Introduction: Poplar and Plywood Chess Set
I try to limit myself to two simultaneous projects in the workshop. This is so that when one project is in a glue up or a drying/curing stage during the finishing process, I can work on the other project instead of just waiting around. Once I get above three, I have a difficult time deciding what I should be/want to be working on and that leads to loss of motivation and unfinished projects.
I keep a running list of project ideas and usually just pick the one that interest and/or excites me at the given time. Sometimes (a lot of the time lately) an open contest or challenge will dictate my next project. This project was neither on my list, nor fit the criteria of any contests at the time of initiation ... it was more of a curiosity.
I work a lot with Poplar and Plywood ... because they are relatively cheap and I can get them at the home center right down the street. I personally like the look of plywood on edge and wondered what it would look like as a chess board ... only one way to find out (two if you count Google)
Step 1: The Board - the Plywood Lamination
First things first ... I needed to laminate some plywood so that I'll be able to cut 1 1/2" strips. It was pretty straight forward ... two plywood panels, glue, and an ink roller from the craft store ... add clamps.
I did take the time to ensure the panels were flush/even with each other on one long side, so that I'd have a nice flat edge to reference against the table saw fence.
I'm going with 1 1/2" squares, so I used panels which were 14" in length. That gives me some extra for squaring edges.
Math
1 1/2" x 8 squares = 12"
1/8" saw kerf x 7 cuts = 7/8"
12" x 7/8" = 12 7/8" minimum
Step 2: The Board - Ripping Strips
The thickness of the board was determined by the thickness of the poplar boards, which is approximately 3/4". I used the actual poplar board to set the fence in relation to the blade. Once set, I ripped as many 3/4" strips as possible from the plywood lamination.
Next, I ripped the poplar into strips the same width as the plywood (approx. 1 1/2"). The lamination of 3/4" plywood should give us 1 1/2", but plywood tends to be a bit undersized. As before, I used the actual plywood strip to set the fence.
Step 3: The Board - First Glue Up
The first glue up is easy. Alternate the plywood and poplar strips, stand them on edge, spread the glue, rotate them 90 degrees so they are on face, and clamp them all up.
I used cauls at each edge to help keep all the individual strips on the same plane. My cauls are just plywood strips with clear packing tape on one face ... to keep them from becoming glued to the project.
I wiped up whatever glue squeeze out I could access, but didn't worry about it too much.
Step 4: The Board - First Flattening and Ripping More Strips
Once the glue was dry on this panel, I scraped off any large spots of glue and then ran it through the drum sander to clean it up.
In order to get a straight edge on one side of the panel, I used a large crosscut sled on the table saw.
I had an extra plywood strip, which worked out well because I was able to set the fence to the same 1 1/2" distance I had before. After that, just cut strips until you run out of material (extra never hurts).
Note: I usually try to avoid cutting panels on the table saw which are wider than their overall length, but my large crosscut sled is not 100% dead accurate. It was when I first built it, but wood loves to move when you don't want it to. I did have a brand new 60 tooth combination blade, was mindful of my feed rate, and used the Gripper.
Step 5: The Board - Second Glue Up
The second glue up follows the same basic operations as before. This time just make sure you flip every other strip so that your squares are staggered. This is also a good time to pic which side of each strip is your favorite and play around with grain pattern/color placement.
Stand them all on edge, spread the glue, rotate them 90 degrees so they are on face, and clamp them all up. Again I used cauls on the ends to keep the panel flat.
Step 6: The Board - Poplar Edging
I decided to add edge banding, so while the panel dried, I ripped another section of poplar into 1/4" widths. It was attached with glue and a few pin nails to hold it in place while the glue dried.
You could go with mitered edges, but I decided on simple butt joints. I started with one edge ... leaving the stock long on each side. The next two pieces align flush with these over hangs. After the glue cured a bit, I cut these two edges flush with the panel using the table saw and then attached the last section of banding. I had a few gaps here and there, so I filled them in with glue and sawdust.
Once all the glue was dry, any excess banding was removed using the bandsaw and flush sanded them using the oscillating belt sander.
Step 7: The Board - Second Flattening
To clean up any remaining glue squeeze out reside, flush the banding with the panel, and get the board flat, I ran it through the drum sander. Several light passes on each side did the trick.
If you don't have a drum sander, this could easily be done with an orbital sander. Hand sanding would be miserable and I'm not sure how a hand plane would deal with the plywood.
Step 8: The Board - Epoxy Filling and Sanding
The plywood had some voids, which was unfortunate, but not the end of the world. Since wood filler would be way too obvious, I chose to fill the voids with two part epoxy.
Once it cured, I sanded it flush to the board with an orbital sander. I broke all the sharp edges by hand with 150 grit, and then did a final 220 grit with a sanding block.
Step 9: The Board - Finishing
I finished the board with 50/50 boiled linseed oil/mineral spirits two coats of shellac ... sanding in between coats. The DIY standoffs are made from scrap plywood and drywall screws.
Step 10: The Pieces - Blanks
For the pieces, I wanted to stay with the Poplar and Plywood theme ... and I wanted cuboid as opposed to cylindrical. I had 1/2" and 3/4" plywood on hand and since the board spaces are 1 1/2" square, I went with the 1/2" plywood. Time to rip some strips and laminate some blanks.
For the poplar, I started by cutting a board to a length of 30". From this, I ripped four 1 1/4" strips ... over-sized so they can be trimmed post glue up.
For the poplar, I ripped six 1 1/4" strips. I figured I'd have to cut out any sections with voids and might lose a few pieces to fatal veneer chip out ... so I'd need extra.
I laid all the strips flat, spread glue, aligned them as pairs, and clamped them all up at the same time. Just pay attention to your glue direction, or you'll end up making a cutting board. I cleaned up any squeeze out I could get to and let these sit overnight. I ended up with 2 poplar blanks and 3 plywood blanks.
Once the blanks were dry, I used the table saw to flush the sides of the plywood blanks and bring them close to 1" wide ... then the drum sander to remove any tool marks/blade burning. The poplar blanks took more work since I had laminated 3/4" stock (didn't have 1/2" stock and my planer was broken). I started by flushing up the sides and getting close to 1", but then I had to rotate the blank so that the lamination line was visible from above. This width needed to go from 1 1/2" to 1", but I wanted it symmetrical ... so I need to trim close to 1/4" off of each side. Once that was done, I ran them through the drum sander to get to the 1" blank.
Note: Your blank lengths will depend on how tall you make each piece. Decided on the heights, add them all up, and then add at least 2" for loss to blade kerf.
Step 11: The Pieces - Shaping and Finishing
I used my small parts crosscut sled to cut all the individual pieces. I trimmed one end flush and then used the stop block to get repeatable cuts.
Note: I got less veneer tear out when I had it against the fence ... as opposed to laying against the deck (ply edges facing up).
8 Pawns at 1 3/8"
2 Rooks at 1 1/2"
2 Knights at 1 3/4"
2 Bishops at 2"
1 Queen at 2 1/2"
1 King at 3"
Next I decided on some very basic shaping to differentiate the pieces ... pictures can be seen in the Glamour section.
Using the 90 degrees small parts crosscut sled:
Pawns - I left them as plain cuboids.
Rooks - I cut a line through the X + Y axes ... to form what looks like a plus sign ... or four crenels of a castle tower.
King - I cut a shallow dado around the top on all four sides ... about 1/4" down from the edge.
Using the 45 degrees small parts crosscut sled:
Knight - I cut a single blade kerf slot at an upwards angle. [Separation of horse head and body basically]. I then cut both front and back faces to somewhat round off the head.
Bishop - I cut the front face at a 45 degree angle.
Using the drill press
For the Queen, I just found the center of one end and drilled a 5/8" hole about 1/2" deep using a fortsner bit
I finished all the pieces with 50/50 boiled linseed oil/mineral spirits two coats of shellac ... sanding in between coats.
Step 12: Glamour Shots
Now it's time to play and beat your friends ... or in my case, lose to the one friend who knows how the pieces move, but never has a specific strategy .... it's very frustrating.
One variation I had considered was stenciling letters on the top of each piece instead of shaping them.
P = Pawn, R = Rook, K = Knight, B = Bishop, Q = Queen, Something else = King.
Wood burning could be cool ... and even metal stamps and then filling the recesses in with stain or black paint.
Dimensions:
Board:
Board Strips: 1 1/2" wide x 3/4" thick
Edging: 1/4" wide x 3/4" thick
Overall board: 12.5" 12.5" x 3/4"
Pieces:
Pawn: 1" x 1" x 1 3/8"
Rook: 1" x 1" x 1 1/2"
Knight: 1" x 1" 1 3/4"
Bishop: 1" x 1" x 2"
Queen: 1" x 1" x 2 1/2" [5/8" hole for the top]
King: 1" x 1" x 3"
Step 13: The Build Video
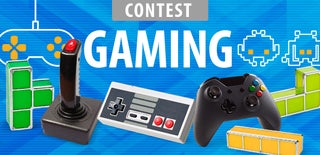
Second Prize in the
Gaming Contest
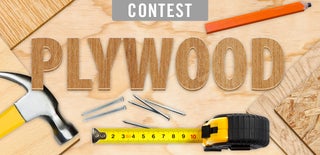
Participated in the
Plywood Contest
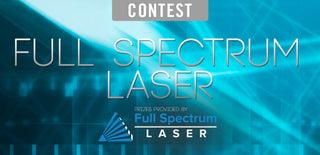
Participated in the
Full Spectrum Laser Contest 2016