Introduction: Sculptures Made From Recycled TIRE TREADS
I was commissioned by Goodyear Tires to create these two sculptures to be presented at the 2019 NCAA Goodyear Cotton Bowl. These sculptures represent both competing teams, Penn State Nittany Lion and The University of Memphis Tiger.
Start to finish, these sculptures were completed in just 15 days! The timeframe is always the hardest part of these builds. The reason there is such a short timeframe is because the NCAA announces the teams on December 8th, which leaves me only a couple of weeks to complete the team's sculptures to be presented at the game. Both sculptures weigh nearly 200 LBS each, and consist of over 400 Goodyear tires combined. There are also thousands of hidden staples, and screws. These two sculptures took nearly 400 man hours to complete and would not have been possible without my amazing team. Special thanks to Jeff Kilbane, Jim McFarland, Camerson Sarff, Sky McCollough and Diego McCollough for making these sculptures possible.
Supplies
4 lb. density polyurethane foam
Fiberglass resin
Fiberglass cloth
Recycled tires
Narrow Crown Staples
Steel
Paint
Wood
artificial turf
wood screws
wheel casters
hot glue
super glue
large paper roll
tape
Step 1: Sketch Out Your Design.
Sketch out your design in a profile view with exact proportions you want to create. Here, I am sketching out the Tiger profile view.
Step 2: 4lb. Density Polyurethane Foam
You can pour your own polyurethane foam (information on this will be on a different intractable) or you can purchase large blocks of foam.
To save costs, I poured my own foam in individual blocks.
Step 3: Cut Out Your Sketch and Start Piecing Together the Foam Blocks.
Cut out your sketch and lay out the polyurethane foam blocks so that they cover the entire surface area of your sketch. You can use any type of saw to cut the foam, my preference is a sawzall. You may cut the foam to better fit your outlined sketch.
Step 4: Start Carving and Refining the Shape
Start carving and refining the shape of the tiger. I mainly use a sawzall for this. When you start to get better proportions I switch it up to a rasp to make more precise details.
Step 5: Sand Smooth/ Add in Metal Armature.
Sand the foam smooth so you get an even finish across the surface. At this point, I add steel armature inside of the sculpture for more strength. To do this, I used a oscillating tool to carve out joints inside of the animals legs. I then welded steel tubing inside, and used foam spray to seal up the caverns.
Step 6: Fiberglass and Paint
Once you are happy with the polyurethane shape, fiberglass the entire sculpture making it extremely rugged, durable and able to withstand the elements.
I then begin to roughly paint on the tigers stripes to give myself reference for the tire portion of this build.
For the Nittany Lion, I wanted to portray tires as more of a muscular look, so I painted on a muscular look for reference.
Step 7: Cutting, Cutting and More Cutting.
Now the real work begins, Cut up hundreds of tires into workable pieces. I use heavy duty shears for this. Get ready for a forearm burnout!
Step 8: Layer the Tires.
I begin by layering tires making sure they overlap one another, and create a muscle like form over the inner structure. For the Tiger, I use thousands of shreds of painted tire to depict fur. This is a very tedious task and takes many hours.
I attach the tires to the fiberglass form by using wood screws and narrow crown staples.
Step 9: Refine the Details
I layer on more tires refining each detail meticulously. I then go over every single visible screw and crown staple with paint to hide them.
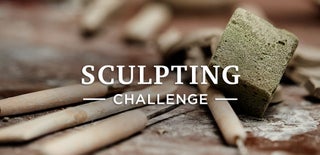
Participated in the
Sculpting Challenge