Introduction: 3D Printed Replacement Handles for a Vintage Pot.
You’re probably asking, “Why wouldn’t you just throw that old pot away and buy a new one?”. Well, this pot belongs to my mom and she has some highly sentimental feelings about it. This pot is from the first set my dad bought for them when they were married in 1961. Of course, back then, things were built to a higher quality too.
Another noteworthy point is that this isn’t the first repair that has been made to this pot. I remember back in the 1970’s, my mom sat the pot on a hot burner and there must have been some water on the bottom of the pot. It caused the water to instantly boil and pop a small hole in the bottom. My dad took the pot and had the spot filled with a TIG weld and buffed out.
Over the years, the handles have loosened and cracked, but my mom still insists on using it. My mom sent some food over to us in this pot, so I decided that this is a good time to use my 3D Printer to make replacement handles for her before I returned it.
Step 1: Materials and Tools Needed...
PLA Filament - I used 1.75mm Hatchbox Black
New Stainless-Steel Screws
Tape Measure or Dial Calipers
Pocket Knife
3D printer – Mine is a Creality Ender 3 Pro
Step 2: Disassembly…
I began by removing the screws from the handles. I was surprised on how corroded the screws were. No wonder the handles kept coming loose, cracked, and failed! The connection point on the pot still looks to be in good condition as does the threaded area. So, it looks like I need to make the handles and purchase a couple of new stainless steel screws.
Step 3: Collecting Measurements…
Since this wasn’t an exact restoration, I just wanted to make a set of similar type handles that functioned as well as the originals. I began by taking the basic measurements from the handle in the best condition. This handle was 2.5” wide where it touches the pot, 2.25” wide at the outer edge, 2.5” tall, and .75” thick. The screw head needed a recess a little over 5/16” (.312) in diameter and ¼” (.25) deep. The threaded portion of the screw is just under 3/16” (.187) in diameter. The pan area that the handle attaches to is about 9-1/4” in diameter.
Step 4: Time to Draw the Handle…
I used Tinkercad to draw the handles. I find that this program is simple and the easiest for beginners creating 3D drawings. I could have used Fusion 360, but for this project I stuck to the basics. I found a Trapezoid in the Shape Generator and after adjusting the dimensions, used it for the handle shape. I used a second trapezoid shape (in “Hole” mode) to form the hollow area of the handle to clear the pot mounting bracket. I then added the screw pocket (also in “Hole” mode) and the curved area that mounts to the pan. The last thing I drew was the grip area under the handle. To do this, I took a cylinder in the Basic Shapes and added three Torus rings to it on the top, bottom, and center. I then combined these parts and made them as a negative space or “Hole” in the shape generator. By turning it sideways and partially pushing it into the side of the handle, then combining the parts, it creates the recessed pattern. I then exported the drawing to my desktop as an .stl file.
The second photo is of the basic individual drawn parts before I combined them to create the finished handle shape. I thought that it would help someone that needed to visualize the process.
Step 5: Converting the File to G Code…
Again, I have used several different slicing programs to generate G Code but decided to use the Creality Slicer that came with my Ender 3 for simplicity.
The main things I set were…
Nozzle Temperature – 200 C
Bed Temperature – 60 C
Wall Thickness – 2 mm
Fill Density – 20%
Print Speed – 80
Layer Height - .10
Support Type – Touching Buildplate
Build Plate – Raft
I then generated the G Code File. It calculated that it would take a little over 3 hours for each to print.
Step 6: Let’s Get Printing! …
I turned on the printer and loaded the file. After the warm up, we were printing! It still amazes me that you can print a usable replacement part at home.
Step 7: Clean Up the Printed Handle...
Once the part was finished printing, I removed it from the print bed, peeled off the raft, and cleaned out the support fill – all done with a pocket knife. I must say that I’m happy with the quality of the finish. I then printed a second handle to make a matching pair.
Step 8: Final Clean Up and Re-Assembly…
Before I install the new handles, lets clean up this pot a little. While it’s not dirty, it sure could use a little help on the copper bottom. Let’s see if we can get it back to looking more attractive. I found that 00000 steel wool with vinegar and salt cleaned it up quickly. It took me about 3 minutes to fully polish up the copper bottom. It sure looks nice now!
Now, re-install the handles with the new screws. What a difference! That should add even more life to a pot that’s 59 years old. I decided to give it a test lift by filling the pan with water, grabbing it by the handles and giving it a couple shakes to check the strength... it Passed! It feels extremely solid again.
I’m glad that I took the time to do this for my mom and I’m sure she is going to be very happy to have her pot back in good working condition again. It looks like this pot will eventually become a great family heirloom!
I wrote this Instructable to hopefully inspire you to look around the house for things that are damaged or not working up to par and making the necessary repairs rather than tossing and replacing. It will give you a sense of pride every time you use it AND it could keep some extra money in your pocket!
Just a note… I used PLA filament when making these handles since my mom doesn’t use a dishwasher. If the PLA doesn’t hold up well, I’ll just reprint them with ABS. It wouldn’t take long since I already have the drawing file made.
Follow Up... It's been a couple of weeks since I made these handles and my mom hasn't had any issues with them. They have stayed tight without any issues. It appears that PLA is more durable than I gave it credit for. In another experiment on a project I worked on last weekend, I tried out PETG filament. I think this may be the best material to use in this case since it is more flexible yet strong with a high melt temperature.
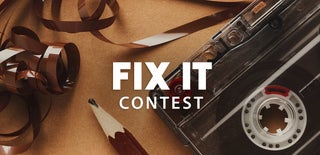
Participated in the
Fix It Contest