Introduction: Poplar and Plywood Plane
I'm not an aviator ... not a frequent flyer ... not particularly fascinated with aeronautics ... and I'm definitely not a bird ... though it would be pretty sweet to be an eagle. Making a wooden plane wasn't anywhere on my long list of desired shop projects and I certainly didn't have a need ... until I heard about the Makers Care fundraiser, which ... you guessed it, involved making a plane.
I didn't just want to make another plane ... I wanted something unique. At the time I perused the Makers Care gallery, there were no seaplanes, so that was a starting point, but it needed something else to set it apart. My first thought ... a moving propeller.
We'll get to the propeller ... first I needed a design via Google images. I found this nice green seaplane and it struck my fancy.
Step 1: The Rough Milling
I decided to make my plane out of reclaimed and scrap wood. Reclaimed pine from a futon frame and poplar off cuts from past projects, which I save.
I ran the pine board through the planer just to clean it up a bit and flatten the faces. The poplar board was planed until its thickness matched that of a drinking straw's diameter ... bear with me on this one.
I ripped the poplar board so that one section was 1" wide ... the remaining width didn't matter at this time.
Lastly, the poplar and two lengths of pine were cut to 10".
Step 2: The Blank Glueup
The blank is just a lamination with the straw in the middle to create a linear cavity free of glue. I knew I'd never be able to drill straight hole 10" in length, but I could turn a lamination into a design feature by using the center as an accent stripe.
1. Slather glue on one section of pine.
2. Secure the 1" width of poplar flush with the bottom using a few pin nails so it doesn't slide around (make sure they aren't in the future path of a blade).
3. Use the straw as a spacer.
4. Secure the wider section of poplar with a few pin nails.
5. Slather the poplar with glue.
6. Add the second section of pine.
7. Apply clamps and wait.
The extra board within the clamps is keeping the boards on the bottom edge flush. It also keeps glue off the bars of my clamps. It has packing tape on its face ... so that it doesn't become part of the blank.
Step 3: The Plane Layout
Most of this project was designed on the fly, but I did start with a profile sketch on graph paper in order to visualize placement of the wings and floats, as well the over all angles and shapes.
Once I was happy with the shape, I transferred the marks to the blank and drew out the profile with various marking tools (speed square, edge marking gauge, combination square, and a ruler).
Basic dimensions listed at the end of my Instructable per usual.
Step 4: Cutting the Plane Shape
Before heading to the bandsaw, I made the angled cuts on the bottom where the floats will attach, which is much easier and safer in block form, as opposed to plane shaped.
The blade was tilted to 45 degrees and I snuck up on the cut until it was wide enough and looked balanced for the 1/4" dowels which will connect the floats.
At the bandsaw, I cut out the profile, taped the block back together with packing tape, and then cut the side tapers.
Step 5: Sanding the Shape
To remove the blade chatter marks and shape the plane body, I used the Oscillating Belt Sander. I did have to use a file and sand paper for the nose and windshield, but that was minimal pain.
Step 6: Fabricating the Floats
With the plane body complete, I moved onto the floats. These are made from a 5/8" poplar dowel and the length was determined by what looked balanced to my eye.
I ran a mark down each down by setting it and a pencil on a flat surface and running the line. I was able to do the same thing on the plane body because my carpenters pencil just happened to land right in the middle of the mitered face. If it wasn't, I would've shimmed it up with paper or cardboard or whatever got the job done.
To get two holes into the dowel on that line, which were also at the same angle, I used the drill press fence to set the distance and a V block to keep the dowel from rolling around. I'd say I drilled about 3/8" deep.
To get the holes in the plane, I used the drill press fence to set the distance and the V block to hold the plane at 45 degrees. Since the miters I made for the floats were at 45 degrees, it sat perfectly flush against the fence. One of those times were my match actually worked out in my favor. I'd say I drilled about 1/2" deep.
Step 7: Fabricating the Wings
The wings were ripped to width at the table saw and cut to length using a small sled. The vertical stabilizer section of the tail wing was cut using the bandsaw and shaped using the. It has a taper and interlocks over the tail wing because I liked the way it looked.
It was at this point I made the decision to connect the wings using dowel instead of just gluing them in place. I marked the middle of the width, as well as marked the middle of the length .. then made a mark at about 1/2" to each side of that length measurement. The last picture in this section will help this make sense.
These holes were drilled using a 1/4" forstner bit. I used the drilled wing to transfer the holes to the plane body .. just lined it up, marked with a pencil, and drilled. Safe deal for the tail wing ... just different measurements.
Lastly, I drilled a 1" diameter hole in the bottom of the plane ... centered side to side and centered between the holes made for connecting the floats. This will be an access hole for the propeller mechanism.
Step 8: Fabricating the Propeller
The propeller blades were made from 1/4" dowel stock. For visual interest, I cut a flat side on each of them using a small cross cut sled and a stop block. This will give them that angled look on the finished project instead of just three round dowels.
The propeller hub was made from 1/2" dowel stock. On one end, three equidistant marks were made around the circumference using a seamstress tape along with some trial and error. These holes were drilled using the V block and a 1/4" forstner bit.
On the other end of the hub, I found the center of the dowel using my shop made guage and drilled another 1/4" hole, which will be for the drive shaft.
Step 9: Wing Supports
The wing supports were a bit tricky and made to fit.
I started by making another set of 45 degree holes in the plane body (one on each side). I eyeballed the location, which ended up being a bit in front of the rear float support. In my head there would be a door on the plane ... so the support couldn't go smack in the middle. The 1/4" holes were drilled using the drill press fence and V block setup.
To get a 45 degree edge on the top of this support ... so that it would mate flatly with the bottom of the wing ... I made a temporary 45 degree fence for the OSS using a speed square, 2x4, and some clamps. It worked surprisingly well.
The angled side of these posts actually fit into 3/8" recesses on the underside of the wing. Trying to drill a perfectly placed and angled hole for the 1/4" was never going to work ... so this was my solution and it works.
The last step was to sneak up on the length using my small parts cross cut sled on the table saw ... trimming the flat end. I would test the fit with the wing in place between each trimming until everything fit without any play.
Step 10: Sanding
Sanding ... you know it's my favorite. Starting with 100 grit paper ... I broke all the edges, chamfered all the dowel ends, and sanded all flat faces. This was followed by 150 and then 220 grit to get everything smooth.
Step 11: Gluing Up the Parts
I've decided ... I might have less love for glueups than I do sanding. Sure sanding can be boring ... but glueups are more stressful with the ticking clock and make more of a mess.
Anyway, as I was making the individual parts for the plane and fitting each piece, I made the decision to not glue everything in place permanently. I personally liked (and still like) the ability to disassemble and reassemble ... kind of like a puzzle. A very simple puzzle admittedly.
You could glue everything up, but here is what I glued up:
1. The tail wing, vertical stabilizer, and 2 short dowels (they will act as assembly pegs basically).
2. Short dowels in the wing (again acting as assembly pegs).
3. Float supports into each float.
4. Propeller blades into the hub.
Step 12: Finishing
All parts were finished with 50/50 boiled linseed oil/mineral spirits, followed by a coat of paste wax and then buffed out.
Step 13: The Spinning Propeller
My over complicated propeller mechanism involved harvesting a fan from a desktop computer and wiring it to a battery, but I've tried that before for costume air conditioning and ended up burning out the motor in record time.
The simple mechanism was going to use a rubber band. However, that wasn't working as planned. They were either too long or too short .. or they were binding and then breaking. Turns out that a hair tie works rather well.
The drive shaft has a very small eye screw threaded into it. I drilled a pilot holes and then threaded this in slowly and carefully. The hair tie gets attached to this eye screw.
To reduce friction between the propeller hub and the nose of the plane, I made a thin washer out of packing tape .. this also worked rather well.
With the help of some thin wire (mine is from a CAT 5 cable), I threaded the hair tie through the internal straw cavity. The back side just loops over a 1/4" dowel peg.
Just wind up the propeller and watch it spin as the hair tie unwinds. It's not spectacular, but it moves.
Step 14: Assembly
Here are some pictures of how all the pieces go together. Again, you could glue everything in place and do that in your desired order.
Step 15: The Display Stand
I felt the plane needed a display stand ... and it need the ability to hold the plane at different angles. I made it out of poplar cut offs, some dowel stock, and a little bit of hardware.
The Base Plate
The base plate gets a hole in the center, but think about that hole in sections of thirds:
1. The top third is 1" diameter for a section of dowel.
2. The bottom third is 3/4" diameter so the bolt head can be recessed.
3. The middle third is 5/16" diameter for the bolt.
The Swiveling Base Section
1. The bottom gets a 1" diameter hole around 1/4" deep. That hole is continued with a 3/4" bit to accept a 5/6" T-nut. You could drill all the way through, but I wanted this T-nut concealed, so I did not. T-nut is secured with epoxy.
2. Both sides are rabbeted at the bottom to accept the bottom section.
2A. One side gets a 1" diameter and a 1/4" T-nut using the same methods as the bottom.
2B. The second side gets a 1" diameter hole 1/3"-1/2" deep. that hole is continued all the way through with a 1/4" bit.
3. The dowel for the base swivel connection is 1" diameter, length cut to fit, and a 5/16" hole drilled through the center.
4. The dowel for the vertical positioning is 1" diameter, length cut to fit, and a 1/4" drilled through the center. This also gets one 3/8" hole in the center anywhere in the rectangular lateral area.
The Post and Plug
1. The post is a 3/8" dowel cut to your desired length (this glues into the lateral hole of the vertical positioning dowel)
2. The plug is a section of 1" dowel (which will lock into the 1" propeller mechanism access hole) inset into a section of 1 1/4" dowel (this acts as a depth stop).
The tightening knob is just a section of 5/8" dowel. It's drilled to accept the 1/4" threaded rod and attached with epoxy.
The only wood parts that I glued were the vertical post assembly and the two sides to the bottom of the swiveling base. Note: Make sure you add the vertical assembly while you are gluing up the swiveling base, but don't get any glue in there.
After writing it up, this sounds quite complicated, but I took a picture of an exploded view to help it make sense.
Assembly
1. 5/16" bolt comes up through the bottom of the base, through the 1" dowel acting as a bearing/axis, and screws into the concealed T-nut. I used some lock tight in this connection. Tighten enough so it rotates freely, but isn't sloppy.
2. The 1/4" tightening knob goes through the open side, through the 1" dowel, and screws into the concealed T-nut. This allows you to lock the vertical position in place so the plane doesn't nose or tail dive into the table.
Step 16: Glamour Shots
Display it ... gift it ... run around the house or yard with it while you make airplane noises .. that's up to you. I have mine displayed when I'm not running around the house making noises.
Plane Dimensions
Body: 10" long x 2 1/4" tall x 2 1/16" wide
Wing: 2 1/8" x 12"
Tail wing: 1 1/6" x 3"
Tail Vertical 2 3/8" tall
Propeller Hub: 1/2" diameter x 5/8" length
Propeller Blades: 1/4" diameter x 2" length
Floats: 5/8" diameter dowel x 6 5/8" length
Wing and float supports: 1/4" diameter dowel x cut to fit
Display Stand Dimensions
Base plate: 3/4" x 5 1/2" x 10 1/4"
Swiveling base sides:
Swiveling base bottom:
Knob: 5/8" diameter dowel x 7/8"
Swivel: 1" diameter dowel
Vertical Post: 3/8" Dowel
Docking plug: 1" dowel inset into a 1 1/4" dowel
1/4" T-Nuts and hardware
Step 17: The Build Video
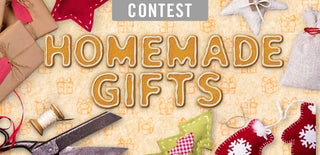
Participated in the
Homemade Gifts Contest 2015