Introduction: Portable Fume Hood
What do you do when your electronics projects
start to take up too much space in your old man's shop?
Why you build an Indoor Fume Hood of course!
Planning it out
By building a 2' x 4' desk with a fume extractor, I take 8-square feet of equipment out of the way. Better yet, all of my electronic projects and equipment don't become smothered in oxy-acetylene reside! I wanted to make sure this fume hood could be easily moved from one place to another; so right from the start I set my dimensions at 5 1/2' high, 4' wide and 2' deep. Hand-holds were also a must. Any time I need to move it I just disconnect the vents, move it to the new location, re-install the window adapter and either reuse the old vents or just grab some flex vent.
In the spirit of Freecycling, I wanted to use a salvaged squirrel-cage fan from a range hood. My plan was to create a 6" x 6" box that the fan would be centered in, exhausting out the top. More fumes would be collected by peg board, that would be set an inch off the back wall.
This is my first Instructable, so pointers for next time would be greatly appreciated.
If you enjoyed it, your Rate and Vote would be really cool
Enjoy the read!
Step 1: Gather Your Materials, and Cut Them to Size.
I used...
- An old desk
- A squirrel cage blower (salvaged from a range hood)
- A under cabinet florescent light
- 1x (8 x 4 foot ¾ inch) plywood
- 2x (4 x 2 foot) pegboard
- ¾ inch trim
- 8-inch exhaust ducting and dryer vent
- Paint and/or Stain
- Masking tape and news paper
- Rollers and brushes
- Silicone
- Some wiring, covered in Split loom casing
- Various brackets, screws and finishing washers
- Scrap wood kicking around
Some tools that could be useful...
- Table saw
- Miter-saw
- Router and/ or your favorite rotary tool
- Cordless drill
- Squares (drywall, T-square and triangle)
- Soldering iron
- Hole-saw
This is fairly easy, just take your time and do it right.
First, disassemble and cut your desk down to size. Mine was quick. I unscrewed the filing cabinet and end cap, leaving only a basic “L,” shape that I could build off. Next, cut the plywood and the peg board. To keep it portable, I wanted to keep the height near 5’6” with an overall width of 4 feet. Most importantly it must be no deeper than two feet (so it will fit through doors). I also wanted to keep this project to a single sheet of plywood, if possible. I began by laying down masking tape where I wanted to make my cuts; then using a drywall square, I drew a line to mark off my cuts.
1. ¾” plywood
a. (2’ x 4’) sheet off the end
b. (2’ x 6”) strip, trimmed to (1’10 ½ “)
c. then split the rest down the middle making 2x (2x5 ½ ft)
2. Peg Board // compensating for the 2x ¾” sides
a. (3’10 ½ “ x 2’)
b. (3’10 ½ “ x 6”) 3. ¾” Pine (3’10 ½ “ x 17”)
4. ¼” plywood (3’10 ½ “ x 6”)
5. (optional) ¾” trim
Step 2: Cut Out Hand-holds
To keep this fume hood nice and portable, I felt it needed hand holds. I started out by marking off a square line at the center of where I wanted the hand holds to be. Using a hole-saw I drilled out 4 holes; then I used my dremel to cut the holes into a pair of oval hand holds. I repeated this on the other side, and then sanded it all smooth.
Step 3: ASSEMBLE !
You will want to start with a flat surface. I used the patio and a sheet of plywood with some shims. Start with the two longer pieces that will eventually be the upright walls. Take some time here to ensure they are square to the desk surface. Use (3 – 4) wood screws with finishing washers per side. It should now look like a goalpost. Then top it off with that shorter 2’x2’ piece and another round of screws and washers.
To form the box that will house the exhaust fan, start by taking the pine that was cut earlier. Mount the pine flush with the front of your fume hood to form a 6” tall 17”deep shelf. This would make a great place for your cable/ satellite box, computer or favorite game console! Then, add the peg board on the bottom and the ¼” plywood to separate the shelf from the exhaust fan. Use brackets or screws to secure them into the side walls.
Step 4: Paint and Stain
There are many ways to finish your project. I took three steps. I didn’t like the look of the knots in the plywood, so I filled them with poly-fill, and then sanded it flat. It made a slightly more uniform finish but still left more character then something like melamine or MDF.
Second, I used the newspaper and masking tape to protect what I did not want to stain. Again, the more time you spend masking, the sharper the end result will be. Preferably use a lint free cloth and rub in a small amount of stain, and add more as needed. Then wipe most of it off with a new cloth, blending as you go. If you are using trim now might be a good time to stain it too.
Lastly, it’s time for paint. I had some left over paint from the last renovation. If you don’t have the same paint, try choosing something with a bit of contrast (without looking like a monolithic cube in the desert.) Use rollers and brushes as needed. It’s always best to do multiple coats (2-3). There are many instructables out there that can explain how to paint better than me, look around if this is something new for you.
I highly recommend you complete painting within 48 hours unless you plan to reapply the masking you used. Otherwise the paint may get thick and cause problems when you peel off the masking. If you decided to use trim, tack it on now.
Step 5: Ventilation
Here is where form meets function. Using masking tape, mark off the slot to cut in the top for the fan. In my case it was 10” wide by 4” deep. Drill pilot holes then cut it out with a jig-saw or Dremel with a rotary cutting bit. Using the hole you just cut, center the fan you are using in the box that you created earlier. I was able to use wood screws straight through the plastic housing of the fan (without interfering with the function of the exhaust fan.) It could have been better, but for a personal project it has worked out great. Running the wires for the fan will come in a minute.
To vent the fumes outdoors, we need to use some plywood to create a spacer that will hold the dryer vent in the window. Use some ¾” plywood and cut it to your window, plus a ¼ inch extra to keep the fit tight while still allowing some leeway. Cut the 8” hole near the top to fit the vent through, and then center the vent in the hole and pre drill the vent’s mounting holes. If you want this adapter to last a long time without warping, moulding or fading; then be sure to paint this piece with 2-3 coats of outdoor paint. Right before you mount the adapter, apply a bead of silicone wherever the adapter will touch the window frame. Use shims to press the adapter plate against the inside of your window frame. Then cut a 2x2 to form a brace to keep the window from opening from the outside, for obvious reasons. Finish it off with a thick bead of silicone along the bottom and smooth it out with a wet finger. Try to create a slope towards the outside of the window to help rain drain away.
For piping I decided to use 8”diameter pipe. I used what is normally a 8”tube ==> 10” x 4” floor vent, 2 x 90deg turns, a 2’ section of pipe and a 8” dryer vent. You could paint the venting like I did.
Mount the dryer vent to the adapter with wood screws and preferably washers. Now, it’s time to dry fit the vents. Be careful not to scratch the paint, and then wrap the joints in a matching color duct tape to seal the pressure in. Secure the floor vent adapter to the top of the fume hood by bending the flashing back and drilling holes to go through with woodscrews / washers. You can paint the screws and washers- like I did- if you’d like.
Step 6: Electronics and Finishing Steps
Just about done! Now it’s time to wire up the fan. Mine was a 3 speed so I had to run 4 wires down through the hole I cut earlier. I decided to wrap them in split loom tubing and secured them with black conduit clamps. Eventually, I will make an Arduino powered relay board, but for now I can live with just plugging it in every time I need it. A good alternative is a spring wound fan timer or just a simple light switch; just be careful to check the maximum current of your switch. If you have the option, be sure to connect the fan’s ground and use a 3 prong plug.
Now grab the peg board and some ¾ to 1” shims. Screw the shims in; try to space them out so air can be drawn from behind it. Double check that your fan’s wiring works and is well secured. Then use wood screws and finishing washers to mount the peg board in the upper rear of the fume hood. Fill the gap between the peg board and the table with the (1’10 ½” x 6”) strip of plywood cut earlier.
Lastly, mount your lighting. Whatever you use, most fixtures will come with a template to help you sink the screws to hold it up. Just fallow the box. Some last minute additions may include a power bar, speakers, tool racks or even a custom cup holder. Oh Yeah!
Now step back and take a moment to admire your creation. Then, grab your favorite beverage and get soldering!
Again this is my first Instructable, I would love some feedback on what needs some improvement.
Special Thanks to my little sister Katie, Editor in Chief
Please RATE and VOTE. More to come soon!
Take care and Happy Hacking!
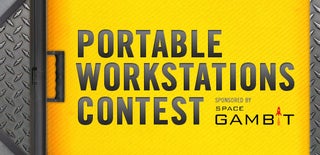
Participated in the
Portable Workstations Contest