Introduction: WarCraft Orc Full Scale Cosplay Costume
Hey everyone SKS Props back again with another complete Halloween costume build!! My big project for this year was to create a full scale Warsong Orc from the RTS game WarCraft 3. I have wanted to build a badass orc for a couple of years now and I figured that this would be the best time to jump in. I started planning the scale and logistics of this build almost a year ago. But because of conventions and orders I was only able to work on it for a few hours here and there.
This build thread is HUGE and extremely pic heave. There are over 200 images documenting this construction of the Orc. Hopefully you can find a trick or two to use in your own builds.
Before we begin let me say some of the products that are used in prop building can be bad for you :(
So be safe!!! Always wear eye protection, wear gloves, and use a respirator when needed.
Lets get started!!!!
Step 1: Reference and Materials
As with all of my prop builds reference material is key. When you start to think about making a prop from a video game, movie, etc. Always try and find as many reference images as you can. These are various screen shots of WarcCraft Orcs throughout out the years. I couldn't decide on just one look so I took ideas from a bunch of different sources and made my own Warsong champion.
The other goal I had in mind for this character was to build something big and awesome while keeping the cost as low as possible.
Above is a pic of all materials and approx costs
Materials:
EVA foam 3", 1/2" and 1/4" http://amzn.to/2nmYrgI
Craft foam 1mm-5mm http://amzn.to/2n9zIfe
Barge Cement http://amzn.to/2nn2ycQ
Loctite Super Glue http://amzn.to/2n8RkqI
Faux Fur http://amzn.to/2o977HH
Fleece http://amzn.to/2o99kCW
Latex http://amzn.to/2n9CNM4
Rubber cement http://amzn.to/2nn3yO8
Smooth on Silicone and Resin http://amzn.to/2o9oCYk http://amzn.to/2o9oCYk
Rattle can Primmer and Colors http://amzn.to/2ns6tH8 http://amzn.to/2ns6tH8
Liquitex Heavy Body Acrylics http://amzn.to/2o9dNFA
Plasti Dip http://amzn.to/2o9iK1h
Upholstery fabric http://amzn.to/2n8DlRS
Painters Tape http://amzn.to/2o9iwaF
Step 2: Scaling This Bad Boy and Framing in the Boots
For my Warcraft Orc I started from the ground up. I figured that if I couldn't stand and walk around ok the rest of the costume wouldn't matter how good it looked. I drew an orc on my wall so I could get a feel for the scale I was wanting.
The main part of the boot is cut out on my band-saw from a of 3" thick block of foam. Like I had mentioned before there is a foam supplier here in Kansas City that sells these awesome scraps to cosplayers. I rimmed the bottom of the block with 1/2" eva from Harbor Freight. This will give me a pretty good shelf for the fake leather to take hold. Using more of the 3" block I cut out a pair of heels that my shoes will be attached to. With the blocks, my shoes, plus the additional sole I will add this will give me a lift of about 10" so far . I used a pair of old Nike shocks because I could secure the straps through the shocks and glue the whole shoe down with Barge cement. By gluing in my Nikes the fit is great and really comfortable. So many of the builds I looked at regarding stilts or risers using wood complained about the weight and lack of comfort. By using all foam the boots weight is minimal and they are extremely comfortable.
Step 3: Skinning the Boots and Mocking Up Armor
After I constructed the foam shell of each boot I had to think about the covering. Here is where I got pretty lucky. I was hanging out with Cullen Cosplay at our local foam supplier and noticed scraps of foam that looked and acted like leather. I inquired as to what it was and was told that when a block of foam comes in the outer layer has to be trimmed off and discarded. I got as much as I could and couldn't believe how great this "junk" foam was. The trimmed off scrap is what I will be using for all soft leather parts (boots, gloves, etc.)
I first skinned the boots in heavy wear areas with 3mm craft foam. Then I made a template out of plastic sheeting that I had lying around and transferred the image to the discarded scrap foam. Using barge cement I started to attach the sides and back to the boot.
Prepping the boot to be skinned I forgot to mention that I reinforced areas on the underside with muslin to keep it from tearing. Like the upper section I patterned the toe guard armor with plastic sheeting and cut it out of 1/2" eva. All of the other boot armor is being mocked up with cheap 1mm craft foam. Straps are cut out of 3mm craft foam and scored using Tandy Leathers leather working tools.
Step 4: Buckels and Straps
Because this is an all freehand custom build I couldn't just go out and buy buckles and rivets. So I took the extra step and sculpted a bunch of bits and pieces out out of Monster Clay. Overall I really wanted a rough hand forged look. I made box molds out of foam core and used Smooth-On's oomoo silicone. I personally hate this stuff but I had some trial kits left over that needed to be used before they went bad.
For my Warcraft Orc I decided to sew a single stitch on the straps rather than a saddle stitch. From a distance I think they individual stitches will show up better since there will be straps all over this build. Individually cut pieces of craft foam were cut and placed on the boots to look like large stitches this will keep with the stylized over the top feel of Warcraft characters.
Step 5: Boot Armor
The Warcraft Orc boots are basically flushed out as far as size and shape. So I'm going to start planning the armor for the top, back and shin. I really want to build all of the armor details at one time so they have a consistent look so this is just the base plates. The top of the foot armor was drawn out on craft foam then transferred to 1/2" eva. I cut it out using my band saw and finished the edges and notches on the back with a Dremel. Once complete it was glued to the boot with Barge cement.
Back of the boot armor was made in the same way as the top. Craft foam was used to make a template then cut out of 1/2" EVA foam. Barge cement was applied to attach the armor plate. Additional straps and details were added to give it a look of functionality.
Step 6: Glove Frames
Once again because there are no pep files or blueprints for this build I am having to size everything based off of the full scale drawing I did on my wall. Like the boots, the hands will have a foam skeleton as the base and will be covered with the foam skin for the leather look. A PVC pipe was cut and installed in the wrist this will be the post I will hold on to. I had to do a little math to scale the back of the hand and start to the fingers
Using a heat gun the skeleton of the hand is heat formed into a fist( a weapon will be placed in the hand later). All of the edges are cut down with a dremel so that when it's covered with the fake leather foam it will appear more natural. I am really getting a grasp of how big this costume is going to be when complete
Step 7: Skinning the Glove
So the hand is primarily an EVA skeleton. I used the same foam skin to cover the hands that was used on the boots. The green craft foam was placed in the fatty parts of the fingers to flesh them out. The hand is positioned int a fist leaving a hole down the center that a future weapon will be placed.
Step 8: Building the Muscles Using Upholstery Foam
Ok what you all have been waiting for the construction of the muscle suit! To start off I took an old long sleeve shirt and installed a zipper down the back for convenience. Then I plotted approx where the muscle groups would be on the duct tape dummy using craft foam. Because their arms are gargantuan to say the least I had to bulk up my arms and shoulders even before muscles were added. One and a half inch upholstery foam was attached to the chest arms and shoulders using 3m 74 spray adhesive. Once it had dried completely I went back in with Barge cement to make sure all of the edges were tacked down really good. I used a Dremel on the upholstery foam to smooth out the bulk. This step was extremely time consuming. I had to go very slow so that it didn't tear the foam. This was also the start to a losing battle with static electricity, the damn foam stuck to everythinggggg!!!!!!!!!!!!!
Once i have the arms bulked out I add an additional layer of upholstery foam on top and begin to build up the actual visible muscles. Just like the first layer this is attached to the foam using 3M 74 spray and Barge cement. I took anatomy in college as part of my art degree and it really helps to not only think about the bulk of the muscle but how the muscle looks when the skin is peeled back.
Continuing to bulk up the suit I add the additional foam to the other side trying to mirror the muscle groups. Again I trimmed off some of the excess foam away with Scissors and Personna blades. Then went to town smoothing everything down with the Dremel
Step 9: Glove Armor and Shoulder Pads
Now I get to spend some time making armor that will cover up half of the muscle suit I just made Ok, so we all know Warcraft shoulder pads. They have to be huge, and they have to have a great look since a large portion of the upper body is the armor. I referenced a couple of orc concepts from Warcraft 3 and World of Warcraft. In the end I decided to combine some of the elements from each and make my own version. The shoulder pads are doubled up foam cut from 1/2"EVA and glued together using Barge cement. The trick to keeping the bend is to already have the top one bent into place and then lay the next layer in you can always cut off the excess. If you glue them together and then try to bend they will want to flatten back out. So I decided that my version will have the shoulder pad and then an additional shoulder guard the will be able to move when I raise my arms. The notch out was made so some big horns can come up from the shoulder guard. 1/2" beveled trim is added to the perimeter of the armor. This was cut down on my band saw and sanded on my belt sander.
Stepping back a little bit to cover the 3 forearm armor plates. These were constructed using 2 sheets of 1/2" eva sandwiched together and cut to shape. The trim was added using the same technique as the shoulder pads. The Horde symbol was freehand cut from 3mm craft foam. I still have the spike molds from my daughters How to Train your Dragon costume so I put them to use again for some additional details. Small spikes were carved from the 3" foam blocks just like the larger ones for the shoulder pads. The right glove with armor is now approx 24" long
Step 10: Orcs Must Have Spikes!!!!
Spikes!!! Orcs have to be big, in my opinion green, and covered in spikes. The shoulder guards were made in the same way as the pads. The spikes were first roughed out of 3" thick foam using my band saw. Then I refined the shape with my belt sander and finally the dremel. I achieved all of the striation and details by using a combination of the dremel on the highest speed possible and a heat gun. All of these spikes created for the shoulder pads are 6" to 8" tall. Best part since they are foam the weight nothing!
The spikes are attached to the shoulder pads with barge cement. After I get all of them glued on I cut craft and 1/2" foam for the base of each spike so that they look like they are attached rather than just stuck on there. Then it's back to casting and gluing hundreds of little fake rivets.
Step 11: Back to Da Boots!!!
The boots (aka alliance stompers) were put on hold a while back so that the majority of the armor could be done at the same time to keep a unified look. I like the way the shoulder pads and arm have turned out so it's time to revisit the boots. The shin guards were constructed in the same was as the arm armor. The only difference being the curve in the design for ankle movement. The knee guards were cut and glue onto the shin guard. I have to leave room for the additional padding and fur at the top of the boot.
Step 12: PVC Skeleton Getting Everything Together to See the Scale
Showing the construction of the PVC skeleton helmet and belt. So to get a scale for the entire costume I built a PVC skeleton out of 1" pipes and connectors. Having the whole costume up helped a bunch when designing the helmet and belt. The skeleton is weighted in the back with a couple of custom made sand bags so he won't tip over.
At this point my Orc has definitely been skipping leg day :)
Step 13: Building the Helmet, Face, and Jaw
So I show you guys a bunch of my pics where the build comes out exactly the way I want. The helmet for this beast gave me problems from the beginning and I want to share some of those steps too. I think it's important that everyone knows it's ok to just scrap an idea no matter how long you worked on it if it's just not coming out right. This helmet goes through several changes before I am finally happy with the end result.
To start off I gathered some tips from Evil Ted on how to build a foam helmet (usually I would hand sculpt and cast it out of resin). But I really want to show people how versatile foam is and how it can really keep the cost of a huge project like this in check. Once I have my template and create the shell I think things are going ok. Problem #1 I had to cut out the middle and resize it because I didn't want a bobble head, I want it to be as snug as possible. All of the seams will be covered with craft foam for a decorative look. The middle strip is glued on to decorate and reinforce the cut.
So for a proof of concept I cut some eva into a rough face and mouth for sizing. The lower jaw and teeth designs were then transferred to the 3" block foam and cut out. I decided to add protruding armor to the front of the helmet this will help conceal the jaw and give me enough room to put the helmet/mask on. I drew a new face on some scrap EVA and did a quick Dremel job on it to get the eyes and nose to show up a little better.
Step 14: Helmet Details and Horns
So here is where I start to lose it and at one point throw the helmet across the shop Luckily it's foam so no damage and I come back to it a little later and fix the issues.
Ok, so I have the base helmet shape and I decide it's time for some horns. Just like the bone spikes on the shoulder pads I go back to my 3" block foam and cut out some basic horn shapes. I am trying to get this done pretty quick again because C2E2 in March 18th and it has to be done by then. I decide I'm just going to put on some generic curved horns. I spend a bunch of time detailing them and attaching them to the helmet. Once I put it on the PVC skeleton next to the shoulder pads I absolutely hate it. I am pissed off at myself for taking the easy way out and wasting a bunch of time. ( This is where the helmet went for a flight ) I go upstairs and cool down for a while.
So here is where I start to lose it and at one point throw the helmet across the shop Luckily it's foam so no damage and I come back to it a little later and fix the issues. Ok, so I have the base helmet shape and I decide it's time for some horns. Just like the bone spikes on the shoulder pads I go back to my 3" block foam and cut out some basic horn shapes. I am trying to get this done pretty quick again because C2E2 in March 18th and it has to be done by then. I decide I'm just going to put on some generic curved horns. I spend a bunch of time detailing them and attaching them to the helmet. Once I put it on the PVC skeleton next to the shoulder pads I absolutely hate it. I am pissed off at myself for taking the easy way out and wasting a bunch of time. ( This is where the helmet went for a flight ) I go upstairs and cool down for a while.
Step 15: The Belt
Decided to post another pic here showing the scale of this beast. To reiterate I'm 5"6" the finished Orc will be 6'7". There are 10" lifts in the boots and a 3" bump in the helmet. To keep everything proportional my hands stop at his wrists.
The construction of his belt. It is pretty straight forward. I patterned it based off of the belt I made for my Destiny hunter. The main parts are cut out of 1/2" EVA floor mats and rounded off with a dremel. The stitch lines and holes were created using a heat tool (remember to war a respirator) Then the pieces were hand stitched, curved with a heat gun, and glued together using Barge cement.
The crest is double layered eva foam and trimmed with the same bevel cut strips that I used on the shoulder pads. The ornamental metal skull is carved from a single block of the same foam I used for the spikes. I had a rough idea of where I wanted to go with it and just went to town with a Dremel. Just like all of the other armor pieces lots of additional details were cut, cast, and added to the sides.
Step 16: Skinning the Muscle Suit
Here is what you all have been waiting for the start to the skinning process of the muscle suit. I will be honest I was pretty nervous through this entire process because I have never done anything close to this before. And if I messed it up now it could ruin the muscles that have already been created.
My inspiration for this technique came to me months ago when I was watching an episode of How It's Made (love that show) I saw a segment on how to build a mascot and figured I could try and replicate the foam and fleece technique but finish it off with a latex coating.
So I have my upholstery foam muscles back on my duct tape dummy. Using 3M 74 spray adhesive I spray a thin line on the outside of the arm and on the green fleece. Once the fleece has been stretched across the arm the seam will be on the inside. Plus all of the cloth will still be covered by latex so you shouldn't even see a seam. Fleece is very stretchy in one direction so I slowly moved around the arm making sure that it go into all of the crevasses to define the muscles. When I had the fleece completely wrapped around I used barge cement to finish off the edges.
The color green was just picked so I could see the muscle groups easier and so that people would understand what I was going for. The color could have been bright pink, my daughters would have loved that. All of this will be covered with latex and repainted to a more desirable green skin color anyway.
The chest was covered in the same fashion as the arms. I sprayed adhesive in the center of the chest and worked my way out. When I go to the edges I trimmed both sides as mush as possible to leave a minimal seam and Barged the excess material down. The back was covered as well I just had to be mindful of the zipper that was installed. Once the armor is on you can see that a lot of the shoulders and forearms will be covered by plates and gloves. A tabard will also be sewn together to cover much of the chest and back. But if I didn't do the muscles right underneath all of this it would still look funny. I am a stickler for correct proportions and details
Step 17: Checking Out the Suit With the Armor
Checking out the Muscle Suit with the Armor
Step 18: Skinning the Face
Now that the upper body has been skinned I can move on to the face. Again the face is just eva foam that has been cut and shaped using a Dremel. The hardest part ( just like the arms and chest ) is to visualize the end product with the skin covering. I will admit the face is not very pretty until the final covering is applied. Just like the arms I know the fleece is the stretchiest side to side so I start gluing at the nose and work my way out. Very slowly I am pushing the cloth into all of those gouges to get folds around the nose, cheeks, and eyes.
After I had the lower jaw matched with the upper I decided to change a couple of things. The large teeth were cut down a little bit and dremeled to points. I added some additional foam to the bottom of the jaw and to the flesh around the large teeth. I also cut the lip and re positioned it up in the gum line. Same principle as the rest of the skin I started in the middle and worked my way out being mindful to keep the glue and material off of the teeth and gums.
Step 19: Bulking Up His Legs and Sewing Some Pants
To bulk the legs up I took an old pair of jeans and drew out basic muscle groups with a marker. Like the arms I cut out rough muscle shapes for the legs and knees and glued them directly to the jeans. (apparently I didn't take pics of the muscles on the back of the legs but they were made too) These muscles were refined with a dremel until smooth. They don't need to be perfect since they to will be covered with cloth. I made a pattern out of scrap cloth and transferred that to the suede material. Everything was sewn together then slipped over the jeans and muscle groups. Once I got the correct fit I sewed the outer layer to the jeans.
No more skipped leg day jokes for this guy!
Step 20: Test Fitting the Suit
These pics so here are the very first shots of me actually wearing all of the major pieces together. These shots helped me figure out any issues and what I need to work on. I really wish that I had put something in the foreground for scale because it just looks like a regular sized costume. But remember that my hands stop at his wrists and my feet stop at the top of the foot.
Step 21: Texturing the Fleece
Honestly I was nervous to attempt these next couple of steps. I have never used latex before and wasn't really sure how the suit would look in the end. But I also knew that this skin would make or break the look of the Orc. Without the realistic latex skin he just looks like a WOW high school mascot and for me personally that just wasn't going to do.
So, to start I took some of the fleece and tested the effects of different materials before I went to town on the muscle suit..The biggest problem with the latex is that the fleece will soak it up and you will have one hot and heavy skin. So while researching I came across videos from Stan Winston by Ted Haines showing him create a huge T-Rex head out of foam. Later in the steps to seal the foam he coated it with 3m 74 spray adhesive before he applied the latex. I thought that the principle would transfer over to the cloth and luckily I was right. So first step was to coat the entire muscle suit and face with spray adhesive. Be very careful no to let any of the parts touch each other because it is a really strong contact adhesive and you will probably have to rip it apart and do that section over. This spray is also pretty expensive (about $20-25 per can)
Once everything had dried enough so that it was tacky to the touch I began to apply the latex. I used just regular mask latex from monster makers. Because I wanted it to look like skin all of the latex was hand applied. This look was achieved by dipping some of my leftover upholstery foam into the latex and stippling it on to the suit/face. This process was time consuming but the results were worth the added effort. I could have tried to spray it on but I was worried that the mist would be to fine and I wouldn't get the correct texture at least for my Orc. For more normal skin a spray gun would probably be the best way to go.
So I applied a couple layers of latex just right out of the tub no additional colors or tints were added at this time. Tomorrow I will show how I tinted the latex to get a base color for the suit.
Step 22: Tinting the Latex
Day 2 of the latex was more about building up a couple more layers and tinting the latex for paint. I work at Lowe's a couple hours a week in the paint department and was lucky enough to buy a little bit of tint that we use for our mixers. When we pour the tint into the hopper there is always a sludge leftover in the bottom of the container that we toss. I talked with management and purchased one of the used containers which had just enough tint in the bottom to color the latex for the entire suit ( a little bit goes a long way ) This step also helped me figure our spots that were thin in the original application since I'm going with a new color now. There are people that paint from light to dark but I prefer to paint dark to light. So that is why this base coat layer is a really dark brown, but he will end up being green.
The veins are one of the simplest tricks in the book. I cut some thick string to length and dipped it in the latex. doubled it up on the bicep and then it splits at the forearm. After a couple more layers it will take away some of the harshness and round everything out. Ta Da! instant veins
Throughout all of this I am still hand applying the latex to keep the skin texture consistent. After everything had dried, I reassembled all of the armor on him to make sure everything lined up the way is was supposed to.
Step 23: Rubber Cement Paint
The suit is based out in the dark brown latex and everything has dried so now it's time to give this guy some color. I used a rubber cement paint technique because I read how durable the final product is. It is basically rubber cement, oil paint, and Naphtha as the thinner. From what I could find out Naphtha is getting harder to find in the states and has been banned in places like California. But here in the midwest we actually still buy it at Lowe's.
First step is to brush on a coat of thinned down rubber cement and Naphtha to prep the surface. This stuff smells absolutely terrible make sure to wear a respirator. Because anything that smells this god awful has to be horrible for your body. You will notice that the Naphtha will pucker the latex this will go back down over time once it evaporates off of the surface. Using the same mason jar of rubber cement mix I added permanent green light oil paint to tint. I started brushing on the mixture with a 2" chip brush but because of the thickness and it's ability to setup over time switched over to a gravity fed air gun (not an airbrush the mix is to thick) Then it was just a process of layering and building up colors. In the end I had 4 different mason jars will with different hues that I applied to the orc to give him some variations in the skin.
Step 24: Final Skin Pics
Here are the final pictures of the completed skin. You can see that from the previous post I went back and gave it an olive hue over most of the surface. Additional visual details were made by hard pressing the trigger on the air gun to give the skin a blotted or sometimes splattered variation. With that much surface area it helped break up the monotony and give the skin more of a realistic appearance.
In truth that was the very first time I had ever used an airbrush or airgun and I was more than happy with the end results.
Once the job was complete I sealed the skin with another layer of just the clear rubber cement and Naphtha mix. This time I didn't thin it down as much so there would be more of a barrier.
Again the stomach and back are not finished because he will have tabard that will be covering most of that surface area. I figured that having these areas not covered with latex (since they will never be seen) should help a little bit with the heat
You will notice a pretty heavy sheen that the rubber cement gives off and there is a little tack to the surface. I talked with Ted Haines from Legacy Effects and he recommended that i use transparent makeup powder to dull it and get rid of the tack. I did that a little later on so the gloss you see here was taken down a bit.
Step 25: The Shield
My warrior grunt Orc is going to have an axe and shield ready to deal damage. The shield is carved from a single block of 3" thick foam and is approx 22x28". The final product was to make it look like 3 stacks of metal were bolted together with a wood insert. All of the carving was done with a Dremel and a sanding drum. Additional 3mm and 5mm craft foam and resin cast rivets were added for details. I teased some info about my Orc's clan with a pic of his axe on my Facebook page. But here I am definitely showing he is a member of the ruthless and bloodthirsty Warsong clan. They are recognized on the battle field with their grinning skull emblems. The skull face was cut out of 5mm craft foam and fake rivets were placed on the individual pieces. Again everything was battle damaged using the same Dremel.
Now that the form is built I had to think about how the shield would
attach to the forearm. I really wanted everything to look like it had a purpose so I drew up a way to have chains loop over the arm to secure it to the shield. I took some 5mm craft foam to simulate leather straps and added more D rings. It may not look like much here but I will say the final version with the chains wrapped around his arm looks amazing.
Step 26: The War Axe
The blade and body of the axe are both cut out of the 3" block foam. The blade was cut on the band saw and contoured on the belt sander. To keep the weight down I used a cardboard fabric tube from Joann's and wrapped that with 5mm craft foam to bulk it up. The spike on the back of the axe where my wife is holding it was just tacked on for scale it was later replaced by a piece that suited the look better. I built a small box out of craft foam and lined the back of it with white card stock. This box will house 6 red leds per side. The grinning skull was freehand cut from the same craft foam and it will be backed with a sheet of plexi glass. The plexi glass was sanded on the back to diffuse the glow of he leds. Additional craft foam, resin cast rivets, and chains were added to the handle for more detail.
Step 27: Battle Damage and Plasti Dip
Large spikes are cut from the block foam and small white spikes are all resin cast. Battle damage was made using various bits on the Dremel at high speed to cauterize the cuts. This keeps the foam cells from being to open and the paint texture not matching later on. Once done everything was hit with a heat gun and Plasti Dip was used to seal the foam. I prefer to coat the foam in 2-3 thin layers so that #1 it doesn't cover up details and #2 it doesn't run and look sloppy.
Once all of the armor is distressed with various Dremel bits. All of the pieces are gone over with a heat gun to close the cells. Then I spend a bunch of time pulling all of the little foam burned bits out of cuts and gouges. Lucky for me it was a crazy warm February and March so everything could be prepped outside instead of in my shop. All of the parts were laid out and base coated with very thin layers of Plasti Dip. To cover all of the parts with 2-3 thin layers took approx 3 cans. Everything was left to try for 24 hours before I started the next phase. The final pic shows the progression of the build last showcasing all of the armor along with his axe and shield.
Step 28: Painting Process - Spray Paint
Here is where the fun begins. This is a helpful trick that I do on almost all of my builds. I take a pic of the costume while the armor is still raw and photoshop approx base colors over it. This helps me decide what direction I wan to go with fur color, armor distressing etc. So the first pic shows one of my early shots in the Orc, next to a Photoshopped color scheme, and then the final product.
Before any of the colors went down I sprayed everything with Valspar black primer. To base out the colors on the orc I used Valspar Color Radiance Flat in 2 different shades of red for the armor. (They don't have names on them just the tops to show the color inside) I used Krylon Hammered Silver for the Trim and Krylon Red Oxide Primer for the horns and leather. I was going to tape off everything then saw how long that was going to take and decided not to. I sprayed in the general areas but wasn't concerned with over-spray since the real details would all be hand painted. Once everything had dried completely I took it all inside to begin the time consuming task of hand painting using Liquitex Heavy Body Acrylics.
Step 29: Painting Process - Hand Painting Armor
All of the armor is now plasti coated, primed, and had a base layer of spray paint. From here I black wash all of the armor using a mop brush and Liquitex Heavy Body acrylics ( Mars Black ). A wash is just like it sounds, you load up the brush with a bunch of paint and water and scrub it all of the surface. Then before it dries take a paper towel, rag etc. and wipe off the excess. This lets paint seep down into the details you have created and weathers the armor. At this point I am not concerned about the leather or the horns I am just focusing on the metal parts. After everything has had a chance to dry I start the long process of hand painting all of the red accents. The first layer is Liquitex heavy body Cadmium Red medium Hue and Cadmium Orange Hue. The red and orange play off each other and give the color more depth. Then that is highlighted with Cadmium Red medium ( not the hue ). The hue version of all the Liquitex paints is more transparent and doesn't seem to have as much pigment, which is fine for a first base coat. The Cadmium Red is really makes the armor pop and a little bit goes a long way. You can see from some of the close up shots I want to leave a bunch of the original wash showing through to give the armor a dirty grimy / gritty look.
Step 30: Painting Process - Hand Painting Leather
To paint the foam to look like leather takes a little more skill than the armor, the multiple layers are key to giving the foam depth. First I spray Rustoleum dark brown camo to break up the monotony of the rust red. Then I apply multiple layers of black washes. Some I put on extremely wet to simulate the weathering and dying as if it was leather. Then I add more pigment behind straps, around the stitches, and in the folds. The final pic shows a before and after with the black wash application.
Now that all of he black washes have dried its time to start adding some color. This step is the hardest to look believable and will take a ton of practice. I use multiple colors in various drybrushing steps to get the desired look.
Here are the Liquitex Heavy Body acrylics I use and pretty much the order in which I use them : Burnt Sienna, Burnt Umber, Raw Sienna, Indian Yellow, Cadmium Yellow Deep and Hue The Cadmium Red and Hue and applied as a wash over certain straps just so everything doesn't look to uniform. You basically just have to judge where you want the highlights and where the "leather" would get the most wear.
Step 31: Painting Process - the Shield and Belt
The shield had a wood texture scribbled into the foam using a dremel and I really want to accent that with the paint job. It is easy when using similar colors to make everything look muddy. The way to alter this is simply by practicing how the paint in applied. Depending on how you drybrush it can drastically make the finished product appear to be a different material. Just like the leather first thing is to black wash the entire piece. Then using Raw Sienna, Indian Yellow, and Unbleached Titanium I drybrush the wood surface of the shield. The laughing skull and metal trim are painted black and highlighted with a mixture of Liquitex Rich Silver and Bright Silver. The same technique is also applied to the skull on his belt.
Step 32: Adding Fur
I will be honest nothing pissed me off more than the combination of spray adhesive, Barge cement, and fake fur. I swear there were random threads sticking to everything!!! But the end result looks pretty cool so I guess it was worth it Before the fur was added I glued some more of the upholstery foam on the bottom of the shoulder pads to lift them up and out. For the fur trim I got some fake camel fur off of Amazon with a descent length and neutral color. Cutting from the back with some leather sheers minimized the amount of fur lost at the cut line. The fur was then doubled over and glued together using the 3m 74 spray adhesive. Once that had dried the strips were glued onto the shoulder pads and gloves with Barge cement
Step 33: Orc Teeth
To bring this Warcraft Orc cosplay to life I know that the face would have to look pretty cool. So I spent some extra time making sure that the teeth looked awesome. The teeth were painted with Liquitex acrylics ( Raw Sienna, Indian Yellow, Unbleached Titanium, and Parchment ) But the real trick was coating them with 5 minute epoxy. This gives the teeth and lips a gloss appearance that really stands out right next to the skin. The nose and tooth rings were sculpted out of Apoxi Sculpt and painted with Rich and Bright Silver along with a little silver Rub and Buff.
Step 34: Finishing the Axe
The axe surface is heat treated and coated with plasti dip just like the rest of the armor. Once it had sufficient time to dry I sprayed on some Rustoleum Dark Silver and mixed in some Brushed Nickel. The face plates were kept separate until the painting was competed since leds would be shinning through the cutouts. I wasn't concerned about making the handle looking to pretty since it would be covered by his hand anyway.
Very thin plexi glass was sanded on the back to diffuse the light of the leds and glued onto the face plates. Once the plates were attached I black washed all of the metal with Liquitex Mars Black. Then highlights were applied to the surface using Liquitex Rich and Bright Silver. The rust color was achieved using Liquitex Raw Sienna and dry brushed over strategic places. Some scrap fur was added to the top and handle for authenticity and to cover up the seams. Then like a giant action figure I slide the axe into his hand and turned on the lights.
Step 35: The Tabard and Shoulder Pad Straps
I really wanted a fabric that looked like it had some weight to it. I purchased some high end upholstery fabric from Joann's ( always bring your coupons and get their app to double dip ) I patterned it by using the draping method and did a rough cut out with scissors. I sewed the 2 halves together at the shoulders with a machine. All of the fake stitching is cosmetic and was achieved by dying some cotton thread in an acrylic bath to get rid of the stark white. To get that battle worn look I spent some time distressing the fabric on my belt sander and rubbing the whole thing on my grass (no joke)
The shoulder straps gave me quite a time because I was trying to over think them. I was envisioning ways where they clip onto the muscle suit, have elastic running in front and back, etc. Then it came to me what if they were strapped like they were real (light bulb) So I designed a 4 way strap the hooks into the front of each pad and crosses in the back. The center ring for the straps was sculpted out of apoxi sculpt. The straps themselves are multiple layers of foam cut into strips and glued together with Barge cement.
Step 36: Final Test Fit
This was the first time all of the pieces came together in their completed forms. The test fit was primarily to see if I had any issues with the armor catching on other pieces and to make sure that everything stayed in place when walking.
I really like these behind the scenes shots though because it shows what went into making it and the scale.
Here is a movement test video I put up on YouTube
Step 37: Glamour Shots
Final shots of this beast!!!
I hope that you all have enjoyed this build and for more of my creations check out
https://www.facebook.com/StevenKSmithProps/
and my prop shop can be found here
https://www.etsy.com/shop/SKSProps
Twitter and Instagram - @SKSProps
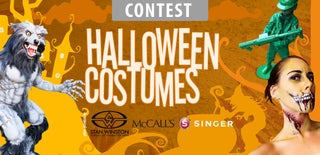
Grand Prize in the
Halloween Costume Contest 2016