Introduction: Cast Aluminum Pendant
In a previous Instructable we saw how to build an inexpensive furnace for melting down aluminum. Now we'll look at making some pendants by melting down scrap aluminum from soda cans, broken car parts, etc. When polished, aluminum shines with a brilliance that rivals silver. However, we can now make these pendants using material that would otherwise be thrown away. In addition, many "silver" pieces of jewelry are actually silver plated, and so the silver wears off after a period of time, but since these will be made from aluminum the finish will never wear away. If the pendant gets scratched or otherwise damaged it can always be sanded and polished and brought back to its original finish.
To start, you'll need the following:
- Furnace w/crucible
- Sand
- Bentonite clay or used motor oil
- Container of your choosing
- Sand paper: 80, 180, 300, and 600 grit
- Metal polish
Step 1: Preparing the Mold
For this Instructable we'll be using a sand mold for the casting. To start you'll need to mix up a batch of green sand. If you're unfamiliar with green sand, I highly recommend doing a quick google search on the subject. Most use a mixture of bentonite clay (found in most cat litters), sand, and a small amount of water. However, for simple castings such as the ones shown here, I've found that mixing some used motor oil and sand works just fine. Keep in mind that finer sand will result in a better surface finish and will not only capture more detail but will also result in a better finish that will require less sanding later. Making this mixture is similar to making conventional green sand, you'll want to mull (mix and squeeze) the mixture of oil and sand, so that the oil binds to the sand particles. Again, a little research on green sand will go a long way. Once you've got your green sand prepared, find a suitable container for your mixture. The container should ideally be about twice as deep as the thickest piece you wish to cast, so as to prevent the heat of the metal from damaging the bottom of the container.
With the green sand prepared it's time to make the actual mold. For this you'll need an object to press into the sand to make an impression. Keep in mind that this technique will leave always leave the top of the part as a flat surface, therefore it may not be suitable for more complicated geometries. Wood carvings work well for this as long as the surface has been sanded smooth. 3D printed parts can also work. However, most prints leave the part a ridge where each layer was added, so additional preparation may be necessary such as sanding the part or even applying body filler or similar product to smooth out the surface of the part. Objects with significant detail can be cast using this method, however it may be beneficial to instead cast a simplified version and add the details later using etching, machining, etc. Talcum powder can also be used to aid in the making of more complex molds by keeping sand from getting caught in the details of your part.
Step 2: The Melt Down
This step is pretty straight forward. If you haven't already got some aluminum ingots lying around, find yourself some scrap aluminum to melt down. Soda cans work fine, but be aware that they produce a large amount of slag due to the inks they're coated in. Also, between the inks being flammable and the aluminum being thin, the cans will try to oxidize very quickly, so wait until your crucible is nice and hot and try to submerge them into the molten aluminum quickly. Aluminum bottles will work even better. They yield far more aluminum as the body is far more thick than aluminum cans. Old or broken car parts and lawn furniture made out of aluminum can be usually be found for little to nothing and yield the most aluminum, but will need to broken up before melting down.
Before pouring make sure to remove any slag or oxidation that comes to the surface and degas as necessary. Any impurities left on the surface of the pool will not only contaminate the pendants but will also make the aluminum more difficult to pour. Make sure to pour slowly and carefully. From my experience I always tend to pour too much into the first mold. Remember, excess material will need to be cut, ground, and sanded away, wasting both time and material. Once all the metal has been poured out let the metal cool for about an hour.
Step 3: Cleaning Up
With the pendants made, next we need to clean up the castings. Start by removing any excess metal. I find that a reciprocating saw does the job quickly and without wasting too much material. Spraying a small amount of WD-40 or similar lubricant on the blade will help to keep the aluminum from gumming up the teeth and will cut through the aluminum faster. Once the excess is removed you'll want to smooth out the surface of the casting and reshape any areas that didn't come out as they were suppose to. The quickest way to do this is with a pneumatic die grinder and about a 40 grit sanding disk. Be careful not to get too carried away as a new disk will remove material very quickly. The goal here is to remove large imperfections and shape the pendant. Before moving on, be sure to drill a hole in the e With that done, if you're sanding by hand you'll want to sand the piece thoroughly with 80 grit sand paper, followed by 180 grit. If you're using a powered sander then go ahead and start with 180. With these two grits we want to remove any remaining imperfections, remove the large scratches left by the 40 grit disk, and perform the final shaping of the piece (rounding off sharp edges, adding fillets, etc.). As with sanding any other material, you're basically making smaller and smaller scratches in the surface until they are no longer visible. Therefore you should not be able to see any scratches left by the previous grit before moving on to the next grit. After sanding with 180, use 320 and start wet sanding the pendant (make sure you have wetordry sandpaper), followed by 600. At this point, if you have a powered polishing tool or attachment, you can go ahead and use metal polish to bring the surface to a shine. However, if doing this by hand or you want a mirror finish, I would recommend wet sanding with 2000 grit first, and then polishing. You can also stop after using the 600 grit to achieve a brushed finish.
Step 4: The Finishing Touches
Now that we have our finished pendant, we can start making some custom jewelry. I've found that eye pins work well when attaching them to your jewelry. Use them for necklaces, as charms on a charm bracelet, use them to make some custom earrings, or whatever comes to mind!
Interested in pendants like this but don't have the time to make them yourself? Check out my Etsy store!
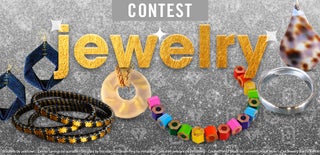
Participated in the
Jewelry Contest
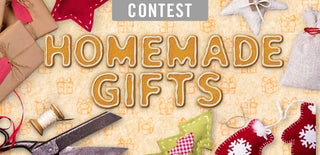
Participated in the
Homemade Gifts Contest 2015