Introduction: Silver "Infinity" Earrings
These sterling silver earrings were made using Lapis Lazuli stones. The great thing about this design is that you can change it up to fit pretty much any shape, size and type of stone. They are a simple classic design that I am excited to share!
Anyone can make these.
Step 1: The Materials:
Sterling Silver Sheet Metal: I chose 22 gauge. This gauge is pretty affordable. There is no need to use thick sheet for these earrings since it's just going to be our base for our bezel.
Fine Silver Bezel: The width of this bezel should be slightly taller than the height of your stones.
Sterling Silver Ear Hooks: These simple findings can be purchased from most any jewelry supply resource.
18 Gauge Round Wire: I chose this thickness because I thought it would be proportionate to the size of my stones. But the size is pretty flexible.
Step 2: The Tools:
Here's a list of the tools needed for this project:
Needle Nose Pliers
Flat Curved Pliers
Sheers
Burnisher
Torch
Flux
Soldering Pick
Soldering Tweezers
Ceramic Block
Charcoal Block
Easy, Medium, and Hard Solder
Flex Shaft
Coarse Silicone Wheel
Bristle Brush Head
Separation discs
High Polish Cotton Polisher Head
Rouge
Copper Tweezers
Jewelers Hammer
Rawhide Hammer
Anvil
Mini Crockpot
Pickle Solution (Epson Salt and Distilled White Vinegar)
Step 3: My Workspace
Since my finances are limited, I don't have a specialized workbench. Instead I purchased a hardwood desk that I could convert into my work space. I wanted to make sure there were lots of drawers for tools, but most importantly, It needed to be able to accommodate a bench pin. As you can see there is a small lip which I attached my bench pin to with a simple vice. I also choose this desk because the roll out keyboard tray works as a great catch for silver dust.
Step 4: Creating Your Bezels
In order to create your bezel, start by wrapping it around your stone. Be careful to try to hug the unique curves of the stone as much as possible. If your having trouble making it tight, you can lightly squeeze it against your stone with pliers. But be careful not to break your stone.
I like to draw a line with marker where the bezel overlaps and cut it with sheers. I am also careful to leave a little extra overlap. Then I very slowly and carefully trim until the bezel is just the right size. Try to leave a little extra room so that the stone slides right in. It may tighten a bit in the soldering process.
Step 5: Cutting Your Sheet
I like to place my stones into their un-soldered bezels in order to determine how much sheet to cut out. Once they are placed, I draw a line with permanent marker and cut out the sheet with my sheers.
Step 6: Shaping Your Wire:
In this design, I am doing somewhat of a figure 8 shape. The loop on the top not only adds to the design, but will also hang from the ear hook, eliminating the need to solder a jump ring.
I like to start with the loop, wrapping the wire around my needle nose pliers. Then I curve the ends in, so that they can meet up with the stone.
There is no right or wrong way to do this. It is all about aesthetic and personal preference. It can be a challenge to make a match, the second time around. That is why I like to start with the loop and finish the ends carefully, while comparing size.
Step 7: Forging Your Wire:
We don't want this infinity detail to just look like bent wire. So for that reason, I like to forge it a little. Creating parts of the wire which are flattened and wider. I decided to forge the ends and the loop itself. You can see in the photo the difference before, and after forging.
Step 8: Final Preperations Before Soldering
Before soldering your earrings, get a few things in order.
I like to use my course silicone wheel to smooth out my wire, and add a fine detailed curve the metal.
Get all your pieces together, and ready.
Now is the time to make sure your bezels have a tight join. Use your pliers to gently make sure the ends are meeting symmetrically, with minimal space between. It's okay to deform your bezel slightly in order to make this join tighter. You can smooth it back out after it soldered.
Step 9: Soldering: Part One
Now its time to solder!
When soldering your bezels, I like to cut a small piece of hard solder, and place it directly underneath the join. Using my brush, I apply flux to the join area. I then heat up the entire bezel, gently with my flame. Too much heat can cause the bezel to buckle and melt. Because it is fine silver, and so thin, it is at risk. Once the bezel has heated up, I maintain my flame above the solder joint. The solder will want to flow towards the heat, so by aiming down at the bezel, the solder is more likely to flow upwards, filling the entire join area.
Once my bezels are soldered, (don't forget to quench everything in water, once you are done soldering) I do a final check that they still fit my stones. I place the stones into them. This will get rid of any deformation that occured earlier. Seeing that the bezels still fit, its now time to attach them to my sheet metal.
I place the bezels down and apply flux to the entire area. I like to cut a few pieces of medium solder and drop them within the bezel, being sure to drop a piece on all sides. The reason I use medium, is so that the solder joint on the bezels will be less likely to flow. We want it to stay intact.
I then apply my flame, moving it in circles, allowing the entire piece to become heated. Once the solder flows, keep your eyes pressed. You should see it flow in a complete circle, adhering the bezel to the sheet uniformly. If it doesn't flow over the entire space, quench it and repeat the process. Apply more medium solder and flux to the areas that didn't solder the first time. Do a test by holding it up to a light source to check for any holes.
Step 10: Trimming the Sheet
Now that everything is soldered, I like to do one final check that the stones still fit. Be careful not to actually push them in, or it may be impossible to get them out again. As a fail-safe you can put dental floss under the stone, so that you can pull it back out.
I just like to lightly place the stone on top. If the stones don't fit, you can adjust this burnishing the bezel from the inside, so that it opens up more. If it still doesn't fit, you can grind away the bezel from the inside with a separating disc, or a silicone wheel. But be aware that this is thinning out your bezel. Expect problems if your bezel is too thin. I;e It will be more likely to melt when heated, it can tear and crack, and polishing it can cause holes to appear.
Now I cut away most of the excess sheet with sheers. You can also saw it away with a jewelers saw. This is still going to leave a rough edge. I grind away more of the edges with my separating discs. Once its reduced to the size I like, I smooth it out with my course silicone wheel. There are many ways to go about doing this, but this is the method that works for me.
Step 11: Soldering Part Two:
Now it's time to solder the wires to the bezels. I squeeze the wires tight so that tension holds each wire to the outside of the bezels.
I apply flux to the ends of the wires and place easy solder on top. I carefully heat the peice, focusing on one solder joint at a time. I watch carefully to ensure that the solder is flowing properly and creates a large meeting point. I want the join to be secure.
After all 4 joins are soldered, I pickle the earrings in order to clean them off.
I don't like using harsh poisons in my home, so I simply fill my crock pot with distilled white vinegar.I wait about 20-30 minutes until the vinegar starts to collect on the inside of the lid. Once that happens, I stir in about 1-2 tablespoons of epson salt until it dissolves.
This is a safe and effective method of cleaning.
Step 12: Setting Your Stones
Now that everything is soldered and cleaned, it's time to set your stones.This can be a challenging process. First, I start with pushing the stones into the bezels ensuring that they are sitting flat.
Once they have been placed into the bezel it's time to burnish. If you have a round or oval stone, this process will be a lot easier. If you have a stone with corners (square, marquise, triangle, rectangular) you will need to take extra care when forming the metal around the corners.
In this case, the stones have soft corners at the top and bottom. In order to help the metal push down more easily, I carefully thin out the bezel around each corner with my handy-dandy coarse silicone wheel. That way the metal is softer and easier to form.
Then, I take my burnisher and push the bezel down around the stone. I always start with the corners, ensuring that they are neat. Once the corners look good, I continue burnishing along the curves of the stone.
Press down hard, but be careful not to bend your wire or harm your jewelry. Use your bench pin to hold your piece in place.
Step 13: Polishing and Finishing
Now its time to finish your pieces!
I use my silicone wheel to clean up and edges that I am not happy with. Many time when I am setting my stones, My bezel winds up getting marked up. Now is the time to smooth everything out. Look at your piece with a critical eye and decide what needs work.
Once you are done finishing the piece, it's time to polish. For those of you who have access to a polishing wheel...great! But I do not. So I use my flex shaft as my polisher. I do this by using a bristle brush head, and a soft cotton polishing head.
Take your bristle head and cover it with green rouge. (I buy rouge in large blocks. You can check step #2 to see what rouge looks like.) I use the bristle brush to get into all the little grooves and hard to reach places.
Tip: For extra fine polish, use Brown Tripoli Buffing Compound on your bristle head before using rouge. This will smooth at any fine rough spots and allow for a finer polish.
Once I have fully polished with the bristle head, I use the cotton polishing buff. Keep covering it with rouge and buffing the entire piece. The idea is to get to a high polish. Just keep at it, and re-applying rouge to your head until you are seeing the finish you want. Keep at it! Your almost done!!
Once your polish is at the level you are seeking, it's time to clean your piece off. If you have access to a ultrasonic, this is the most efficient way to clean all of the polishing compound off of your piece. Otherwise, you can run it under warm water and wipe it off with a moist paper towel. Try to make use of what you have. Not having access to machinery and high end jewelers tools is never an excuse. Find a way to make it work for yourself.
Once the polishing and cleaning are complete, put your earrings onto the ear hooks. This is as simple as opening them up with pliers, and squeezing them shut.
Step 14: Your Done!
Congratulations!!
You are done!
Don't forget this design can work for any and all stone choices. Just adjust the wire proportions in order to have balance with the stones you choose.
If you can make these earrings, you can make many different designs! Just change it up and experiment. I really hope that you like my tutorial. Thanks for reading!
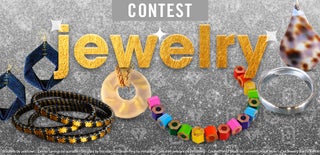
Runner Up in the
Jewelry Contest