Introduction: Moving Cloak of Levitation - V1
Hello hello hello! I'm back from the void and here with an 'ible on how to make an astounding astonishing mystical magical moving Cloak of Levitation!!
My inspiration for this? Well, I'm moving somewhere a bit colder than I'm used to, and I wanted to have something warm to make it through the winter (what, I'm planning ahead). But rather than being a logical human and buying a coat, I decided to do something new, something strange, something fantastic! A cloak!
And then: there was an idea. Why settle for a cloak when I could make the cloak?
Currently, only the upper portion of the cloak (around the collar piece) is animated, but I'm hoping to make another model with more servos and also sensors! In the meantime, Cloaky can dry your tears away, squish your cheeks, or give you a light slap to stop you from falling asleep in Algebra.
Anyway, read on to learn how to make this seriously loyal piece of outerwear!
If you haven't got time to read everything and need to rush off to save half the universe (understandable, it's a long 'ible, have a nice day), skip to step 17 to watch a video of the cloak moving!
And please consider a quick vote if you were intrigued by this project! Don't forget to share with your fellow makers and MCU fans as well :)
Step 1: Materials and Tools
Materials
- 1-2 old bedsheets
- 3 yards of dark red fabric
- 1 yard of Pellon interfacing
- Spool of multipurpose red thread
- 4 microservos
- Arduino Nano or similar
- Breadboard cables
- Extra wire
- Vector boards
- Velcro
Tools
- Large scissors (preferably fabric shears)
- Small scissors
- Measuring tape
- Highlighters/markers/Sharpies
- Glasshead pins
- Safety pins
- Sewing machine
- Extra needle (to sew certain sections by hand)
- Mannequin or willing victim
- Mini hot glue gun and refills
- Soldering iron and accompanying things
No amusing narrative for this bit, but be patient-- it's one of the most valuable traits a soldier or student can have (Captain America, 2017).
- The cloak took me 108 hours to complete. Yep, I kept track. On the bright side, the cloak should take you substantially less time to complete if you avoid making even half the mistakes I did.
Step 2: Prototyping Main Cloak
- You'll need around 1 old bedsheet (2 if you mess up).
- The 2nd picture above (filched and modified, original from this very helpful thread, https://www.therpf.com/showthread.php?t=259750) should give you an idea of what pattern to trace on the bedsheet. Measure your height shoulder-to-floor and scale accordingly.
- Keep in mind that the cloak is asymmetrical-- very asymmetrical. Image references on https://imgur.com/a/CAMhq and https://hollywoodmoviecostumesandprops.blogspot.c... if you need them.
- Use a measuring tape and highlighter to measure out landmarks on the bedsheet. Sketch an outline of the cloak.
- Also sketch lines to split the cloak into 4 (or more, if you'd like) panels.
- Cut out the outline. Try it on. Trim edges and tape on extra fabric as needed. Sketch new panel lines as needed.
- Once your panels are mostly set, sketch swoosh lines within the panels.
- Outline the final panel and swoosh lines with a darker or differently colored marker.
- Cut along panel and swoosh lines to end up with multiple, smaller pieces.
All right! First off, a quick explanation of some cloak terminology I may have made up on the spot:
Panel: A vertical section of the cloak; boundaries extend from the shoulderpiece (that white oval in the prototype picture) to the floor.
Swoosh: A horizontal section of the cloak; boundaries extend from the left side of a panel to the right side of a panel.
You can check the picture above if you need more clarification!
So here's a quick, amusing/pitiful narrative. When I was starting out, I may have tried to make a miniature model of the cloak with bedsheet scraps. I didn't have a mannequin, and I certainly didn't have a mini mannequin. I needed a substitute, something vaguely shoulder-shaped.
Glass of water? Nope. Jug of orange juice? Nah. Bottle of horseradish? ...close enough!
I made a cloak prototype with the bottle of horseradish, scaled it up onto an entire bedsheet, and made the discovery that a bottle of horseradish is not a near approximation of my shoulders in real life.
Shocking, right? You didn't see that coming?
Step 3: Picking Out Fabric
- cheat code: Richloom Studio Multi-Purpose Decor Fabric, Jerome Spice, approximately 3 yards
Some general tips if you're picking your own cloak fabric: go for upholstery or something with a noticeable texture. Try not to choose excessively neon colors; stick with the dark side (it had Loki).
And don't forget that the swooshes in each panel alternate between the front and back of the upholstery-- make sure both sides of the fabric look nice.
- Surprise, upholstery fabric is expensive! You can usually get discounts online; try to avoid paying full price.
- Avoid excessively flammable fabric/double check you're using insulated wires. Just in case.
- Bring a sample of fabric with you for comparison if you go to different stores; pictures taken on your phone might not be super accurate. Also don't forget to bring a sample if you're buying thread, trim, or other fabric to match.
- Wash the fabric when you get it! Not only to shrink it, also to get rid of dust/bugs (sorry spidey) and also because you won't get another chance to actually wash it.
Step 4: Cutting Fabric Panels and Swooshes
- Lay out the bedsheet pieces on top of the fabric.
- Arrange the little panel-swoosh chunks so they optimize space, and don't forget to flip swooshes upside down so that the cloak pattern alternates between the sides of the fabric.
- Trace lines, add approximately an inch of fabric to each panel side to allow for hem space between panels, and cut.
So the way I cut out the panels originally (the way shown in the pictures) isn't exactly an optimized strategy-- I opted to keep the panels of the cloak together, but rotate them in a sort of staggered pattern so that the grain would change direction in a subtle and enthralling effect. Emphasis on subtle: when you're showing off a moving cloak, people don't often note the intricacies of grain direction in the fabric...
Also, I cut the fabric before I decided to do the whole swoosh-fabric-alternating thing, so I had to resort to cutting extra swoosh pieces from the remaining fabric I had. Luckily, 3 yards should give you plenty extra (...if you're short like me).
- There will be dozens of near-identical fabric pieces strewn around. You should label the pieces' inner sides' with their draft number (e.g. version 1, 2, or 14,000,605) and panel/swoosh numbers.
- This will require a wide open space for laying out fabric.
- You will also very likely make a complete mess of your room/workspace. (i am groot I AM GROOT)
- Swoosh shapes should be the reverse of the outer fabric shape. Flip the relevant bedsheet sections before tracing them onto the outer fabric.
Step 5: Sewing Fabric Together
- For each panel, fold and pin swoosh sections over each other.
- Stitch those swoosh sections together. The fabric sticking from the seam should be on the inner side.
- Stitch the panels together similarly.
my mom showing me how to use the sewing machine: Look. Pretty, isn’t it? Perfectly balanced, as all things should be. Too much to one side... then the other... you try.
me using the sewing machine: the needle gets gummed up, the thread spool gets stuck, the lower spool gets all frayed, I sew the wrong fabric pieces together, there are alarming loud clacking noises, I forget to flip around the fabric, the machine jams a billion more times, the light thing overheats, I tear out some stitches and nearly rip the fabric apart, I sew over the glasshead pin thingies, the lower spool runs out of thread again, I finally finish a section but whoops the thread wasn't in the needle
- Maybe practice beforehand if you're not great with sewing (like me); cut up those old bedsheet prototypes and sew some panels and swooshes.
Step 6: Cloak Shoulder
- The main idea here is to sew an oval of fabric to the empty shoulder space.
- Before you do that, cut out multiple ring-shaped pieces of fabric and sew them to the empty shoulder space as a sort of trim.
- Sew the oval between the layers of trim.
- By hand, sew the edges under so it looks slightly less raggedy.
So this looks super complicated-- rest assured, I had no idea what I was doing at this point.
What I basically did was use a fabric glue to sandwich the oval of fabric between the rings of trim.
Did it work? Sorta, if ending up with a gluey sticky mess counts as "working". After gumming up all my needles (including the sewing machine needle), I decided to stick the cloak in the washing machine for a bit, which got rid of the worst of the glue. And thus, I discovered that my nice red Jerome Spice fabric had a particular penchant for fraying to the point of disintegration in the washer. Okay, okay, it wasn't that bad, but still.
Long story short, I stopped putting off hemming all the edges of the cloak, re-stitched the shoulder by hand, and made it through this particular set of obstacles somewhat satisfactorily.
- Avoid using glue.
- Be careful when washing upholstery.
- Don't sew the oval to the collar space, sew it to the shoulder space.
Step 7: Fail - Inner Lining and Patterning
- Nothing to see here, this section is completely still, it's invisible, nothing to see here at all, move along. (...hi Drax)
Here it comes-- the first total failure of the 'ible!
Okay, okay, making a lining for the cloak wasn't a total failure. I just sorta ran out of time and also realized that the cloak was kinda heavy and the lining looked really weird when I sewed it together and I didn't have dye or anything to make the patterns--
Fine, I was too lazy to finish it. ¯\_(ツ)_/¯
Same thing goes for the patterning I was trying to make with some leftover fabric scraps I picked up at the store. Advice: don't underestimate the time it'll take to cut out lots of little bouncy circles or the time it'll take to cut out little sophisticated ribbon thingies. It's kind of like the grain patterning thing: save the effort for the more noticeable parts of your costume.
- Surprisingly, the inner lining shape should be the reverse of the outer fabric shape (my first mistake).
Step 8: Prototyping Collar, No-Duct-Tape Mannequin
- You can skip to the next step and use the general pattern I made, but if you want to prototype your own collar, it's fairly straightforward.
- Cut out a kind of U-shaped piece of fabric.
- Place fabric on a mannequin or willing victim, and trim edges until it reaches the desired shape.
- Secure the upper portion and lower portion of the fabric with tape and wads of bedsheet, so that the collar stays in the correct shape.
- Use a marker to trace a halfway line around the second collarpiece.
- Make quote mark things (") to remind yourself where the pieces of fabric fit together.
So for this bit, I finally got to making a mannequin-- not by using the well-known duct tape method which offensively assumes that you have friends, but rather by making a mannequin out of toilet paper and some old t-shirts. Worked pretty well, I might make another 'ible on it later.
I also tried to make the collar out of clay-- I planned to let it sit on my shoulders and dry. This probably would have worked, except I had a hair appointment and had to discard my amazing work on the couch.
Ah well. It was much easier to do the collar with interfacing anyway.
- There should be 2 major parts to the collar: the U-shaped base and a strip of fabric on top of it which is the actual "collar" collar.
Step 9: Building Collar
- Lay out the collar prototype thing you've made on top of some interfacing.
- Align the quote mark (") looking things, and sew down landmarks to keep everything stable.
- Crease the top part of the collar and sew down two other landmarks to keep it creased.
- Hot glue the join between the two pieces to make it more stable.
Hmm... can't really think of any funny stories to go here.
I ended up doing this twice for a double layer (recommended if you have thin interfacing or if you want to minimize wire pokiness later on), if you're wondering why the pictures don't match up completely.
(Remember, if you have questions, feel free to comment and I'll get to them as soon as I can!)
- Remember to stay hydrated!
Step 10: Fail - Flexinol
- Move along, move along. (Earth is closed today.)
Ah, flexinol. Where to begin? Flexinol, or muscle wire, is basically a type of wire that assumes a recorded shape when you run a current through it.
This was easily the most time-consuming part of the project, and I ended up not using it anyway... Here's some of the stuff I did/went through:
- Read through and analyze the entire flexinol datasheet.
- Plan flexinol wiring using knowledge of Ohm's law and-- and that's about all I know. ¯\_(ツ)_/¯
- Code flexinol circuit. This part went along fine. Ish. I had this amazing plan for a machine-learning interface that would learn from the environment and activate certain wires... board wasn't big enough, though, so I downgraded that to something that would activate different wires based on the cloak's "mood"... board still wasn't big enough.
- Test the flexinol circuit. Add tubing insulation stuff to the flexinol.
- Solder together a couple MOSFET kits I got to be able to use more power.
- Realize I had no clue what to do next. Then realize that the flexinol wasn't an amazing perfect substance that would magically bequeath life to my cloak. More specifically, it heated up a bit too much and wasn't as strong/manipulable in 3D as I thought it would be.
- I even conducted burn tests-- since flexinol involved heating up wire, there'd be a non-negligible risk that the cloak might catch on fire. Since I'd already bought my fabric and had no idea how flammable it was, I used matches to burn small swatches of the fabric in the sink...
Shuri to me: I'm sure you did your best.
- If you didn't notice, this was a Disastrous Failure that ate up hours and hours of time.
Step 11: Coding Servos
- cheat code: file included above
Kinda mentioned this before, but I had this AMAZING plan and all this code to create this seemingly sentient cloak with sensors and full-cloak movement but I had to scrap it cuz I didn't have the right stuff to run it on...
Anyway, the code above does the Doctor Strange movie's tear-wiping thing and then slaps your face a few times.
:)
The code is a little inefficient and cringey but I'll work on improving it when I get some sensors!
Attachments
Step 12: Attaching Servos to Collar
- Cut two small strips of interfacing for each servo.
- Use a hot glue gun to glue a strip of interface accordion-style to the bottom of the servo to get a level surface.
- Hot glue that surface to the base of the collar; also hot glue the side touching the top of the collar.
- Put dots of glue on the other strip of interface and secure the servo.
- Put a dot of hot glue towards the end of the wire to secure it a little.
- Make sure that the moving part of the servo has free space to move.
Step 13: Soldering the Arduino
- Place the Arduino Nano on the vector board.
- Place breadboard cables near the relevant pins (5, 6, 9, 11 or whatever digital output you use; 5V; GND).
- Solder each digital output pin to its breadboard cable.
- Wind some wire around the 5V group and the 5V pin; solder the wire onto the pins.
- Repeat the winding/soldering for the GND group and pin.
Disclaimer: I have no actual idea what I'm doing here, just fluent in Google.
- Be sure not to solder the 5V and GND pins together.
- Double check that the pins on your board support PWM or similar output.
Step 14: Adding the Arduino
- Place the Arduino on top of the collar interfacing, in the area that will be about between your shoulders.
- Sew down all four corners of the board.
- Cut slots next to each of the groups of wires and pull the wires through.
- Secure the wire openings with dots of hot glue.
- Connect each servo cable to a digital output, a 5V, and a GND.
- If you'd like, hot glue some Velcro to securely sandwich the wires between the interfacing layers.
I placed my Arduino near the bottom edge of the cloak collar, which was fine, but in retrospect I wish I would have placed it a bit further up-- that way, it's easier to contain/spread out the wires that lead from it below the interfacing. The advantage of keeping the Arduino further down, though, is that later on you'll have more room to Velcro down the collar covering.
Note that if you only have one layer of interfacing, you'll be sandwiching between the interfacing and the cloak material.
- By the way, since the Arduino Nano's built-in LED can be a bit bright, I just put a tiny square of interfacing over it (if you were wondering what that thing in the picture was).
- It helps to keep track of which digital output leads to which servo, but you can always just check this later by running some code.
Step 15: More Pictures, Extending Servos
- Use hot glue to attach a mini hot glue stick (improvisation!) to the plastic attachment thingy from a microservo.
- Repeat for each of the four.
- Also hot glue the top portions of the hot glue sticks to the collar interfacing.
Above are a couple extra pictures of the minor chaos that inevitably resulted from the previous step! Fun story, I had some long wires that I braided-- I was planning to place the Arduino Nano on the shoulder area, then realized I didn't really need to reach it anyway. So I placed the Arduino on the back of the collar instead, and never got to use all of that nicely braided wire. Oh well.
- When gluing the hot glue sticks, be sure to securely glue to the servo attachment and to the interfacing. (see the picture above for an example of the servo attachment slipping)
- Don't hot glue the part of the stick close to the servo to the interfacing; leave room for the interfacing to bend.
- Try to avoid using heavy-duty high-temp hot glue for this; a smaller hot glue gun makes it easier to tear down and restart (and is more than strong enough).
Step 16: Making the Fabric Covering
- Lay out the remaining portion of red fabric on top of the collar.
- Sew some earmuff-ish things to cover the tips of the collar. Basically sew two sides of two long parallelograms together, then flip inside out.
- Cut out a U-shaped piece of fabric to cover the base.
- Sew the earmuff pieces to each end of the U-shaped fabric.
- Cut and sew smaller pieces of fabric to fill in the gaps.
- Fold over the edges of the U-shaped fabric and sew the folds.
- Add velcro to the inside of the earmuff (helps to flip it inside out before you do this) and to the tip of the cloak.
- Add some other pieces of velcro all over the collar to help secure the covering.
So basically-- this step is just making a highly complicated pillowcase for the collar. It's not completely necessary to make the collar covering detachable... the main thing is that you should have access to the servos and to the Arduino in case something snaps or catches on fire or something.
- Hopefully you had a remaining portion of red fabric...
Step 17: Upload and Test
- Attach anything left: hand-sew or hot glue down sections of the cloak that are sticking out.
- Hot glue some vector boards onto the ends of the collar piece.
- Hot glue strips of Velcro to each end of the collar piece, and hot glue matching strips to a T-shirt.
- Also add Velcro to the back of the collar and back of the T-shirt.
- Make any final touches-- it helps to have a second person pin down any remaining areas sticking out.
Turns out vector boards actually work really well as cloak attachers, since the hot glue oozes through the holes and keeps the board from separating from the interfacing.
- Make sure your T-shirt is made out of relatively heavy material!
Step 18: Endgame
And voila! 108 hours later, you have a seriously loyal piece of outerwear!
Like I mentioned before, I'm kind of sort of maybe planning on a second version of the cloak, just because I have a clearer idea of what to do now. I'd especially like to add some more servos and maybe some sensors like I originally planned, so here's hoping.
That's about it! And if you've got any questions, feel free to comment below! Thanks for reading!
Helpful links:
https://hollywoodmoviecostumesandprops.blogspot.co...
https://www.therpf.com/showthread.php?t=259750
- Kudos to you if you read the warnings after the instructions :)
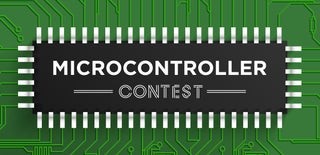
Participated in the
Microcontroller Contest