Introduction: Portable Bluetooth Speaker (FREE PLANS)
Hello everyone! In this Instructable I will show you how I built this Portable Bluetooth Speaker that sounds as good as it looks. I have included Build Plans, Laser-Cut plans, all the links for products that you would need in order to build this speaker by yourself and the Wiring Diagram is free download and you can find it at the end of this intro or in the Electronics Step. Make sure to zoom in to see the connections up close!
I was always astonished by the design of Bose - the manufacturer of amazing speakers. With that I mind I wanted to create my own portable speaker for the fraction of the price. Many hours were spent designing the speaker and sourcing materials in order to build this speaker. Therefore I will share the whole building process with you!
Step 1: Idea and Design
To begin with I created a 3D model of the speaker in Sketchup keeping in mind the inner volume of the speaker enclosure required for the drivers. Sketchup is a great tool for visual assembly and designing of the speaker. I then made drawings in CAD for the panels needed for the build and brought them to my local laser-cutting company to cut the panels out of 4mm plywood. The laser made incredibly accurate and clean cuts in the plywood resulting in perfectly fitting parts and easier assembly.
Step 2: Parts and Materials
The materials and parts for this speaker are available from the links below and/or your local suppliers. For the enclosure of the speaker I used 5 layers of 12mm MDF. The main and supporting panels where cut out of 4mm plywood sheet. The Wiring Diagram for the electronics is provided so make sure you take a look!
🎁 $5 OFF your first App order on AliExpress - https://a.aliexpress.com/_mPN8FLo
Parts:
- 1.5 Inch speakers - https://bit.ly/3XsYPu0
- Amplifier - https://bit.ly/3GEYoWI / https://geni.us/wOpMh
- Passive radiators (40x78mm) - https://bit.ly/3ZBn6Aa / https://geni.us/WZxqbZv
- 12V Latching LED switch - https://bit.ly/3XcIgCs / https://geni.us/4pbi1
- 3S BMS board - https://bit.ly/3Q85BmI / https://geni.us/E30JaSC
- Bluetooth audio receiver - https://bit.ly/3VZ6LSK / https://geni.us/KBHU
- 3S Battery level indicator board - https://bit.ly/3W90Nyy
- DC input jack - https://bit.ly/35s1rxq / https://geni.us/Hbs3uD
- Audio input jack - https://bit.ly/3GMsgly / https://geni.us/BNMj
- B0505S-2W isolated 5V converter - https://bit.ly/3nefFLb
- Step down converter - https://bit.ly/3eSKu9t / https://geni.us/PcR1Je4
- Momentary Push Button - https://bit.ly/2q8FJPU
- 555 Timer Chip - https://bit.ly/3ll4Pm8
- Resistors - https://bit.ly/37Ukr9Q
- Foam gasket tape - https://bit.ly/3hXlrnu
- 2mm Red, Green and Blue LEDs - https://bit.ly/3k7gU2B
- 12.6V 1A Charger - https://bit.ly/3X0263S / https://geni.us/Si0zNc
- M2.6X12 screws - https://bit.ly/3CvFPmO
- 3X 18650 Cells - https://bit.ly/3J3KCNl
- Adhesive rubber feet - https://bit.ly/3X1nPsG / https://geni.us/VkuJ
- Faux leather vinyl - https://bit.ly/3IKlspM / https://geni.us/dqaM
Tools:
- TS101 soldering iron - https://bit.ly/3hQm4PP / https://geni.us/owyDm5G
- Multimeter - https://bit.ly/3VOFjYv / https://geni.us/UmrhyYk
- Hot glue gun - https://bit.ly/3QdYfhg / https://geni.us/1dwxqIM
- Wire stripper - https://bit.ly/34kBgLn / https://geni.us/6epIs
- Cordless drill - https://bit.ly/2UiMSbL / https://geni.us/A5AZi
- Jig saw - https://bit.ly/3GpY8w6 / https://geni.us/D8GC
- Drill bit set - https://bit.ly/3S3i6zC / https://geni.us/ktAK1M
- Step drill bits - https://bit.ly/3eM5GtB / https://geni.us/xYRx7J
- Forstner bits - https://bit.ly/35snpjW / https://geni.us/F6it
- Hole saw set - https://bit.ly/3YZU8tg / https://geni.us/hONP
- Wood router - https://bit.ly/3I7Aplm / https://geni.us/6okRl
- Roundover bits - https://bit.ly/3ijBZWU / https://geni.us/cc82
- Center punch - https://bit.ly/3xslc8u / https://geni.us/o5WBEwB
- Helping hand - https://bit.ly/3B9mIgt / https://geni.us/Yyqyte
Attachments
Step 3: Speaker Enclosure
I have uploaded free build plans for this speaker! You can find them at the end of this step. Make sure you print the plans and make sure that the measurements are correct using a ruler! Also you can download the .dxf plans and ask your local laser-cutting company to cut them out for you in few minutes instead!
To build the enclosure I used a router and a laser-cutter to achieve almost perfect results with minimal effort but I have also uploaded a set of plans for those who may not have access to such tools. Using the plans provided, the speaker can be built using the same materials (12mm MDF and 4mm plywood) and simple tools, such as a jig saw and a drill. The most important thing is to make sure that you print the plans at the correct scale. To check if you have printed the plans correctly, simply print out a page and using calipers or a ruler check whether the speaker holes match the dimensions written.
I traced out the plywood template on all 5 MDF pieces. Four holes where then drilled through the boards with a decent sized drill bit and a jigsaw was used to cut around the template staying as close to the edge as possible. Once I had the 5 pieces cut out, I applied narrow double sided tape on the plywood template and stuck it down on the MDF cutout. A spiral flush trim bit was loaded in to my router and the height adjusted to cut the MDF only. Turning the router and dust collection on, made the job of creating five copies of the template quite easy. I lightly sanded both sides of the enclosure pieces to get rid of any burr left on the edges. Using a plastic card I spread the wood glue on the enclosure piece and glue one on top of another stacking 5 layers of MDF together. Once the glue has dried, I sanded the enclosure for a smoother finish. I then took a flush trim bit, removed its bearing and replaced it with a smaller one in order to cut very little into the MDF enclosure. The lip that is carved out by this process on both sides, ensures that the supporting panels sit nice and tight in the enclosure. I made sure to use sufficient dust collection because trimming MDF with a router makes a LOT of nasty dust. After that I used a roundover bit to roundover the edges of the enclosure. This makes the enclosure a lot smoother and nicer to hold in hand and also provides curves that are more easily wrapped in vinyl later. I then proceeded by drilling a 16mm hole in the enclosure for the main switch. A step drill bit was used to drill the hole – this tool is amazing! A healthy amount of wood glue was then spread along the edges created by the router bit and the support panels put in place and allowed to dry.
Step 4: Plywood Panels
I then sanded the faces of the laser-cut plywood panels using fine grit sandpaper to remove any burn marks on the wood from laser cutting. I placed both panels on a sheet of paper and sprayed couple of coats of lacquer. This brought more depth in the wood grain, highlighted the text and created a protective layer on the plywood.
Step 5: Gluing in the Plywood Panels
I then applied glue around the edge of the speaker enclosure, spread it out and pressed in the supporting plywood panels which sit nicely on the edge that is made with the flush trim bit with a smaller bearing. The panels are pressed in place for a few hours until proceeding to the next step.
Step 6: Covering in Leather Vinyl
For this process it is necessary to have good ventilation and to cover both sides of the speaker enclosure in masking tape to protect any plywood surfaces from unnecessary contact adhesive on the edges which would later prevent the plywood panels to be attached close together. It is important to only cover the MDF in contact adhesive. Once both sides of the enclosure were covered in tape, I started applying the contact adhesive with a soft brush, making sure to cover the whole enclosure where the leather vinyl would wrap around.
Once the enclosure was covered in contact adhesive, I cut a long and narrow piece of vinyl leather and applied the same adhesive on the back side of the fabric itself, being careful not to apply any glue to the leather side of the vinyl. Once the glue has become dry to the touch on both surfaces (drying takes only few minutes), the vinyl can be applied.
Unfortunately, I have lost the footage of me wrapping the material around the enclosure and gluing in the passive radiators, but I will try to explain the process as best as I can.
It is important that the leather vinyl piece is a rectangle with straight edges on all four sides. That is important because when wrapping the enclosure in vinyl we will end up with a seam on the bottom side of the enclosure. This seam can be almost invisible if the edge of the vinyl is cut as straight as possible and the tucked into another side of the vinyl piece once the vinyl is wrapped all the way around the enclosure.
The most difficult and skill-requiring part of wrapping the enclosure is taking care of the corners. Using the roundover bit in the previous step helps a lot since it creates soft curves which are more forgiving for wrapping the material. The key is to pull the vinyl with a lot of force and tuck in the inside of the speaker and slowly working your way down to avoid any wrinkles and bumps. A plastic gift card is a great tool here.
Once the vinyl is tucked around the edges, a sharp (brand new) blade is used to cut along the plywood support panel in order to remove the excess of the vinyl.
Step 7: Electronics
Feel free to download the wiring schematic and zoom in for a better view!
These tactile momentary button switches were used to turn on the Bluetooth and the battery capacity board. The face of the button was lightly sanded and two-part epoxy was used to glue them in place. It is important to seal the edges so that no air leaks out of the speaker once it is done. A dab of epoxy was placed on the switch and the plywood disc pushed in place. I also used epoxy to glue in four (1 red and 3 green) LEDs. Four 330 Ohm resistors were soldered in place of the LEDs that were on the battery capacity tester board. The shorter wires that were soldered to the board will later be soldered to the switch. The longer wires that were soldered to the board will later be soldered to the outputs of the BMS (Battery management system) board. Then four pieces of wire were soldered to the board which will be connected to the four LEDs glued on the panel. A piece of double sided tape is used to attach the board to the panel. Three 18650 cells were then glued in a triangular arrangement for better fitment inside the enclosure. Then the cells were connected to the BMS board. The wiring diagram is shown above. I then soldered black (negative) and red (positive) wires to the DC jack for charging. I then proceeded to wire up the audio sources. I began with soldering the blue LED to the KRC-86B Bluetooth audio receiver board. I then took a 3.5mm audio jack and soldered two 1kOhm resistors. One from Left channel to Ground and the other from Right channel to Ground. This almost entirely eliminates any background noise when using the AUX port. The wires from the audio jack were then soldered to the Bluetooth board to the according terminals. I then soldered wires to the ‘GND’ and ‘VCC’ pins of the Bluetooth board from a 555 timer chip and a few components to create switching circuit that only turns on when a button is pressed and that way the battery energy is not consumed when the speaker is not in use. A step-down converter and an isolated converter was used to supply power to the Bluetooth board and eliminate any ground-loop noise. I then took the White LED switch and soldered two of its pins together to make the LED turn on when the button is pressed in. The remaining wires were then soldered to the PAM8610 amplifier. The two remaining wires from the battery capacity baord were soldered to the DC jack. The blue LED from the Bluetooth board was then glued in place and the wires from the switching circuit soldered to the button. The audio jack was ten attached in place and the wires from the DC jack soldered to the ‘P+’ and ‘P-‘ terminals of the BMS board. The remaining wires were soldered to the main LED switch which was the pushed in place.
Attachments
Step 8: Final Assembly
For the final assembly the full-range speakers were bolted down using M3 bolts and nylon nuts from behind. This creates an air-tight seal around the drivers. Once the speakers were bolted in place, the output wires from the amplifier were soldered to the speakers. Wood glue was spread around the edges of the panel and pressed in place for a tight fit. I then stuck a long piece of double sided foam tape around the back panel support to create an air-tight seal once the back panel is screwed in place. Four adhesive rubber pads were put on the speaker bottom. With that done the speaker is now ready for a quick charge and proper use.
Step 9: Finished Product
Once the speaker is charged it is ready to produce some noise. The battery indicator lights show that the battery is now full. The white LED switch is pushed in turning on the speaker. With the button pressed, the Bluetooth is enabled and the speaker is ready to pair with an audio device. Once paired, the music can be streamed for up to 6 hours on full volume and nearly 5 days on 50% volume! The battery life on this speaker is stellar due to high capacity Lithium-Ion cells and very efficient class-D amplifier board.
The audio recorded on my end and then played through your speakers may not be the best depiction of audio quality but I can ensure that this speaker delivers great sound quality and decent bass filling an entire room.
Thank You so much for following me through this tutorial! I hope I have managed to inspire you to create your own speaker using my or your own design :)
And that's how my Portable Bluetooth Speaker came to be! It was a pretty cool project that helped me improve my skills, and I truly hope that you learned something new as well. If you have any questions, feel free to ask in the comments. Also consider visiting my YouTube channel for more videos. Thanks!
Also, take a look at my Etsy shop!
Thank You!
- Donny
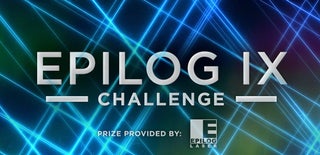
Participated in the
Epilog Challenge 9