Introduction: Layered Sheet Metal Snare Drum
I can't pinpoint exactly why, but I really like the look metal and rivets ... it just resonates with me. Two examples which immediately come to mind are the P-51 Mustang Figher and the Airstream trailer.
The P-51 with it's flush mounted panels and rivet lines on either side.
The Airstream with it's overlapping panels and single line of rivets.
I also like the industrial look of metal patchwork. Think industrial, Mad Max, Steampunk, etc. This is the style I used on my Gnome Door.
I like both styles, but metal patchwork is a bit more forgiving. The panels don't need to align perfectly since they are overlapping and fewer rivets are required.
I wanted to see this style on a drum. Correction, I NEEDED to see this style on a drum.
Step 1: Shell Prep and Laying Out for Hardware
Shell Prep
The shell is a 5 1/2" x 14", 9-Ply Magnum shell from Keller. It was part of a full 24" deep tube and cut to the 5 1/2" depth at the same time I was cutting the shell for The Pink Brocade Snare Drum. I use a shop built roller fixture to safely and accurately cut shell stock to size on the table saw. If you're interested in seeing how that works, check out Step 1 of The Zipper Snare Drum.
I use a 80 or 90 tooth Diablo Blade, so the cuts are pretty much finish quality. At most, there are a few tooling marks or burning in places were I briefly paused to reposition my hands while rotating the shell, but those are quickly removed with a sheet of sandpaper on a flat surface. I've seen several builders use a sheet of tempered glass with adhesive backed sandpaper, but I just use a broken feed belt from a drum sander.
Laying Out For Hardware
Since I need to know the location of the lugs, throw off, and butt plate in order to avoid any complications with the layout of the metal patchwork, I laid out and drilled holes for the hardware prior to any finish work.
You could do the layout with math and a seamstress tape, but I use a commercially available layout mat. It has marks for drum diameters up to 28" and gives all the lines the placement of lugs (6, 8, 10, and 12 lug configurations), throw off/butt plate, kick drum spurs, and snare beds.
1. Center the drum on the mat - the concentric rings help with this.
2. On the bottom edge, mark the locations of the lugs (10 in this case), throw off and butt plate.
3. Use a 12" combination square to extend those vertical lines across the shell.
4. I'm using Double Ended Champagne lugs, which have a single, centered mounting point, so the combination square is set to 2 3/4".
5. I wanted the throw off centered on the vertical line and its mounting hole spacing is 1 3/8". I used a seamstress tape to make marks 11/16" above and below the center point. [Picture 6]
6. I wanted the butt plate to be mounted 1 3/4" up from the bottom edge. I used the small combination square to draw that reference line so that it intersected the vertical reference. The mounting hole spacing is 2", so I made marks 1" to the left and right of the vertical center.
Note: I marked right on the drum shell, instead of using masking tape for the layout lines, since it will be covered with metal.
Step 2: Drilling for Hardware
All of the necessary holes could be made with a handheld drill, but I do most of the work using the drill press for accuracy. I made a fixture which fits onto the existing table mount, supports the shell, and prevents blowout ... just remove the table and put it in place. It's constructed from plywood and is basically a channel or cradle for a length of 2x4. Since it's an open channel, the 2x4 length can be whatever you need to support the shell depth in question. The best part is that once the 2x4 is full of holes, you just replace it with a new one.
I start by marking all the hole locations with an awl, which helps guide the bit exactly where I want it. I make a point to only drill holes as large as necessary, in order to eliminate and slop or shifting. Champagne lugs don't have posts like you'd see on a tube lug. The are designed to sit flush on the exterior face and a secured with a single #8-32 bolt.
At the drill press
For the 10 lug holes, I used a 11/16" brad point bit.
For the throw off holes, I used a 13/16" brad point bit.
With the hand drill
If you drill the butt plate holes using the drill press, the screws will not properly thread into the plate, because they will be angled inward. I recommend drilling them by hand ... doing your best to keep the drill level and tracking straight.
I also drill the vent hole by hand, so as not to drill a huge hole in my 2x4 backing block. I use a unibit and drill from both the exterior and interior of the shell until I meet in the middle. It takes extra time, but it's worth it to avoid a catastrophic blowout scenario.
Step 3: Bearing Edges
Bearing edges are cut using my big ass router table. I clamp a straight edge down to the table so that I have two points of contact on the drum shell. I find this gives me more control and the cut is more consistent compared to just running the shell around the bit freehand.
For this drum, I used an offset 45-degree bearing edge. It's also referred to as Standard 45-degree or just 45-degree. Some basic information on bearing edges can be found here. My bit of choice for this edge is a Diablo 45-degree chamfer bit.
On this 9 ply shell, I cut through 2 plies for the outside edge, and 7 plies for the inside edge. You can start with either edge, but I prefer to establish the outside edge and then make the inside counter cut. I'm cautious, so I take several smaller cuts .. raising the bit between each pass until I get my desired edge.
Step 4: Snare Beds and Sanding
Snare beds are made on opposite sides of the bottom edge ... in line with the throw off and butt plate. Some basic information on snare beds can be found here.
There is a commercially available sled for cutting snare bed, but for now I use an orbital sander and a sanding block.
For this drum, I'm trying out a wider snare bed, which spans almost the entire space between the lugs, just to see what happens. I sanded down close to 1/8" in the center with a gradual incline/arc on each side. Final shaping and smoothing was done by hand with 150 grit sandpaper.
I also took this opportunity to sand the bearing edges, interior, and exterior up to 150 grit.
Step 5: Branding and Oiling the Shell
A lot of custom builders use badges, but I don't use them because I want as much of the finish showing as possible. I used a toner transfer method, which I learned from John Heisz. Just print the desired text/image in reverse using a laser printer (ink jet won't work), tape it in place, and make a few passes with acetone on a rag. This instance didn't end up as dark/bold as some of my past attempts, but I'm fine with the ghosted/distressed look.
I like to finish the inside of my drums and bearing edges with 50/50 boiled linseed oil/mineral spirits. My thought process is that it helps seal the drum against humidity, but that could be totally false. Since I'm wrapping this with an unconventional material, I ended up oiling the outside as well. That decision set my timeline back because I had to let the shell dry overnight in order for the adhesive tape to actually stick.
Step 6: Sheet Metal Wrap
For the metal wrap, I'm using thin aluminum flashing, which was left in my house by the previous owners, but I'm sure it's reasonably affordable at the big box stores. I used a quick clamp to hold it down against the table ... instead of having it constantly try to roll up and slash my face.
I measured and marked out a 45" long by 4 3/4" wide section, which provides a 1" overlap at the circumferential seam. The 5" width keeps the metal out of the zone of the bearing edge. I clamped a long straight edge down to the table and scored the aluminum with a sharp razor knife. Go slow, use light pressure, and take multiple passes.Cutting through the aluminum isn't the goal ... just score it enough for a clean break when it's folded back on itself. The edges of the metal are sharp, but I found that a sanding block with 100 grit paper quickly smooths them out and renders them non-fatal.
Initially, I attempted to laminate the aluminum flashing to the plywood shell using contact cement, but it was a failure and a time wasting mess. I was using sections of dowel to separate the layers and trying to align the parts like you would with a laminate counter top, but I couldn't keep the tracking straight. Trying to reposition the metal was near impossible because the contact cement became a stringy mess and I risked kinking the thin aluminum. Thankfully, I was able to undo the attempt and remove all the contact cement, from the metal and wooden surfaces, using acetone.
The second attempt and solution was to use Killer Red Tape, which is an industrial double-sided adhesive tape. It's great stuff, but it's rather expensive - this roll of 1" wide tape was around $22. Five rows around the drum covered the surface and I removed the excess at point of overlap using a sharp razor and combination square.
Before removing any of the plastic backing from the tape, I positioned the aluminum on the shell until I was satisfied with the alignment and locked it in place with several spring clamps towards one end, but the actual tape seam was towards the middle of the sheet metal's length.
My actual adhesion process was more methodical ... because I overthink everything and slow and steady wins the race.
1. Remove the plastic backing to expose a few inches of tape on all five rows.
2. Pull the two leftmost rows out towards the left and pull the two rightmost rows out towards the - so they function as pull tabs.
3. Take the plunge and press the metal against the exposed tape on the shell.
From here on out, we only advance 3-4 inches at a time as we work from this middle point to the end of the sheet.
4. Remove a few inches of the backing from the center row and press the metal in place. This is enough hold to keep the sheet from shifting left or right.
5. Remove the backing from the remaining rows and press the metal in place.
6. Repeat this two step process until you reach the edge.
7. Return to the middle point and repeat the process until you reach the opposite edge.
Note: You can do all five rows in one shot, but I just felt better about having the ability to work out any bubbles/ripples and progressing slowly.
I ran an ink roller around the surface of the shell a few times to ensure solid adhesion.
For the metal overlap, I used a single strip of Killer Red Tape.
Step 7: Extending Hardware Holes
With the aluminum skin in place, I needed to drill out all the hardware locations. The quick and accurate solution was to lay the exterior face of the drum shell on a foam mat, insert the properly sized brad tip bit into the hole, and give it a light tap with a hammer. This left a small piercing, which I could then use as a center guide for the bit while drilling the hole from the exterior face.
Drilling from the outside was the best option because the forward force just pushed the metal against the shell. Drilling from the inside was possible, but the metal would bulge out a bit and I didn't want any deformation or actual separation from the adhesive tape.
Step 8: Sheet Metal Patchwork
I wanted the patchwork to have a random look, but I also needed to ensure there weren't any major conflicts with the drum hardware. The difference between one and two layers of aluminum is negligible, but I wanted to avoid overlaps/seams, as well as any nail heads. It only took a few minutes to install all the hardware and it created a good opportunity to catch any issues prior to final assembly, of which there were none.
Masking tape was haphazardly applied to any area in which I envisioned patchwork, so that I could scribble all over the shell until I was happy with the overall layout. After agonizing over those decisions, I measured all of the panels and compiled them into a cut list.
All of the patches were cut using a speed square and the aforementioned score with a razor knife, then the "bend to break" method. Sharp edges were eradicated with 100 grit sandpaper and Killer Red Tape was applied to the entire back surface. Any excess tape was trimmed off with a razor and you are in effect, left with a tenacious, metal sticker.
One section at a time, I removed the masking tape, removed the plastic backing tape from the metal patch, aligned the patch, and then pressed it against the shell. Once it's pressed down, it's not coming back up without a fight at disfigurement, so take your time. Patches against the bottom or top edge were easy to align with the edge of the base sheet. The few patches, which landed in the center field, were aligned with the aid of a tape measure.
Hand pressure was probably enough for adhesion, but I removed all the hardware and hit everything with the ink roller just to be sure.
Step 9: Faux Rivet Layout and Drilling
Onto the tedious work of adding the look of rivets, which started with laying out all of the nail locations.
I wanted the offset from the edge to be consistent across all of the patchwork, so I used a 5/16" thick piece of scrap wood, aligned flush with each patch edge, and then drew the line directly on the metal with a fine tip Sharpie.
Note: This isn't necessary for any edges which abut the wooden bearing edge. We don't want any nails along that edge, because they may interfere with the fit of the drum head.
The patches don't share a standard dimensional ratio, so I couldn't just space the nail locations by a set distance (dangit). I also had to be mindful of how close to the bearing edge I could actually go, which is why you'll see a reference mark in the second picture of this section. That line represents the bottom edge of the drum head - prior to tensioning, so leave additional space to allow for that.
Any exposed corner was a guaranteed rivet point. For any edge containing an overlap, I took care to make it look visually correct, which mostly meant not having the nail head too close to the overlap. I would then transfer that spacing to the opposite edge for symmetry. Picture 2 & 3 give prime examples of this. Lastly, I used a seamstress tape to equally space 1-2 rivet locations between the corner locations.
Drilling the holes went quicker than expected. I started by lightly punching all the hole locations with an awl, which did an excellent job of guiding the brad point bit exactly where I wanted it to go. This drum shell is 7'16" thick, so I set the drill press depth stop to a boring depth of 1/4".
I'm using 4D nails, so I just grabbed a bit which was large enough for the nail to fit, but not too loose.
Step 10: Cutting Faux Rivets
The shortest 4D nails available at my local store were 1 1/2", which were way too long and would turn this drum into an Iron Maiden - the medieval torture device ... not the metal band.
I used a 1/4" thick piece of scrap to make a quick mark on each nail with a Sharpie and then cut 82+ nails using bolt cutters. The nails ended up being 1/4" or less in length.
To hold the nails in place for eternity, I used 5 minute epoxy. I mixed up enough to do one patchwork section, added a dab of epoxy to each hole using a toothpick, added the nails, and tapped them flush to the shell with a hammer. Notice the sissy grip - no need to go full framing carpenter mode on the nails. This process was repeated 4-5 times, until every hole had a nail.
Note: Prior to adding the nails, I removed all of the layout lines using Acetone - worked like a dream.
Step 11: Finishing the Shell
Initially, I wanted to add some contrast between the shell and chrome hardware by weathering the aluminum. My idea was to use some sort of paint wash to add the look of dirt and grim around the patch edges and nail heads and add visual depth. All of my attempts were futile.
Failed Attempts
Acrylic paint wash totally wiped off when wet and peeled off when dry.
Leather dye wiped off, but left a purple hue.
Spray paint surprisingly totally wiped off when wet and scratched/rubbed off when dry.
Clear topcoat (which I was going to used over the grime) made the metal look dull and plastic-like.
Instragram comments were all in favor of no added weathering - they won by default.
I still didn't like the full on shine of the aluminum and it had a few scratches in it from being stored in the basement, as well as from the hammer taps. I decided to take down the shine and add some texture with sandpaper. I used 150 grit - some diagonal swipes, but mostly circumferential scuffing. A happy byproduct was that this seemingly made the nail heads pop out a bit more.
I gave the exterior a final wipe down with acetone to remove the sanding dust and gunk and then applied a healthy coat of Renaissance wax - both to the exterior and interior of the drum. I let the wax sit up for a few minutes before buffing it out with a cotton towel.
Step 12: Assembly
Final assembly was straightforward, but I was extra excited to see what this drum looked like with all its shiny bits.
1. Lugs are attached using bolts and washers, which go through their respective holes from the inside of the shell.
2. Throw off and butt plate are attached using provided bolts and washers.
Note: I used a small dab our blue thread lock on each bolt.
3. Drum heads are hoops are next. The hoop with the snare gates goes on the bottom ... and the gates are inline withe the snare beds.
4. Hoops are held in place with tension rods, which are just specialty bolts for drums. I add a plastic washer to eliminate metal on metal contact between the lugs and hoop. I also add a dab of lithium grease in the lugs to keep the threading lubricated. I start the tension rods by hand, take up most of the slack with a drill, and then tension/tune by hand.
5. Snares are added last. They are connected to the throw off and butt plate via snare straps, which pass through the gates on the bottom hoop.
Step 13: Glamour Shots
It's metal ... and it's awesome. I had my doubts, but I'm extremely happy with this drum. If I can acquire a magnum shell cut off in an 16" or 18" diameter, I just might make a matching "traveler size" kick drum.
As you can see in Picture 1... even with all my layout planning, I still landed one lug on an overlap. The rubber lug gasket has enough give to make this a non-issue, fortunately.
You may also notice in Picture 7 that I misplaced (lost) a lug stem. I had to order a replacement from Canada.
Common Questions
Don't all the nail holes deaden the sound? No. None of the 82+ nail puncture the shell interior. In fact, they only go halfway into the shell.
Don't all the nails add extra noise? No. They are all firmly locked in place with epoxy.
Doesn't the sheet metal deaden the sound? No more than a plastic wrap would on a commercially available drum.
Why don't you do a proper sound test in the video? In my opinion, that would ruin the momentum, mood, and entertainment value of the video. Also, it's my video, so that's how it is. I am trying to get time in a recording studio, so that I may record all of these drum with a few mics other than the onboard DSLR microphone, which people would also complain sounds terrible
Parts:
Shell: 5 1/2" x 13" Keller maple 9-ply Magnum
Lugs: Champagne aluminum lugs
Hoops: Drum Factory Direct
Throw Off & But Plate: DW 3- position Magswitch
Snares: Puresound brass 20 strand wires
Vent: Drum Factory Direct Tension
Rods: Drum Factory Direct Top Drum
Head: Evan Coated Heavyweight
Bottom Drum Head: Evans Glass 500
Metal: Aluminum flashing
Adhesive: Killer Red Tape
Step 14: The Build Video
Step 15: How Does It Sound?
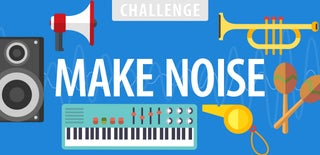
Runner Up in the
Make Noise Challenge
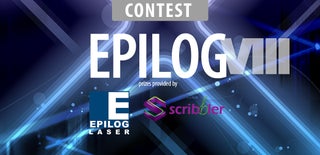
Participated in the
Epilog Contest 8