Introduction: Dual-Weight Slide Hammer From Scraps
We all know a slide hammer is a great tool to have around the shop. The problem with the commercially made units are that they're expensive and not terribly versatile. I didn't want to buy 3 or 4 hammers for various purposes. So I set out to design a slide hammer that could do both light and heavy jobs, as well as have exchangeable tips so I could build different tools for the end.
Step 1: Gather Up the Pieces
I rummaged through my scrap metal pile and here are the parts I used to create the tool. There is a 1/2 inch smooth rod about 18" long, a large bolt, two nuts that fit on the bolt, a block of steel with a hole drilled through the center, and a large chunk of round stock. Missing are a few nuts and a bolt I use on the rod, you'll see in them in the next step. All pretty random pieces I suppose... not exactly the project you can run down to the hardware store and collect everything, so I do apologize for that. These are all pieces I've picked up along the way, it's more of the idea I wanted to share in this instructable.
Step 2: Weld Up the Parts
Here are the pieces all welded together. I'm not the best welder as far as beauty is concerned, but they're all together. One piece is just the large bolt welded to the heavy chunk of round stock. The square block gets the rod run through the center of it and the two large nuts welded on top. While welding the nuts onto the block I had the bolt threaded through the nuts to ensure alignment. The rod itself gets a welded nut at each end, one to serve as the stop for the slide, and the other is a fine threaded nut that serves as a connector to allow for different tips.
Step 3: Assemble
Here it is all assembled. This is a dual weight slide hammer. So if I need to only use very light force I don't have to screw in the addition of the large bolt and weight.
Step 4: Use It!
Note that the square block can be placed at the end of the stop nut and directly pounded on by a hammer if needed. Since the bolt and weight piece can be threaded in by either direction, threading in from the front of the block allows me to work in areas where space may be at a premium. You can also hammer on the end of the weight when in this position.
On the vise-grip attachment you'll notice a long bolt welded on the frame near the head of the pliers. Other designs I've seen have the fixture welded directly onto the adjusting screw. I didn't want to do that because I don't think hammering on the adjusting screw for the tool is a good idea. The other thing is that I wanted to pull in a straight line with the jaws of the tool. If pulling from the adjusting screw the jaws of the vise-grip pulls at an angle and hence can bend, break, or simply make what you're pulling on hard to pull out.
I hope you've enjoyed this instructable! If you really liked it, please vote for it! Thanks for visiting!
On the vise-grip attachment you'll notice a long bolt welded on the frame near the head of the pliers. Other designs I've seen have the fixture welded directly onto the adjusting screw. I didn't want to do that because I don't think hammering on the adjusting screw for the tool is a good idea. The other thing is that I wanted to pull in a straight line with the jaws of the tool. If pulling from the adjusting screw the jaws of the vise-grip pulls at an angle and hence can bend, break, or simply make what you're pulling on hard to pull out.
I hope you've enjoyed this instructable! If you really liked it, please vote for it! Thanks for visiting!
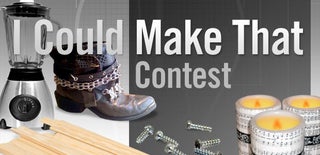
Participated in the
I Could Make That Contest
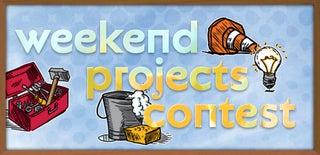
Participated in the
Weekend Projects Contest