Introduction: Rainbow Ring / Regnboga Hringur
I find circle packed objects compelling to look view and fun to make. Ever since my last trip to Iceland I have been harboring a minor obsession with applying patterns of circles to surfaces of various objects.
Perhaps it's the combination of the volcanic stones, the bubble chambers in caves I visited, and the magical feeling of the whole place. I don't know what it is about the environment there but it really drew me in and I can't get it out of my head.
I've given these patterns an Icelandic name - hringpoki - which means circle or ring packed or bagged. It's much more fun to say and carries a little more meaning (at least to me).
And that's what eventually lead me to this Instructable. That and Steven Gray who suggested that I look into putting some resin in one of my hringpoki objects.
I decided to make a little project out of this experiment and create a special hringpoki ring for my wife for Mother's Day - on May 10th in the US. I ran into some issues designing the ring, and then there were some production delays from the silver casting service, and then there was a PEBCAK error which delayed things until it was finally ready on June, 1st.
So, even if you don't make a hringpoki ring but some other object where you plan to use UV resin, you might want to read this anyway if only to not repeat my mistakes.
Supplies
Things You'll Have to Make/Design
The ring - I made mine using Rhino 3D, a little ZBrush, and the service bureau i.materialise.
Things You'll Have To Buy (I Purchased all on Amazon):
UV Activated Resin- there are many to choose from. I got this bottle because the reviews were good and teh size was decent but not too big.
UV Nail Dryer - UV Lamp Light- this one is nice because it has a sliding tray and time settings.
Resin Coloring - these are decent and seem to work.
Quilting Pins - you probably have a bunch of these lying around in your sewing kit. I used these to mix the dye with the resin and apply the colored resin.
Fine Grit Sandpaper - the finer the better. (I got this at Home Depot actually).
Things I Had That Made This Easier
Bench Top Buffer - an invaluable tool to have when working with easy to polish metals like silver or bronze. A dremel will work in a pinch but these bench polishers are really fast.
Goggles - every time you work with things that spin at high speed you should be wearing goggles or some sort of eye protection. Invest in a nice pair of goggles or glasses so that you don't mind wearing them. I use this pair with side protection and bifocals built in. I used to not need that extra magnification, but it is nice to have when working on something small and fiddly like earrings or something. If you choose not to get eye protection, Amazon also sells a good number of eyepatches.
Step 1: Design Your Ring
Easier said than done but it's really not that hard to make a basic ring in any 3D modeling program. It's particularly simple in Rhino because all you need an a circle with the inside diameter a little bigger than the size you want. You want it a little bigger because when you cast an object it tends to shrink slightly. The computer size is the "ideal" and the casting is "reality" so unless you're just making ring for a computer environment, you'll need to fudge the numbers a bit if you want the ring to fit in real life.
If you mess up you can always get a ring stretcher. That's a last resort though.
I made a different ring using a similar technique for myself decided that the new ring would be a little less wide and have more of a profile curve like a dome style wedding band.
To make my ring I started with a circle and an idea of how I wanted the outside profile to look. Then I used the Sweep1 command.
More detailed Rhino instructions are available on this instructable. YouTube videos are also a great resource.
Step 2: Create Your Hringpoki Pattern and Apply to the Ring
You've got limited space to work with on the surface of a ring. There is also a limit to how detailed to can make your surface and have it come out in silver. And then, there's the resin step as well. Do you really want to be filling many many many little holes with colored resin? So find something that will work for you both in terms of getting it produced and in terms of preserving your sanity when it comes time to fill all those holes in.
There are a lot of ways to create your hringpoki pattern.
- You can just eye it: make it by hand by drawing a pattern on paper, scanning it and then tracing over it in Rhino to get a more artisan look.
- You can use Processing: here is a definition to get you started.
- Use Grasshopper: this is probably the best method because you can really play around with how you arrange your circles along your surface. It's a beast of a program to learn though.
There are probably a bunch of other ways. Just use whatever works best for how you like working. I used a mix of scripting and just eyeballing it. I'm learning the grasshopper method but you know how it goes - not enough time in the day for all the things I need to do and want to do.
However you make your pattern of whatever you want to inlay with resin, you then have to apply that pattern to your ring and boolean it off of the ring so that you are left with indentations. They are about 0.75 mm deep in this ring.
Next all you have to do is send the ring off to get cast in the material of your choice. I went with silver and used i.materialise.
Step 3: Cast the Ring and Acquire Resin + Dye
While you are waiting for the raw casting to arrive you should go out and get the resin you need for the project.
I made the mistake of thinking the dye was the UV resin - I think because of the way sellers put UV in the titles of their dyes in order to work the SEO system.
I was scratching my head trying to figure out why the color wasn't hardening during testing. Sunlight wasn't working and a UV lamp was similarly ineffective. I was about the send an email to the seller of the dye when I decided to take some extra time to actually read the description of the dye and saw that it was in fact just dye FOR resin.
I felt like a pretty big idiot and ordered a small bottle of clear UV activated resin. This time when I tested the resin mixed with a bit of dye everything worked! This PEBCAK error messed with my timetable.
A slight delay in casting also dragged things out (but that was more the fault of UPS than i.materialise) but eventually the raw silver ring arrived from Leuven.
Step 4: Mix Resin With Dye and Apply
This is the most time consuming part of the whole process.
First pick your colors. I wanted the ring to really stand out and look cheerful. What's more cheerful than a rainbow? So I went with 5 different colors - yellow, green, red, violet, and orange.
- Put on a movie you've seen before that you like but don't need to necessarily pay attention to in order to know what's going on.
- On your work-surface put down a paper bag from a supermarket or something similarly tough that will hold up but that you can dispose of after you are done.
- Put maybe a dime sized dollop of resin on the work surface and mix in maybe a drop or two of the dye.
- Swirl the resin and dye together with a pin - one for each color.
- Use the pin to collect a tiny bit of colored resin and apply the resin to the depression in the ring.
- Put the ring on a mandrel or something similar and then place the ring into the UV chamber. Wait a minute or two for the resin to cure.
- Repeat steps 5 and 6 until complete.
Step 5: Wet Sand and Then Polish
Now you need to make the enamel flush with the metal surface. I used some very fine sandpaper that I kept wet and hand sanded the ring. Dry the ring and examine it. Use a magnifying glass if you have one so you can really see if it's flush. The resin might look flush with the naked eye, but if you really want to make it look good you need to magnify the surface. If it's not quite there, start wet sanding again.
Once you have done this part to your satisfaction you then have to polish the ring. I used my bench polisher and some jeweler's rouge.
Step 6: Present the Ring (even If It Is a Little Late)
This is the best part. You give the ring to the person you made it for.
If the movie you put on during the resin application step was Contact, you will be aware of the first rule of government spending. I happened to think the same way and made a second ring.
Step 7: Thanks for Looking and Checkout #hringpoki
If you like these patterns as much as I do, check out #hringpoki on Instagram to see some of my latest designs using the technique - including this ceramic Hringpoki Galdur Egg with platinum divots!
Website: J O Y C O M P L E X
Instagram: @joycomplex
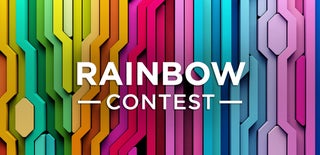
Runner Up in the
Colors of the Rainbow Contest