Introduction: Reclaimed Wood and Structural Pipe Full Wall Bookshelves
My wife and I are both avid readers, and have talked about having a bookshelf that takes up an entire wall since we first met almost 15 years ago. We now own a house and were finally able to make it happen! I was inspired by some other designs using pipe and thicker wood, but have a lot of suggestions in this Instructable on how to make this project a bit easier and a bit stronger than using galvanized plumbing pipe. This project could be scaled up or down, depending on your space, budget and needs.
Supplies
Supplies:
I'm linking to what I used, but you don't have to use these specific items.
Wood - I used reclaimed 2x10 joist wood
Pipe - SteelTek pipe and fittings from Lowe's are what I settled on. I used 6x 10-foot sections of their 3/4" galvanized pipe with some remainder.
A variety of fittings for pipe - will vary with your wall, here's what I needed
- 24x tees
- 4x railing supports
- 4x elbows
- 25 floor flanges
- 1x end cap
Wall fasteners - these 5/16" togglers are great
Tack cloth
Sandpaper - 320 grit or above
If painting pipes:
- Primer
- High quality metal paint
- White vinegar
- Baking soda and water
- Acetone or other solvent
- 3M Green Scotch Pads
Short drywall screws
Pipe straps
Scrap wood about 5' or 6' in length, 2x4s are best
Tools:
Circular Saw
Speed Square
Orbital Sander and/or Belt Sander
Router
Tubing cutter
Stud sensor
Paintbrushes and stain brushes
Old t-shirts
Painter's points
Clamps
Large and small bubble levels
Drill and bits
1/4" allen wrench
Step 1: Plan Your Design
I spent quite a bit of time planning this project to ensure that it would look great and also be strong enough to hold all of our books. Additionally, I ended up adding a few joist braces in our basement to ensure that the full weight of the shelves and books wouldn't harm our house - this is not something you will necessarily need to do, but it doesn't hurt to consider it.
Our wall in our living room is a little over 13 feet in length with a doorway into other rooms. So, we decided to do 6 total shelves along the wall, with 5 of them from the wall to the doorway and the top shelf going over the top of the doorway. My shelves ended up being 113" in length for the 5 shorter shelves, and 156" in length for the longest. This allowed for a bit of space on each end - I didn't want to have them bump up against the wall, but have a gap all the way around. In planning for the spacing and height of everything, I also considered the light switch, outlet and vent cover on the wall.
It's pretty typical to support bookshelves at least every 3 feet. Our stud spacing is 16" on center, so I chose to create four standards (the vertical supports) and thus four horizontal supports for each shelf, three of which were secured to the studs. Given that I'm using 2x10 boards with a lot of strength, this design worked out to be very solid. I strongly recommend planning your design around securing the shelves to the studs!
The horizontal supports in the studs also share the load of the books with the vertical pipe standards, which also help keep the shelves level - I feel this is an extremely strong design that way, and after finishing wouldn't hesitate to line every shelf full of books. It avoids having to run the pipes through the wood as in other designs, which I feel adds a lot of unnecessary complication and work. I planned for 4 standards/columns but probably could have gotten away with three. "If it's worth doing, it's worth over-doing" as the Mythbusters are fond of saying.
Regular threaded galvanized pipe is somewhat of a pain to get all of the fittings and measurements to meet up - you have to thread the ends of the pipe for this to work, and get it in lengths, have it cut or buy a die to make it work, so I opted for a more modular approach with the Steel-Tek pipe. It was easy to work with, and I already had all tools necessary to perform the assembly - a tubing cutter and a 1/4" allen wrench are really all you need.
As you'll note if you ever have to move your books, they are quite heavy. In researching the total weight of our entire shelf assembly plus books, I came across a few websites that indicated books weigh between 20-40 pounds per foot of length - that's a lot! It depends on the type and size of the books you are considering, I thought it safe to assume about 25 pounds per foot for the type of books that we would be putting on these shelves. In total, this bookshelf - including wood, pipes and books, was going to weigh between 1500-2000 pounds. Given that we're putting all of our books in the house on this one shelf assembly, I thought it prudent to consider the engineering aspects of the wall and floor where we would be installing.
Floors are designed to hold a lot of weight - like really a lot. So are load-bearing walls. I attached this to a load-bearing wall and fastened it to the studs, but my main worry is that it would be parallel to the joists rather than perpendicular. There is a bit of a difference here because all of that weight rests mostly on two joists rather than several of them. So, I installed an extra row of these amazing cross-braces from EZ-X Bridging to distribute the weight more evenly across the joists, and could not be happier. I also remediated some notching in the joist and a brace that was not functional. It might be overkill, but I didn't want to ruin my floor! This is just a consideration, not something that you should worry a ton about, pun intended.
Step 2: Cut Pipe to Length
It ended up being much cheaper for our shelves to purchase the galvanized Steel-Tek pipe and paint it. Plus, I was unable to source the black pipe in 10-foot lengths at our local Lowe's and it is not on their site or app, so I chose to just purchase 10-foot sections of the galvanized and paint it black. You can purchase this pipe in 1-foot and 5-foot lengths as well, which is handy if you don't have a tubing cutter and a good setup to cut the tubing - I happened to so chose to go the more economical route. I also looked into and got some samples of Maker Pipe, if your application is a lighter duty one this might be a cheaper option for you and looks promising. Their video on painting galvanized pipe was enormously helpful for me.
My design required standards for the shelves (the vertical pipes) of 82" to allow the very top shelf to be parallel with the top of the door. Each of the little support tubes were 11.75" - this allowed for the fittings to slide over the tube and leave just a bit of wiggle room for the board to rest between them. 1-foot sections would have worked just fine as well, if you choose to use this design you could easily purchase 1-foot sections for the horizontal tubes instead of cutting them.
I have a very large vise, and these types have jaws intended for holding pipe, so I clamped it (somewhat gently - these jaws will leave marks in your pipes if you clamp it down too hard) and measured out 11.75" sections for the horizontal pipes and cut with a tubing cutter.
I'll note that the overlap for the tees where the pipe goes into the fitting is 1", and the flanges is 1.5". This is an important consideration in the design so that the tubes can be the proper length to be secured by the grub screw that bites into them.
One tip for cutting pipe (that I'm sure most plumbers out there will already know) - if you want to prevent the cutter from making a spiral instead of cutting, start going in one direction one rotation and then reverse. This creates a track for the cutting wheel to follow back around, which keeps it from wandering down the pipe. I've been cutting tubing wrong for years and struggled with this, and finally figured it out on this project - it's always nice to learn a new technique!
Step 3: Dry Fit Pipe Assemblies
If you're not painting the pipes, congratulations - you have saved yourself hours of labor! But you'll still need to "dry fit" your design. I took the first set of my basic assembly in from the garage to make sure that the standards were tall enough, and the horizontal supports were the right length. I put one of the horizontal supports on a board with fittings to ensure that the gap between the board and fittings was the right length. I'll note I did this before cutting allof the pipe to make sure all was going to fit as expected. Same with the shelves, I brought one inside to ensure it fit perfectly before cutting the others. It is always helpful to get a feel for how the design might work and what issues you need to address before you go and cut all of your materials to the lengths you think you need.
Step 4: Build Pipe Painting Holders
My design for holding the pipes for painting was pretty basic - I drilled a bunch of holes in some scrap pieces of wood. For the small supports - I had 25 of them in total - I took a 28mm forstner bit and drilled through some old flooring and a 2x4. With the 2x4 I just went down about 1/2-3/4", the flooring I went all the way through. My strong recommendation is to just use a 2x4 - the flooring rack had a lot of tubes in it and they went all the way through to the floor, and it's just not as stable as a heavier base to hold all of the slightly floppy tubes upright when painting. You won't be able to paint the very ends, but that does not matter - the fittings will cover this up nicely.
For the longer pipes, I clamped two offcuts from the shelves that I was using together and drilled all the way through one of them into the other. I then drilled down about 1/2-3/4" in the second one. This allowed me to stick my finger in the end of the pipe through the piece that I'd drilled all the way through and rotate it for painting - it worked very well!
Step 5: Prep the Pipe for Painting
There is a local bar that we frequent which has a larger diameter of this same pipe and fittings as a main design element for their railings and shelves. I sort of based this design off of that, with black pipe and galvanized fittings (plus, the black fittings were way more expensive and harder to get). So, we chose to paint the pipe black. If you want yours to be completely black, I would recommend just buying all of the black fittings instead of painting them.
Now, if you've ever painted galvanized pipe before, you know that it doesn't like to take spray paint very well - the zinc in the galvanized layer reacts with paint and creates a film that doesn't allow the paint to adhere.
So, to paint galvanized pipe properly you need to etch and partially remove the zinc layer. I did some research and testing, and settled on the following process - scrub the pipe with 3M green scotch pad, wipe with vinegar, clean off with water and baking soda, wipe with acetone, then prime with self-etching primer then paint.
I love 3M green "scrubbies" for a large variety of projects, and always keep a lot on hand. They are great for removing rust from metal, and cleaning a lot of things. Buy the big bulk packs and cut them in half with a regular pair of scissors, it is much cheaper that way. I just put on a pair of gloves and went to town scrubbing the pipes lengthwise - it probably took about an hour to do all of my pipes.
I then just took a shop towel and some regular white vinegar and wiped down the pipes, applying the vinegar liberally. I left it for about an hour, then mixed some baking soda with water and cleaned them off - this stops the etching process of the vinegar by neutralizing it. You'll notice quite a difference after this step - the vinegar really etches the rough surface created by the scrubby, and there is a lot more friction on your towel when wiping down the pipe.
After cleaning off the vinegar, the last step before painting is to wipe down with a solvent - I chose acetone but mineral spirits, xylene, denatured alcohol, etc. all work just fine. I typically wear a respirator and gloves when handling acetone and suggest you do the same - it's pretty nasty stuff. Also, always put the towels you use with these solvents in a metal trash can or seal up inside the gloves that you're throwing away - solvents that evaporate quickly can heat up the rags and start a fire.
Step 6: Paint the Pipes
Painting is about 80% prep work, 19% drying time and 1% actual painting. I used an automotive self-etching primer to ensure very good adhesion to the pipes, and some flat black paint of good quality. I recommend getting a good finish paint - really cheap Krylon is the absolute worst for stuff like this. It was cold in my garage, so I heated it up with my propane heater for painting and kept the paint cans inside, and allowed for a much longer cure time for the paint than I would have otherwise.
Two coats of primer and two of paint seemed pretty good. I did this all about a week before install, and brought the pipes inside to my basement so that the paint could cure properly - if you're painting in the winter in a cold climate this is a really good way to do all of this.
Step 7: Cut the Wood to Length
We managed to score some really nice lumber for very cheap from a friend, but it had been sitting out in their yard for a bit, so took more time to prepare than if it were purchased new. I cut these shelves to be a bit shorter than the length of the wall to allow for a bit of a gap between the shelf and the wall, as well as the shelf and the door. The shorter ones were 113" long, the top shelf ran the length of the room minus about 3" and was 156" long.
In addition, to keep from bumping into the corner of the shelf as you walk in and out of the door, I cut the corners closest to it at a 45-degree angle. This is really easy to do with a Swanson Speed Square and your circular saw. If you don't have one of these, get one - they really should just come standard to accompany a circular saw in my opinion, and are probably one of the most valuable woodworking tools to own.
Simply cut the wood to the desired length straight along its width (using your speed square as a fence to keep your cut straight). Then, rotate the square and scribe a line at a 45-degree angle following that side of the square. Bump your speed square over to account for the gap between where the blade is on your saw and the edge of the flat guard and use the square as a fence to keep the cut straight. I clamp the square in place on wider boards like this since it is safer and more accurate, for 2x4 cuts it's easy to just hold in place with one hand and saw with the other. This gap is exactly the width of a furring strip for my saw (not sure how standard this is), so I use a scrap of one of those as a spacer to make this whole operation much quicker when adjusting the square - YMMV.
Step 8: Sand, Sand, Sand
Sanding always takes more time and effort than you think it will. Our boards were rough joists that had weathered which we wanted to have a bit of character and imperfections, but smooth and finished enough to look nice and put books on. I took our belt sander and 50 grit belts to rough sand the weathered patina off, then an orbital sander with 120 grit paper to smooth it out. My wife and I tackled this together and it took the better part of a Saturday to accomplish. I put down some hockey puck bench cookies that I made to keep the wood stable while rough sanding, then plopped on some sawhorses for finish sanding.
Also, to round the edges down a bit in a more uniform fashion than sanding, I routed the circumference of the edge on both sides with a 1/4" roundover bit.
If you have a thickness planer, this will take hours off the time of your project and in retrospect I would have just rented or borrowed one of those instead of belt sanding, then finished off with the orbital sander. Sometimes you just gotta use what you have and put some elbow grease into a project, though!
Step 9: Build a Stain Drying Rack
To vastly expedite the staining and finishing of the wood, I made a little rack to hold each piece while it dried. While we were staining and finishing, we put the wood on a set of these hockey puck painter's points that I remixed and made - you can also just buy painter's points at the hardware store, or make your own with a 3d printer or some scrap wood and screws or nails.
I just took an offcut from the board that was a 2x12 which I had to rip down for this project, and drilled holes into it at regular spacing of the boards plus a bit of a gap for fingers. Using a pilot hole drill bit for this step is critical - it lets you countersink the screw head enough so that the board sits flat. I used 3" wood screws. Once you are done you can reuse the screws and the wood!
Step 10: Stain the Wood
We matched the color of our wood as closely as possible to our floor in the living room where the bookshelves would be by using stain. I'm a fan of Varathane finish products, so used one of their wiping stain - Gunstock was the color, it's slightly reddish.
All you have to do is brush some of this stuff on the wood (we used those foam brushes because it's oil-based and I hate cleaning that out of paintbrushes), then wipe it off. They sell t-shirt fabric wiping rags for this purpose, but we used old clothing - an old worn out t-shirt works great, and is cheaper and less wasteful. Use a drop cloth if you don't want to stain your floor the same color as your bookshelves.
Before you stain the wood, take some tack cloth and wipe it down - this removes all of the sanding dust and will make for a much smoother finish.
For the stain we used, you apply, wait two minutes (we set a timer so we didn't get distracted) then wipe off. So, we did this to each board on one side, flipped over and did the other, then set on the rack to dry until the next day.
Step 11: Polyurethane the Wood
After the stain had fully dried, we applied a coat of Varathane polyurethane. This stuff is great, it's water based and durable, dries quickly and comes in non-glossy finishes as well. I use it for most applications that require sealing wood with polyurethane. We put a coat on with a paintbrush using the same process as the stain (without the wiping of course) and waited a couple of hours. You can store the brushes in a plastic bag between coats, and clean up with water.
We then sanded lightly with 400-grit sandpaper - don't go crazy with this step, you're just knocking off any little bits of sawdust or grit from the polyurethane. After that, we wiped again with tack cloth, and applied another coat of Varathane. We did this about a week before installation so it had a good long time to dry out. Two coats seemed plenty for this application, high-wear situations usually require three.
Step 12: Install Initial Horizontal Supports
As with painting, most of a project like this is the prep and planning, and very little of it is the actual installation. With all of our materials properly sized and finished, it was time to finally attach them all to the wall.
We started with the lowest shelf and attached all of the horizontal supports to the wall. Keep in mind a few things for spacing - we landed the lowest shelf just above an outlet so we could still use it, and spaced the shelves with the light switch in mind so that it was between two shelves and accessible. If you replicate this project in your own home, you'll need to plan around such things in the design phase.
Our house was built in 1955 and has metal lath and plaster instead of drywall - this is the hardest wall in which to find studs! A stud sensor doesn't really work, you can't use a magnet or magnetic stud finder app or sensor, etc. I had to do a lot of knocking and some "exploratory drilling" to get the center of the first stud. Fortunately, our studs are 16" on center dead on so the rest of them were a breeze. I intentionally drilled my exploration holes to be hidden behind one of the flanges so we didn't have to fill and paint them.
We spaced the first row so that at least two of the flange screws were into the stud, with the other two being installed in my favorite wall anchors. One could rotate it so the hole pattern makes a diamond shape with relation to the stud and achieve the same effect, I don't think there's honestly a difference. Only one of the columns of supports was exclusively into the plaster, the last one closets to the perpendicular wall - this seemed just fine.
We then measured out 32" and installed the second support level with the first, and repeated for the other two columns. Getting this first row's spacing dead on was critical for all of the others so it took the longest.
Step 13: Determine Shelf Spacing and Install a Vertical Column
Here we took a little time to really figure out our shelf spacing before proceeding - I had a rough idea for what that would be, but I do a lot of projects like this by feel and repeated measurement. We took a standard and ensured that the spacing between the tee fittings was even, then attached flanges and traced their holes on the wall so that we'd have a good start to each run of horizontal supports. There is quite a bit of slop in the pipes where they go in the fittings, so I used a little bubble level to ensure all supports were level before scribing the hole pattern.
Once the pattern for the holes of the flange was scribed on the wall, I drilled with a 5/16" bit for the wall anchors, and a 1/8" pilot bit for the screws that would go into the studs. I recommend installing one screw into the anchors, then going across in an "X" pattern for the others, not tightening all screws until last - I think of this like installing a tire on a car, it allows you to straighten out and adjust as you go. If you put a little box underneath you can catch a lot of the plaster and minimize the mess.
After installing this column of supports, the rest of the supports can simply be level with them and follow the studs up the wall.
Step 14: Install All Horizontal Supports
To ensure that our columns were straight and into the stud, I just took the level and ensured it was plumb, and scribed a line along the wall where the studs were - this cleaned off our paint easily with some light scrubbing and some Simple Green. If your wall is white you may want to use a piece of tape instead.
For each row of horizontal supports, we took the level and placed a flange with two of the holes over the scribed line and completely level with the previously installed support. Rinse and repeat for the rest of the supports. I checked them all for level before tightening down the screw that holds them in place, and adjusted as necessary in the next step.
Step 15: Add Shelves and Standards
With all of the horizontal supports in place, the rest of the installation went quickly. We simply placed each shelf on the supports, selecting cool features in the grain and edge to be visible based on placement. Then, we slipped each standard over the horizontal supports and adjusted the tee as necessary to keep the horizontal supports level and in contact with the shelf boards. It helped to space these all out roughly before installation, just don't tighten down the tees too tight so you can adjust them as needed to slip over the horizontal supports.
The very top shelf simply sits on top of the last row of supports, and since it ran over the top of the doorway I just waited to install that last little support until we put it in place to make sure it was level with the top of the doorway.
Step 16: Add Underside Clips
To keep the shelves from getting bumped and moved, I installed a few of these 3/4" plastic clips with 1" drywall screws on the underside - there was one wonky shelf with a bit of twist in the wood that needed them to pull it down onto the boards. I used plastic because it was easy to paint black, but metal electrical clips work equally as well - they are galvanized so you'll have to etch, prime and paint if you decide to go this route (or just leave them shiny if you want).
Step 17: Add Books and Enjoy!
We were finally able to put almost all of our books in one place in our house, which is very exciting! Our cat was very interested in the shelves so we had to get the books up quickly before he ran around and scratched them up, as he is wont to do with everything (darn cats!).
We're both very pleased with how this all turned out and are excited to get our books organized for years of enjoyment.
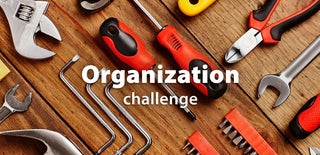
First Prize in the
Organization Challenge