Introduction: Realistic Moon Lamp
Build a realistic, detail rich lamp from fiberglass that looks like a lunar surface!
Step 1: Building a Realistic Fiberglass Lunar Sphere
For this instructable, I set out to create a lamp that looked as realistically like the moon, as we view it with the unaided eye, as possible. I have been searching for a while for a lamp that accurately looks like a lunar surface, and glows in a similar way. I ultimately decided on using fiberglass as my construction medium. If you have never used fiberglass before in your life, this is a great way to get started in using this exciting material. It’s simple, inexpensive, and you will have a gorgeous piece of art to show off in the end. Fiberglass is a wonderful and underutilized creative medium in my opinion. It is exceptionally forgiving, easily accessible, durable, and rather inexpensive. It doesn’t require the use of electricity, computers or modeling programs, and can be used by nearly anybody. Unpainted, its translucence lends fiberglass exceptionally well to creative lighting, making it perfect for shades and pendants. The materials used in this instructable were all purchased off the shelf at my local hardware store and Ikea, but they're available for even less if you look around. For the sake of simplicity (and for those who live in apartments or cannot tap into electric lines to hang a pendant fixture) I used a simple and inexpensive plug-in light cord. The entire project can be done in the span of a day, however, letting the fiberglass resin cure overnight greatly aids in sanding the surface later on.
Step 2: DISCLAIMER
!DISCLAIMER!
Although fiberglass isn’t particularly harmful, it is advised that wherever you do this project that it be well ventilated. Fiberglass resin emits strong odors while curing, and trapping them in a closed environment with you is never a great idea. When cutting raw fiberglass and sanding after the resin has cured, very fine fibers are released into the air. WEAR A DUST MASK AT ALL TIMES WHEN SANDING. If possible, wear goggles too. Although it won’t kill you, fiberglass can be rather itchy and irritating if basic safety isn’t taken into account. Pants and long sleeve shirts are recommended, as is a painters head sock of you have one. If you choose to use power tools to sand, ear protection is always a good idea. Please exercise caution when working with a new medium!
Step 3: Basic Materials
The materials used in this project are readily accessible at most hardware stores and big box stores. You may have a decent supply of these materials already sitting around your garage, workshop, or home as well.
- Fiberglass cloth. You don't need a whole lot of this, or any at all. I had some, and used it with the idea that the weave of the fabric would provide additional strength, requiring less layers to be built up. To be honest, the fiberglass mat when used alone is plenty strong enough for this project.
- Fiberglass mat. Unlike standard fiberglass cloth, this is exactly as the name suggests- a dense mat of glass fibers running in all directions, it is not woven and can be pulled apart rather than needing to be cut. When handling fiberglass mat raw, I highly suggest wearing gloves at all times. since it isn't woven like cloth, the fibers can easily come loose and cause quite a bit of itching.
- Fiberglass resin. There are a few types of fiberglass resins available. For this project I chose to use standard all-purpose resin. If you visit a fiberglass supply shop, they sell resin in different grades. You want the cheaper amber tinted resin (as you build up layers, the amber tinting will create light and dark areas, mimicking the lunar surface.) You don't need the giant can, the 1 or 2 quart can is plenty.
-Resin hardener. The hardener, or catalyst for this resin is methylethyl keytone peroxide, or MEK. MEK is no good to ingest and can cause skin irritation if you aren't careful. The resin should come with some, check inside the plastic lid when at the store. If not, it will be sold nearby and is only a couple dollars for more than you will need.
-Play balls. These are the inexpensive play balls you see piled up in racks in big box stores on the end of kids toy aisles. They only cost a couple dollars, the resin does not stick to them, and if you have an inflator needle and a vacuum pump they can be reused.
-Lamp cords. I got mine from Ikea, but I have seen the simple, plug-end cords and sockets at many places including hardware and big box stores. Feel free to use whatever fixture you like- hardwired, plug-in, or even battery. I chose these because they looked nice, were only a couple dollars apiece, and are simple.
-Gloves. Nitrile gloves work best, as natural rubber latex can be negatively affected by the resin in its liquid stage. Buy a box of them if you don't have them around already, you will go through quite a few for this project alone. I love the harbor freight black 9mil gloves, since they have a much longer cuff.
-Dust masks. These don't need to be fancy, the standard bungee masks are fine. I wear glasses that fog up when wearing the normal ones, so I use the masks that have the small one-way valve on the front.
-Face socks. These aren't entirely necessary but they are nice to have to keep the resin dust out of your hair and face when sanding. They are usually sold in the paint aisles at hardware stores.
-Mixing cup(s). Any plastic container (a small bucket, quart size deli/crabos/to-go containers) will work, but make sure you have a way of noting fluid ounces on the outside. I picked one of these up for that exact reason; the container was pre-graduated with both fluid ounce and ML.
-Chip brushes. Chip brushes are your best bet as the hair used doesn't dissolve in the resin, they're cheap and are a one-time use consumable for this project. I suggest buying at least 4 of the 2" size. You can also use old paint brushes that are ready to retire.
-Drop cloth. If you're doing this on cement, in your parents driveway, or in your friends garage, be polite and put a drop cloth down. Removing cured epoxy resin from concrete is not an easy task.
NOT PICTURED
There are a few other tools that will facilitate this project not pictured above:
-Power sanders. you don't NEED them, but they will make the sanding process so much easier and less frustrating. To really take some high spots down, I used an angle grinder and coarse grit flap wheel. Then, I switched to an oscillating multitool with a diamond grit plate and 120 grit sanding pads.
-Scissors and razor blades. If you're only using mat, and not fiberglass cloth, you don't need these but they help cut the raw cloth to size.
-jute twine or hemp cord. This isn't absolutely necessary but the loosened fibers add another level of realistic dimension.
-Hanging plant hook. Again, if you don't have one of these you don't have to go buy one. you can hang your lamp from a tree while you work on it, from the ceiling in your (open) garage, or build a small stand.
Step 4: Suspend the Play Ball
It is easiest to work on this lamp shade while it is suspended. the easiest way is to hot glue a length of twine to the top of the ball. Use a decent amount of hot glue and twine on top, as it will easily pull free from the ball at first. Tie the string so that the ball hangs at a comfortable working level for you- for me this was below shoulder height.
Step 5: Cut the Fiberglass Cloth Into Strips
If you're going the route I did and using cloth for the initial layer, it is going to need to be cut into strips first. think of it like you're building a round piniata from fiberglass instead of newspaper. You want to build up layers of overlapping strips. The most efficient way to cut it down to size is with a razor, but sharp scissors work well, too.
Step 6: Mixing Resin
Follow the steps on the can and add the required amount of harder to your resin. Stir it very well with a paint mixing stick for at least 2 minutes. I only needed about 8oz, but I like to mix more beforehand, as mixing additional on the spot takes too much time.
Step 7: First Layer
The resin will have a workable time frame of about 12-15 minutes before it sets up too firm to be usable. As soon as your resin is mixed, paint a layer of it over the full face of the ball. Lay overlapping strips of fiberglass cloth over the surface, and paint more resin onto the surface of them. Then, you can begin working the resin into the cloth with your hands and the brush until the fiberglass has absorbed all the resin it can hold and turned transparent. This is known as wetting it out. Once the ball is coated with a full layer of cloth strips and thick resin, stop. Give it about 30 minutes and it will have set into a hard shell.
Step 8: Cut/tear the Fiberglass Mat
Once the first layer is down, you're going to begin building additional layers on top with fiberglass mat. Instead of strips from now on, you want to use rounded edged, irregular, pieces. If you have a very round piece, cut lines in toward the center to help it fold around the the curvature of the ball. since it isn't woven, the mat can be easly torn and ripped into sections by hand.
Step 9: Wetting Fiberglass Mat
Mix up another batch of resin, and begin dunking the mat into the resin, and layering them over the first layer of fiberglass cloth. Pat the resin soaked mat pieces all around into the sphere and let dry. Don't worry too much about irregularities and imperfections and drips, thats what makes the surface look naturally formed when lit from inside.
Step 10: Separate Jute Twine
While the second coat is on and setting up, but still tacky, take about a one foot section of jute twine and begin unwinding it into a small pile of loose fibers. Take these fibers and stick them randomly all over the outside of the sphere, and leave to adhere while the resin sets up again. It may look a bit odd and un-moonlike at this step, but the fibers will be embedded under the third layer of resin and mat.
Step 11: Add the Third and Final Layer of Resin and Glass
Add the final layer of of resin and fiberglass over top of the jute fibers. Paint in additional resin on top as it begins to set up. Continue to do this until the resin is too firm to brush onto the surface of the sphere.
Step 12: Time to Sand
This is the most tedious part of the entire project, leave plenty of time for sanding. Wear a mask, face sock, gloves, and a long sleeve shirt if you have them. I started with the heaviest, coarsest grit of sandpaper that I could find- this turned out to be the flap wheel for my angle grinder. It is at this stage that determines the final finished product. Using the coarsest grit quickly takes down high and uneven spots, burrs, and lumps. You want to use this step to start smoothing out the surface.
Step 13: Check for Irregularities and Roundness
After you have sanded and sanded...And sanded some more, stop, and check out your little moon. Walk away for a minute or two, and come back with fresh eyes. Look it over carefully, check for any exposed glass fibers sticking out. Exposed fibers can be trimmed back with nail clippers or an x-acto hobby knife. If you sand through one layer and into a bubble where a void is created, leave it be. This will look like a crater when lit!
Step 14: Finish Sanding
In the final sanding step, once the high spots and craters have been leveled, the surface is as round as you would like, its time to dull the surface and add detail with finer grits. This will build up resinous dust that will collect in all the tiny cracks, voids, and edges of some craters. At this point, it will begin to look really lunar without even being lit. After this stage you are mostly done outside.
Step 15: Clean Up
Just as with cooking, and any project, cleanup between steps should be considered part of the project.
Step 16: Washing the Surface
Once you're done sanding, take a damp paper towel and wipe down the entire exterior of the moon. Toss the paper towel and repeat, a couple times, until all the dust has been removed from the surface. It starts to look ever more moonlike with each step!
Step 17: Remove the Play Ball From Inside the Shell
If you didn't grind a small hole where the string was attached when sanding, you can cut small hole, about an inch and a quarter diameter in the top of the shell. Puncture or deflate the ball, grab with a pair of pliers and pull it through the hole in the top. The ball will slide out very easily, leaving a perfectly smooth surface inside.
Step 18: Test It Out!
Once the ball was out, I held it up to a ceiling fixture so that I could get an idea of how it looked and to check for anything else I may want to remove. It looked fine to me, so I went on to mounting the light inside.
Step 19: Trace, Cut, and Mount the Pendant Threaded Ring
The pendant cord that I had came with a small threaded ring, which threads around the socket and has a flange meant to be larger than a hole cut for it. I traced the smallest outside area of the threaded ring and cut it out using a rotary saw. you could easily use a dremel, a jewelers saw, or even a set of files. I affixed the ring inside the hole using a quick set 2 part epoxy.
Step 20: Let There Be Light!
The type of light bulbs used in this application have to be as narrow as the inside of the ring epoxied to the top. This rules out incandescent bulbs, but there are a myriad of other options available. For this particular light and size I used a narrow CFL bulb, 40watt equivalent. I have also recently seen LED light "sticks" that would work great for this application, as well as a narrow fish tank bulb. Insert your light, plug it in, and stand back in amazement at the gorgeous work of art you just created!
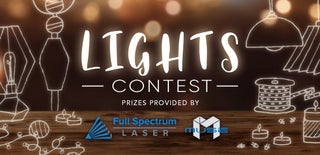
Second Prize in the
Lights Contest 2017
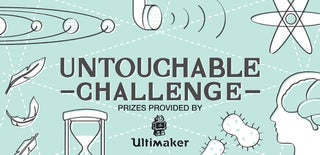
Grand Prize in the
Untouchable Challenge