.
Slide the power wire back up and strip two small areas in the each wire to solder the read to the positive pin on circuit board and black to the negative pin. Add a tiny bit of hot melt to make sure they don't touch and to keep wire from being pull the excess back downward so the joints and heatshrink are below the top of the bushing ring so to not interfere with the rotation of the grey tube.
Testing time! Plug in the power wire coming out the area next to grey tube into your skelly or inferno neck plug coming out of torso. Turn the power on using their regular switch. After a few seconds, the servo will begin to randomly move from side to side. Take note of the wire travel in the slot. The torso ring needs to be mounted so the wire doesn't get chopped or crimped as it goes back and forth!
A note about power supply - The power supply that comes with both is 5.9v 1.5 amp which is right on the edge of being able to run everything. When turning it on, you may sometimes find it goes into shutdown mode and you have to press the power button a couple times to get it to come back on. You can upgrade this part if you wish to a 2-3 amp model (look for a waterproof one on Amazon for under $10 if needed).
Step 9: Torso Ring
In the last step, you loosely installed the torso ring with the wire feeding up through it first. Now, you will center the slot in the ring over the hole in the flange plate. NOTE - The "Center" needs to be the average of far left and far right travel when you tested. You want the wire to never get pinched when permanently secured). Use 2 small screws and attach it to the grey tube (you don't want the screws to go all the way into the inside of the tube!) You want the ring to be flush to the bottom of the flange, but still enough clearance to not restrict movement. Next, drill a 5/32" hole on the side opposite of the slot. This will go through one side of the grey tube. Use a 10-24 tap and thread the hole. Install a 10-24 setscrew (1/2" long for the inferno version, 3/4" long for skelly version).
Step 10: Final Assembly!
Take your skull and unscrew the circular base plate if you haven't already. Carefully fish out the plug that powers the eyes. This will tuck inside the skill after you plug it to the top of the motor cylinder. Lower the cylinder into the skull with the wire clearance slot facing frontwards towards the face. Use the screws you pulled out to attach the motor cylinder.
Take the wire from the neck of torso and plug into the bottom plug on the motor cylinder. Make sure set screw is backed out far enough to allow the grey tube to slide down onto torso metal pole. Gently move the torso front to back to center the neck hole around the metal tube and lower the head down into it. The lowest round flange of the torso ring should fit down into the torso hole. Tighten the set screw that will clamp the grey tube down to the metal torso pipe. Plug in the skelly's power supply to the wall and hit the switch and watch him come to life!
ENJOY!
Step 11: Enjoy Your Finished Project!
Creep it real!
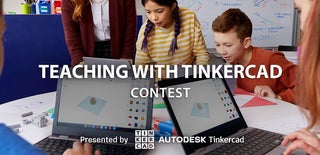
Participated in the
Teach With Tinkercad Contest