Introduction: Nerf Light Gun Controller
Ever since building my Nerf Vulcan Sentry Gun, I wanted to modify a Nerf blaster that allows me to control a computer and play games.
It took me a long time to get started, but I can finally show you the results. Ever since I have finished modifying the blasters, I can't put them down. Playing them is insanely fun and I hope you enjoy the mod as much as I do.
The blaster can not only be used to control a PC but also to play games with for example a RetroPie or MAME.
Step 1: What You Need
There are two different light gun sets, one that is connected with a wire and a wireless version. Getting the Bluetooth version to work is a bit trickier than getting the wired version to work, so you will have to decide which one you prefer. Btw. I am not sponsored by Ultimarc, I bought the kits and am not getting any money for promoting them (they have no idea I am writing this instructable).
Material
- NERF Zombie Strike Doublestrike Blaster (e.g. from Amazon #CommissionsEarned* or way cheaper used)
- Light Gun Set
- Wireless + LED Bar
- or Wired (Complete kit)
- + Internal Connector
- 6x6x7 mm push button switch (e.g. from this kit #CommissionsEarned*)
- Two Hinge Lever Micro Switches (e.g. from here #CommissionsEarned*)
- M8 washer
- Brass Knurled Nut M3x6x5 (e.g. from this kit #CommissionsEarned*)
- M3 screw (12 mm)
- Stainless Steel Rivet Nut
- Two-component glue
- Hot glue
- Wires + heat shrink tubing
- Optional: 3 mm acrylic glass (I used black acrylic glass that is ir transparent)
Tools
- Dremel
- Screwdriver
- Soldering iron
- 3D printer
- Optional: Lasercutter
* As an Amazon Associate I earn from qualifying purchases.
Step 2: 3D Printing + Laser Cutting
A Nerf dart is slightly smaller than the electronics that need to go into the barrel. Therefore, I have created a few parts that can be 3D printed. You do not really need a 3D printer. All the parts can also be replaced with cardboard, hot glue, and reusing parts of the plunger, but a 3D printer will make everything a lot easier.
The electronics should fit into a Nerf Rival blaster without any problems, but I wanted to go with a small, lightweight, and cheap blaster. You can of course pick whichever blaster you would like.
Since the two kits (wired or wireless) are slightly different, you will have to download the files that fit your kit.
I started by smoothing the prints with THF. Afterward, I used a primer filler, wet-sanded the pieces and spray painted them black. I have written a whole Instructable on how to smooth 3D prints. You can find it here.
I didn't want to leave the front open and therefore I used black acrylic glass that is ir transparent to fit the opening I designed. The wired kit comes with a small piece of round acrylic you can use, but you will have to design your own 3D parts for it to fit. I have uploaded the file that can be laser cut to this step. It can be opened with Inkscape.
Step 3: Taking the Blaster Apart
Start by taking the blaster apart. Luckily all the screws are the same.
I used a Doublestrike, because I liked the idea of being able to reload with one hand. Sadly Nerf doesn't produce them anymore, but you should be able to buy used ones really cheap. Another blaster that would probably look great is the NERF Fortnite SR Blaster (#CommissionsEarned*).
Once you have opened the blaster, remove the plunger. Be careful not to lose the small plastic piece on top of the rail since we need it later on.
Step 4: Modifiying the Cocking Mechanism
The cocking mechanism needs to be modified since otherwise, it would block the trigger from moving.
Start by removing the small pin as shown in the first picture or remove the whole part by sawing it off. I decided not to saw the parts apart since I figured that I would be able to reuse the plunger for another project. This is also the reason why I 3D printed the parts to fill the holes in the body of the blaster. You can of course just saw the plunger apart and glue them in place.
The parts that need to be removed are marked black in the second image. I used a Dremel SpeedClic cutting wheel to do so. Be careful with the trigger and leave it where it is, since putting the small spring back in is a bit tricky. If it falls out, don't worry, it is a bit fiddly, but you should be able to reattach it so that it looks like in the second picture.
Step 5: Shortening the Spring
Next, we are going to shorten the spring. Not shortening it means that you will need quite a lot of strength to use the reload bottom. I also tried replacing it with a spring with a thinner wire but couldn't find one that worked well.
To shorten the spring, I once again used a Dremel SpeedClic cutting wheel. You will need to remove about 1.5 cm.
Step 6: Attaching the 3D Printed Files
The only difference in the 3D printed body parts is that the slot in the barrel of the wired version is slightly bigger. Therefore, this step is the same for both kits.
Use two-component glue to attach the 3D printed files to the Doublestrike.
Make sure everything fits by placing the two halves together before the glue is completely set. You can see where the parts go by looking at the picture.
On top of the spring, I placed an M8 washer since I was afraid that the cut spring might damage the plastic.
Glue the brass knurled nut in place as shown in the second picture. You might need a hammer to carefully push it in place.
Step 7: Wireless
Since the two kits are slightly different, we are going to start with the Bluetooth version.
I didn't want to remove the screw hole in the handle of the blaster and therefore it took me a while to make the electronics fit. As you can see in the pictures, I even had to make the PCB smaller and remove parts of the socket. Make sure that the plug can be pushed far enough into the blaster and be careful not to damage any conducting paths.
Once everything fits, glue the PCB in place with hot glue.
Placing the power socket PCB underneath the cylinder of the blaster would be a lot easier, but I figured that it would look a lot better to connect the cable to the handle.
Step 8: Wireless #2
Next, we are going to use the two 3D printed parts that are still left. They help you place the hinge lever micro switches, as shown in the pictures.
Glue the 3D printed pieces in place and make sure that the switches are working. Don't glue the switches in place just yet, because the wires still need to be connected.
Step 9: Wireless Wiring :-)
Finally, we are going to connect all the wires. I used a small amount of hot glue, to hold the PCB that goes into the barrel in place. If you are going to do the same, make sure that both sides of the blaster fit. The part I marked red in the first image is slightly angled and therefore won't fit if you glue it too close to the rail.
In the first picture, I have marked the position of the 6x6x7 mm push-button switch yellow. It has to go underneath the small plastic piece in the rail. Make sure that the push button is working. You might have cut a bit of the 3D printed part off.
The second picture shows you how to connect the wires. The longer wire must connect the trigger. It should be long enough for you to solder it directly in place without having to elongate it.
The wire that is on the left (in the picture) has to connect all the ground wires. The other two wires need to go to the other two switches.
The battery can be placed inside of the cylinder.
Don't forget to place the acrylic glass into the slot before assembling the blaster again.
Step 10: Assembling the Wired Version
Assembling the wired version is similar to the wireless version, but you don't have to worry about placing the power socket PCB into the handle.
All you need to do is to cut a small hole into the bottom of the barrel as you can see in the pictures. Then glue the 3D printed switch holder pieces in place as shown in the first two pictures.
Look at the previous step to see how to connect the wires. Once again, the 6x6x7 mm push-button switch needs to go underneath the small plastic piece in the rail.
I used some hot glue to prevent the wires from getting tangled in the spring. Make sure that all the switches work and that you have placed the acrylic glass into the rail in the front of the barrel before reassembling the blaster.
Step 11: Getting the Blaster to Work
Getting the blaster to work is simple since all you need to do is to mount the LED bar on the top of the monitor using the adhesive pads and to plug the controller in.
The movement of the gun should cause the mouse pointer to move. The pointer may not move to the edge or may go off the edge and bounce to the other side since the gun is not yet calibrated. Calibration is only required once. The settings are stored in the gun. You can download a program to calibrate the blaster here and here you can find detailed instructions on how to use the program and how to configure MAME.
MAME is a free emulator designed to recreate the hardware of arcade game systems. You can see me playing Duck Hunt in the intro step via MAME. So, check it out should you want to play some old school light gun games.
The wireless version can be added via Bluetooth to the devices. Here is a detailed instruction on how to install it.
Congratulations, you are done. I hope you enjoy this mod as much as I do.
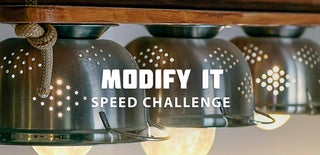
Second Prize in the
Modify It Speed Challenge