Introduction: Non-VESA Monitors and Computer Hardware Wall Mounts
Conception
This idea originated from a desire to organize the desktops of both a Graphics Work Station and a Twitch Broadcast Studio. Both dedicated applications were eye sores having excessive cabling tangles and a clutter of dangling support hardware.
Instructable Intro
The Instructable will begin by modifying the Mechanical Pivot connecting a non-VESA Dell Monitor to it’s base, so it can be attached to a wall or an articulating arm. This step by step process of disassembly, modification and re-assembly will render a 180-degree reversed monitor arm. The process is also reversible if you want to return the monitor to a desk top mount, in the future.
After the monitor modification section, I will present two different applications of equipment organization using dedicated aluminum tube wall mountings.
The first will be a detailed step by step, that will illustrate the principals of planning and hardware attachment specific to a triple monitor mount application.
The second will showcase an application of the principals previously established. This section is meant to inspire your creative energies.
My Instructable target audience is the novice. Those with advanced experience, can simply look over the photos and drawings to understand exactly how I did this, but I encourage you to read the exacting details of the step by step pivot modifications.
Recycled Materials and Hardware
All of the aluminum tubing, lag bolts, machine screws and other hardware used here, was all salvaged from products or projects found in industrial / commercial dumpsters. The re-claimed aluminum tubing was sanded and brushed to remove scars and scratches. The hardware was brushed and cleaned with mineral spirits. The only pieces of new hardware and material used is one aluminum tube used for the triple monitor mount, one plastic drywall anchor, zip ties, three 6 mm machine screws and double-sided mounting tape.
The Tools, Hardware and Materials list is composed of the items needed only for the first two sections of this Instructable, since the third section is only a gallery showcase.
TOOLS
Pencil
Black Marker
Masking Tape
Tape Measure
Yard Stick
Carpenter’s Square
Bubble Level
3/32” or 1/8” (slim blade) Standard Screwdriver
#1 Phillips Screwdriver
#2 Phillips Screwdriver
#3 Phillips Screwdriver
Metal File
Vise or Vise Grip Pliers
Needle Nose Pliers
Hammer
8 mm Wrench
7/16” Nut Driver
7/16” 3/8 Drive Socket
3” or 6” 3/8 Drive Socket Extension
3/8 Drive Socket Wrench
Electric Hand Drill with a ½” Chuck or Drill Bits with a ¼” Shank.
1/16” Drill Bit
11/64” Drill Bit
¼” Drill Bit
3/8” Drill Bit
½” Drill Bit
11/16” Drill Bit
HARDWARE
Three = 6 mm x 1.0 mm, 16 mm long Machine Screws, Phillips Pan Head, Stainless Steel 18-8
Three = 6 mm (or ¼”) Lock Washers, Stainless Steel 18-8
Two = ¼” x 2” Lag Bolts, Hex Head, Stainless Steel 18-8
Two = ¼” Lock Washers, Stainless Steel 18-8
One = ½” Dry Wall Anchor (Plastic) with #8 - 1 ¼” Pan Head Phillips Screw
One = 4D 1 ½” Common Nail
One = 3D 1 ¼” Brad
6” = 3M Scotch 4011 Exterior Permanent Mounting Tape, 1 in wide
10 = 6” Zip Ties
MATERIALS
1 ½” x 1 ½” x 45” (1/8” wall) Aluminum Square Tubing
Touch Up Paint (optional)
Fast Dry Latex Caulk (optional)
Monitor Modification
I have three identical 24” Dell 2340 Monitors, which I’ve used with my hobbyist level, CAD work station. I recently added a 32” primary monitor and I want to mount the three Dells, as support monitors, just above the 32”. All three will be mounted onto a single 1 ½” by 1 ½” square, 45” long, 1/8” thick wall, piece of aluminum tubing, which in turn will be mounted directly to a wall’s 2x4 studs.
Section 1 – Modifying the Monitor Brackets
Step 1:
Remove the monitor from the pivot bracket arm of the base (1). Un-screw the base from the bracket arm (2).
Step 2:
Use the slim blade standard screwdriver to separate the flat curved plastic fascia from the rounded plastic arm covering. Use caution and slowly pry the curved piece away from the flat piece to separate the internal clips (3).
Step 3:
Use the #1 Phillips screwdriver to remove the screw holding the curved plastic housing onto the metal arm (4). Then remove the screw holding the small plastic pivot cover onto the metal arm (5).
Step 4:
Use the 8 mm wrench to loosen the nylon self-locking hex nuts from their respective bolts. The bolts are square flattened on two sides, so the bolts won’t rotate while you loosen the hex nuts. Caution – Only loosen the nuts, don’t remove them yet (6).
Step 5:
Note the orientation of the two domed washers to one another in the middle of both the left and right pivot bolt assemblies (7).
Carefully remove one nut at a time and then
use the needle nose pliers to slide all the components off each bolt, noting orientation and assembly order of the parts. It’s best to line up all the parts in the order that they are removed from each bolt. Make two rows of parts, one for the left bolt and one for the right bolt (8).
The parts on each bolt are similar except for the travel limit cams with the bent tangs that fit into the small square slots on each side of the monitor latch bracket (9 and 10). Swap the hardware line-ups of the two travel limit cams with one another (11). For clarity compare photo 11 to photo 8.
Step 6:
Gently slide the two bolts out of the assembly and slide the latch bracket out of the arm’s yoke. Note – When the bracket is slid from the yoke, there are four identically tanged, flat bushings (12). Each is coated with white grease so they will probably stay in their positions. If not, remember to replace them with their tangs in the squared notches before re-assembly of the bracket and yoke.
Step 7:
Rotate the bracket 180 degrees (13) then re-insert it between the yoke and slide the two bolts into the assembly. Note - When the bolts are in place, the bracket can’t rotate any closer to the arm than the position shown in photo (14). This is because the bracket tabs hit the two screw stops mounted in the yoke. I’ve blackened the area of the tabs that interfere with the rotation (15 and 16). Mark your tabs similarly.
Step 8:
Dis-assemble the bracket and remove it from the yoke once again. Then use a vise or vise grip pliers to hold the bracket (17) and file down the blackened portion of the tabs so that those portions of the tabs, mimic the preceding tab curvature (18). While filing, periodically check the clearance by re-fitting the bracket with bolts into the yoke, until the bracket rotates without hitting the screw stops (19). Afterwards, make sure to file off any metal burs created on the edge of the bracket’s tabs.
Step 9:
Re-assemble the pivot assembly, making sure to position the tang flat bearings, dome washers, travel limit cams and the 180-degree rotated bracket into their proper positions (20). Use the 8 mm wrench to tighten each assembly until the pivot only moves when adequate force is applied.
Step 10:
Re-assemble the plastic housing and fascia pieces onto the arm in the reverse order of step 3 and then step 2 (21).
Section 2 – Mounting Everything to the Wall
Before beginning, I’d like to point out the ergonomic choice of monitor placement at my desk / workstation. There is a 7” gap between the front desk edge and a wall. The bottom of a wall mounted 32” monitor is lowered into that gap approximately 2”.
Seated in my chair at normal working posture, looking straight ahead, I penciled a level line of sight mark on the wall. This mark is where I located the top of the 32” monitor’s display. Then I pulled the desk top away from the wall until I could see the bottom of the display above the top front edge of the desk, while sitting normally in my chair. This created the 7” gap and 2” recess. This placement will allow me to comfortably view both the 32” and the three Dells mounted above, without creating eye or neck strain from excessive viewing angles.
It’s not part of this Instructable, but for design context I want to mention that the 32” is mounted to the wall using a tilt / swivel, low profile 100 mm VESA wall mount. The monitor only weighs 12.36 lbs without the stand so I’m confident in the mount being secured to the drywall (no stud) using screws and 75 pound rated dry wall anchors.
Locating mounting points in my particular wall.
Step 11:
Using the yard stick, level, masking tape and pencil, I marked a vertical center line of the mounted 32” monitor, on the wall above it (22).
Step 12:
Holding a modified mounting arm on top of the 32”, I penciled the height of the arm above the 32” (23). This mark will be the location of the bottom edge of the aluminum square tube.
Step 13:
Using Acoustical Variation Analysis (knuckle rapping:) I located the nearest stud to the centerline. a 4D 1 ½” common nail and hammer were used to locate the edges of the stud (24).
Step 14:
I then measured and recorded the distance of 6 7/8” from the 32” monitor center line to the stud center line (25). Click on picture for full view.
Step 15:
Finally, I measured 24” from the first stud’s center to find the second stud on the opposite side of the 32” monitor center line. I then used the hammer and common nail to verify the edges of the second stud (26). Click on picture.
I completed this step by using latex caulk to fill the stud finding holes and installed a temporary 3D 1 ¼” brad at the top of arm or bottom of square tube mark (27). Click on picture. The brad will be used to balance the tube while I mark the mounting hole locations in the wall, in a later step.
After the caulk is dry, I used left over paint to hide my stud search holes. If you don’t have paint suitable for touch up, place your stud search holes beneath where the aluminum square tube will be mounted later.
Locating aluminum tube mounting holes.
Now that the studs are located, I can find the proper locations for drilling the square tube’s mounting holes, to insure everything will be center above the 32”.
Step 16:
The three identical Dells are each 21” wide. Since the bracket arm is mounted in the center of each monitor, I need to have a 21” gap between the three Bracket arm mounting bolt holes in the 45” long aluminum square tube.
Place a piece of masking tape across two adjoining faces, at the approximate center of the tube. Use a tape measure to find the exact center of the tube’s length and mark the location on the masking tape with a pencil and carpenter’s square. Use a piece of tape and pencil to label one face “TOP” and the adjoining face “FRONT” (28).
The side of the square tube labeled “TOP” is where we will drill ½” access holes, so we can tighten machine screws inside the square tube. Those screws will hold the monitor mount arms to the “Bottom Face” of the tube. The Bottom face will have three ¼” holes drilled through it to support the three 6 mm machine screws with lock washers.
Step 17:
Use a yard stick to measure 21” to each side of the center and mark the locations on pieces of masking tape with a carpenter’s square and pencil (29).
Step 18:
Locate and draw a pencil line, at the ¾” width of the tube at the marks made in step 16 and 17 (30).
Step 19:
Rotate the square tube 90 degrees, to the “FRONT” label.
This side of the square tube will be the “Front Face” where we will drill three 11/16” access holes so we can tighten the lag bolts and drywall anchor screw inside the square tube. The bolts and screw will hold the tube’s “Back Face” to the wall. The back face will have two ¼” holes to accommodate the lag bolts and one 11/64” hole for the #8 anchor screw.
Use the yard stick, masking tape and pencil, to measure and mark 6 7/8” from the center line on the front face (31). Note – your dimension will be different.
Step 20:
Use the yard stick, masking tape and pencil, to measure and mark 24” from the center line on the front face (32). Note – 24” is the stud center spacing in my wall. Adjust these stud measurements for your application.
Step 21:
Use the yard stick, masking tape and pencil, to measure and mark an equal distance location for the dry wall anchor screw location, on the opposite end of the square tube (33). Note – your dimension will be different.
Step 22:
Locate and draw a pencil line, at the ¾” width of the tube at the marks made in step 19, 20 and 21 (34).
Step 23:
Use a 11/64” drill bit and drill a hole through the FRONT and BACK faces of the square tube, at the location of the dry wall anchor marked in Step 21 (35).
Step 24:
Use a 1/4” drill bit and drill five holes through all the faces (FRONT and BACK) (TOP and BOTTOM) of the square tube, at the locations of the remaining five marks of steps 18, 19 and 20 (36).
Step 25:
Use a ½” drill bit and drill three holes through the TOP face ONLY, using the ¼” holes as guides (holes drilled in step 24) (37).
Step 26:
Use a 11/16” drill bit and drill three holes through the FRONT face ONLY, using the two ¼” holes and the 11/64” hole as guides (holes drilled in steps 23 and 24) (38).
Step 27:
The brad I installed in step 15 is located at the intersection of the 32” center line and the bottom placement of the square tubing, so I centered the tubing, aligning the ¼” hole with the brad. I leveled the tubing with a bubble level and used the 11/64” drill bit to surface mark the wall mounting hole location (39). Click on picture for full view.
Step 28:
After removing the brad, caulking the hole and applying some touch up paint, I drilled a 3/8” hole and installed the dry wall anchor. I then used a 1/16” drill bit and drilled a 2” deep guide hole through the dry wall and two studs at the marks made in Step 27 (40). Click on picture for full view.
Step 29:
Using the three 6 mm machine screws and lock washers I mounted the modified arms to the square tubing (41).
Step 30:
I then mounted the square tubing to the wall using the ¼” lag bolts and #8 anchor screw. These were applied with a combination of a 7/16” driver, 7/16” socket / driver and #2 Phillips screwdriver (42). Click on picture for full view. Caution – Do not over torque the lag bolts with the socket / driver.
Step 31:
The monitor’s power transformers were mounted to the top of the tubing with double sided tape (43). The excess electrical cords were folded in half and slid inside the tubing (44). The power jack for the center monitor was fed through the tubing and extracted through the middle 11/16” hole (45).
Step 32:
The transformer’s primary power cords were added next and arranged to overlap so when zip tied, they would stay neatly bundled next to the wall. Then a heavy-duty multi-outlet was added after the excess power cords were coiled and zipped (46).
Step 33:
The heavy-duty outlet / coiled cords were then routed behind the 32” monitor and secured with two zip ties wrapped around the center arm (47).
Step 34:
The three monitors were then hung, powered and cabled (48).
Now it’s time to enjoy the multi-screen organization, of multiple software windows, simultaneously being used in one project's work flow.
Step 35: Section 3 – Studio Hardware Organization
This system is used primarily as a Twitch Studio. The two desk monitors display the Twitch Console and the Game Play Screen. The TV/Monitor above is used for display of the broadcast from the Viewers Perspective (49).
Five aluminum tubes are used for two separate assemblies (50 and 51).
The top assembly consists of three tubes bridging the 22 1/2” gap between two wall studs while supporting the heavy TV/Monitor, with an attached retail monitor mount (52 and 53).
The bottom assembly supports the peripheral hardware; three power transformers, wi-fi router, modem, power supply bus and associated cabling (54 thru 60).
The Aluminum Tubes were mounted using the same principals as outlined in Section 2, after I had located all the proper mounting points on the wall’s 2x4s.
Computer hardware was hung using #8 pan head machine screws slid into the hole/slot plastic mounts (61) on the back of the power bus, router and modem. Power transformers were mounted with 5 lb. double sided tape. The lengths of cabling were folded in half and slid between the tubes behind the mounted hardware.
When planning aluminum tube mounting of equipment, remember to include access holes large enough for tool access. The layout planning should begin with how you intend to mount the hardware to the tubes, and then proceed to wall locations of the tubes. Be ever mindful of Ergonomics and how you will interact with the equipment.
If you plan on a more open display of the tubes, you might want to consider using round and square black plastic plug inserts for a professional finish.
I hope this Instructable has inspired your creativity and maybe sparked some Instructable ideas.
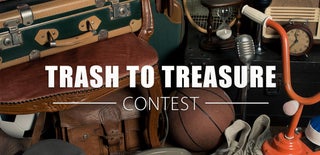
Participated in the
Trash to Treasure