Introduction: Coffee Table
Some college friends of mine live in an off-campus house and have a living room full of “were-broke-college-kids-and-don’t-have-a lot-of-money” furniture. They came to me and decided that it was time to add some style to their house. They wanted to start with a new coffee table. The one they had was from a garage sale, and definitely looked the part. I had an abundant supply of 70-year-old, oak fence wood that I offered up for the new table. I showed them some designs similar to pallet-esque tables I’d seen previously, and I eventually came up with the design we built.
Step 1: The Design
I’d seen all of these pallets-turned-tables and thought the look they had was killer. The downside was that it didn’t provide a lot of space for drinks or anything else because of the large gaps in the tabletop. The “clients” and I ultimately decided that we needed to close all of the gaps in the top. The rest of the table was to somewhat match these tables; such as the open boarded sides and three table legs per side. They liked how the wood looked naturally, which saved me tons of time in the long run (I only had to sand one small board to show them the difference, and none of the stains the liked).
Step 2: The Pre-Work
I pulled down around 15-20 12’ boards from the fence to ensure that I had enough “good-sections” that could be used for the top and sides of the table without having too many knot holes, cracks, or slashed edges. I also brought down 4 4’ posts for the table legs.
I cut all of the boards down to 54” for the top and sides. I ripped all of the boards on both sides so they would have a flat edge, which allowed for easier biscuits and a cleaner look.
Attachments
Step 3: The Work Part 1
The top of the table was 8 boards of approx. 42” wide (5 1/4” board width) and 54” length. I used about 4 or 5 biscuits to join each pair of boards together, being sure to lay them out before cutting the holes as to line up the biscuits appropriately and also to not cut the top or bottom. I glued up two boards together at a time, and then went in halves until all 8 were together. Once the top was glued, I left it clamped for several hours (4-6).
The legs were all cut to 20” and mounted to the under support using two or three L/Corner brackets and 1 ¼” screws. I made sure to mount the brackets in the middle of the post as to not cause any bending when the table had weight on it.
The two shorter sides of the table had two boards (42”) separated 3 ¼” apart and secured to two posts. The longer two sides had boards secured to all three legs, but on the inside. I did this to keep half of the table open so people could put their legs underneath it when sitting on the couch or the floor. These two boards were mainly to keep all the table legs straight, secure, and added loads of support overall.
Step 4: The Work Part 2
I added the under support by making an outline of the table plus a middle board support. I used 1 1/4” screws and countersunk them so the heads were hidden and to pull the boards together better.
Attachments
Step 5: The Work Part 3
The legs were all cut to 20” and mounted to the under support using two or three L/Corner brackets and 1 ¼” screws. I made sure to mount the brackets in the middle of the post as to not cause any bending when the table had weight on it.
The two shorter sides of the table had two boards (42”) separated 3 ¼” apart and secured to two posts. The longer two sides had boards secured to all three legs, but on the inside. I did this to keep half of the table open so people could put their legs underneath it when sitting on the couch or the floor. These two boards were mainly to keep all the table legs straight, secure, and added loads of support overall.
Step 6: The Pre-Finish
Now the table was built and standing, it needed to look good before I delivered it. Since this was 70 year old wood, I figured it wouldn’t hurt to reseal it. I used sanding sealer, which livened up the wood significantly, and also protected the wood. Any edge that I had ripped I stained with a “Red Mahogany” stain, but not after smoothing them over with a belt sander. This little amount of stain gave a very nice contrast to the gray of the wood and overall made the table look even better.
The clients and I decided that if we were going to leave the top of the table natural and raw, that it would need some sort of covering so it wouldn’t be so rough. I found an epoxy that would do the trick, but the table had to many holes and cracks and the epoxy would just run through. I used clear silicone to seal several knots, some small gaps, and two parts on the edge where a big knot gap had been exposed. The sealer also helped, as the wood was very dry and soaked up an immense amount of anything I put on it.
Step 7: The Finish
Once the top of the table would hold liquids, I went around the edge and made a blue tape wall to hold the epoxy on top of the table. My dad and I mixed the whole batch and once and both poured. Once we poured we took the same stain for the edges and dabbed over the silicone that was supposed to be clear (but was white) and got it to darken up almost to the same color as the table. Although it was supposed to cover 4 ½ sq. ft at 1/8”, some of the boards had knots that were taller, and so the epoxy covered about 90%, with a few knots being above the epoxy line. This turned into a happy accident though after it all dried, giving a very cool look to the whole table top.
After the epoxy was done the table was all but installed. We delivered it the next week and they couldn’t be happier with it! They said they already have a list of other things they want built for the house.
Step 8: The End
As always, if you have any questions or comments or inquiries, feel free to comment below or email me @ raleighdavisup@gmail.com !
-Raleigh
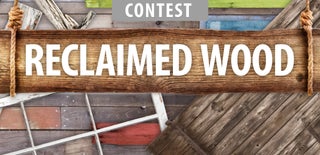
Participated in the
Reclaimed Wood Contest 2016