Introduction: Underwater Window
I had made a big beveled glass window for the youngest daughter, and now the middle daughter wanted one. The previous window design was all straight lines and wasn't very original, so this time I wanted to have lots of curves.
A beveled glass window is heavy and requires lead strips between each piece of glass to hold it in place. The lead strips, called "lead came", are soldered together at the ends. This creates a unified panel which is reasonably strong when held vertically. Held horizontally, the weight would pull it all apart, so during construction it all needs support from a flat work table.
I was able to buy beveled glass in curves so I ordered a good assortment and played with the design. This led to the idea of simulating seaweed with the curved bevels, with wavy clear glass in between for the water.
This Instructable is intended mostly as an overall guide to working with leaded glass (versus the Tiffany method where copper foil is wrapped around glass pieces and covered with solder). It also addresses some of the issues that arise when making a large piece.
Supplies
Beveled glass pieces - various lengths and radii - I can not find my online source. Maybe they're gone.
Flat glass (two kinds: seedy and wavy)
Lead came
Horseshoe Nails (to hold glass temporarily)
Zinc came
Glazing compound (putty)
Whiting powder (for cleaning putty off surfaces)
Solder
Soldering Flux and brush (to get solder to flow nicely where desired)
Soldering Iron
Glass cutter (the kind with oil reservoir)
Glass grinder (very important for getting any kind of precision)
Diagonal cutters (to cut lead)
Fine blade saw (to cut zinc)
Steel angle - 1/2 inch
Steel cut-off saw
Welder (I used stick welder)
Resin paper (comes in big rolls)
Wooden work table
Step 1: Overall Plan
Size
I had heard that the window in question was large. But when I got to her house and measured - OMG. The window opening was about 5 by 6 feet. Too big for any leaded glass window I could imagine handling. Also the thing was very high in the room, requiring ladders just to do the measuring. The solution was to break it into four panels to be held in place with a steel frame. If curves within the design could be made to flow across panels, it would make it look more like a unified structure. So that was the overall plan for the build.
Protection
For the youngest daughter's window, the old window needed replacing. So that's what I did, putting the new one in place and protecting it on the outside with a piece of polycarbonate. But this was a different situation. The existing window had mullions (pieces between the panes) which left in place would distract from my design. But taking out that window seemed beyond the scope of my volunteer effort. I rationalized that leaving it in place would also provide a layer of protection.
Design Constraints
Since it's over an hour's drive away. she and I did a lot of emailing back and forth haggling about the overall design requirements. She didn't want color, and she didn't want a lot of straight lines. So those, plus the dimensions were the constraints.
Step 2: Design
Steel Frame
Early on, I welded together the 1/2 inch steel angle pieces that would support the panels. The center is two pieces, and the bottom, centers, and sides are single pieces, oriented to support and contain the panels. There is no steel needed at the curved top.
Zinc Came
Leaded glass panels are assembled using lead came (Kame) which has a cross section of a capital "I" center which separates glass pieces, and a top and bottom which hold the glass. But for the panel edges, Zinc came is used. It's much stronger and stiffer than lead and forms a rigid structure. After the steel structure, I then assembled the zinc came (Kame) frames that would contain each panel. I did this to ensure that during the build, the glass assembly would not outgrow the steel frame. To bend the top zinc pieces, I went to a stained glass shop and used their bending machine. It's nearly impossible to bend zinc without kinking without a special tool.
Overall Design
I wanted to ensure all four panels were unified in design so I taped together heavy resin paper to be as big as the whole window. The steel and zinc frames on top of the paper then provided the constraints for my design. I used the curved glass pieces to trace some trial designs. There were a lot of false starts but I came up with a drawing that seemed to serve. For the spaces between the beveled glass I used two different kinds of flat glass: One was wavy, and one was "seedy", with tiny bubbles. The final design (called a cartoon) is drawn in Sharpie (fine point), about the right thickness to match the thickness of the lead.
Step 3: Assembly
This is an enjoyable part of the project. You get to see it coming together and the design being realized. I was able to follow the design "pretty well", but in several cases I had to grind the ends of the curved pieces to change the angles slightly. In other cases I had to cut and grind beveled pieces to get them to fit within the zinc boundary at the top. The flat glass was easiest, filling in between the beveled pieces. I tried to stagger use of seedy and wavy to give it some dimension and so there would be a "counter flow" in diagonals crossing the "seaweed".
Piecing
I would start in the lower left corner and work out from there. Per my design it's always flat glass on the sides so that's easy. Hold them in place with horseshoe nails. I use little scraps of came so the nail doesn't push directly on the glass. Then I'd cut a long piece of came to hold all the flat pieces in place. Move the nails to the outside of that, and start fitting the beveled pieces. Short pieces of came separate the curves at their ends. Hold everything in place with nails, then cut another long piece of came. Repeat until done.
Cutting Glass
Cutting flat glass is fun. Figure out how the glass should be oriented to follow the pattern, lay it on the pattern, then trace using the glass cutter, pressing fairly hard. All it does is put a scratch on the glass. Tap under the glass along the scratch and it cracks magically along the scratch (if you're lucky). Luck gets better with practice. Clean up any ragged or oversize edges with the grinder.
Final Fitting
Of course the hardest part is getting it all to fit at the top and the final side. After getting the top to fit, flat glass pieces finish off the sides. They need to be "tucked in" to the came. You can slightly lift the panel and the pieces sag apart temporarily to allow tucking.
Soldering
Then the fun of soldering. When all joints are soldered on one side, the panel needs to be turned over and all joints soldered on the other side. Turning it over requires another piece a wood slid under so it can be lifted, wood moved, then let down without damage. Even after both sides are soldered, they're still very saggy and fragile.
Putty
The next step is putty (glazing compound). The putty is squished by hand (finger) into all the gaps between the came and the glass. Again, you have to use a wooden board to flip the panel over to putty the opposite side. Use whiting powder before the putty stiffens to clean putty off glass surfaces. For the flat glass that has textured surface (the seedy stuff), it's important to clean off the putty before it stiffens up. Later, when the putty has hardened some, the assembly is much stronger, and you can handle it without a supporting board.
Step 4: Installation
I got a lot of help here from my son-in-law and his dad. First we mounted the steel frame, using flat-head screws going through pre-drilled holes into wood. Individual panels were light enough to be lifted into place in the frame.
Late in the game (but before installation) I wondered how the panels would be secured into the steel frames. So to help with this, I welded four 3 inch lips onto the horizontals to hold the panels at the bottoms. The panels could then be balanced on the horizontals while we put screws with big washers into the wooden window frame at tops and sides. Seems to hold fine.
Step 5: Result
I like it. And the daughter and son-in-law like it. The mullions of the existing window don't show much. I made Dory and Nemo as possible add-ons to swim among the seaweed.
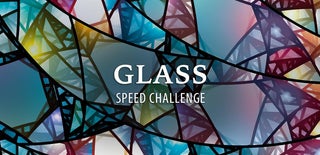
Grand Prize in the
Glass Speed Challenge