Introduction: Reverse Resin Intaglio
The Quest for Reverse Intaglio: /inˈtalyō,inˈtälyō/
Engraving has been around for centuries and this form of reverse carving is extraordinary. As an artist I find it truly rewarding to research the history of such unique things. Reverse Intaglio seals and jewelry like cameos have intricately carved portraits and scenes, mostly created in Quarts, Onyx, shell, and other stone.
The Artisans use many tiny carving tools and painstakingly start carving out the details.
I sought out to find similar works in resin.
What I found was lots of vintage pieces of reverse carvings from around the 1940s created in Lucite. However, I didn’t really find works cast in epoxy.
Yes, we can embed things in resin and cast things in resin, but it was this clear and semi-transparent engraved look that I was interested in. Most important was that I wanted to create not only small jewelry items but large-scale pieces.
I went into the studio and began thinking about how I could recreate this elegant style but in Epoxy. After many tries, finally, I could say I did it.
So if you are interested in how to achieve the look of hand-carved Reverse Intaglio, you’re in the right place.
This Ible will teach how I create intricate pieces without using drills and carving tools.
So let’s start with the look. I pulled some photos from Google on Reverse Intaglio jewelry, this really was inspiring and gave me a great sense of the look and the amount of detail that each piece possesses.
I have a few methods, but the one we are doing today is the wax version. Similar to the lost wax method in metalworking. There are high temp waxes if you don't want to cast in silicone.
Wax is more affordable but silicone or composimold are reusable.
Step 1: Wax V/s Silicone
I wanted to show the difference between the 2 methods so you can make an informed decision.
The pink mold is a silicone casting mold it is what is common. My silicone shapes are not common.
The 2 yellow pieces that are ahead and a part of the Seahorse is made of Amazing putty silicone. I used the putty to make a positive it was pressed into the silicone mold so I could then have a flexable shape that could easily be removed from cured resin shape. Leaving behind an embossed space resembling Reverse intaglio
Resin gets warm or very hot depending on the volume your mold requires. my pieces with wax are small jewelry size silicone molds so they don't heat up as much. But in my testing, I had an epic fail.
Oh! Yes, I did!!
I really love large projects so once I got the jewelry figured out it was time for a large piece. Going to create a table with a Reverse Intaglio piece in it. So I have my skull, cast of wax and ready for my large disk of resin.
You heard Large right???
The resin is mixed and poured in my silicone cake pan, then in goes, my wax skull suspended with a paint stick.
Guess what ?? Yep,
My global warming experiment past. My mass of resin ran a temp and melted my wax like a snowman on the beach !!
So PLEASE look at the pictures, read the instructions and ask questions. It works with wax but silicone shapes are better if your not a person who loves playing and testing.
Step 2: Materials
Inspiration (study the style this will aid you in your composition)
Clear casting resin (liquid Diamonds) or UV Resin use coupon code( The Juliart ) for 20% off $20 or more at The Epoxy Resin Store (I don't work for them just use their product a lot)
Silicone figure molds ( common molds)
Silicone jewelry molds
Clean candle wax or paraffin (used candles to work fine, just no dirt etc.)
Mixing cups and stir sticks
Resin color (optional)
Cornstarch. ( Stone powder) Optional
Face mask
Gloves
Eye protection
Sanding files or paper 80 grit to 1200 grit, polish
Paper towels
A small torch (used for melting wax pieces and removing air bubbles in resin)
Embossing heat tool or Hairdryer
Safe and clean work area (put down wax paper or butcher paper)
Hobby knife, scissors, tweezers, toothpicks, paintbrush
Alcohol Inks( great for a transparent color) Matte UV sealer
Black or white paint ( colors you desire) Acrylic paint
Step 3: Casting Mold in Wax
These silicone molds help keep us from sculpting but you can carve your own wax design and eliminate this step or sculpt and make a silicone master. The scale is entirely up to you and the project you want to do, but I do recommend testing.
Place the silicone figure mold down in front of you. Decide how much of the design you want to use. Like if it is a horse you may only want the head, or if it is a cameo mold and you only want the relief portion.
Now take a small piece of the wax with tweezers, while you are holding over the mold heat with the torch dripping the melted wax into your mold. If you overfill or git drips, no problem you can take the hobby knife and clean it up. You can carve added detail or merge multiple pieces to create your desired look. Like 2 horses head together.
Let cool completely and remove from molds. Set aside. (Can chill in the freezer to speed up time)
Note: If you are going to mass produce your pieces or want thick resin pieces, this is where my other method of using silicone instead of wax to make the design pieces is very important. I cast silicone in silicone, but you must use release. Now you have a flexible shape to be used in the resin. Follow the rest of the steps.
Step 4: Sizing the Wax and Casting Resin
You want to size up the wax to fit into your base mold. Position it to check for fit and layout. Place the wax piece to the side.
Now make sure the base mold is clean and start mixing your resin. I used a 1 to 1 resin Liquid Diamonds.
VERY VERY Important::: Resin heats up if you are doing the wax method and cast resin to thick it will melt the wax. if thick casts are what you desire, use silicone.
Pour resin in the mold. Don’t over fill, leave a little space because the resin will rise once the wax is placed in. Use a torch with quick bursts to eliminate bubbles.
See pictures for the next portion.
I take a flat stick and add a little wax in the middle, then heat and apply it to the backside of my cast shape. Wax to wax. This is how it stays suspended in the resin. Note: if your resin is not all the way to the edge no problem, just add more resin once the wax is in place.
Let your piece cure without being disturbed. I place a plastic container over the top.
Follow resin directions: usually, if the room is warm over 78°F it will cure in 12 hours. Cold room longer curing.
Too thick maybe to hot for wax.
I use UV resin for some and they are done in minutes. Even though it heats up it cures the design before it melts. Some other brands of epoxy resin cure much faster and much hotter just do your research.
Step 5: I’m Melting I’m Melting
Now, this is the fun part. Just like the lost wax method, we are going to melt out the wax. Fold up paper towels, pop off the stick. With a hair dryer or heat gun, begin melting away the wax. It won’t take much so don’t overheat. (If you did the silicone method, it just pulls free and can be reused no melting needed)
Blot the wax out as you go. You can flip the piece over and warm the front the wax will drip free. Take soap and a nailbrush and clean very well. Let dry
At this point, you should have a piece that resembles the hand-carved Intaglios of the past. Oh yeah!
Step 6: Sanding
You should be proud because no matter what your subject is they look really cool.
Like ice sculpture, hidden inside the ice. But let’s finish these babies.
Depending on how you use your creation will determine the finish.
See pictures:
Most plastic and silicone molds have a shiny interior and that produces a shine on the resin surface if it is dull it will cast dull and sanding may be needed.
You sand the back and the top should be clear and glossy from the mold.
Start with coarse sandpaper working your way to fine. I only had to sand the back on the seahorse and cameo but the black piece in the picture is to show if you flip the back upward just the edges are sanded and left matte.
Study the art and you will see the difference. More resin can be applied to the top and back to make crystal clear. ( called doming) Only do this after you have finished painting or detailing.
Step 7: To Color, or Not to Color?
Engraved from the back or engraved from the front.
If the back is facing you, you can sand the back, apply color to the flat part of the back and leave the design clear, you can apply nail polish lightly to the inside and then dust with stone powder or cornstarch. Use a clean, soft brush to dust and remove extra, or just mix some in the polish and keep on hand.
For a permanent option do all your pieces then coat the inside with clear resin to seal. This gives the piece a semi-transparent look.
Most plastic and silicone molds have a shiny interior and that produces a shine on the resin surface if it is dull it will cast dull.
To color, you can paint solid with acrylic, nail polish etc. I love transparent and semi-transparent so I colored the seahorses with alcohol ink and sealed with a matte nail polish.
This technique can really create some great looks in our small art pieces but it can be dynamic in large projects and make the lighted piece even more amazing.
I love the clear bowling ball with the skull in it so I hope my table will be just as cool!
Thank you! The Juliart
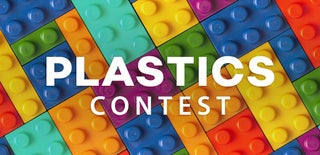
Participated in the
Plastics Contest