Introduction: Step by Step Epoxy River Pour for Beginners
You have probably noticed countless pour videos and finished river tables being coated in oils all over social media lately. After seeing all of those perfect glassy looking colors, you are probably trying to figure out how you too can make your own piece. Epoxy and filling things with it is the way all the cool kids are doing woodworking right now, so who could blame you? I'm going to go through the process step by step as well as share a few tricks and tips to make it a little easier and the results look professional.
If you are already a pro or can't quite get the look your trying for. Scroll to the end (Step 8) to see some helpful Pro Tips.
To Watch the process being done please check out the video above.
Supplies
- Epoxy Resin
- Wood
- Tuck Tape
- Mixing Cup
- Propane Torch or Heat Gun
- Caulking
- Gloves and Mask
Step 1: Epoxy Limits
Epoxy will stick to pretty much anything so the limitations are very few. That being said, most issues come when the surface isn't prepared properly or the curing temperature is not within spec. If you're going to pour on wood, then plane, cut, lightly sand and wipe down all of the pieces before you pour. With all of that done as long as your work surface is dust free, your room temperature is within manufacturers specs and your epoxy is fully mixed you're good to go.
Step 2: Safety First
First thing, be safe always wear a respirator or be in a well ventilated area. Epoxy resin makes a mess so wear gloves and tape off the sides and bottom of the void or spot that you're filling to hold the epoxy where you want it to stay.
Step 3: Build a Form
For large pours or river pours, you will want to contain the epoxy. Build a box to fit the wood you want to pour into. Caulk where the side seems meet the bottom to help prevent any leaks. Once the caulk is dry seal the bottom and sides of the box in sheathing tape, (tuck tape) to keep the epoxy from sticking to the wood (available at any hardware store). Finally make sure the form is level in all directions, to keep the epoxy flat and even.
Step 4: Mix It Up!
Time to get mixing! The resin usually comes in two bottles - one part resin and one part hardener. Mix the two liquids into a measuring cup and stir for as long as directed. Stirring is no easy feat. To properly mix the epoxy, you will have to stir it until your arm feels like it will fall off. The epoxy may even heat up in the process. Add any pigment powders or dyes (acrylic paint works) and stir for another minute. Ensure your project is completely level so the epoxy will sit flat. Pour away making sure to evenly fill the void in 1/4 inch increments until the void is slightly overfilled.
You can do a single pour deeper than 1/4 inch if you use deep pour epoxy. For standard epoxy layer it at 1/4 inch until filled.
Step 5: Heat It Up!
Once poured, the epoxy will have bubbles in it mostly from stirring. These pesky bubbles not only look bad but can float to the top and leave craters in the nice glassy finish. Don't worry. This is where the magic of a propane torch comes in! The torch clears the bubbles quickly giving the large pour a glassy finish.
With the flame about 2 inches away from the surface of the epoxy, move the torch across the epoxy. Make sure to get all the edges and corners. This will pop the bubbles and allow bubbles deeper in the epoxy to rise. Repeat this process every few minutes until all the bubbles are gone or the epoxy begins to gel.
Step 6: Curing the Epoxy
Let the epoxy cure for as long as it needs. Most epoxy will cure overnight but some of the deeper pours could take several days. To get the smoothest finish, you want to extend curing time. Keep the epoxy in a cool (not cold) dust free area while curing.
Step 7: Finishing the Epoxy
To finish the epoxy, you will need to remove the excess from the surface. To do so, sand the epoxy down flat. I work from 80-4000 (80, 150, 180, 220, 400, 1000, 2000 and 4000) grit paper/sponges using the 80 to do most of the removal then working through the other grits until it's polished to glass.
For some pours with large amounts of excess, you can run the epoxy through a planer before sanding to quickly remove the excess.
Once your done planing/sanding, finish the epoxy in whatever finish you want. For cutting boards or anything related to food i recommend just using regular mineral oil. For anything non food related I use a gel polyurethane or hard wax oil.
Step 8: Pro Tips
Trying to get professional finishes takes time but here are a few ways to get the job done quicker.
#1-Use a heat gun to warm the epoxy in the bottles prior to mixing. It not only makes the pour from the bottles easier, but will ensure it's at a proper mixing temperature.
#2-When mixing always use one container. Measuring in separate containers or pouring into another one will change the ratio of the mixture.
#3-Heat the bubbles out of the mixing cup before pouring.The less bubbles you start with the less need removing.
#4-Pour low. It may look cool on your video to do a real long pour, but you're adding air to the epoxy causing more bubbles needing to be removed later.
#5-Fully cured excess epoxy removals can be sped up by using a carbide scraper or a planer prior to sanding.
#6-If you're building a river table, caulk the bottom edges of the box/form to hold in any accidental leaks.
#7- Mix some clear epoxy and using a foam brush, apply it to any wood contacting the epoxy. Allow it to fully cure, it will make less epoxy needed during the pour and help with air from the wood.
#8-If you have a deep void or knot to fill, you can fill the bottom half of it with clear glue or caulk and pour the epoxy on top to save on epoxy costs.
#9-Shine your epoxy like glass, literally. Use Windex to clean the epoxy once finished.
#10- The only way to get the truly crystal clear water like finish is to use a flood coat (pouring a final layer of epoxy over the finished product)
Step 9: Done
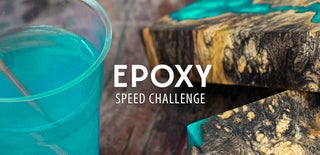
Participated in the
Epoxy Speed Challenge