Introduction: Travel Guitar With Loudspeaker Resonator . Model Z10.1
I was given classical guitar with a destroyed bridge.
I could glue this bridge again, but I decided to turn this guitar into a travel guitar. ... But, for me .... It would not be fun if the job is too easy!
So this travel guitar is not an usual travel guitar, as it is possible to see on the internet, with a wooden acoustic table.
The sound comes from a loudspeaker cone resonator.
The principle is the same as the one described in my previous instructables about Z8.1 and Z8.2: the strings vibrate on a bridge wich can move because there is a hinge on one side, and a spring on the other side.
The hinge is there for elasticity, and the spring compensates the pressure of the string set.
Supplies
An old classical guitar.
Two curved bed slats
An ovoid speaker (in my case 96mmx160mm) with a polypropylene membrane (because a travel guitar must stand humidity)
An hinge, a spring, L-shaped aluminum profiles, plastic milk jugs (Plastic = HDPE = PHED = recycling logo N°2), 10 mm plywood, balsa, foam (read text) , screws, wood glue, silicon mastic (brown is better, if you can) ...
Usual wooden tools, hot gun, drilling machine, scroll saw and band saw if possible.
Step 1: Design
On the Z10 model, I choosed to mount the loudspeaker and the mechanical elements from the back in order to improve the mounting process, because it is a bit difficult to mount all components from the front panel , and do the final tune. This was the Z8 models weak point
First of all, on the guitar you have, measure PRECISELY the distance between the neck saddle and the 12th fret. This is the diapason distance. (322,5mm for me).
If you want to keep clean the sound table, protect it with tape.
On the actual acoustic table,
1) draw the center of the loudspeaker at two times the diapason distance (322,5+322,5=645mm for me) . Be precise, otherwise, the final sound will be awfull. It is in this point that the vibrations of the strings sound will be transmitted to saddle, then the bridge, then the cone of the loudspeaker. Note that some guitar makers introduce a linear compensation of this distance: for nylon strings, they add +0mm for E high and +3mm +E low. I did not try. If you do that, please et me know what is the result!
2) draw the place of the loudspeaker centered on the point you measured in 1) on the front panel
3) draw a 1,5cm margin (at least) between the external side of the guitar and the loudspeaker
4) now you can draw the shape of the future paddle travel guitar
Step 2: External Shape Cut
Cut following your drawing. The best is to use a band saw. Hand saw is possible, of course!
If the sound table brakes (like me do), don't panic! you'll glue later the broken sides on the sides (....according to the diapason distance, of course!)
Step 3: Internal Mobile Part Cut & Side Mounting
The principle of this guitar is based on the transfer of the vibrations coming from the bridge wich does not vibrate on the sound table but on the center of a loudspeaker cone, and the vibrations are transmitted using a mobile device, able to move on one side (on a spring) and anchored with a hinge on the other side.
The mobile part must hold the bridge, be strong, be esthetic, open a hole in order to let the sound going out of the loudspeaker hole) . but the most important mechanical constraint is that the saddle of the bridge must be EXACTLY a t the diapason distance (I allready said it , did I? Ha Ha Ha! ). That's why the drawing must be super precise before sawing. I repeat, but it is important, and you have to keep this constraint in mind...
Use as hand scroll saw to saw this part
Then, the bridge will be drilled under the saddle, just in the middle.
Nota: As you can see on the next pictures, I changed later the final shape of te mobile part according to efficency and esthetism during the development. It's a normal process for prototypes. As an example, at the begining I did not want to use an hinge, and use the elasticity of the wood. That's why the mobile part was not cut on the pictures... But the wood was not elastic enough, and the sound of the guitar was stuffted, so that later, I cut completely the part of the acoustic table, and I put an hinge (glue+ screw)
I used curved bed slat (because I had them on my shelf). I sawed inside the sides in order to curve the slats a bit more. But you can use whatever you want. The condition is that these sides are strong, because there is no other way to reinforce the box .
(remember : the length of the sides have an influence ont the diapason length: be precise!)
Step 4: Loudspeaker Modifications
1-Remove the magnet from the speaker (with a screw driver)
2-inside the open hole of the magnetic coil, ajust and stick a thick (15mm hight) and light and rigid washer (balsa, hard foam for example). Then this washer is drilled and a long (M3x15mm) nut (ideally nylon because of the low weight) is fitted and glued with epoxy glue.
Step 5: Mounting Inside Parts
1- the hinge must be glued with epoxy glue and screwed (on the prototype, I did not screw, and the hinge came off, so I screwed later in the project)
2- the loudspeaker must be approximately 1 cm lower than the bottom of the acoustic table to be sure that the cone does not touch the wood. I chose to make and glue ovoid wooden blocks (epoxy) to the shape of the loudspeaker, including the fixing screws, so that the tops of the screws are not visible from the front panel.
3- the springs area. For the prototype, I tried different springs, which did not have the same behavior in compression. This is why you can see 3 locations in the photo that I used for the tests
4 the mobile part:
4.1 glue the bridge (saddle to the length of the tuning fork) on the mobile part (facade side)
4.2 Drill a 3mm hole in the middle of the deck, just under the saddle.
4.3 In the middle of the bridge under the saddle, screw and glue an M3x10 screw (conical head) into an M3 nut 15mm or 20mm long (ideally 20mm long nylon),
4.4 This part needs to be strengthened. Aluminum L-shaped profile bars glued with epoxy glue. In all cases use a light and strong material
Step 6: The Back
To close the sound box, I didn't choose the simplest method, because I wanted to experiment my new plastic reuse technique. This technique consists of making a male plaster mold, and melting plastic HDPE= PHED (recycling logo =Nb 2) layers on it with a hot gun. The first layer is a thick sheet of plastic HDPE coming from a plastic jug, (when melted , this layer gives the global shape of the structure), and the second layer is made with a lot of milk bottle chips (because they are white an black inside , so that when the plastic melts, white and black are artisticly mixed)
1) Making the plywood (Thickness 9 or 10mm) frame (draw according to the external shape of the guitar). The frame should be 2 cm wide
2) Making the plaster mold (male form). on a plywood sheet. The plywood frame should encircle the plaster mold
3) When the plaster mold is dry, screw a plastic sheet ( jug HDPE N°2) on the mold, and melt the plastic sheet with a hot gun pushing the hot plastic onto the mold with a wooden tool . When the plastic sheet is smooth, then screw the plywood frame on it . This first sheet will be the basis of the back.
Be careful! Work outside (because of the fumes). Do not overheat because you will make holes .
Continue to heat slowly, and cover the basic plastic sheet with small melted chips from HDPE milk bottles . Do not unscrew until the mold and the pastic are cold (because if they are hot, the plastic shrinks)
At the end, when you finished filling in all the mistakes and all the holes you made during this process ( you are going to make a lot like I did, it is sure) , you should obtain a strong and rounded box, which fits into the frame.
Then sand, sand, and sand again...
Step 7: Decoration
This is my creation for example.
I used acrilic white paint , a permanent black marker and acrilic varnish.
Step 8: Tuning
Mount a hard nylon strings set (tension=45Kgs), and tune strings in E A D G B E.
The mobile part goes down because of the string pressure.
The mobile part must become horizontal (at the same level than the sound table).
Otherwise, experiment an change the springs in order to get this result.
When the mobile part is horizontal, screw a M3x50 screw + counter nut in the back of the nut in the midlle of the loudspeaker. When the M3 screw is completey screwed, then he cone of the loudspeaker is free of any constraint, and you may screw the counter nut.
Then, adjust the saddle in order to obtain a gap around 2mm between the 12th fret and the strings
and voila!! You may go on the roads and play anywhere!
Step 9: Closing the Body
Screw the back .
In my prototype, I had to add and glue some wooden parts inside the sound box in order to have enough material for screwing
Step 10: Tests
This guitar sounds correctly , and makes harmonics (not so strong than with a usual wooden sound table) but can be used in a philharmonic concert!!! 😉 , but I must admit that nylon strings do not vibrate that clear and strong than metal strings.
... But this paddle travel guitar makes the job : small footprint, insensitive to humidity and plays music!
Examples: These are just unpretentious examples: Be kind to the guitar player!
Natalia : https://youtu.be/KvhjMgIAUHI
Rumba : https://youtu.be/oCIn4YbRYYs
Step 11: Final Thoughts
It seems to be fine
1) to connect a pick up (drill a hole in the box and place a 6,35mm female jack) on an external amplifier, (powered with batteries)
2) to add a guitar strap
3)- to make a travel bag with a pant leg!
4) to do the same guitar with a folk guitar body, with a reinforced neck (with a truss rod) wich can stand metal strings (in this case , diapason linear correction must be +2mm on E hight and +7mm on E low). May be I'll try if I get a broken folk guitar.
Step 12: Conclusion
It took me a long time for making this guitar (about 4 complete working days, without glue drying time), but I am very glad to have this unique world guitar!
I hope you enjoyed .
Send me your realisations! Greetings from France! Bruno...
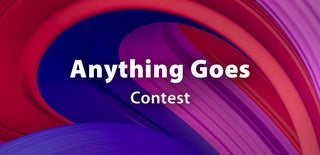
Participated in the
Anything Goes Contest